Introduction to Hole Production
Hole production is a crucial aspect of manufacturing processes across various industries. Blind holes and buried holes are two specific types of holes that require specialized techniques and tools for their creation. This article will delve into the intricacies of blind hole and buried hole production, exploring the methods, challenges, and best practices associated with these processes.
What are Blind Holes?
Blind holes, also known as non-through holes, are holes that do not pass completely through the workpiece. They have a specific depth and terminate within the material. Blind holes are commonly found in applications such as:
– Threaded holes for fasteners
– Lubrication reservoirs
– Locating pins
– Electrical connectors
Challenges in Blind Hole Production
Producing blind holes presents several challenges that manufacturers must address:
1. Depth control: Ensuring consistent and accurate depth is crucial for blind holes. Over-drilling can lead to damage or weakening of the workpiece.
2. Chip evacuation: As the hole does not pass through the material, chip removal can be difficult, especially in deep holes. Inadequate chip evacuation can cause tool breakage and affect hole quality.
3. Surface finish: Achieving a smooth surface finish at the bottom of the blind hole can be challenging due to limited access and chip accumulation.
Methods for Blind Hole Production
Several methods are employed for the production of blind holes, depending on the material, hole size, and required precision:
Drilling
Drilling is the most common method for creating blind holes. It involves using a twist drill or a specialized drill bit to remove material and create the hole. For blind holes, drills with modified geometry, such as spotting drills or flat-bottom drills, are often used to achieve a flat bottom surface.
Drill Type | Description | Advantages |
---|---|---|
Twist Drill | Standard drill bit with helical flutes | Versatile and widely available |
Spotting Drill | Drill bit with a short fluted length and a flat or angled tip | Provides a flat bottom surface and improves hole location accuracy |
Flat-Bottom Drill | Drill bit with a flat cutting edge at the tip | Creates holes with a flat bottom surface |
Reaming
Reaming is a finishing process that improves the dimensional accuracy, surface finish, and straightness of a previously drilled hole. For blind holes, reamers with a flat or chamfered tip are used to maintain a flat bottom surface.
Boring
Boring is a machining process that enlarges and improves the accuracy of a previously drilled hole. It involves using a single-point cutting tool on a boring bar. For blind holes, boring can be performed using a flat-bottom boring tool or a stepped boring bar to achieve the desired depth and bottom surface finish.
Helical Interpolation
Helical interpolation is a milling technique used to create precise blind holes with a flat bottom surface. It involves using a milling cutter to follow a helical path, gradually cutting the hole to the required depth. This method offers excellent control over hole geometry and surface finish.
What are Buried Holes?
Buried holes, also referred to as cross-holes or intersecting holes, are holes that intersect with another hole or feature within the workpiece. They are commonly used for:
– Fluid transfer in hydraulic or pneumatic systems
– Lubrication channels
– Coolant passages
– Cross-drilling in engine components
Challenges in Buried Hole Production
The production of buried holes presents unique challenges:
1. Alignment: Ensuring precise alignment between the intersecting holes is critical. Misalignment can lead to leakage, reduced performance, or assembly issues.
2. Drill wander: When drilling long buried holes, drill deviation can occur, affecting the accuracy and intersection point of the holes.
3. Cleaning: Removing chips and debris from the intersecting holes can be difficult, as the chips may accumulate at the intersection point.
Methods for Buried Hole Production
The production of buried holes often involves a combination of drilling techniques and specialized tools:
Gun Drilling
Gun drilling is a specialized deep hole drilling process that produces long, straight holes with high aspect ratios. It involves using a high-pressure coolant to flush chips out of the hole continuously. Gun drilling is commonly used for creating the main hole in buried hole applications.
Cross-Drilling
Cross-drilling refers to the process of drilling a hole that intersects with another hole at a specific angle. It requires precise positioning and alignment of the workpiece and drill bit. Specialized fixtures or multi-axis machines are often used to achieve the desired intersection angle.
Electro-Discharge Machining (EDM)
EDM is a non-traditional machining process that utilizes electrical sparks to remove material. It is particularly useful for creating small, precise buried holes in hard or difficult-to-machine materials. EDM can be used to create the intersecting hole after the main hole has been drilled.
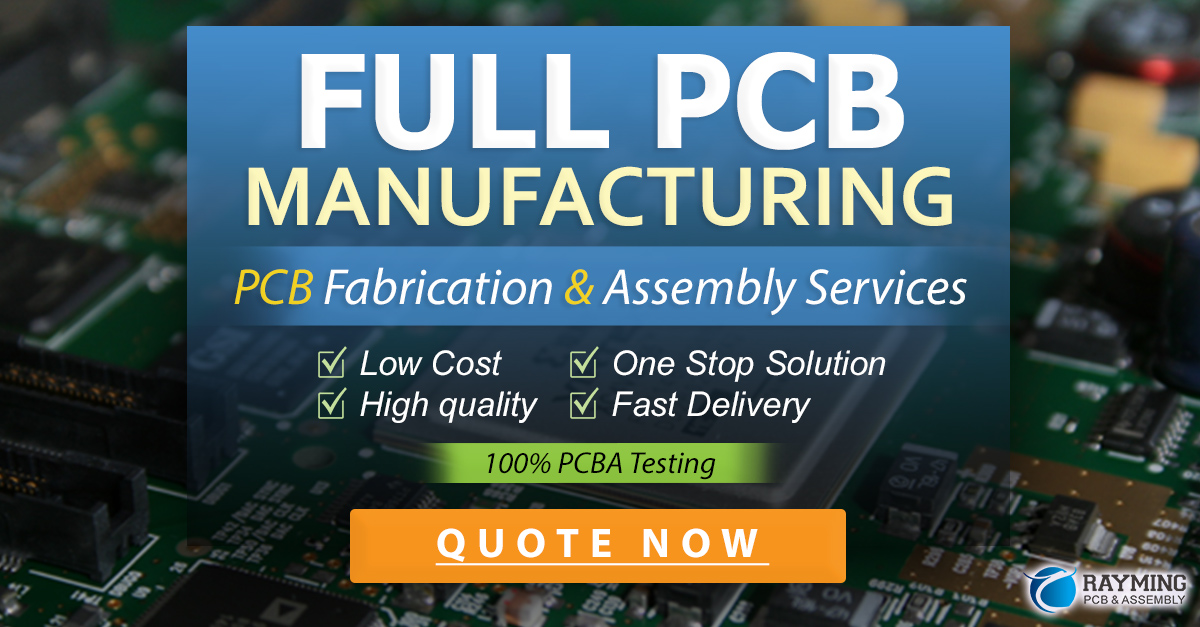
Best Practices for Blind and Buried Hole Production
To ensure successful and efficient production of blind and buried holes, consider the following best practices:
-
Tool selection: Choose the appropriate tools for each operation, considering factors such as material, hole size, depth, and required surface finish. Use coated or high-performance tools for improved tool life and hole quality.
-
Cutting parameters: Optimize cutting speeds, feeds, and depths of cut based on the tool and material combination. Consult tool manufacturers’ recommendations and perform tests to determine the best parameters for your specific application.
-
Coolant and lubrication: Use adequate coolant and lubrication to reduce heat generation, improve chip evacuation, and extend tool life. High-pressure coolant systems are particularly beneficial for deep hole drilling and buried hole production.
-
Workpiece fixturing: Ensure proper workpiece fixturing to minimize vibration and maintain alignment during the machining process. Use specialized fixtures or multi-axis machines for complex buried hole configurations.
-
Process monitoring: Implement process monitoring techniques, such as force monitoring or vibration analysis, to detect tool wear, breakage, or anomalies during the machining process. This helps prevent damage to the workpiece and ensures consistent hole quality.
Frequently Asked Questions (FAQ)
- What is the difference between a blind hole and a through hole?
-
A blind hole is a hole that does not pass completely through the workpiece, while a through hole extends from one surface of the workpiece to the opposite surface.
-
Can blind holes be threaded?
-
Yes, blind holes can be threaded using tapping or thread milling techniques. However, chip evacuation and tapping depth control require special consideration.
-
How can I ensure the accuracy of the intersection point in buried holes?
-
To ensure accurate intersection, use precise fixturing, multi-axis machines, or specialized drilling techniques like gun drilling. Perform test runs and measure the results to validate the process.
-
What are some common materials that require blind or buried hole production?
-
Blind and buried holes are commonly found in various materials, including metals (steel, aluminum, titanium), plastics, and composites. The specific material depends on the application and industry.
-
How can I improve the surface finish of blind holes?
- To improve the surface finish of blind holes, consider using specialized drill bits (e.g., flat-bottom drills), reaming, or boring techniques. Optimize cutting parameters and use adequate coolant and lubrication to minimize tool wear and vibration.
Conclusion
The production of blind holes and buried holes is a critical aspect of manufacturing processes in numerous industries. Understanding the challenges, methods, and best practices associated with these hole types is essential for achieving high-quality results and meeting functional requirements. By selecting the appropriate tools, optimizing cutting parameters, and implementing process monitoring techniques, manufacturers can effectively produce blind and buried holes with the desired accuracy, surface finish, and intersecting geometry. As technology advances, new methods and tools will continue to emerge, further enhancing the capabilities and efficiency of blind and buried hole production.
Leave a Reply