PCB Composition: An Overview
The Layers of a PCB
A typical PCB consists of several layers, each serving a specific purpose. The number of layers can vary depending on the complexity and requirements of the circuit design. The most common PCB configurations are:
- Single-layer PCB: Consists of a single conductive layer, usually copper, on one side of the insulating substrate.
- Double-layer PCB: Features two conductive layers, one on each side of the insulating substrate.
- Multi-layer PCB: Incorporates three or more conductive layers, alternating with insulating layers.
Layer Type | Description |
---|---|
Copper | Conductive layer for electrical connections |
Substrate | Insulating layer, typically made of FR-4 |
Solder Mask | Protective layer applied over copper traces |
Silkscreen | Printed layer for component labels and markings |
The Substrate Material
The substrate is the foundation of a PCB, providing mechanical support and electrical insulation between the conductive layers. The most commonly used substrate material is FR-4, a composite made of woven fiberglass cloth impregnated with an epoxy resin. FR-4 offers excellent electrical insulation properties, high mechanical strength, and good thermal stability.
Other substrate materials used in PCBs include:
- Polyimide: Known for its high heat resistance and flexibility, often used in flexible PCBs.
- Ceramic: Offers superior thermal conductivity and low dielectric loss, ideal for high-frequency applications.
- Aluminum: Provides excellent thermal dissipation, used in heat-sensitive applications.
The Conductive Layer: Copper
Copper is the most widely used conductive material in PCBs due to its excellent electrical conductivity, thermal conductivity, and relatively low cost. The copper layer is responsible for carrying electrical signals between components on the PCB.
The thickness of the copper layer is measured in ounces per square foot (oz/ft²). Common copper thicknesses include:
- 0.5 oz/ft²: Used in low-power, high-density designs.
- 1 oz/ft²: The most common thickness, suitable for a wide range of applications.
- 2 oz/ft² or higher: Used in high-power applications or when greater mechanical strength is required.
Solder Mask and Silkscreen
The solder mask is a protective layer applied over the copper traces on a PCB. It serves several purposes:
- Insulates and protects the copper traces from oxidation and corrosion.
- Prevents accidental short circuits by covering exposed copper areas.
- Provides a surface for applying solder paste during the component assembly process.
The silkscreen layer is a printed overlay on the PCB that contains component labels, logos, and other markings. It helps in identifying components and their orientations during assembly and troubleshooting.
The PCB Manufacturing Process
Step 1: Designing the PCB
The PCB manufacturing process begins with the design phase. Engineers use specialized software to create schematic diagrams and PCB layouts, specifying the placement of components, routing of traces, and other design elements.
Step 2: Printing the PCB Artwork
Once the design is finalized, the PCB artwork is printed onto a transparent film or photomask. This artwork contains the patterns for the copper traces, solder mask, and silkscreen layers.
Step 3: Applying the Copper Layer
The PCB substrate is laminated with a thin layer of copper on one or both sides, depending on the desired number of layers. For multi-layer PCBs, additional copper layers are laminated with insulating layers in between.
Step 4: Etching the Copper
The copper-clad substrate is coated with a light-sensitive photoresist. The photomask is then placed on top of the photoresist, and the assembly is exposed to ultraviolet (UV) light. The UV light hardens the photoresist in the areas not covered by the artwork.
The unexposed photoresist is then removed using a chemical developer, leaving the desired copper pattern exposed. The exposed copper is etched away using an acidic solution, while the hardened photoresist protects the desired copper traces.
Step 5: Applying Solder Mask and Silkscreen
After etching, a solder mask is applied to the PCB, covering the copper traces while leaving the pads and other designated areas exposed. The solder mask is typically applied using a silkscreen printing process.
The silkscreen layer is then printed onto the PCB, adding component labels and other markings.
Step 6: Finishing and Quality Control
The PCB undergoes a series of finishing processes, such as surface finish application (e.g., HASL, ENIG, or OSP) to protect the exposed copper pads and improve solderability.
Finally, the PCB is inspected for quality control, ensuring that all the layers are properly aligned, and the PCB meets the required specifications.
Advanced PCB Materials and Technologies
As electronic devices become more sophisticated and demanding, new PCB materials and technologies have emerged to meet these challenges. Some of these advanced developments include:
High-Frequency Laminates
For applications operating at high frequencies, such as 5G networks and radar systems, specialized laminates with low dielectric loss and stable dielectric constant are used. Examples include PTFE (Polytetrafluoroethylene) and low-loss hydrocarbon ceramic laminates.
Embedded Components
Embedded PCB technology allows passive components, such as resistors and capacitors, to be embedded within the PCB substrate. This approach saves space, reduces parasitic effects, and improves overall circuit performance.
Flexible and Rigid-Flex PCBs
Flexible PCBs are made using thin, flexible substrate materials like polyimide. They are ideal for applications requiring bendability or conformity to irregular shapes.
Rigid-flex PCBs combine the benefits of both rigid and flexible PCBs, featuring rigid sections for component mounting and flexible sections for interconnections. This technology is often used in wearable devices, medical equipment, and aerospace applications.
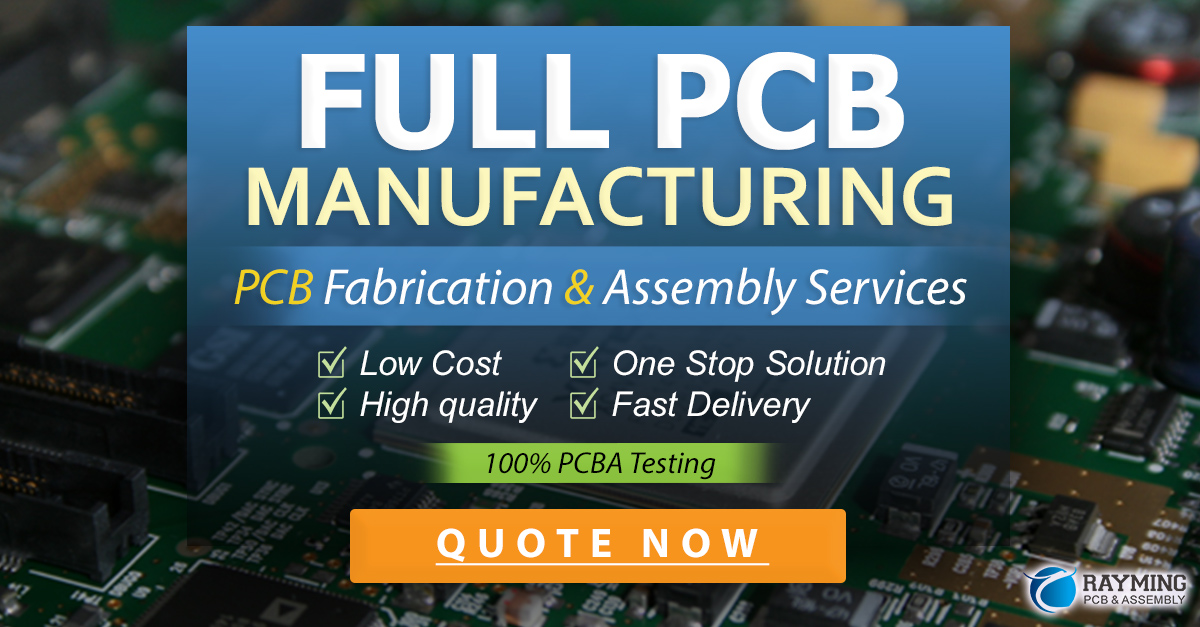
Frequently Asked Questions (FAQ)
-
Q: What is the most common substrate material used in PCBs?
A: FR-4, a composite of woven fiberglass and epoxy resin, is the most widely used substrate material in PCBs. -
Q: How does the number of layers in a PCB affect its functionality?
A: More layers in a PCB allow for higher component density, better signal integrity, and improved power distribution. However, increasing the number of layers also makes the PCB more complex and expensive to manufacture. -
Q: What is the purpose of the solder mask on a PCB?
A: The solder mask protects the copper traces from oxidation and corrosion, prevents accidental short circuits, and provides a surface for applying solder paste during component assembly. -
Q: Can PCBs be made using materials other than copper for the conductive layers?
A: While copper is the most common choice for the conductive layers in PCBs, other materials like aluminum, silver, and gold can be used in specific applications that require different properties, such as higher conductivity or better corrosion resistance. -
Q: What are the advantages of using embedded components in PCBs?
A: Embedded components in PCBs save space, reduce parasitic effects, and improve overall circuit performance by minimizing the distance between components and the PCB substrate.
Conclusion
PCBs are the unsung heroes of the electronic world, providing the foundation upon which modern devices are built. Understanding the composition and manufacturing process of PCBs is crucial for engineers, designers, and anyone involved in the electronics industry.
From the insulating substrate to the conductive copper layers, and from the protective solder mask to the informative silkscreen, each element of a PCB plays a vital role in ensuring the reliable operation of electronic devices.
As technology advances, so do the materials and techniques used in PCB manufacturing. By staying informed about these developments, we can continue to push the boundaries of what is possible in the world of electronics.
Leave a Reply