Introduction to PCB Tabs and Mouse Bites
Printed Circuit Boards (PCBs) are essential components in modern electronics, providing a platform for connecting and supporting various electronic components. In the manufacturing process of PCBs, it is common to produce multiple boards on a single panel to optimize production efficiency and reduce costs. However, this approach requires a reliable method to separate the individual boards from the panel after the assembly process. This is where PCB tabs, also known as breakaway tabs or mouse bites, come into play.
PCB tabs are small, perforated sections that connect the individual boards to the main panel. These tabs are designed to be easily broken or removed, allowing for the separation of the individual boards without damaging the circuits or components. There are several types of PCB tabs, including mouse bites, V-grooves, and scoring.
What are Mouse Bites?
Mouse bites, also known as perforations or break-off tabs, are a series of small, circular holes drilled along the edge of a PCB panel. These holes are typically arranged in a linear pattern, creating a perforated line that allows for easy separation of the individual boards. The term “mouse bites” comes from the appearance of the small, rounded holes, which resemble the bite marks of a mouse.
Mouse bites are created during the drilling process of PCB manufacturing. The holes are drilled using a specialized drill bit that creates clean, precise perforations without causing damage to the surrounding material. The size and spacing of the mouse bites can be adjusted based on the specific requirements of the PCB design and the desired ease of separation.
Advantages of Using Mouse Bites
There are several advantages to using mouse bites for PCB panel separation:
-
Easy Separation: Mouse bites provide a simple and intuitive method for separating individual boards from the panel. The perforated line created by the mouse bites allows for clean, controlled breaks without the need for special tools or equipment.
-
Minimal Waste: Compared to other panel separation methods, such as V-grooves or scoring, mouse bites generate minimal waste material. The small, circular holes remove only a small amount of PCB material, reducing the overall waste generated during the manufacturing process.
-
Versatility: Mouse bites can be used with a wide range of PCB materials, including FR4, aluminum, and flexible substrates. They can also be incorporated into various PCB designs, regardless of the shape or size of the individual boards.
-
Cost-Effective: Implementing mouse bites in the PCB manufacturing process is relatively inexpensive compared to other separation methods. The drilling process can be easily integrated into the existing manufacturing workflow without requiring significant additional equipment or setup costs.
Disadvantages of Using Mouse Bites
Despite their advantages, mouse bites also have some limitations and drawbacks:
-
Potential for Damage: If not handled carefully, separating boards along the mouse bite line can lead to accidental damage to the PCB or its components. Rough handling or excessive bending during the separation process can cause stress on the board and potentially damage delicate components.
-
Limited Strength: Mouse bites are not as strong as solid PCB material, which means that the tabs can break prematurely during handling or transport. This can be particularly problematic for larger or heavier boards that require more support during the manufacturing process.
-
Aesthetic Impact: The presence of mouse bites along the edges of the PCB can affect the overall appearance of the final product. The perforated line may be visible and detract from the aesthetic appeal of the board, especially in applications where visual appearance is important.
V-Groove PCB Tabs
V-groove PCB tabs are another popular method for separating individual boards from a panel. Unlike mouse bites, which use perforated holes, V-grooves are continuous channels cut into the PCB material using a specialized cutting tool.
What are V-Grooves?
V-grooves are narrow, V-shaped channels that are routed or cut into the PCB panel along the desired breakaway line. The depth and angle of the V-groove can be precisely controlled to ensure a clean, smooth break when the individual boards are separated from the panel.
The V-groove cutting process is typically performed using a CNC (Computer Numerical Control) router equipped with a V-shaped cutting bit. The router follows a predefined path, cutting the groove to the specified depth and width. The resulting V-groove creates a weakened line in the PCB material, allowing for easy separation of the individual boards.
Advantages of Using V-Grooves
V-groove PCB tabs offer several advantages over other separation methods:
-
Clean Break: V-grooves provide a clean, smooth break when separating the individual boards from the panel. The precise control over the depth and angle of the groove ensures a consistent and even break line, minimizing the risk of damage to the PCB or its components.
-
Strength and Durability: V-grooves offer better strength and durability compared to mouse bites. The continuous nature of the groove provides more support to the individual boards during handling and transport, reducing the risk of accidental breakage.
-
Improved Aesthetics: V-grooves result in a cleaner and more visually appealing edge compared to mouse bites. The smooth, continuous break line creates a more professional and polished look, which can be important in certain applications where aesthetic appearance is a key consideration.
-
Compatibility with Automated Processes: V-grooves are well-suited for automated PCB assembly processes. The clean, predictable break line allows for easy separation of the individual boards using automated equipment, streamlining the manufacturing workflow and reducing manual labor.
Disadvantages of Using V-Grooves
While V-grooves offer several benefits, they also have some limitations:
-
Increased Material Waste: V-grooves remove more PCB material compared to mouse bites, resulting in higher material waste during the manufacturing process. The continuous nature of the groove means that a larger amount of PCB material is removed along the breakaway line.
-
Higher Production Costs: Implementing V-grooves in the PCB manufacturing process can be more expensive compared to mouse bites. The CNC routing equipment and specialized cutting tools required for creating V-grooves can add to the overall production costs.
-
Limited Flexibility: V-grooves are less flexible than mouse bites in terms of PCB design and shape. The continuous nature of the groove means that it must follow a straight or gently curved path, which can limit the design options for irregularly shaped boards or those with complex geometries.
Breakaway Tabs
Breakaway tabs, also known as snap-off tabs or break-off tabs, are another method for separating individual PCBs from a panel. Unlike mouse bites and V-grooves, which rely on perforations or grooves, breakaway tabs use a solid tab of PCB material that can be easily snapped off.
What are Breakaway Tabs?
Breakaway tabs are small, solid sections of PCB material that connect the individual boards to the main panel. These tabs are typically located along the edges of the board and are designed to be easily snapped off by hand or with the use of simple tools.
The breakaway tabs are created during the PCB routing process, where the outline of the individual boards is cut from the main panel. The tabs are intentionally left uncut, providing a solid connection point between the board and the panel. The size and thickness of the breakaway tabs can be adjusted based on the specific requirements of the PCB design and the desired ease of separation.
Advantages of Using Breakaway Tabs
Breakaway tabs offer several advantages for PCB panel separation:
-
Simple and Intuitive: Breakaway tabs provide a simple and intuitive method for separating individual boards from the panel. The solid tab can be easily snapped off by hand or with the use of basic tools, making the separation process straightforward and accessible.
-
Strength and Support: Breakaway tabs offer excellent strength and support to the individual boards during the manufacturing process. The solid connection between the board and the panel helps to prevent accidental breakage or damage during handling and transport.
-
Minimal Material Waste: Breakaway tabs generate minimal material waste compared to other separation methods. Since the tabs are solid and do not require the removal of PCB material, there is no additional waste generated during the separation process.
-
Cost-Effective: Implementing breakaway tabs in the PCB manufacturing process is cost-effective, as it does not require specialized equipment or tooling. The tabs can be easily incorporated into the existing routing process without incurring significant additional costs.
Disadvantages of Using Breakaway Tabs
While breakaway tabs offer several benefits, they also have some limitations:
-
Potential for Damage: Separating boards using breakaway tabs requires manual force, which can lead to accidental damage if not done carefully. Excessive bending or twisting during the separation process can cause stress on the PCB and potentially damage components.
-
Inconsistent Break Line: The manual nature of separating boards using breakaway tabs can result in an inconsistent break line. The quality and smoothness of the break can vary depending on the individual performing the separation and the amount of force applied.
-
Aesthetic Impact: Breakaway tabs can leave a visible residue or stub on the edge of the PCB after separation. This can affect the overall appearance of the final product and may require additional processing, such as sanding or filing, to achieve a clean, smooth edge.
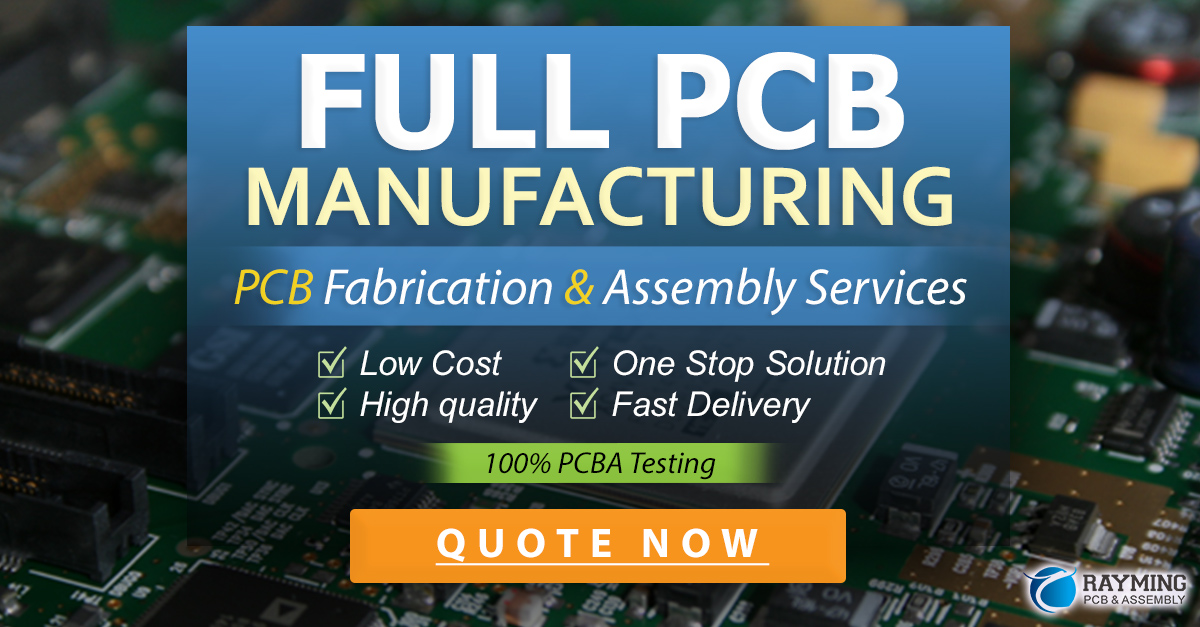
Comparison of PCB Tab Separation Methods
When selecting a PCB tab separation method, it is important to consider the specific requirements of your project and weigh the advantages and disadvantages of each approach. Here is a comparison table highlighting the key aspects of mouse bites, V-grooves, and breakaway tabs:
Aspect | Mouse Bites | V-Grooves | Breakaway Tabs |
---|---|---|---|
Ease of Separation | Easy | Easy | Moderate |
Strength and Durability | Limited | High | High |
Material Waste | Minimal | Moderate | Minimal |
Production Cost | Low | Moderate | Low |
Aesthetics | Perforated | Clean | Visible Residue |
Design Flexibility | High | Moderate | High |
Automation Compatibility | Limited | High | Limited |
As shown in the table, each separation method has its own strengths and weaknesses. Mouse bites offer easy separation and minimal material waste but have limited strength and may impact aesthetics. V-grooves provide a clean break and are compatible with automated processes but generate more material waste and have higher production costs. Breakaway tabs offer strength and minimal waste but require manual separation and may leave visible residue.
FAQ
-
Q: What are the most common PCB tab separation methods?
A: The most common PCB tab separation methods are mouse bites, V-grooves, and breakaway tabs. Each method has its own advantages and disadvantages, and the choice depends on the specific requirements of the PCB design and manufacturing process. -
Q: Can mouse bites be used with any PCB material?
A: Yes, mouse bites can be used with a wide range of PCB materials, including FR4, aluminum, and flexible substrates. The drilling process used to create mouse bites can be adapted to work with different materials, making them a versatile option for PCB panel separation. -
Q: What is the main advantage of using V-grooves for PCB separation?
A: The main advantage of using V-grooves for PCB separation is the clean, smooth break line they provide. The precise control over the depth and angle of the groove ensures a consistent and even break, minimizing the risk of damage to the PCB or its components. V-grooves also offer better strength and durability compared to mouse bites. -
Q: Are breakaway tabs suitable for automated PCB assembly processes?
A: Breakaway tabs are less suitable for automated PCB assembly processes compared to V-grooves. The manual nature of separating boards using breakaway tabs can be challenging to integrate into automated workflows. V-grooves, on the other hand, provide a clean, predictable break line that is well-suited for automated equipment. -
Q: How do I choose the right PCB tab separation method for my project?
A: When choosing a PCB tab separation method, consider factors such as the required strength and durability, material waste, production cost, aesthetics, design flexibility, and compatibility with automated processes. Evaluate the specific needs of your project and consult with your PCB manufacturer to determine the most suitable method based on your requirements and constraints.
Conclusion
PCB tab separation methods, including mouse bites, V-grooves, and breakaway tabs, play a crucial role in the manufacturing process of printed circuit boards. Each method offers unique advantages and disadvantages, and the choice of separation method depends on various factors such as design requirements, material properties, production costs, and manufacturing capabilities.
Mouse bites provide an easy and cost-effective solution for separating individual boards from a panel, with minimal material waste. However, they have limited strength and may impact the aesthetic appearance of the final product. V-grooves offer a clean, smooth break line and are compatible with automated assembly processes, but they generate more material waste and have higher production costs. Breakaway tabs provide strength and support during manufacturing but require manual separation and may leave visible residue on the board edges.
When selecting a PCB tab separation method, it is essential to carefully consider the specific needs and constraints of your project. Collaborate with your PCB manufacturer to evaluate the available options and determine the most suitable approach that balances performance, reliability, cost, and manufacturing efficiency.
By understanding the characteristics and trade-offs of different PCB tab separation methods, you can make informed decisions that optimize the manufacturing process and ensure the successful production of high-quality printed circuit boards.
Leave a Reply