Incorrect Component Placement
One of the most common issues in PCB assembly is the incorrect placement of components. This can occur due to human error, machine malfunction, or incorrect programming of the pick-and-place machine. Incorrect component placement can lead to short circuits, open circuits, or other malfunctions that can render the PCB unusable.
To avoid this problem, it is essential to:
– Double-check the component placement program before starting the assembly process
– Ensure that the pick-and-place machine is properly calibrated and maintained
– Implement quality control checks to verify correct component placement
Solder Bridging
Solder bridging occurs when excess solder creates an unintended connection between two or more component leads or PCB pads. This can cause short circuits and other malfunctions that can be difficult to detect and repair.
To prevent solder bridging:
– Use the appropriate amount of solder for each joint
– Ensure that the soldering iron temperature is set correctly
– Implement proper cleaning procedures to remove excess flux and solder
Cold Solder Joints
Cold solder joints occur when the solder does not melt completely, resulting in a weak or incomplete connection between the component lead and the PCB pad. This can cause intermittent or complete failure of the affected component.
To avoid cold solder joints:
– Ensure that the soldering iron temperature is set correctly
– Use high-quality solder and flux
– Allow sufficient time for the solder to melt and flow properly
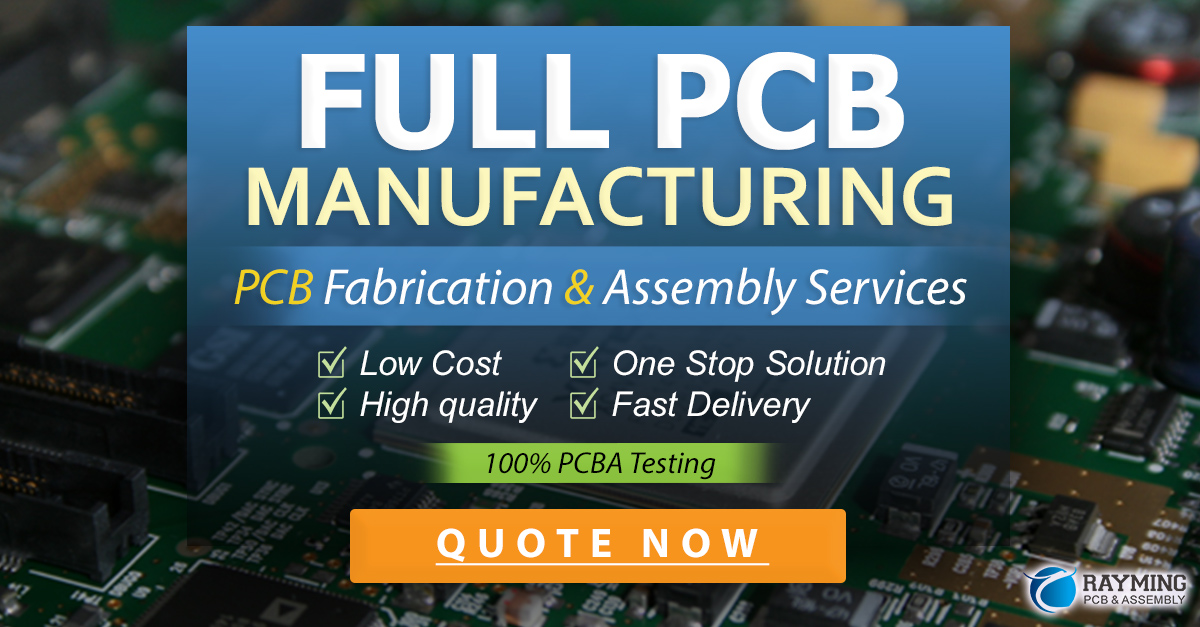
Tombstoning
Tombstoning, also known as drawbridging, occurs when a surface-mount component stands up on one end during the soldering process. This can be caused by uneven heating, incorrect placement, or other factors.
To prevent tombstoning:
– Ensure that the component pads are properly designed and sized
– Use a reflow oven with even heating across the PCB
– Implement proper component placement procedures
Insufficient Solder
Insufficient solder can occur when too little solder is used, resulting in a weak or incomplete connection between the component lead and the PCB pad. This can cause intermittent or complete failure of the affected component.
To avoid insufficient solder:
– Use the appropriate amount of solder for each joint
– Ensure that the soldering iron temperature is set correctly
– Implement quality control checks to verify proper solder coverage
Overheating
Overheating can occur when the soldering iron temperature is set too high or when the PCB is exposed to excessive heat during the assembly process. This can cause damage to the PCB, components, or solder joints.
To prevent overheating:
– Use the appropriate soldering iron temperature for the components and PCB material
– Implement proper heat sinking and cooling procedures
– Monitor the PCB temperature during the assembly process
Electrostatic Discharge (ESD) Damage
ESD damage can occur when static electricity builds up on the PCB or components and is suddenly discharged, causing damage to sensitive electronic components.
To avoid ESD damage:
– Use ESD-safe workstations, tools, and packaging materials
– Ensure that all personnel are properly trained in ESD prevention procedures
– Implement proper grounding and static dissipation techniques
Incorrect Component Polarity
Incorrect component polarity can occur when a component is placed on the PCB with the wrong orientation, resulting in reverse polarity or other malfunctions.
To prevent incorrect component polarity:
– Use clear and consistent component markings and labels
– Implement quality control checks to verify correct component orientation
– Ensure that the pick-and-place machine is programmed correctly
Flux Residue
Flux residue can occur when excess flux is not properly cleaned from the PCB after the soldering process. This can cause corrosion, short circuits, or other issues over time.
To avoid flux residue:
– Use the appropriate amount of flux for each joint
– Implement proper cleaning procedures to remove excess flux
– Use no-clean or low-residue flux when possible
Warping or Bending
Warping or bending of the PCB can occur due to improper handling, excessive heat, or other factors. This can cause component misalignment, solder joint failure, or other issues.
To prevent warping or bending:
– Use proper handling and storage procedures for PCBs
– Implement proper cooling and heat dissipation techniques during the assembly process
– Use PCB materials with appropriate thermal expansion properties
Here is a table summarizing the most common PCB Assembly Problems and their solutions:
Problem | Solution |
---|---|
Incorrect Component Placement | Double-check placement program, calibrate machine, implement quality control checks |
Solder Bridging | Use appropriate solder amount, set correct iron temperature, implement proper cleaning |
Cold Solder Joints | Set correct iron temperature, use high-quality solder and flux, allow sufficient time |
Tombstoning | Design proper component pads, use even heating, implement proper placement procedures |
Insufficient Solder | Use appropriate solder amount, set correct iron temperature, implement quality checks |
Overheating | Use appropriate iron temperature, implement heat sinking and cooling, monitor PCB temp |
ESD Damage | Use ESD-safe workstations and tools, train personnel, implement grounding techniques |
Incorrect Component Polarity | Use clear markings, implement quality checks, program pick-and-place machine correctly |
Flux Residue | Use appropriate flux amount, implement proper cleaning, use no-clean or low-residue flux |
Warping or Bending | Use proper handling and storage, implement cooling and heat dissipation, use appropriate PCB materials |
FAQ
1. What is the most common PCB assembly problem?
The most common PCB assembly problem is incorrect component placement, which can occur due to human error, machine malfunction, or incorrect programming of the pick-and-place machine.
2. How can I prevent solder bridging during PCB assembly?
To prevent solder bridging, use the appropriate amount of solder for each joint, ensure that the soldering iron temperature is set correctly, and implement proper cleaning procedures to remove excess flux and solder.
3. What causes cold solder joints in PCB assembly?
Cold solder joints occur when the solder does not melt completely, resulting in a weak or incomplete connection between the component lead and the PCB pad. This can be caused by incorrect soldering iron temperature, low-quality solder or flux, or insufficient time allowed for the solder to melt and flow properly.
4. How can I avoid ESD damage during PCB assembly?
To avoid ESD damage during PCB assembly, use ESD-safe workstations, tools, and packaging materials, ensure that all personnel are properly trained in ESD prevention procedures, and implement proper grounding and static dissipation techniques.
5. What should I do if I notice warping or bending of the PCB during assembly?
If you notice warping or bending of the PCB during assembly, use proper handling and storage procedures for PCBs, implement proper cooling and heat dissipation techniques during the assembly process, and consider using PCB materials with appropriate thermal expansion properties to minimize the risk of warping or bending.
By understanding the most common PCB assembly problems and implementing the appropriate solutions and preventive measures, manufacturers can ensure the production of high-quality, reliable PCBs that meet the required specifications and performance standards. Proper training, equipment maintenance, and quality control procedures are essential to minimize the risk of assembly issues and maximize the efficiency and productivity of the PCB assembly process.
Leave a Reply