PCB Design Complexity
One of the most significant factors influencing the cost of custom PCB assembly is the complexity of the PCB design. The more intricate and demanding the design, the higher the manufacturing costs will be.
Number of Layers
The number of layers in a PCB directly affects its manufacturing cost. As the layer count increases, so does the complexity of the manufacturing process, resulting in higher costs. Here’s a breakdown of how the number of layers can impact PCB assembly costs:
Number of Layers | Cost Impact |
---|---|
1-2 layers | Low |
4 layers | Medium |
6-8 layers | High |
10+ layers | Very High |
Component Density
The density of components on a PCB also plays a significant role in determining the manufacturing cost. Higher component density requires more precise placement and soldering techniques, which can increase assembly time and costs. PCBs with a high component density may also require specialized equipment and skilled labor, further driving up the overall cost.
Trace Width and Spacing
Trace width and spacing are critical aspects of PCB design that can impact manufacturing costs. Narrower traces and tighter spacing between components require more advanced manufacturing processes and higher precision, leading to increased costs. When designing a PCB, it’s essential to strike a balance between performance requirements and cost-effective manufacturing capabilities.
Material Selection
The choice of materials used in PCB manufacturing can significantly affect the cost of custom PCB assembly. Different materials offer varying properties and price points, making material selection a crucial factor in managing costs.
PCB Substrate Material
The substrate material is the foundation of a PCB, providing the base on which the circuits are built. Common substrate materials include:
- FR-4: A popular and cost-effective choice for most PCB applications.
- High-Tg FR-4: Offers better thermal stability than standard FR-4 but comes at a higher cost.
- Polyimide: Provides excellent thermal resistance and stability but is more expensive than FR-4.
- Aluminum: Used for PCBs that require better heat dissipation, but it comes with a higher price tag.
Copper Weight
The thickness of the copper used in PCB traces, measured in ounces per square foot (oz/ft²), also affects the manufacturing cost. Higher copper weights offer better current-carrying capacity and thermal performance but increase the overall cost of the PCB. Common copper weights include:
- 0.5 oz/ft²: Thin and cost-effective, suitable for low-power applications.
- 1 oz/ft²: The most common choice, offering a good balance between performance and cost.
- 2 oz/ft² and above: Used for high-power applications but come with a higher price tag.
Solder Mask and Silkscreen
The solder mask and silkscreen are essential components of a PCB that provide insulation and component labeling, respectively. The choice of color and material for these elements can impact the manufacturing cost. For example, using a standard green solder mask is generally more cost-effective than opting for custom colors or matte finishes.
Manufacturing Volume
The volume of PCBs being manufactured is another significant factor that affects the cost of custom PCB assembly. Higher production volumes often result in lower per-unit costs due to economies of scale.
Economies of Scale
As the manufacturing volume increases, fixed costs such as setup, tooling, and equipment are spread across a larger number of units, reducing the per-unit cost. This principle, known as economies of scale, is a key factor in determining the cost-effectiveness of custom PCB assembly.
Minimum Order Quantities (MOQs)
Many PCB manufacturers have minimum order quantities (MOQs) that must be met to initiate production. These MOQs can vary depending on the manufacturer and the specific PCB requirements. Smaller MOQs generally result in higher per-unit costs, while larger MOQs can lead to more significant cost savings.
Prototype vs. Production Runs
The cost of custom PCB assembly also differs between prototype and production runs. Prototype runs typically involve smaller quantities and may require more manual labor, resulting in higher per-unit costs. On the other hand, production runs benefit from automation and economies of scale, leading to lower per-unit costs.
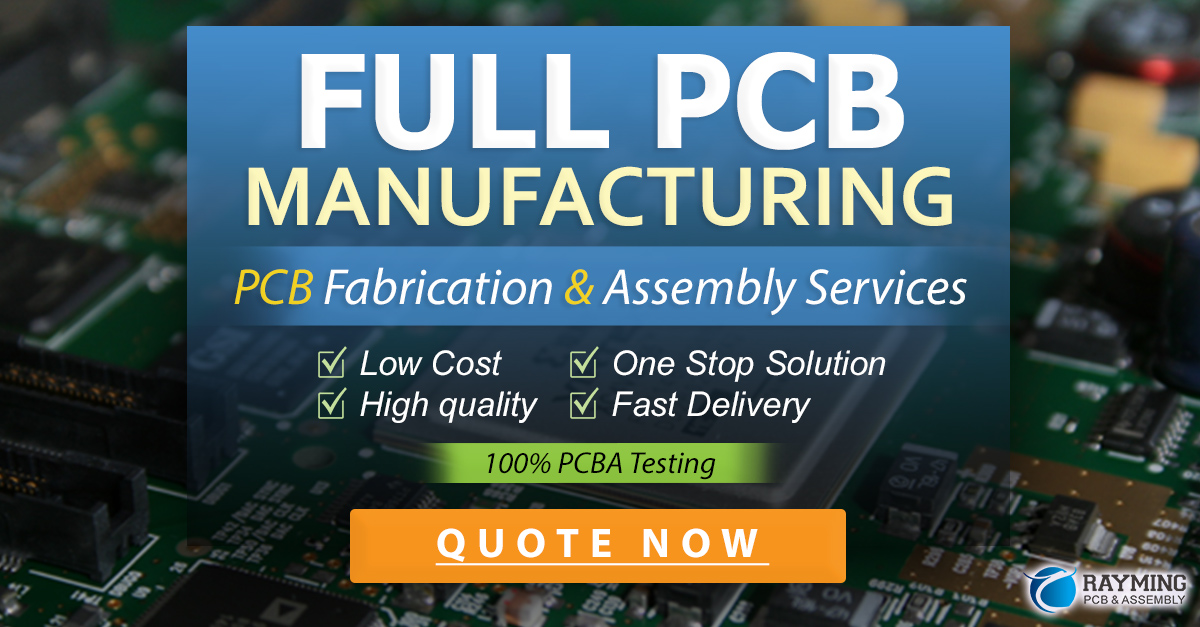
Manufacturing Turnaround Time
The turnaround time for custom PCB assembly can also impact the overall cost. Faster turnaround times often come with a premium price tag, while longer lead times can result in cost savings.
Standard vs. Expedited Production
Most PCB manufacturers offer standard and expedited production options. Standard production typically has longer lead times but comes at a lower cost. Expedited production prioritizes faster turnaround times but often involves additional fees and higher overall costs.
Rush Orders
In some cases, businesses may require rush orders to meet urgent deadlines. Rush orders are usually associated with significantly higher costs due to the need for overtime labor, expedited shipping, and the disruption of regular production schedules.
Quality Control and Testing
Ensuring the quality and reliability of custom PCBs is essential, but it also contributes to the overall cost of assembly. More stringent quality control measures and testing procedures can increase manufacturing costs.
Visual Inspection
Visual inspection is a basic quality control measure that involves examining the PCB for any visible defects or issues. This process is relatively inexpensive but may not catch all potential problems.
Automated Optical Inspection (AOI)
Automated Optical Inspection (AOI) uses cameras and image processing software to detect surface-level defects on PCBs. AOI is more thorough than visual inspection and can help identify issues such as incorrect component placement, solder bridging, and missing components. However, implementing AOI systems can increase the overall manufacturing cost.
Functional Testing
Functional testing involves verifying the electrical performance and functionality of the assembled PCB. This process can range from simple continuity tests to more complex functional tests that simulate real-world operating conditions. Functional testing is crucial for ensuring the reliability of the PCB but can add to the overall manufacturing cost, especially for more complex designs.
Frequently Asked Questions (FAQ)
-
Q: How can I reduce the cost of custom PCB assembly without compromising quality?
A: To reduce costs without sacrificing quality, consider simplifying your PCB design, choosing cost-effective materials, and opting for standard manufacturing processes when possible. Additionally, ordering in larger quantities can help you take advantage of economies of scale. -
Q: What is the most significant factor affecting the cost of custom PCB assembly?
A: The complexity of the PCB design is often the most significant factor influencing the cost of custom PCB assembly. More complex designs with higher layer counts, dense component placement, and tight tolerances generally result in higher manufacturing costs. -
Q: How do I choose the right material for my custom PCB?
A: When selecting materials for your custom PCB, consider factors such as the intended application, performance requirements, and budget constraints. Consult with your PCB manufacturer to determine the most suitable material options based on your specific needs. -
Q: Is it always more cost-effective to order PCBs in larger quantities?
A: In most cases, ordering PCBs in larger quantities results in lower per-unit costs due to economies of scale. However, it’s essential to consider factors such as inventory storage costs and the risk of obsolescence when deciding on the appropriate order quantity. -
Q: How can I ensure the quality of my custom PCBs while managing costs?
A: To ensure the quality of your custom PCBs while managing costs, work closely with your PCB manufacturer to establish clear quality control standards and testing procedures. Opt for a balance between cost-effective and reliable quality control measures, such as automated optical inspection (AOI) and targeted functional testing.
Conclusion
Understanding the top manufacturing factors that affect the cost of custom PCB assembly is essential for businesses and individuals looking to optimize their budgets while maintaining high-quality results. By considering factors such as PCB design complexity, material selection, manufacturing volume, turnaround time, and quality control, you can make informed decisions that balance cost and performance.
When navigating the custom PCB assembly process, it’s crucial to work closely with experienced PCB manufacturers who can provide expert guidance and support. By collaborating with a reliable partner and making strategic choices throughout the manufacturing process, you can effectively manage costs and ensure the success of your custom PCB projects.
Leave a Reply