1. Experience and Expertise in Rigid-flex PCB Manufacturing
When searching for a rigid-flex PCB manufacturer, it’s essential to consider their experience and expertise in this specific area. Rigid-flex PCBs are more complex than traditional rigid or flexible PCBs, requiring specialized knowledge and manufacturing processes. Look for a manufacturer with a proven track record of successfully producing rigid-flex PCBs for various applications and industries.
Questions to Ask:
- How long has the manufacturer been producing rigid-flex PCBs?
- What industries have they served with their rigid-flex PCB solutions?
- Can they provide examples of previous rigid-flex PCB projects they have completed?
2. Manufacturing Capabilities and Technology
A Reliable Rigid-Flex PCB manufacturer should have state-of-the-art manufacturing facilities and technology to ensure the highest quality products. Inquire about their manufacturing capabilities, including the types of materials they work with, the minimum feature sizes they can achieve, and the maximum number of layers they can produce.
Key Manufacturing Capabilities to Consider:
Capability | Description |
---|---|
Materials | Variety of substrate materials, such as polyimide, FR-4, and high-frequency laminates |
Feature Sizes | Minimum trace width, spacing, and hole size achievable |
Layer Count | Maximum number of layers that can be produced in a single rigid-flex PCB |
Lamination | Ability to laminate flexible and rigid layers together without causing defects or delamination |
3. Quality Control and Testing Procedures
Ensuring the quality and reliability of your rigid-flex PCBs is crucial for the success of your project. A reputable manufacturer should have stringent quality control measures and testing procedures in place to identify and address any issues before the final product is delivered.
Quality Control Measures to Look For:
- Automated optical inspection (AOI) for detecting surface defects
- X-ray inspection for identifying internal defects and voids
- Electrical testing to ensure proper functionality and performance
- Thermal cycling and mechanical stress testing to validate the product’s durability
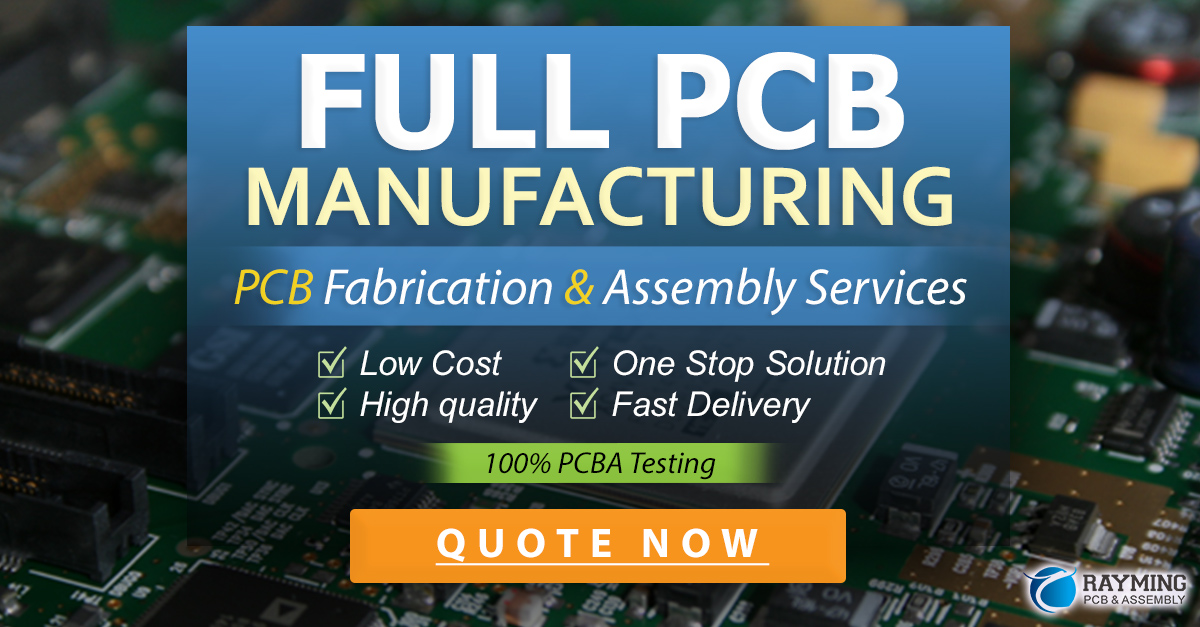
4. Certifications and Standards Compliance
When choosing a rigid-flex PCB manufacturer, it’s important to verify that they hold relevant certifications and comply with industry standards. These certifications demonstrate the manufacturer’s commitment to quality, safety, and environmental responsibility.
Key Certifications and Standards:
- ISO 9001 (Quality Management System)
- IPC-6013 (Qualification and Performance Specification for Flexible Printed Boards)
- UL 94 (Flammability Rating)
- RoHS (Restriction of Hazardous Substances)
- REACH (Registration, Evaluation, Authorization, and Restriction of Chemicals)
5. Design Support and Collaboration
Collaborating with a rigid-flex PCB manufacturer that offers design support can help streamline your project and ensure optimal results. Look for a manufacturer willing to work closely with your team, providing guidance on design considerations, materials selection, and manufacturing feasibility.
Design Support Services to Consider:
- Design for Manufacturability (DFM) analysis
- Signal integrity analysis and simulation
- 3D modeling and visualization
- Prototype development and testing
6. Lead Times and Delivery
When selecting a rigid-flex PCB manufacturer, it’s crucial to consider their lead times and delivery options. Ensure that the manufacturer can meet your project’s timeline and provide reliable shipping and logistics services.
Factors Affecting Lead Times:
- Project complexity and layer count
- Material availability and sourcing
- Manufacturing capacity and workload
- Quality control and testing procedures
7. Cost and Pricing Structure
While cost is an important consideration when choosing a rigid-flex PCB manufacturer, it should not be the sole deciding factor. Strike a balance between cost and quality, ensuring that the manufacturer can deliver a high-quality product within your budget.
Cost Considerations:
- Material costs and availability
- Tooling and setup fees
- Minimum order quantities (MOQs)
- Volume discounts and pricing tiers
8. Customer Support and Communication
Effective communication and responsive customer support are essential when working with a rigid-flex PCB manufacturer. Look for a manufacturer that prioritizes clear, timely communication and offers dedicated support throughout the project lifecycle.
Communication Channels to Expect:
- Designated project manager or point of contact
- Regular progress updates and status reports
- Online portal for order tracking and documentation
- Technical support for design and manufacturing questions
9. References and Reputation
Finally, research the rigid-flex PCB manufacturer’s reputation and seek references from previous clients. A reputable manufacturer should be willing to provide references and case studies that demonstrate their ability to deliver high-quality rigid-flex PCBs.
Ways to Evaluate a Manufacturer’s Reputation:
- Request references and contact previous clients
- Read online reviews and testimonials
- Attend industry events and trade shows to network and gather feedback
- Consult with industry associations and forums for recommendations
FAQ
1. What are the advantages of using rigid-flex PCBs?
Rigid-flex PCBs offer several advantages, including:
– Reduced size and weight compared to separate rigid and flexible PCBs
– Improved reliability and durability due to fewer interconnects
– Enhanced signal integrity and reduced electromagnetic interference (EMI)
– Increased design flexibility and 3D packaging options
2. How do I determine the layer stack-up for my rigid-flex PCB?
The layer stack-up for your rigid-flex PCB will depend on various factors, such as:
– The number and placement of rigid and flexible layers
– The required electrical performance and signal integrity
– The mechanical requirements and bend radii
– The available space and weight constraints
Work closely with your rigid-flex PCB manufacturer to determine the optimal layer stack-up for your specific application.
3. What materials are commonly used in rigid-flex PCBs?
Common materials used in rigid-flex PCBs include:
– Polyimide (PI) for the flexible layers
– FR-4 or high-frequency laminates for the rigid layers
– Copper foil for the conductive traces
– Adhesives and coverlays for bonding and protection
4. How can I ensure the reliability of my rigid-flex PCBs?
To ensure the reliability of your rigid-flex PCBs:
– Follow best practices for rigid-flex PCB design, including proper bend radius and strain relief
– Select high-quality materials that meet your application’s requirements
– Work with a reputable manufacturer that adheres to strict quality control and testing procedures
– Conduct thorough testing and validation of your rigid-flex PCBs under real-world conditions
5. What is the typical turnaround time for rigid-flex PCB manufacturing?
The turnaround time for rigid-flex PCB manufacturing can vary depending on factors such as:
– The complexity of the design and layer stack-up
– The availability of materials and components
– The manufacturer’s capacity and workload
Typical turnaround times can range from 2-3 weeks for simple designs to 6-8 weeks for more complex projects. Discuss your timeline requirements with your chosen manufacturer to ensure they can meet your needs.
Conclusion
Choosing the right rigid-flex PCB manufacturer is essential for the success of your project. By considering factors such as experience, manufacturing capabilities, quality control, certifications, design support, lead times, cost, customer support, and reputation, you can make an informed decision and select a manufacturer that will deliver high-quality rigid-flex PCBs that meet your specific requirements.
Remember to prioritize clear communication, collaborate closely with your chosen manufacturer, and thoroughly test and validate your rigid-flex PCBs to ensure optimal performance and reliability in your final application.
Leave a Reply