PCB Size and Complexity
The size and complexity of your PCB design significantly influence the overall cost. Larger PCBs require more materials and take longer to manufacture, resulting in higher prices. Additionally, complex designs with intricate traces, multiple layers, and high component density also contribute to increased costs.
Consider the following table, which illustrates the relationship between PCB size and pricing:
PCB Size | Approximate Price Range |
---|---|
Small (< 50 sq. cm) | $5 – $20 |
Medium (50 – 200 sq. cm) | $20 – $50 |
Large (> 200 sq. cm) | $50 – $100+ |
Note: Prices are for reference only and may vary based on other factors.
To minimize costs, it’s essential to optimize your PCB design by considering the following:
- Minimize the overall PCB dimensions while ensuring functionality
- Simplify the design by reducing unnecessary components and traces
- Use standard sizes and shapes whenever possible
Number of Layers
The number of layers in a PCB directly impacts its manufacturing cost. Each additional layer requires more materials, processing time, and complexity. Generally, PCBs can have anywhere from 1 to 16 layers or more.
Here’s a rough guide to the relationship between the number of layers and pricing:
Number of Layers | Approximate Price Multiplier |
---|---|
1 – 2 | 1x |
4 | 1.5x – 2x |
6 | 2x – 3x |
8+ | 3x+ |
Note: Price multipliers are for reference only and may vary based on other factors.
To optimize costs, consider the following:
- Use the minimum number of layers required for your design
- Carefully plan the layer stackup to minimize the need for additional layers
- Consider using blind and buried vias sparingly, as they increase complexity and cost
PCB Material Selection
The choice of PCB material also plays a role in pricing. The most common materials used in PCB manufacturing are FR-4, which is a flame-retardant glass-reinforced epoxy laminate, and various high-frequency materials like Rogers or Isola.
Here’s a comparison of common PCB materials and their relative costs:
Material | Relative Cost |
---|---|
FR-4 | Low |
Rogers | High |
Isola | Medium – High |
Polyimide | High |
Note: Relative costs are for reference only and may vary based on specific material grades and suppliers.
When selecting PCB materials, consider the following:
- Choose the most cost-effective material that meets your design requirements
- Consider the dielectric constant, loss tangent, and thermal properties of the material
- Be aware of any special processing requirements for exotic materials
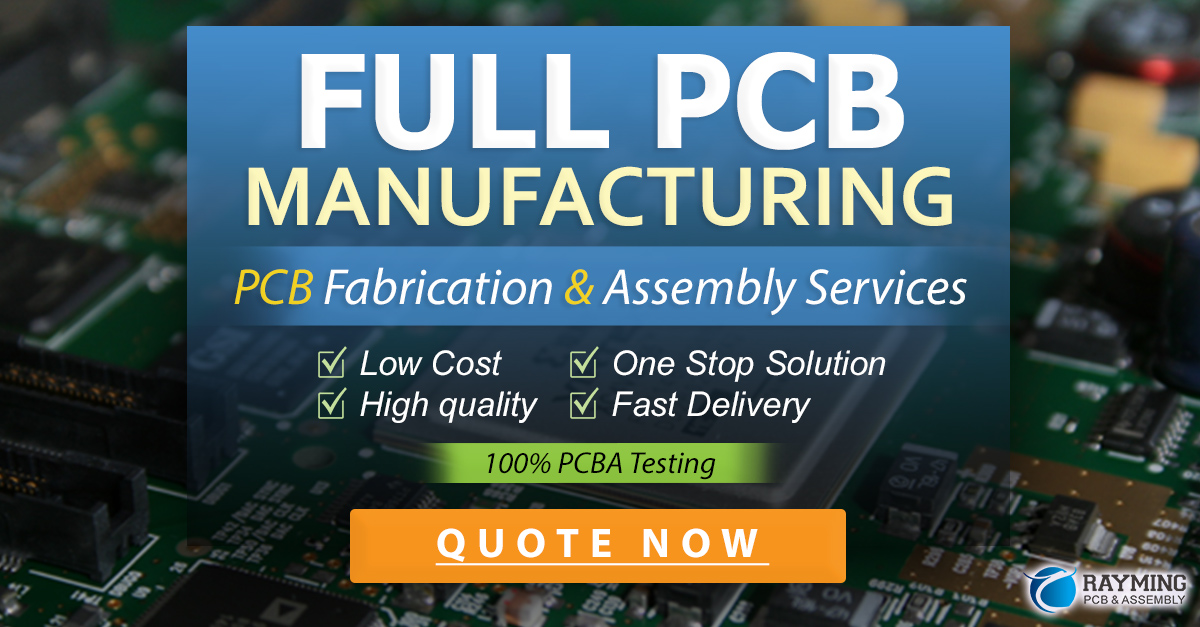
Surface Finish
The surface finish of a PCB affects its solderability, durability, and overall cost. Common surface finishes include Hot Air Solder Leveling (HASL), Electroless Nickel Immersion Gold (ENIG), and Organic Solderability Preservative (OSP).
Here’s a comparison of popular surface finishes and their relative costs:
Surface Finish | Relative Cost |
---|---|
HASL | Low |
ENIG | High |
OSP | Low – Medium |
Immersion Tin | Medium |
Immersion Silver | Medium – High |
Note: Relative costs are for reference only and may vary based on specific process requirements and suppliers.
When choosing a surface finish, consider the following:
- Select the most cost-effective finish that meets your solderability and durability requirements
- Consider the shelf life and storage conditions of the finished PCBs
- Be aware of any compatibility issues between the surface finish and the components or assembly processes
Quantity and Economies of Scale
The quantity of PCBs you order significantly impacts the unit price. Larger quantities benefit from economies of scale, as the fixed costs associated with setup, tooling, and processing are spread across more units.
Here’s an example of how quantity affects PCB pricing:
Quantity | Approximate Unit Price |
---|---|
1 – 10 | $50 – $100+ |
11 – 100 | $10 – $50 |
101 – 1000 | $5 – $20 |
1000+ | $1 – $10 |
Note: Prices are for reference only and may vary based on other factors.
To optimize costs, consider the following:
- Order in larger quantities when possible to take advantage of volume discounts
- Consider future demand and plan for larger production runs
- Work with your PCB manufacturer to determine the most cost-effective quantity breaks
Lead Time and Rush Fees
The lead time for PCB manufacturing can vary depending on the complexity of the design, the chosen manufacturer, and their current workload. Shorter lead times often incur rush fees, which can significantly increase the overall cost.
Here’s a general guide to lead times and their impact on pricing:
Lead Time | Approximate Price Multiplier |
---|---|
Standard (2-3 weeks) | 1x |
Rush (1-2 weeks) | 1.5x – 2x |
Super Rush (< 1 week) | 2x – 3x |
Note: Price multipliers are for reference only and may vary based on the specific manufacturer and their policies.
To manage costs related to lead times, consider the following:
- Plan ahead and allow for standard lead times whenever possible
- Communicate your lead time requirements clearly with your PCB manufacturer
- Be prepared to pay rush fees for urgent projects, but try to minimize their occurrence
Design for Manufacturability (DFM)
Design for Manufacturability (DFM) refers to the practice of designing PCBs in a way that optimizes their manufacturability and reduces costs. By following DFM guidelines, you can minimize the chances of design-related issues that can lead to increased costs and delays.
Some key DFM considerations include:
- Adhering to the manufacturer’s design rules and guidelines
- Using standard components and footprints whenever possible
- Avoiding unnecessary tight tolerances and small feature sizes
- Incorporating proper grounding and power distribution techniques
By incorporating DFM principles into your PCB design process, you can:
- Reduce the likelihood of design revisions and associated costs
- Minimize the risk of manufacturing defects and scrap
- Improve the overall reliability and performance of your PCBs
Testing and Quality Control
Testing and quality control procedures are essential for ensuring the reliability and functionality of your PCBs. However, these processes also contribute to the overall cost. Common testing methods include:
- Automated Optical Inspection (AOI)
- In-Circuit Testing (ICT)
- Flying Probe Testing
- Functional Testing
The cost of testing varies depending on the complexity of the PCB, the required coverage, and the specific testing methods employed. In general, more extensive testing will result in higher costs but can also help catch defects early, reducing the risk of costly field failures.
To balance testing costs and quality, consider the following:
- Work with your PCB manufacturer to determine the most appropriate testing methods for your project
- Consider the criticality of your application and adjust testing requirements accordingly
- Implement a risk-based approach to testing, focusing on the most critical aspects of your design
Shipping and Logistics
Shipping and logistics costs can also impact the overall cost of your PCBs, especially when dealing with international suppliers or urgent deliveries. Factors that influence shipping costs include:
- Distance and destination
- Shipping method (e.g., air, sea, ground)
- Package size and weight
- Customs and import duties
To manage shipping and logistics costs, consider the following:
- Choose a PCB manufacturer with a location that balances production costs and shipping expenses
- Plan ahead to allow for cost-effective shipping methods
- Consider consolidating shipments to reduce overall shipping costs
- Work with your PCB manufacturer to optimize packaging and minimize dimensional weight
Frequently Asked Questions (FAQ)
1. How can I get the best price for my PCB project?
To get the best price for your PCB project, consider the following:
- Optimize your design for manufacturability and cost-effectiveness
- Choose the most appropriate materials, surface finishes, and testing methods
- Order in larger quantities to take advantage of volume discounts
- Plan ahead to allow for standard lead times and cost-effective shipping
2. What is the most cost-effective PCB material?
FR-4 is generally the most cost-effective PCB material for the majority of applications. It offers a good balance of mechanical, electrical, and thermal properties at a relatively low cost compared to more specialized materials like Rogers or Isola.
3. How do I choose the right surface finish for my PCBs?
When choosing a surface finish, consider the following factors:
- Solderability and assembly requirements
- Durability and shelf life
- Compatibility with components and assembly processes
- Cost and availability
HASL and OSP are generally the most cost-effective options, while ENIG and immersion silver offer better solderability and durability at a higher cost.
4. Can I reduce costs by using a smaller PCB manufacturer?
While smaller PCB manufacturers may offer lower prices, it’s essential to consider other factors such as quality, reliability, and customer support. Established manufacturers with a proven track record may provide better value in the long run, even if their prices are slightly higher.
5. How can I manage the costs associated with rush orders?
To manage the costs associated with rush orders, consider the following:
- Plan ahead and allow for standard lead times whenever possible
- Communicate your requirements clearly with your PCB manufacturer and discuss potential cost-saving options
- Consider alternative designs or materials that may be more readily available
- Prioritize the most critical aspects of your project and focus rush orders on those areas
By understanding and managing these nine key PCB Pricing Factors, you can make informed decisions, optimize your costs, and ensure the success of your PCB projects.
Leave a Reply