Introduction to Multilayer PCB Fabrication
Multilayer PCB Fabrication is a complex process that involves the creation of printed circuit boards with multiple layers of conductive and insulating materials. These boards are essential components in a wide range of electronic devices, from smartphones and computers to medical equipment and aerospace systems. However, the fabrication process is not without its challenges, and manufacturers must be aware of the potential problems that can arise.
In this article, we will explore seven common problems that can occur during the multilayer PCB fabrication process, along with solutions and best practices for avoiding them.
Problem 1: Layer Misalignment
One of the most significant challenges in multilayer PCB fabrication is ensuring that all layers are correctly aligned. Misalignment can occur due to a variety of factors, including:
- Incorrect registration of layers during the lamination process
- Shrinkage or expansion of materials during processing
- Inaccurate drilling or punching of holes
Misaligned layers can lead to a range of issues, including:
- Short circuits between layers
- Open circuits due to broken or disconnected traces
- Reduced signal integrity and performance
To prevent layer misalignment, manufacturers must:
- Use high-quality materials with stable dimensions and properties
- Employ precise registration and alignment techniques during lamination
- Use advanced drilling and punching equipment with tight tolerances
- Implement strict quality control measures to detect and correct misalignment issues
Problem 2: Delamination
Delamination is another common problem in multilayer PCB fabrication, where the layers of the board separate or peel apart. This can occur due to several factors, including:
- Poor adhesion between layers during lamination
- Excessive heat or pressure during processing
- Contamination or impurities on the surface of the layers
- Mechanical stress or shock during handling or use
Delamination can cause a range of issues, such as:
- Reduced structural integrity and reliability of the board
- Exposure of internal layers to moisture, chemicals, or other contaminants
- Electrical failures due to broken or disconnected traces
To prevent delamination, manufacturers should:
- Use high-quality adhesives and bonding materials
- Control the temperature and pressure during lamination to ensure proper bonding
- Maintain a clean and controlled environment to minimize contamination
- Use gentle handling and packaging techniques to avoid mechanical stress
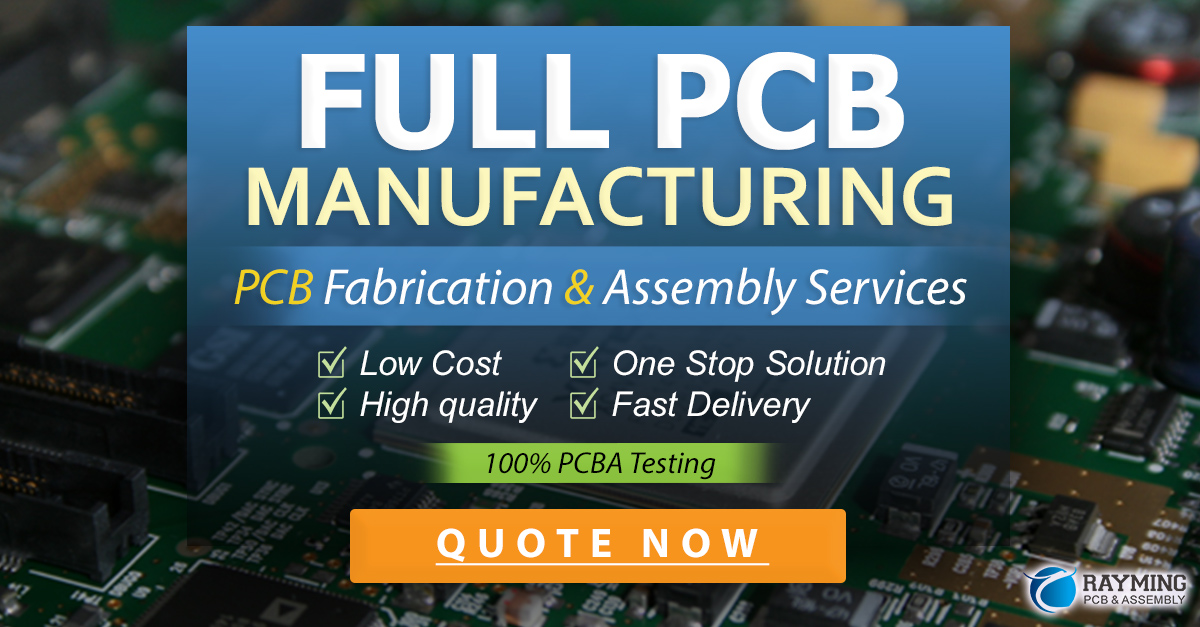
Problem 3: Copper Foil Defects
Copper foil is a critical component in multilayer PCBs, providing the conductive pathways for electrical signals. However, copper foil can be susceptible to various defects that can affect the performance and reliability of the board, such as:
- Pinholes or voids in the copper surface
- Scratches, dents, or other mechanical damage
- Oxidation or corrosion of the copper surface
- Contamination or impurities in the copper foil
These defects can lead to issues such as:
- Increased resistance or impedance in the conductive pathways
- Reduced signal integrity and performance
- Electrical failures due to open or short circuits
To prevent copper foil defects, manufacturers should:
- Use high-quality copper foil with minimal imperfections
- Handle and store the copper foil carefully to avoid mechanical damage
- Control the environment to minimize oxidation and contamination
- Implement strict quality control measures to detect and reject defective foil
Problem 4: Drilling and Plating Issues
Drilling and plating are critical steps in the multilayer PCB fabrication process, creating the holes and vias that connect the layers of the board. However, these processes can be prone to various issues, such as:
- Inaccurate or inconsistent hole sizes or locations
- Roughness or burrs on the hole walls
- Incomplete or uneven plating of the holes
- Voids or gaps in the plating
These issues can cause problems such as:
- Poor electrical connections between layers
- Increased resistance or impedance in the vias
- Reduced reliability and durability of the board
To prevent drilling and plating issues, manufacturers should:
- Use high-quality drilling and plating equipment with tight tolerances
- Optimize the drilling parameters (speed, feed rate, etc.) for each material and thickness
- Use appropriate plating chemistries and processes for the desired finish and performance
- Implement strict quality control measures to detect and correct drilling and plating defects
Problem 5: Solder Mask Defects
Solder mask is a protective coating applied to the surface of the PCB to prevent solder bridges and short circuits during assembly. However, solder mask can be susceptible to various defects that can affect the quality and reliability of the board, such as:
- Pinholes, cracks, or other openings in the solder mask
- Misalignment or registration errors in the solder mask pattern
- Contamination or impurities in the solder mask material
- Adhesion failures between the solder mask and the board surface
These defects can lead to issues such as:
- Solder bridges or short circuits during assembly
- Exposure of the copper traces to moisture, chemicals, or other contaminants
- Reduced protection and durability of the board surface
To prevent solder mask defects, manufacturers should:
- Use high-quality solder mask materials with good adhesion and coverage properties
- Employ precise registration and alignment techniques during solder mask application
- Control the curing and drying processes to ensure proper crosslinking and adhesion
- Implement strict quality control measures to detect and correct solder mask defects
Problem 6: Bow and Twist
Bow and twist are dimensional distortions that can occur in multilayer PCBs due to uneven stress distribution or material properties. These distortions can cause issues such as:
- Difficulty in assembly or mating with other components
- Reduced reliability and durability of the board
- Warpage or cracking of the board under thermal or mechanical stress
To prevent bow and twist, manufacturers should:
- Use materials with matched thermal expansion coefficients and mechanical properties
- Balance the copper distribution and orientation between layers to minimize stress gradients
- Control the lamination and curing processes to ensure even pressure and temperature distribution
- Implement strict quality control measures to detect and correct bow and twist issues
Problem 7: Electrical Testing Failures
Electrical testing is a critical step in the multilayer PCB fabrication process, ensuring that the board meets the required performance and reliability specifications. However, electrical testing can reveal various failures or defects, such as:
- Open or short circuits between layers or traces
- High resistance or impedance in the conductive pathways
- Signal integrity issues, such as crosstalk or reflections
- Insulation resistance or dielectric strength failures
These failures can be caused by various factors, such as:
- Manufacturing defects or process variations
- Design errors or inadequate simulation and verification
- Handling or environmental damage during testing or shipping
To prevent electrical testing failures, manufacturers should:
- Implement a robust design for manufacturing (DFM) process to identify and correct potential issues early in the design phase
- Use high-quality materials and processes throughout the fabrication process to minimize defects and variations
- Employ advanced electrical testing equipment and techniques to detect and diagnose failures
- Implement strict quality control measures to ensure that only boards that pass all electrical tests are shipped to customers
Conclusion
Multilayer PCB fabrication is a complex and challenging process that requires careful attention to detail and strict quality control measures. By understanding the common problems that can occur during fabrication, manufacturers can take proactive steps to prevent or mitigate these issues, ensuring the highest quality and reliability of their products.
Frequently Asked Questions (FAQ)
1. What is the most common problem in multilayer PCB fabrication?
Layer misalignment is one of the most common and critical problems in multilayer PCB fabrication. Misaligned layers can cause a range of issues, from short circuits to reduced signal integrity, and can be difficult to detect and correct once the board is assembled.
2. How can manufacturers prevent delamination in multilayer PCBs?
To prevent delamination, manufacturers should use high-quality adhesives and bonding materials, control the temperature and pressure during lamination, maintain a clean and controlled environment, and use gentle handling and packaging techniques.
3. What are the consequences of copper foil defects in multilayer PCBs?
Copper foil defects, such as pinholes, scratches, or contamination, can lead to increased resistance or impedance in the conductive pathways, reduced signal integrity and performance, and electrical failures due to open or short circuits.
4. How can manufacturers ensure accurate and consistent drilling and plating in multilayer PCBs?
To ensure accurate and consistent drilling and plating, manufacturers should use high-quality equipment with tight tolerances, optimize the drilling parameters for each material and thickness, use appropriate plating chemistries and processes, and implement strict quality control measures.
5. What are the benefits of implementing a robust design for manufacturing (DFM) process in multilayer PCB fabrication?
Implementing a robust DFM process can help identify and correct potential issues early in the design phase, reducing the risk of manufacturing defects, process variations, and electrical testing failures. This can lead to higher quality, reliability, and yield of the final product, as well as reduced costs and time to market.
Leave a Reply