Introduction to Impedance Control
Impedance control is a crucial aspect of designing and manufacturing high-speed electronic systems. It involves managing the impedance of transmission lines to ensure signal integrity and minimize signal distortion, reflections, and crosstalk. Proper impedance control is essential for maintaining signal quality, reducing electromagnetic interference (EMI), and ensuring reliable system performance.
In this article, we will explore ten effective ways to avoid signal integrity problems through impedance control. By following these guidelines, engineers and designers can optimize their designs, minimize signal degradation, and achieve robust and reliable electronic systems.
1. Understand the Basics of Impedance Matching
What is Impedance Matching?
Impedance matching is the practice of designing transmission lines and terminations to have the same impedance as the source and load impedances. When the impedances are matched, maximum power transfer occurs, and signal reflections are minimized. Mismatched impedances can lead to signal reflections, causing signal distortion, ringing, and other signal integrity issues.
Characteristic Impedance
The characteristic impedance (Z₀) of a transmission line is determined by its physical properties, such as the dielectric constant of the substrate, the width and thickness of the conductor, and the height of the dielectric. The characteristic impedance is given by the following equation:
Z₀ = √(L/C)
Where:
– L is the inductance per unit length
– C is the capacitance per unit length
To achieve impedance matching, the characteristic impedance of the transmission line should match the source and load impedances.
Termination Techniques
Proper termination is essential for impedance matching. There are several termination techniques commonly used in high-speed designs:
- Series Termination: A resistor is placed in series with the source to match the impedance of the transmission line.
- Parallel Termination: A resistor is placed in parallel with the load to match the impedance of the transmission line.
- AC Termination: A resistor and a capacitor are placed in series at the load to provide high-frequency termination while allowing DC bias.
- Differential Termination: Termination resistors are placed between the differential signal pairs to match the differential impedance.
Choosing the appropriate termination technique depends on factors such as the signal type, data rate, and power consumption requirements.
2. Consider the PCB Stack-up and Materials
PCB Stack-up
The PCB stack-up plays a crucial role in impedance control. The number of layers, their arrangement, and the dielectric materials used can significantly impact the impedance of the transmission lines. When designing the PCB stack-up, consider the following:
- Use a consistent dielectric material with a known dielectric constant (Dk) and dissipation factor (Df).
- Minimize the number of different dielectric materials in the stack-up to reduce impedance variations.
- Maintain a symmetrical stack-up to ensure balanced impedances for differential pairs.
- Use appropriate layer spacing and trace widths to achieve the desired impedance.
Dielectric Materials
The choice of dielectric materials is critical for impedance control. The dielectric constant (Dk) and dissipation factor (Df) of the material determine the impedance and signal loss characteristics. Common dielectric materials used in PCBs include:
- FR-4: A popular and cost-effective dielectric material with a Dk of approximately 4.5.
- Rogers: High-performance dielectric materials with lower Dk values and better high-frequency performance.
- Isola: A range of dielectric materials with varying Dk values and performance characteristics.
When selecting a dielectric material, consider the operating frequency, signal speeds, and cost requirements of the design.
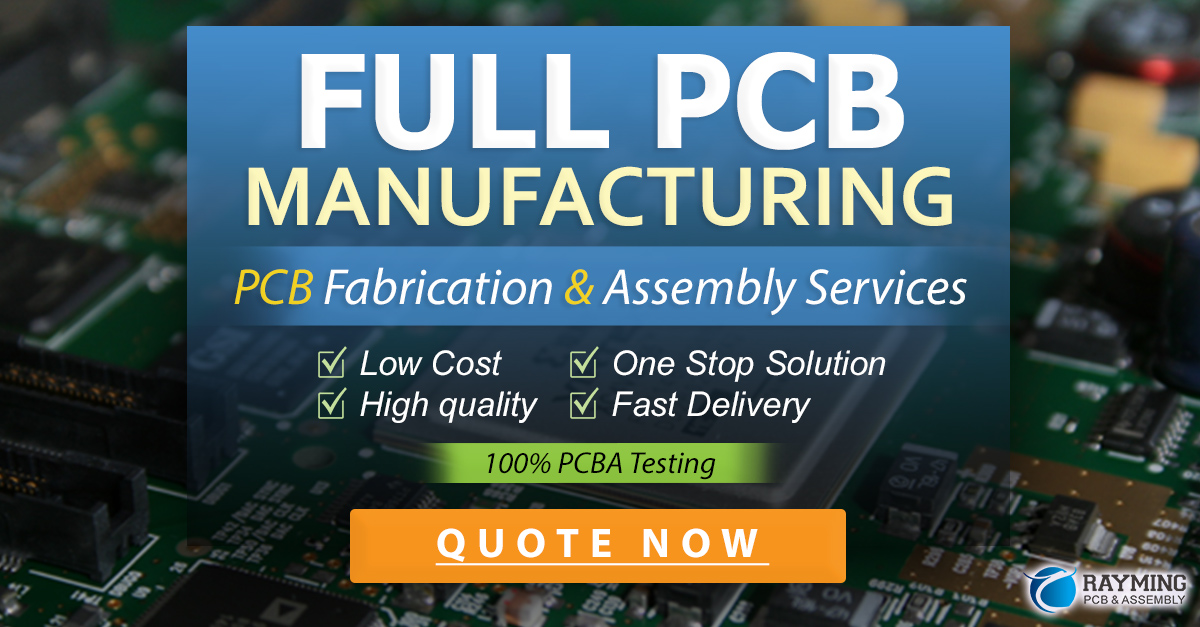
3. Optimize Trace Geometry
Trace Width and Spacing
The width and spacing of traces on the PCB have a direct impact on impedance. Wider traces have lower impedance, while narrower traces have higher impedance. The spacing between traces also affects the coupling capacitance and can influence the impedance.
To achieve the desired impedance, use PCB design tools and impedance calculators to determine the appropriate trace width and spacing. Consider the following guidelines:
- Use consistent trace widths for signals with the same impedance requirements.
- Maintain adequate spacing between traces to minimize crosstalk and coupling.
- Follow the manufacturer’s recommendations for trace width and spacing based on the chosen dielectric material and copper thickness.
Microstrip and Stripline Traces
Microstrip and stripline traces are commonly used in PCB designs for controlled impedance. Microstrip traces are routed on the outer layers of the PCB, with a ground plane beneath them. Stripline traces are routed on the inner layers, sandwiched between two ground planes.
Microstrip traces have higher impedance compared to stripline traces of the same width. Stripline traces offer better shielding and reduced EMI, but they require more complex routing and may have limited access for probing.
Consider the following when using microstrip and stripline traces:
- Use microstrip traces for outer layer routing and stripline traces for inner layer routing.
- Maintain a consistent dielectric thickness between the trace and the reference plane.
- Use ground planes adjacent to the signal layers to provide a low-impedance return path.
Trace Length Matching
Trace length matching is essential for maintaining signal integrity in high-speed designs. Mismatched trace lengths can lead to timing skew, signal reflections, and other signal integrity issues.
To ensure proper trace length matching:
- Route signals with the same length to maintain consistent propagation delays.
- Use serpentine routing or meandering techniques to adjust trace lengths when necessary.
- Minimize the difference in trace lengths within a group of related signals.
- Consider the velocity factor of the dielectric material when calculating trace lengths.
4. Implement Proper Grounding and Shielding
Ground Planes
Ground planes play a crucial role in impedance control and signal integrity. They provide a low-impedance return path for signals and help to minimize EMI and crosstalk. When implementing ground planes:
- Use a continuous and uninterrupted ground plane whenever possible.
- Avoid splitting the ground plane unnecessarily, as it can create impedance discontinuities.
- Use multiple vias to connect ground planes across different layers to minimize impedance mismatch.
- Keep the ground plane as close to the signal layer as possible to minimize loop area and inductance.
Shielding Techniques
Shielding is an effective way to reduce EMI and crosstalk between signals. Various shielding techniques can be employed in PCB designs:
- Copper Pour: Use a copper pour on unused areas of the PCB to provide additional shielding and reduce impedance variations.
- Guard Traces: Place grounded guard traces adjacent to sensitive signals to provide localized shielding.
- Shielded Cables: Use shielded cables for off-board connections to minimize EMI and ensure signal integrity.
- Shielding Cans: Implement shielding cans over sensitive components or regions of the PCB to reduce EMI and crosstalk.
Via Stitching
Via stitching is a technique used to create a low-impedance connection between ground planes on different layers. By placing vias at regular intervals along the edges of the ground planes, a continuous and low-impedance path is established.
When implementing via stitching:
- Place vias at a regular pitch along the edges of the ground planes.
- Use a sufficient number of vias to minimize impedance discontinuities.
- Keep the via size and drill hole size consistent to maintain impedance control.
- Consider the current carrying capacity of the vias when determining the via size and spacing.
5. Manage Discontinuities and Transitions
Impedance Discontinuities
Impedance discontinuities occur when there is an abrupt change in the impedance of a transmission line. These discontinuities can cause signal reflections, ringing, and other signal integrity issues. Common sources of impedance discontinuities include:
- Vias: Vias introduce inductance and can cause impedance mismatches if not properly designed.
- Connectors: Connectors can introduce impedance discontinuities due to their geometry and contact resistance.
- Layer Transitions: Transitions between different layers of the PCB can create impedance discontinuities if not managed properly.
- Trace Width Changes: Abrupt changes in trace width can lead to impedance discontinuities.
To manage impedance discontinuities:
- Minimize the use of vias whenever possible, especially in high-speed signal paths.
- Use impedance-matched connectors and carefully design the connector footprints to maintain impedance control.
- Ensure smooth transitions between layers by using appropriate via sizes and placement.
- Avoid abrupt changes in trace width and use tapered transitions when necessary.
Managing Layer Transitions
Layer transitions are inevitable in multi-layer PCB designs. Proper management of layer transitions is crucial for maintaining signal integrity and minimizing impedance discontinuities. Consider the following techniques:
- Via-in-Pad: Place vias directly in the component pads to minimize the stub length and reduce impedance discontinuities.
- Blind and Buried Vias: Use blind and buried vias to minimize the stub length and improve signal integrity in high-speed designs.
- Backdrilling: Remove the unused portion of the via barrel to reduce the stub length and minimize impedance discontinuities.
- Impedance Matching: Use impedance matching techniques, such as series termination or capacitive compensation, to match the impedance at layer transitions.
Impedance Matching at Connectors
Connectors are critical points in a system where impedance discontinuities can occur. To maintain signal integrity, it is essential to ensure proper impedance matching at connectors. Consider the following:
- Use connectors with a characteristic impedance that matches the transmission line impedance.
- Design the connector footprints and landing pads to maintain the desired impedance.
- Use ground pins or shielding in connectors to provide a low-impedance return path and minimize crosstalk.
- Carefully route traces to and from the connectors to avoid impedance discontinuities.
6. Simulate and Analyze Signal Integrity
Signal Integrity Simulation
Signal integrity simulation is a powerful tool for analyzing and optimizing PCB designs for impedance control and signal quality. By simulating the behavior of signals in the PCB, designers can identify potential issues and make necessary adjustments before fabrication.
Signal integrity simulation tools, such as Hyperlynx, Sigrity, and Ansys SIwave, allow designers to:
- Model the PCB stack-up and trace geometry to accurately represent the impedance characteristics.
- Analyze the signal propagation, reflections, and crosstalk in the PCB.
- Identify impedance discontinuities, signal integrity issues, and EMI problems.
- Optimize the design by adjusting trace widths, spacing, and termination strategies.
When performing signal integrity simulations:
- Use accurate models of the PCB stack-up, materials, and components.
- Define the appropriate simulation parameters, such as rise/fall times, data rates, and voltage levels.
- Analyze critical signals and bus interfaces to ensure signal integrity.
- Validate the simulation results against the design requirements and make necessary adjustments.
Time-Domain Reflectometry (TDR)
Time-Domain Reflectometry (TDR) is a technique used to measure and characterize impedance discontinuities in transmission lines. TDR sends a fast-rising pulse down the transmission line and measures the reflections caused by impedance mismatches.
TDR can be used to:
- Locate impedance discontinuities in the PCB, such as vias, connectors, and trace width changes.
- Measure the characteristic impedance of transmission lines.
- Determine the delay and velocity of propagation in the transmission lines.
- Optimize the design by adjusting trace geometries and termination strategies based on TDR measurements.
When using TDR for impedance control:
- Use a high-quality TDR instrument with sufficient bandwidth and resolution.
- Calibrate the TDR instrument to ensure accurate measurements.
- Perform TDR measurements on critical signals and interfaces to identify impedance discontinuities.
- Analyze the TDR results and make necessary adjustments to the PCB design to improve impedance control.
7. Consider High-Speed Design Techniques
Differential Signaling
Differential signaling is a technique commonly used in high-speed designs to improve signal integrity and reduce EMI. In differential signaling, a pair of signals with equal and opposite amplitudes are transmitted over two separate traces.
Differential signaling offers several advantages:
- Improved noise immunity: Differential signals are less susceptible to common-mode noise and interference.
- Reduced EMI: The equal and opposite currents in differential pairs cancel out each other’s electromagnetic fields, reducing EMI.
- Higher data rates: Differential signaling allows for higher data rates compared to single-ended signaling.
When implementing differential signaling:
- Route differential pairs with matched trace lengths to minimize skew.
- Maintain a constant spacing between the traces of a differential pair to ensure consistent differential impedance.
- Use appropriate termination techniques, such as differential termination, to match the differential impedance.
- Consider the use of tightly coupled differential pairs or serpentine routing to minimize differential impedance variations.
Equalization Techniques
Equalization techniques are used to compensate for the frequency-dependent losses and dispersion in transmission lines. Equalization helps to improve signal integrity and extend the maximum data rates achievable over long transmission lines.
Common equalization techniques include:
- Pre-emphasis: The transmitter boosts the high-frequency components of the signal to compensate for the frequency-dependent losses in the transmission line.
- De-emphasis: The transmitter attenuates the low-frequency components of the signal to balance the frequency response of the transmission line.
- Continuous Time Linear Equalization (CTLE): An analog equalizer that provides frequency-dependent gain to compensate for the losses in the transmission line.
- Decision Feedback Equalization (DFE): A digital equalizer that uses the previously received symbols to cancel out the intersymbol interference (ISI) caused by the transmission line.
When considering equalization techniques:
- Analyze the frequency response of the transmission line to determine the appropriate equalization strategy.
- Consider the data rate, transmission line length, and signal integrity requirements when selecting the equalization technique.
- Implement equalization at both the transmitter and receiver ends of the transmission line for optimal performance.
- Validate the equalization settings through simulations and measurements to ensure signal integrity.
Spread Spectrum Clocking
Spread spectrum clocking (SSC) is a technique used to reduce EMI in high-speed designs. SSC modulates the clock frequency over a small range, typically less than 1%, to spread the energy of the clock harmonics over a wider frequency range.
The benefits of spread spectrum clocking include:
- Reduced peak EMI: By spreading the energy of the clock harmonics, the peak EMI levels are reduced, making it easier to meet EMI regulations.
- Improved electromagnetic compatibility (EMC): SSC helps to minimize the interference caused by clock harmonics on nearby sensitive circuits.
When implementing spread spectrum clocking:
- Use a clock generator or synthesizer that supports SSC modulation.
- Choose an appropriate modulation profile, such as triangular or Hershey-kiss, based on the EMI reduction requirements.
- Consider the impact of SSC on timing margins and ensure that the system can tolerate the slight variations in clock frequency.
- Verify the effectiveness of SSC through EMI measurements and compliance testing.
8. Implement Robust Power Distribution Network (PDN)
Decoupling Capacitors
Decoupling capacitors are essential components in a robust power distribution network (PDN). They provide a local source of charge to the integrated circuits (ICs) and help to stabilize the power supply voltage by reducing voltage fluctuations caused by sudden changes in current demand.
When placing decoupling capacitors:
- Place decoupling capacitors as close as possible to the power pins of the ICs to minimize the inductance in the power path.
- Use a combination of bulk, ceramic, and small-value capacitors to provide decoupling over a wide frequency range.
- Consider the resonant frequency of the decoupling capacitors and choose values that provide optimal decoupling at the relevant frequencies.
- Use simulation tools to analyze the PDN impedance and optimize the placement and values of decoupling capacitors.
Power Plane Partitioning
Power plane partitioning is a technique used to isolate different power domains and reduce noise coupling between them. By partitioning the power plane into separate regions, each with its own power supply and ground connection, the noise generated by one power domain is less likely to affect the other domains.
When partitioning power planes:
- Identify the different power domains in the design, such as analog, digital, and RF sections.
- Assign separate power and ground planes to each power domain to provide isolation.
- Use appropriate isolation techniques, such as split planes or moats, to minimize noise coupling between the power domains.
- Place decoupling capacitors near the boundary of each power domain to provide local decoupling and reduce noise propagation.
Impedance Control in Power Distribution
Impedance control is not only important for signal integrity but also for power integrity. A low-impedance power distribution network is essential for providing a stable and clean power supply to the ICs
Leave a Reply