Introduction to PCB impedance Control
Printed Circuit Board (PCB) impedance control is a critical aspect of modern electronics design, particularly in high-speed and high-frequency applications. Impedance control ensures that the signals propagating through the PCB traces maintain their integrity, minimizing signal reflections, crosstalk, and other undesirable effects. This article will provide 10 essential tips for achieving advanced requirements impedance control in PCB design.
Understanding Impedance and Its Importance in PCB Design
Impedance is a measure of the opposition that a circuit presents to a current when a voltage is applied. In PCB design, impedance control refers to the process of managing the impedance of the traces to ensure proper signal propagation. Failing to control impedance can lead to signal integrity issues, such as reflections, crosstalk, and signal distortion, which can compromise the performance and reliability of the PCB.
Types of Impedance in PCB Design
There are two main types of impedance in PCB design:
-
Characteristic Impedance: This is the impedance of a transmission line, such as a PCB trace, when it is infinitely long. It is determined by the geometry and materials of the trace and the surrounding dielectric.
-
Differential Impedance: This is the impedance between two coupled traces, such as a differential pair. It is important for maintaining signal integrity in high-speed differential signaling applications.
Tip 1: Choose the Right Dielectric Material
The dielectric material surrounding the PCB traces plays a crucial role in determining the impedance of the traces. The dielectric constant (Dk) and the loss tangent (Df) of the material are the key properties that influence impedance. When selecting a dielectric material for impedance control, consider the following:
- Low Dk materials, such as Rogers RO4003C or Isola IS410, are preferred for high-speed applications as they reduce the capacitance between the traces and the reference plane, resulting in lower impedance.
- Low Df materials help minimize signal attenuation and maintain signal integrity over longer distances.
Material | Dielectric Constant (Dk) | Loss Tangent (Df) |
---|---|---|
FR-4 | 4.2 – 4.5 | 0.02 |
Rogers RO4003C | 3.38 | 0.0027 |
Isola IS410 | 3.65 | 0.0090 |
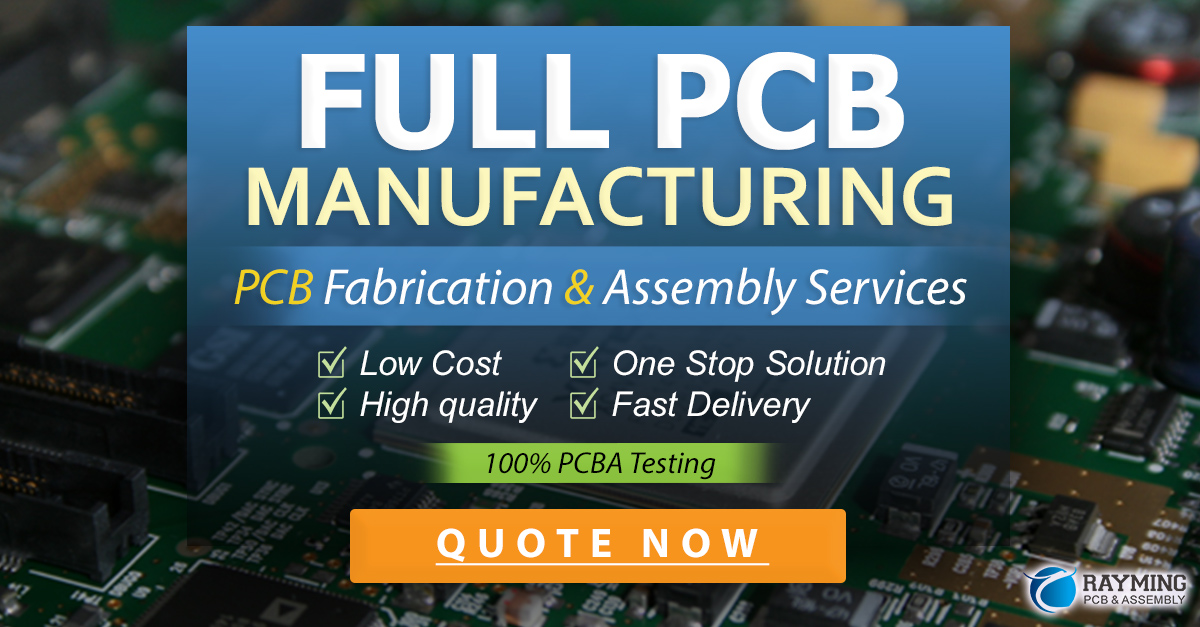
Tip 2: Optimize Trace Geometry
The geometry of the PCB traces, including their width, thickness, and spacing, directly affects their impedance. To achieve the desired impedance, follow these guidelines:
- Use a PCB Stack-up calculator or impedance calculator to determine the appropriate trace width and spacing for your target impedance.
- Maintain a consistent trace width throughout the length of the signal path to avoid impedance discontinuities.
- Consider using differential pairs for high-speed signals, as they offer better noise immunity and signal integrity compared to single-ended traces.
Impedance (Ω) | Trace Width (mil) | Trace Spacing (mil) |
---|---|---|
50 | 15 | 10 |
75 | 10 | 15 |
100 | 8 | 20 |
Tip 3: Implement Proper Grounding and Power Distribution
A solid grounding strategy and proper power distribution are essential for maintaining impedance control and signal integrity. Follow these best practices:
- Use a continuous ground plane beneath the signal traces to provide a stable reference for the signals.
- Implement a grid-like power distribution network with decoupling capacitors to minimize power supply noise and maintain a stable reference voltage.
- Avoid splitting the ground plane or creating slots or gaps, as they can introduce impedance discontinuities and degrade signal integrity.
Tip 4: Minimize Discontinuities and Reflections
Discontinuities in the signal path, such as vias, connectors, or changes in trace geometry, can cause reflections and degrade signal integrity. To minimize these effects:
- Use a minimum number of vias and place them strategically to avoid creating stubs.
- Ensure proper impedance matching when transitioning between different layers or trace geometries.
- Implement proper termination techniques, such as series termination or parallel termination, to minimize reflections at the source or load end of the signal path.
Tip 5: Employ Simulation and Modeling Techniques
Simulation and modeling tools can help you analyze and optimize your PCB design for impedance control before fabrication. Consider the following:
- Use a 2D or 3D electromagnetic (EM) simulator to accurately model the PCB traces and predict their impedance.
- Perform time-domain reflectometry (TDR) simulations to identify impedance discontinuities and optimize the signal path.
- Analyze the frequency response of the PCB traces using S-parameter simulations to ensure proper signal propagation and minimize losses.
Tip 6: Follow High-Speed Design Guidelines
When designing high-speed PCBs with strict impedance control requirements, adhere to the following guidelines:
- Route high-speed signals on inner layers, surrounded by ground planes, to minimize crosstalk and electromagnetic interference (EMI).
- Avoid routing high-speed traces parallel to each other for long distances to reduce crosstalk.
- Use serpentine routing or add meanders to match the trace lengths of differential pairs or bus lines.
Tip 7: Consider the Effects of Manufacturing Tolerances
Manufacturing tolerances can impact the impedance of PCB traces. To account for these variations:
- Specify controlled impedance requirements in your PCB fabrication files, including the target impedance, tolerance, and test method.
- Work with your PCB fabricator to understand their manufacturing capabilities and tolerances.
- Design your traces with sufficient margin to accommodate manufacturing variations without exceeding the impedance tolerance.
Tip 8: Implement Impedance Matching Techniques
Impedance matching is crucial for ensuring proper signal transmission between the source, transmission line, and load. Some common impedance matching techniques include:
- Series termination: Adding a resistor in series with the source to match the source impedance to the transmission line impedance.
- Parallel termination: Adding a resistor in parallel with the load to match the load impedance to the transmission line impedance.
- AC termination: Using a resistor and a capacitor in series to match the impedance over a specific frequency range.
Tip 9: Perform Impedance Testing and Validation
After PCB fabrication, it is essential to perform impedance testing and validation to ensure that the manufactured board meets the specified impedance requirements. Common impedance testing methods include:
- Time-Domain Reflectometry (TDR): Measuring the impedance profile of a trace by sending a fast rise time pulse and analyzing the reflections.
- Impedance Test Coupons: Designing dedicated test traces on the PCB that can be probed to measure the impedance.
- Vector Network Analyzer (VNA): Measuring the S-parameters of the PCB traces to characterize their impedance and frequency response.
Tip 10: Collaborate with Experienced PCB Design and Fabrication Partners
Engaging with experienced PCB design and fabrication partners can greatly benefit your impedance control efforts. These partners can provide valuable insights, advice, and support throughout the design and manufacturing process. When selecting a partner, consider the following:
- Look for companies with a proven track record in designing and manufacturing high-speed, impedance-controlled PCBs.
- Ensure that they have the necessary expertise, tools, and manufacturing capabilities to meet your specific requirements.
- Establish clear communication channels and collaborate closely with your partners to optimize your design and resolve any issues promptly.
Frequently Asked Questions (FAQ)
1. What is the difference between characteristic impedance and differential impedance?
Characteristic impedance refers to the impedance of a single transmission line, such as a PCB trace, when it is infinitely long. It is determined by the geometry and materials of the trace and the surrounding dielectric. Differential impedance, on the other hand, is the impedance between two coupled traces, such as a differential pair. It is important for maintaining signal integrity in high-speed differential signaling applications.
2. How does the dielectric material affect PCB impedance?
The dielectric material surrounding the PCB traces plays a crucial role in determining the impedance of the traces. The dielectric constant (Dk) and the loss tangent (Df) of the material are the key properties that influence impedance. Low Dk materials reduce the capacitance between the traces and the reference plane, resulting in lower impedance, while low Df materials help minimize signal attenuation and maintain signal integrity over longer distances.
3. What are some common impedance matching techniques?
Common impedance matching techniques include series termination, parallel termination, and AC termination. Series termination involves adding a resistor in series with the source to match the source impedance to the transmission line impedance. Parallel termination involves adding a resistor in parallel with the load to match the load impedance to the transmission line impedance. AC termination uses a resistor and a capacitor in series to match the impedance over a specific frequency range.
4. How can I test and validate the impedance of my PCB?
There are several methods for testing and validating the impedance of a PCB. Time-Domain Reflectometry (TDR) involves measuring the impedance profile of a trace by sending a fast rise time pulse and analyzing the reflections. Impedance test coupons are dedicated test traces on the PCB that can be probed to measure the impedance. A Vector Network Analyzer (VNA) can be used to measure the S-parameters of the PCB traces to characterize their impedance and frequency response.
5. Why is it important to collaborate with experienced PCB design and fabrication partners?
Collaborating with experienced PCB design and fabrication partners can provide valuable insights, advice, and support throughout the design and manufacturing process. These partners have the necessary expertise, tools, and manufacturing capabilities to help you optimize your design, meet your specific requirements, and resolve any issues promptly. Engaging with experienced partners can ultimately lead to better impedance control, improved signal integrity, and higher-quality PCBs.
Conclusion
Achieving advanced requirements impedance control in PCB design requires careful consideration of various factors, including material selection, trace geometry, grounding and power distribution, discontinuities, simulation and modeling, high-speed design guidelines, manufacturing tolerances, impedance matching, testing and validation, and collaboration with experienced partners.
By following the 10 tips outlined in this article, you can effectively manage impedance in your PCB designs, ensuring proper signal propagation, minimizing signal integrity issues, and ultimately creating high-performance, reliable electronic products. Remember to continuously learn, stay updated with the latest industry trends and best practices, and engage with the PCB design community to further enhance your impedance control skills and knowledge.
Leave a Reply