Introduction to Low-Cost PCB Manufacturing in China
China has emerged as a global hub for low-cost PCB manufacturing, offering businesses and individuals the opportunity to produce high-quality printed circuit boards at competitive prices. In this comprehensive article, we will explore ten key factors that contribute to achieving low-cost PCB Production in China, helping you navigate the process and optimize your manufacturing outcomes.
1. Selecting the Right PCB Manufacturer
1.1 Research and Due Diligence
When looking for a low-cost PCB manufacturer in China, it is essential to conduct thorough research and perform due diligence. Start by creating a list of potential manufacturers and evaluate their reputation, experience, and customer reviews. Look for manufacturers with a proven track record of delivering high-quality PCBs at competitive prices.
1.2 Certifications and Standards
Ensure that the PCB manufacturer you choose adheres to industry standards and holds relevant certifications, such as ISO 9001, ISO 14001, and UL. These certifications demonstrate the manufacturer’s commitment to quality, environmental responsibility, and safety, which are crucial factors in achieving low-cost PCB production without compromising on quality.
1.3 Communication and Support
Effective communication is key to successful low-cost PCB manufacturing in China. Look for manufacturers that offer responsive and reliable support, with dedicated sales representatives who can address your queries and concerns promptly. Clear communication helps prevent misunderstandings, reduces lead times, and ensures that your PCB design requirements are accurately translated into the final product.
2. Optimizing PCB Design for Cost-Effectiveness
2.1 Design for Manufacturability (DFM)
To achieve low-cost PCB production in China, it is crucial to optimize your PCB design for manufacturability. Implement DFM principles, such as using standard component sizes, minimizing the number of layers, and avoiding unnecessary complexity in the design. By designing with manufacturing in mind, you can reduce production costs, improve yields, and minimize the risk of defects.
2.2 Component Selection and Sourcing
Carefully select components for your PCB design, considering factors such as availability, cost, and compatibility. Whenever possible, opt for readily available, off-the-shelf components to reduce lead times and minimize sourcing costs. Additionally, consider sourcing components directly from China, as many Chinese PCB Manufacturers have established relationships with local component suppliers, enabling them to secure competitive pricing.
2.3 Panelization and Routing
Optimize your PCB design for panelization and routing to maximize manufacturing efficiency and reduce costs. Group multiple PCB designs onto a single panel to minimize material waste and optimize production throughput. Implement efficient routing techniques, such as using the smallest possible trace widths and spacing, to reduce the overall PCB size and minimize the amount of copper required.
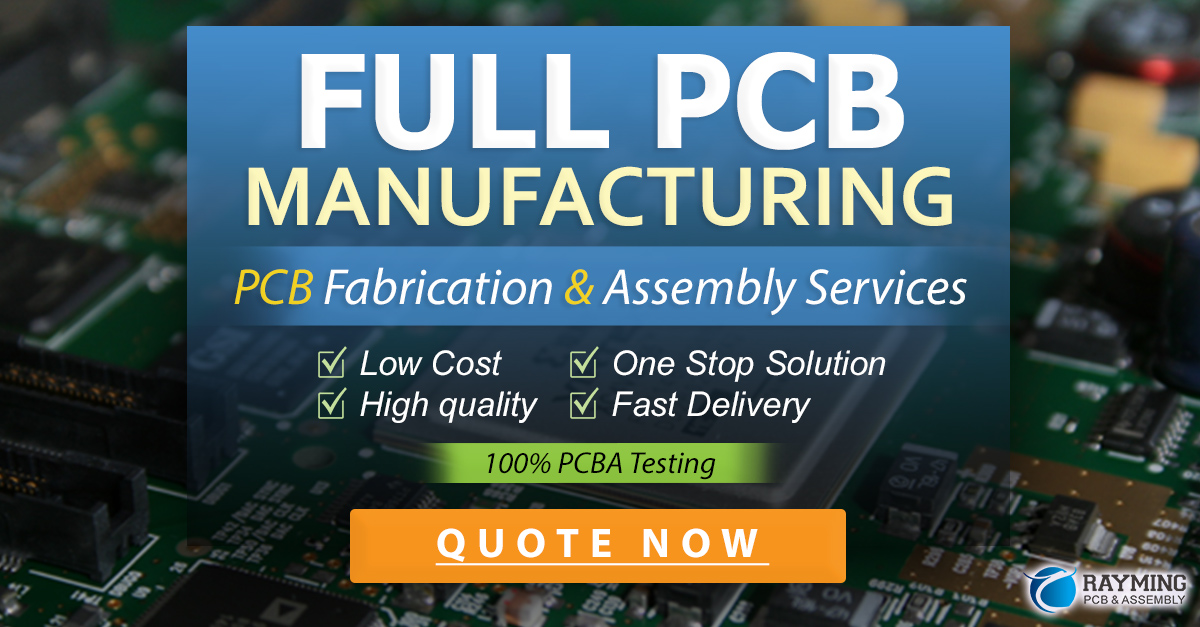
3. Material Selection and Cost Optimization
3.1 PCB Substrate Materials
Choose the most cost-effective PCB substrate material that meets your design requirements. Common substrate materials include FR-4, aluminum, and flexible substrates. FR-4 is the most widely used and cost-effective option for general-purpose PCBs. However, if your application requires specific properties, such as high thermal conductivity or flexibility, consider alternative materials that offer the best balance between performance and cost.
3.2 Copper Weight and Thickness
Select the appropriate copper weight and thickness for your PCB design to optimize cost and performance. Thinner copper layers, such as 1 oz or 0.5 oz, are generally more cost-effective than thicker layers. However, consider the current-carrying requirements of your design and choose a copper thickness that provides adequate conductivity while minimizing costs.
3.3 Surface Finish Options
Choose a cost-effective surface finish that meets your design requirements and protects the exposed copper on your PCB. Common surface finishes include Hot Air Solder Leveling (HASL), Immersion Tin, and Organic Solderability Preservative (OSP). HASL is often the most cost-effective option, while Immersion Tin and OSP offer improved solderability and flatness at a slightly higher cost.
4. Leveraging Economies of Scale
4.1 Batch Size Optimization
To achieve low-cost PCB production in China, consider optimizing your batch sizes to leverage economies of scale. Larger batch sizes often result in lower per-unit costs, as fixed costs such as setup and tooling are spread across a greater number of PCBs. Work with your Chinese PCB manufacturer to determine the most cost-effective batch size for your specific design and production requirements.
4.2 Standardization and Reusability
Standardize your PCB designs whenever possible to maximize reusability and reduce costs. By using common component footprints, layer stackups, and design rules across multiple projects, you can minimize the need for custom tooling and streamline the manufacturing process. This approach also allows you to maintain a stock of frequently used components, reducing lead times and enabling faster production cycles.
4.3 Volume Discounts and Long-Term Contracts
Negotiate volume discounts and establish long-term contracts with your Chinese PCB manufacturer to secure the most competitive pricing. Many manufacturers offer tiered pricing structures based on order quantities, with higher volumes yielding lower per-unit costs. Additionally, entering into long-term contracts can provide price stability, ensuring consistent low-cost PCB production over an extended period.
5. Quality Control and Testing
5.1 In-Process Inspections
To ensure the quality of your low-cost PCBs from China, work with a manufacturer that implements robust in-process inspections. These inspections should be carried out at critical stages of the manufacturing process, such as after solder mask application, legend printing, and final assembly. By identifying and addressing potential issues early in the process, manufacturers can minimize defects and reduce the overall cost of quality.
5.2 Automated Optical Inspection (AOI)
Ensure that your Chinese PCB manufacturer utilizes Automated Optical Inspection (AOI) technology to detect surface-level defects, such as solder bridges, missing components, and incorrect component placement. AOI systems can quickly and accurately inspect PCBs, reducing the need for manual inspection and minimizing the risk of human error. This technology helps maintain high quality standards while keeping costs low.
5.3 Electrical Testing
Verify that your Chinese PCB manufacturer conducts thorough electrical testing to ensure the functionality and reliability of your PCBs. This may include in-circuit testing (ICT), Flying Probe testing, and boundary scan testing, depending on the complexity of your design. By identifying and addressing electrical issues before the PCBs leave the factory, manufacturers can minimize the risk of field failures and associated costs.
6. Inventory Management and Logistics
6.1 Just-in-Time (JIT) Manufacturing
Implement Just-in-Time (JIT) manufacturing principles to minimize inventory costs and reduce the risk of obsolescence. Work with your Chinese PCB manufacturer to establish a lean production system that aligns with your demand forecasts and delivery schedules. By producing PCBs only when needed, you can reduce the amount of capital tied up in inventory and minimize storage and handling costs.
6.2 Freight and Shipping Optimization
Optimize your freight and shipping strategies to minimize transportation costs and lead times. Consider factors such as shipment consolidation, mode of transportation (e.g., air, sea, or land), and customs clearance requirements. Work with your Chinese PCB manufacturer to identify the most cost-effective and reliable shipping options, taking into account your specific delivery requirements and budget constraints.
6.3 Local Warehousing and Distribution
Explore the possibility of establishing local warehousing and distribution capabilities in China to reduce shipping costs and improve delivery times. By storing finished PCBs in a local warehouse, you can quickly fulfill customer orders and minimize the need for international shipping. Additionally, local distribution can help you navigate complex import/export regulations and streamline the customs clearance process.
7. Intellectual Property Protection
7.1 Non-Disclosure Agreements (NDAs)
Protect your intellectual property when working with Chinese PCB manufacturers by establishing robust Non-Disclosure Agreements (NDAs). These agreements should clearly outline the confidentiality obligations of both parties and specify the measures to be taken to safeguard sensitive information, such as PCB designs, bill of materials (BOM), and manufacturing processes. Ensure that the NDA is legally enforceable in both China and your home country.
7.2 Secure Data Transfer and Storage
Implement secure data transfer and storage protocols to minimize the risk of intellectual property theft. Use encrypted communication channels, such as virtual private networks (VPNs) or secure file transfer protocols (SFTP), when exchanging sensitive information with your Chinese PCB manufacturer. Additionally, store your PCB design files and related data on secure, access-controlled servers to prevent unauthorized access.
7.3 Audits and Compliance Monitoring
Conduct regular audits and compliance monitoring to ensure that your Chinese PCB manufacturer adheres to the agreed-upon intellectual property protection measures. This may involve on-site visits, document reviews, and interviews with key personnel. By actively monitoring your manufacturer’s compliance with IP protection requirements, you can identify and address potential risks before they escalate into costly legal disputes.
8. Environmental and Social Responsibility
8.1 RoHS and REACH Compliance
Ensure that your Chinese PCB manufacturer complies with international environmental regulations, such as the Restriction of Hazardous Substances (RoHS) Directive and the Registration, Evaluation, Authorization, and Restriction of Chemicals (REACH) Regulation. These regulations restrict the use of hazardous substances in electronic products and promote environmentally friendly manufacturing practices. By working with a compliant manufacturer, you can minimize the environmental impact of your PCBs and avoid potential legal and reputational risks.
8.2 Waste Management and Recycling
Choose a Chinese PCB manufacturer that implements effective waste management and recycling practices. This may include the proper handling and disposal of hazardous materials, such as lead and other heavy metals, as well as the recycling of scrap materials and production byproducts. By minimizing waste and maximizing resource efficiency, manufacturers can reduce their environmental footprint and lower overall production costs.
8.3 Fair Labor Practices and Working Conditions
Verify that your Chinese PCB manufacturer adheres to fair labor practices and provides safe and healthy working conditions for their employees. This includes compliance with local labor laws, minimum wage requirements, and occupational health and safety standards. By partnering with a socially responsible manufacturer, you can ensure that your low-cost PCBs are produced in an ethical and sustainable manner, minimizing the risk of reputational damage and supply chain disruptions.
9. Continuous Improvement and Innovation
9.1 Process Optimization and Automation
Work with a Chinese PCB manufacturer that embraces continuous improvement and invests in process optimization and automation. By streamlining production processes, implementing lean manufacturing principles, and adopting advanced manufacturing technologies, such as automated assembly lines and robotic systems, manufacturers can reduce waste, improve efficiency, and lower production costs over time.
9.2 Design for Excellence (DFX)
Collaborate with your Chinese PCB manufacturer to implement Design for Excellence (DFX) principles, which encompass Design for Manufacturability (DFM), Design for Assembly (DFA), and Design for Testing (DFT). By optimizing your PCB designs for each stage of the manufacturing process, you can reduce the risk of defects, improve yields, and minimize production costs. Regularly review and refine your designs based on feedback from your manufacturer and real-world performance data.
9.3 Technology Roadmapping and Future-Proofing
Engage with your Chinese PCB manufacturer to develop a technology roadmap that aligns with your long-term business objectives and industry trends. By staying informed about emerging technologies, materials, and manufacturing processes, you can future-proof your PCB designs and ensure that your products remain competitive in the market. Regularly review and update your technology roadmap to reflect changes in customer requirements, regulatory standards, and market conditions.
10. Building Strong Partnerships
10.1 Clear Communication and Collaboration
Foster strong partnerships with your Chinese PCB manufacturer through clear communication and collaboration. Establish regular communication channels, such as weekly or monthly conference calls, to discuss project progress, address challenges, and share insights. Encourage open and transparent dialogue to build trust and resolve issues quickly. Consider appointing a dedicated liaison or project manager to facilitate communication and ensure that all stakeholders are aligned.
10.2 Cultural Awareness and Sensitivity
When working with Chinese PCB manufacturers, it is essential to develop cultural awareness and sensitivity. Take the time to understand Chinese business etiquette, communication styles, and decision-making processes. Show respect for local customs and traditions, and be mindful of potential language barriers. By building strong, culturally sensitive relationships with your Chinese partners, you can foster a more collaborative and effective working environment.
10.3 Long-Term Commitment and Mutual Benefit
Approach your partnership with a Chinese PCB manufacturer as a long-term commitment based on mutual benefit. Recognize that building a successful, low-cost PCB Supply Chain requires ongoing investment in the relationship, including regular visits, knowledge sharing, and joint problem-solving. By demonstrating a genuine commitment to your manufacturer’s success and working together to achieve shared goals, you can create a more resilient and profitable partnership over time.
Conclusion
Achieving low-cost PCB manufacturing in China requires a comprehensive approach that takes into account a wide range of factors, from manufacturer selection and design optimization to quality control, logistics, and intellectual property protection. By carefully considering each of these factors and implementing best practices in partnership with your Chinese PCB manufacturer, you can unlock significant cost savings while maintaining high quality standards and mitigating potential risks.
As you embark on your low-cost PCB manufacturing journey in China, remember that success is built on a foundation of clear communication, cultural sensitivity, and long-term commitment. By fostering strong, mutually beneficial relationships with your Chinese partners and continuously improving your processes and designs, you can create a sustainable competitive advantage and achieve your business objectives in the dynamic and ever-evolving world of PCB manufacturing.
Frequently Asked Questions (FAQ)
-
Q: How can I ensure the quality of low-cost PCBs manufactured in China?
A: To ensure the quality of low-cost PCBs from China, work with a reputable manufacturer that adheres to industry standards, implements robust quality control processes, and utilizes advanced inspection and testing technologies. Regularly monitor your manufacturer’s performance and conduct on-site audits to verify compliance with your quality requirements. -
Q: What are the key considerations when selecting a Chinese PCB manufacturer?
A: When selecting a Chinese PCB manufacturer, consider factors such as reputation, experience, certifications, communication capabilities, and support services. Conduct thorough research and due diligence to ensure that the manufacturer can meet your specific requirements for quality, cost, and delivery. -
Q: How can I protect my intellectual property when working with a Chinese PCB manufacturer?
A: To protect your intellectual property, establish robust Non-Disclosure Agreements (NDAs), implement secure data transfer and storage protocols, and conduct regular audits and compliance monitoring. Work with a manufacturer that demonstrates a strong commitment to intellectual property protection and has a proven track record of safeguarding sensitive information. -
Q: What are some strategies for optimizing PCB design for low-cost manufacturing in China?
A: To optimize your PCB design for low-cost manufacturing, implement Design for Manufacturability (DFM) principles, select cost-effective components and materials, and leverage panelization and routing techniques. Collaborate with your Chinese PCB manufacturer to identify opportunities for design optimization and continuously refine your designs based on feedback and performance data. -
Q: How can I navigate cultural differences when working with a Chinese PCB manufacturer?
A: To navigate cultural differences, develop cultural awareness and sensitivity, take the time to understand Chinese business etiquette and communication styles, and show respect for local customs and traditions. Establish clear communication channels, appoint a dedicated liaison, and approach the partnership with a long-term, mutually beneficial mindset. By fostering strong, culturally sensitive relationships, you can build a more effective and successful partnership with your Chinese PCB manufacturer.
Leave a Reply