What is a Wire Harness?
A wire harness, also known as a cable harness or wiring loom, is a systematic and organized assembly of electrical wires, cables, and connectors that are designed to transmit signals or electrical power throughout a vehicle, machine, or electronic device. The primary purpose of a wire harness is to simplify the wiring system by bundling multiple wires together, making it easier to install, maintain, and troubleshoot electrical components.
Wire harnesses are essential components in various industries, including:
- Automotive
- Aerospace
- Medical devices
- Telecommunications
- Consumer electronics
- Industrial machinery
Components of a Wire Harness
A typical wire harness consists of several key components:
-
Wires: The primary component of a wire harness, wires are made from conductive materials like copper and are insulated with materials such as PVC, Teflon, or cross-linked polyethylene.
-
Connectors: These components allow the wire harness to interface with various electrical devices, sensors, and power sources. Connectors come in various types, such as:
- Pin connectors
- Blade connectors
- Circular connectors
-
Rectangular connectors
-
Terminals: These conductive elements are attached to the ends of wires and are designed to fit into specific connectors, ensuring a secure and reliable connection.
-
Protective coverings: Wire harnesses are often covered with materials like braided sleeves, conduits, or tapes to provide additional protection against abrasion, heat, moisture, and electromagnetic interference (EMI).
-
Labels and identification tags: These components help technicians identify specific wires and connectors within the harness, making installation and maintenance more efficient.
The Wire Harness Assembly Process
The process of assembling a wire harness involves several steps, each of which is critical to ensuring the final product’s quality, reliability, and performance.
1. Design and Engineering
The first step in the wire harness assembly process is the design and engineering phase. During this stage, engineers create detailed schematics and drawings that specify the following:
- Wire types, gauges, and lengths
- Connector types and positions
- Termination methods
- Protective covering requirements
- Labeling and identification specifications
These designs are created using computer-aided design (CAD) software, which allows engineers to create 3D models and simulate the wire harness’s performance under various conditions.
2. Prototyping and Testing
Once the design is finalized, a prototype wire harness is built for testing and validation. This process involves:
- Cutting wires to the specified lengths
- Stripping insulation from wire ends
- Crimping terminals onto wire ends
- Inserting terminals into connectors
- Applying protective coverings and labels
The prototype harness is then subjected to various tests to ensure it meets the required specifications and performance standards. These tests may include:
- Continuity testing to verify proper connections
- Insulation resistance testing to ensure adequate insulation between wires
- Environmental testing to assess performance under extreme temperatures, humidity, or vibration
- EMI testing to ensure the harness does not interfere with or become affected by electromagnetic fields
3. Production and Assembly
After the prototype has been validated, the wire harness enters the production and assembly phase. This process typically involves the following steps:
-
Wire cutting: Wires are cut to the specified lengths using automated cutting machines or manual methods.
-
Wire stripping: The insulation is removed from the ends of the wires using stripping machines or manual tools to expose the conductive core.
-
Terminal crimping: Terminals are attached to the exposed wire ends using crimping machines or manual crimping tools. The crimping process ensures a secure and reliable connection between the wire and the terminal.
-
Connector assembly: Terminals are inserted into the appropriate connectors, following the design specifications. This process may involve using specialized insertion tools or manual methods.
-
Protective covering application: Braided sleeves, conduits, or tapes are applied to the wire harness to provide additional protection against abrasion, heat, moisture, and EMI.
-
Labeling and identification: Labels and identification tags are attached to the wire harness to facilitate easy installation and maintenance.
-
Quality control: Throughout the production process, quality control measures are implemented to ensure that each wire harness meets the required specifications and performance standards. This may involve visual inspections, electrical testing, and sample testing.
4. Installation and Integration
Once the wire harness is assembled, it is ready for installation and integration into the final product, such as a vehicle, machine, or electronic device. The installation process typically involves the following steps:
-
Positioning: The wire harness is routed and positioned within the product according to the design specifications.
-
Securing: The harness is secured in place using clips, ties, or other fastening methods to prevent movement and ensure proper positioning.
-
Connecting: The wire harness connectors are plugged into their corresponding components, such as sensors, actuators, and power sources.
-
Testing: After installation, the entire system is tested to ensure proper functionality and performance. This may involve operational testing, diagnostic checks, and safety validations.
Benefits of Wire Harness Assembly
Using wire harnesses in various applications offers several key benefits:
-
Simplified installation: By bundling multiple wires together into a single harness, the installation process becomes more streamlined and efficient, reducing the time and labor required.
-
Improved reliability: Wire harnesses are designed and tested to ensure proper connections and insulation, minimizing the risk of electrical failures and short circuits.
-
Enhanced protection: The use of protective coverings and strategic routing helps shield the wires from damage caused by abrasion, heat, moisture, and EMI, improving the overall durability and longevity of the electrical system.
-
Space optimization: Wire harnesses allow for a more organized and space-efficient routing of electrical wires, which is particularly important in applications where space is limited, such as in vehicles or compact electronic devices.
-
Customization: Wire harnesses can be customized to meet the specific requirements of a particular application, allowing for greater flexibility in design and functionality.
-
Cost-effectiveness: By streamlining the installation process and improving reliability, wire harnesses can help reduce overall costs associated with electrical system maintenance and repairs.
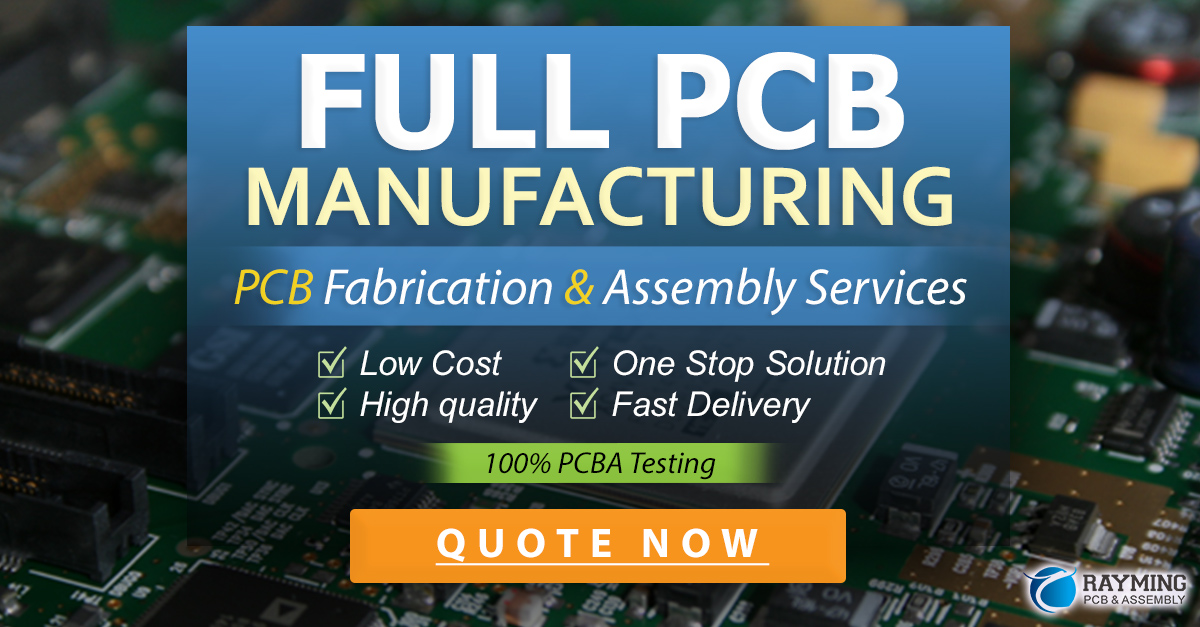
Wire Harness Applications
Wire harnesses are used in a wide range of industries and applications, each with its own unique requirements and challenges. Some of the most common applications include:
Automotive Industry
In the automotive industry, wire harnesses are used to interconnect various electrical components, such as:
- Engine control modules
- Sensors (e.g., oxygen sensors, temperature sensors, pressure sensors)
- Actuators (e.g., fuel injectors, throttle bodies, solenoids)
- Lighting systems (e.g., headlights, taillights, interior lights)
- Infotainment systems (e.g., audio systems, navigation systems, displays)
- Safety systems (e.g., airbags, anti-lock braking systems, stability control systems)
Automotive wire harnesses must be designed to withstand harsh environmental conditions, including extreme temperatures, vibrations, and exposure to moisture and chemicals. They must also be lightweight and space-efficient to minimize vehicle weight and optimize fuel efficiency.
Aerospace Industry
In the aerospace industry, wire harnesses are used in a variety of applications, such as:
- Avionics systems (e.g., flight control systems, communication systems, navigation systems)
- Cabin management systems (e.g., lighting, entertainment, environmental control)
- Engine control systems
- Fuel management systems
- Landing gear systems
Aerospace wire harnesses must meet stringent safety and performance requirements, as well as comply with industry standards and regulations. They must be designed to withstand extreme temperatures, pressure changes, and vibrations, and must be highly reliable to ensure the safety and integrity of the aircraft.
Medical Device Industry
In the medical device industry, wire harnesses are used in a range of applications, including:
- Diagnostic equipment (e.g., MRI machines, CT scanners, X-ray machines)
- Monitoring systems (e.g., ECG monitors, blood pressure monitors, pulse oximeters)
- Surgical instruments (e.g., electrosurgical devices, surgical robots)
- Implantable devices (e.g., pacemakers, defibrillators, neurostimulators)
Medical device wire harnesses must be designed to meet strict safety and performance standards, as well as comply with industry regulations such as those set by the FDA. They must be biocompatible, highly reliable, and able to withstand sterilization processes.
Industrial Machinery
Wire harnesses are used in a wide range of industrial machinery, such as:
- Manufacturing equipment (e.g., CNC machines, injection molding machines, 3D printers)
- Material handling systems (e.g., conveyors, cranes, forklifts)
- Packaging machines
- Printing presses
- HVAC systems
Industrial wire harnesses must be designed to withstand harsh environmental conditions, including exposure to dust, moisture, chemicals, and extreme temperatures. They must also be durable and able to withstand the vibrations and mechanical stresses associated with industrial machinery.
Quality Control in Wire Harness Assembly
Ensuring the quality and reliability of wire harnesses is critical to the performance and safety of the final product. Quality control measures are implemented throughout the wire harness assembly process, from design and engineering to production and installation.
Some of the key quality control measures include:
-
Design validation: Before production begins, the wire harness design is thoroughly reviewed and validated to ensure it meets all functional, performance, and safety requirements.
-
Material selection: High-quality materials, such as wires, connectors, and protective coverings, are selected to ensure the harness can withstand the intended operating conditions and meet performance requirements.
-
Process control: During production, strict process controls are implemented to ensure consistency and accuracy in wire cutting, stripping, crimping, and connector assembly.
-
Testing and inspection: Various tests and inspections are conducted throughout the assembly process, including continuity testing, insulation resistance testing, and visual inspections, to identify and correct any defects or non-conformities.
-
Traceability: Each wire harness is assigned a unique identifier, allowing for traceability throughout the production process and facilitating easier troubleshooting and recall management if necessary.
-
Operator training: Assembly operators receive comprehensive training to ensure they have the necessary skills and knowledge to produce high-quality wire harnesses consistently.
-
Continuous improvement: Quality control data is collected and analyzed to identify opportunities for process improvements and to prevent the recurrence of defects or non-conformities.
By implementing these quality control measures, wire harness manufacturers can ensure that their products meet the highest standards of quality and reliability, ultimately contributing to the performance and safety of the final product.
Future Trends in Wire Harness Assembly
As technology continues to advance and industries evolve, wire harness assembly is also undergoing significant changes. Some of the key trends shaping the future of wire harness assembly include:
-
Miniaturization: With the increasing demand for smaller, lighter, and more compact products, wire harnesses are becoming smaller and more intricate. This trend requires the use of finer wires, smaller connectors, and more precise assembly techniques.
-
Automation: Automated assembly processes, such as robotic wire cutting, stripping, and crimping, are becoming more prevalent in Wire Harness Manufacturing. Automation helps improve efficiency, consistency, and quality while reducing labor costs.
-
Modular design: Modular wire harness designs, which allow for the easy replacement or upgrade of specific sections without having to replace the entire harness, are gaining popularity. This approach facilitates easier maintenance, repair, and customization.
-
Wireless technology: The growing use of wireless technology, such as Bluetooth and Wi-Fi, is changing the way wire harnesses are designed and integrated into products. While wireless technology may reduce the need for some wired connections, it also presents new challenges in terms of EMI shielding and power management.
-
Sustainable materials: There is a growing demand for wire harnesses made from sustainable and eco-friendly materials, such as biodegradable plastics and recycled metals. Manufacturers are exploring ways to reduce their environmental impact while still meeting performance and reliability requirements.
-
Industry 4.0: The integration of advanced technologies, such as the Internet of Things (IoT), artificial intelligence (AI), and big data analytics, is transforming wire harness manufacturing. These technologies enable real-time monitoring, predictive maintenance, and data-driven decision-making, leading to improved efficiency, quality, and responsiveness.
As these trends continue to shape the wire harness industry, manufacturers must adapt their processes, technologies, and skills to remain competitive and meet the evolving needs of their customers.
Frequently Asked Questions (FAQ)
-
Q: What is the difference between a wire harness and a cable assembly?
A: A wire harness is a collection of wires, connectors, and protective coverings that are designed to transmit signals or electrical power within a specific system. A cable assembly, on the other hand, typically refers to a single cable or a small group of cables with connectors on each end, designed to connect two devices or components. -
Q: How do I choose the right wire gauge for my wire harness?
A: The choice of wire gauge depends on several factors, including the current carrying capacity, voltage drop, and environmental conditions. Generally, a larger wire gauge (smaller number) is used for higher current applications, while a smaller wire gauge (larger number) is used for lower current applications. It’s essential to refer to industry standards and manufacturer specifications when selecting wire gauges. -
Q: What are the most common types of connectors used in wire harnesses?
A: There are various types of connectors used in wire harnesses, depending on the application and requirements. Some of the most common types include: - Molex connectors
- Deutsch connectors
- D-sub connectors
- Circular connectors (e.g., M12, M8)
- Blade connectors
-
Pin connectors
-
Q: How can I ensure the quality and reliability of my wire harness?
A: To ensure the quality and reliability of your wire harness, consider the following: - Use high-quality materials, such as wires, connectors, and protective coverings
- Follow industry standards and best practices for design, assembly, and testing
- Implement strict quality control measures throughout the assembly process, including inspections and testing
-
Partner with experienced and reputable wire harness manufacturers who have a proven track record of quality and reliability
-
Q: What are the benefits of using automated wire harness assembly processes?
A: Automated wire harness assembly processes offer several benefits, including: - Improved consistency and accuracy
- Increased efficiency and productivity
- Reduced labor costs
- Enhanced quality control and traceability
- Ability to handle more complex and intricate designs
By leveraging automated technologies, wire harness manufacturers can improve their competitiveness and better meet the evolving needs of their customers.
Leave a Reply