Printed circuit boards (PCBs) form the backbone of electronics. The substrate on which the circuit is fabricated plays a key role in PCB performance and capabilities. While FR-4 glass-epoxy is the most common substrate, aluminum PCBs provide some unique advantages for certain applications.
This article examines the key reasons why aluminum may be chosen as the PCB substrate material for specialized needs.
Aluminum PCB Overview
Aluminum PCB uses a thin aluminum base plate/sheet as the substrate instead of the typical FR-4 or other insulating material. The aluminum provides an ideal metal foundation for circuit fabrication using processes like photochemical etching, CNC milling or direct bonding.
Aluminum’s electrical and thermal conductivity allows it to function additionally as a ground plane and/or heat sink for the PCB components. The metal surface also enables direct component bonding without dielectric layers.
Benefits of Using Aluminum PCB
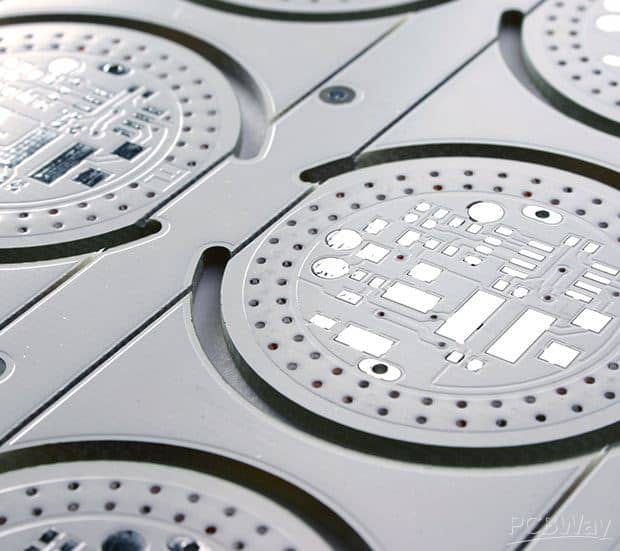
Some of the main benefits offered by aluminum PCBs include:
Thermal Management
Aluminum has excellent thermal conductivity, around 100 times that of FR-4. This allows aluminum PCBs to act as a heat sink keeping components and PCB cool. The entire metal substrate can dissipate heat efficiently.
This thermal spreading helps maintain circuit stability and integrity under high power or fluctuating heat loads. It extends electronic component lifespan by reducing operating temperatures.
Current and High Power Handling
The high electrical conductivity of aluminum coupled with its heat dissipation capability makes it suitable for handling large current loads without overheating. Aluminum PCBs can manage higher current densities compared to FR-4 boards.
High power applications like automotive electronics, power converters and LEDs running several amperes can utilize aluminum PCBs.
Thermal Stress Reduction
The near-zero thermal expansion coefficient of aluminum closely matches that of copper traces. This reduces thermal stresses and cracking failure resulting from PCB heating/cooling during operation or soldering. Reliability improves.
Thin and Lightweight
Aluminum has density one-third that of FR-4 allowing thinner and lighter weight PCB solutions. This saves space and weight which is especially critical in aerospace, defense and portable electronics applications.
Design Flexibility
Aluminum allows more flexibility in PCB design. Components can be directly bonded to the substrate without needing insulating dielectric layers. Vias and channels can be easily incorporated into the aluminum for routing air or liquid cooling.
Cost Savings
The raw material cost for aluminum PCBs can be lower than FR-4 laminates, especially when using aluminum alloys like 6061 or 5052. Etching aluminum is also less expensive than copper etching. This allows cost savings in some high volume applications.
Shielding EMI/RFI
The conductive metal substrate offers shielding against electromagnetic interference (EMI) and radio frequency interference (RFI). This helps protect or isolate sensitive analog and digital circuits.
Environmental Resistance
Aluminum offers high resistance to moisture, humidity and other corrosive elements. Aluminum PCBs can better withstand harsh operating environments compared to FR-4 boards.
Types of Aluminum PCBs
There are two main types of aluminum PCBs:
Direct Bonded Copper (DBC)
This consists of a ceramic dielectric layer like aluminum oxide directly bonded onto the aluminum base plate. A thin layer of copper is bonded onto the ceramic dielectric for circuit patterning.
DBC aluminum PCBs provide insulation between the aluminum and circuits, allowing higher voltages and improved reliability. But the DBC layer slightly reduces thermal transfer compared to direct bond PCBs.
Direct Bonded (DB)
In DB aluminum PCBs, copper tracks are formed directly on the aluminum substrate with no insulating dielectric layer in between. This offers maximum thermal conductivity and heat sinking capability. But has restrictions on the maximum voltage that can be used.
Aluminum PCB Fabrication
Some key aluminum PCB fabrication processes include:
Metal Substrate Pretreatment
This includes abrasive blasting and chemical cleaning of the aluminum surface for optimal bonding and/or coating adhesion.
Direct Copper Bonding
For DB aluminum PCBs, thin high purity copper foil is directly diffusion bonded onto the aluminum at high temperature and pressure. This creates a continuous bond without adhesives.
DBC Layer Attachment
For DBC PCBs, the aluminum is first anodized to create a controlled aluminum oxide layer, followed by bonding a copper foil onto the oxide which serves as the dielectric.
Photochemical Etching
A photoresist layer is applied on the copper foil and imaged to create a pattern mask. Etching then removes exposed copper while retaining the masked tracks and features.
CNC Milling/Routing
CNC milling machines cut away aluminum or copper to create PCB traces, cutouts, holes, slots and other mechanical features. No chemical etching is involved.
Component Attachment
Components can be soldered or epoxied onto the PCB surface. Some components are also directly bonded to the aluminum or copper substrate.
Aluminum PCB Design Considerations
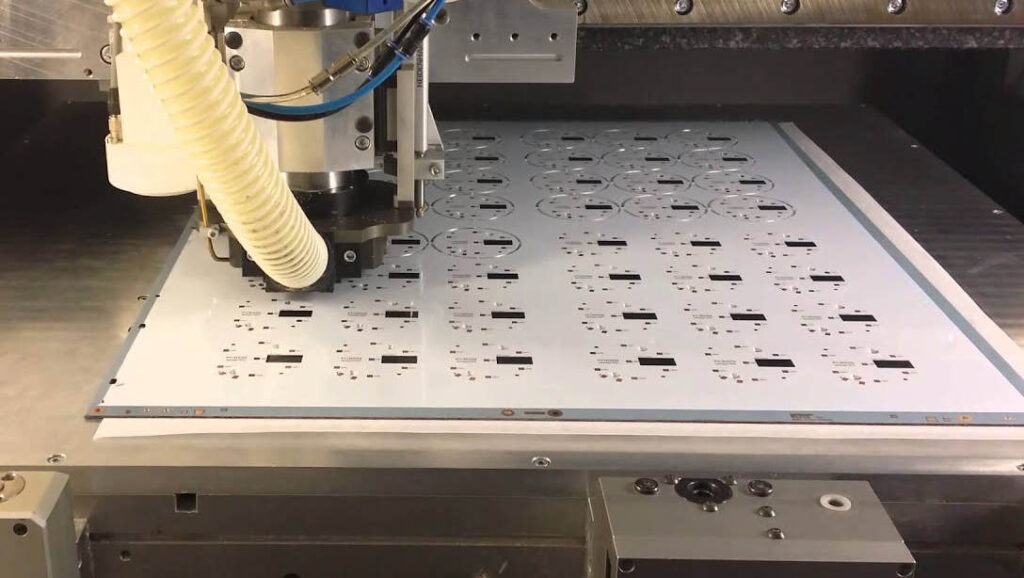
Some key design aspects to consider for aluminum PCBs include:
- The lack of solder mask on bare aluminum requires electrical isolation of exposed pads and tracks.
- Thermal expansion mismatch with components must be managed, for example using low temperature solder.
- Heat sinking capacity should be utilized while ensuring temperature uniformity across the PCB.
- Direct bonding allows components to act as localized heat sinks, but limits reworkability.
- Higher weight and difficulties of cutting, drilling and machining aluminum must be accommodated.
- Protective coatings are needed to prevent aluminum oxidation and corrosion over time.
Applications of Aluminum PCBs
Some typical applications where aluminum PCBs provide benefits include:
- Power electronics: IGBT modules, motor drives, power converters etc.
- Automotive: Engine control units, charging systems, hybrid electric modules.
- LED lighting: LED drivers, signage and high power lighting.
- Aerospace and Defense: Radars, controls, avionics, power supplies, missile systems.
- Industrial: Programmable automation controllers, robotics, process control.
- Power supplies: High current rectifiers, converters, inverters, adapters.
- 5G Telecom: 5G base stations, microwave radios, antenna feeder cables.
- Solar and Wind Power: Inverters, grid interconnection electronics.
- Electric Vehicles: Battery management systems, powertrain components.
Aluminum vs FR-4 PCB Comparison
The table below compares aluminum and FR-4 PCB properties:
Parameter | Aluminum PCB | FR-4 PCB |
---|---|---|
Thermal conductivity | Excellent, up to 250 W/mK | Poor, around 0.25 W/mK |
Electrical conductivity | Excellent | Very low |
Thermal expansion | 23 ppm/K | 17 ppm/K |
Dielectric strength | Moderate, breaks down above 400V without insulation | Excellent, several kV range |
Moisture absorption | Minimal | Absorbs moisture affecting performance |
Weight | Two times heavier than FR-4 | Lower density than Al |
Machining | Challenging, requires diamond tooling | Easier to drill and cut |
EMI/RFI shielding | Excellent due to metal substrate | Poor, requires shielded enclosures |
Cost | Lower material cost, but higher fabrication cost | Overall lower cost |
Aluminum PCB Manufacturers
Some leading companies offering aluminum PCB manufacturing services include:
- Advanced Assembly
- Metal Etch Services
- Lightning Circuits
- SigmaTron
- Thermal Clad
- VT Composites
- Amitech
- Tecknit Europe
These companies can fabricate custom aluminum PCBs in low to high volumes catering to various industries and applications.
FAQs
How are components mounted on aluminum PCBs?
Soldering and conductive epoxy adhesives are common ways to mount components on aluminum PCBs. Some components are also directly diffusion bonded to the aluminum or DBC layer to maximize heat transfer.
Can you solder aluminum PCBs?
Soldering to aluminum requires special solders and techniques to overcome the quick oxide formation on aluminum. Use of ultrasonic soldering or protective coatings allows easier soldering. Some components are also epoxied instead of soldering.
Is aluminum PCB better than FR4?
Aluminum PCBs offer superior thermal performance compared to FR4 but have lower dielectric strength. Aluminum is preferred for high power applications where thermal management is critical. FR4 remains suitable for simpler, low cost PCB needs.
Is aluminum PCB expensive?
The raw material cost of aluminum is lower than FR4 laminates. But the PCB fabrication process is more complex requiring direct bonding and advanced milling. So for lower volume production, aluminum PCB cost may be higher than FR-4.
Can you bend aluminum PCBs?
No, aluminum PCBs have minimal flexibility compared to FR4 PCBs. Bending stress will damage the traces. Small aluminum PCBs may allow slight bending, but in general aluminum boards do not allow flexing.
In summary, aluminum PCBs provide specialized benefits like excellent thermal management, high power handling and lightweight construction. These advantages make aluminum the substrate of choice for demanding applications, despite higher fabrication costs. With the rising performance needs of modern electronics, aluminum PCBs will continue seeing increased adoption in the future.
Leave a Reply