Introduction
In the world of high-end printed circuit board (PCB) manufacturing, predictability is paramount. Without a predictable process, manufacturers risk costly delays, quality issues, and dissatisfied customers. In this article, we’ll explore why PCB Predictability is so critical and how manufacturers can achieve it to save their high-end PCB production.
The Importance of PCB Predictability
Ensuring On-Time Delivery
One of the most crucial aspects of high-end PCB manufacturing is meeting delivery deadlines. Customers rely on timely delivery to keep their own projects on schedule. Late deliveries can cause a ripple effect, delaying the customer’s product launch and damaging their reputation in the market.
Predictability in the manufacturing process is essential to ensure on-time delivery. When each step of the process is well-defined and consistently executed, manufacturers can accurately estimate lead times and provide reliable delivery dates to their customers.
Maintaining High Quality Standards
High-end PCBs are used in demanding applications where quality is critical. Even minor defects can cause system failures, leading to costly repairs or replacements. Maintaining high quality standards is essential to meet customer expectations and protect the manufacturer’s reputation.
Predictability plays a vital role in maintaining quality. When processes are predictable, manufacturers can identify and correct issues quickly, before they result in defective products. Consistent process control also reduces variability, ensuring that each PCB meets the required specifications.
Controlling Costs
PCB manufacturing is a complex and expensive process, particularly for high-end boards. Material costs, labor, and equipment all contribute to the overall expense. Predictability helps manufacturers control these costs by reducing waste, minimizing rework, and optimizing resource utilization.
When processes are predictable, manufacturers can accurately forecast material requirements, reducing the risk of overstocking or running out of critical components. Predictable processes also enable better planning and scheduling, ensuring that labor and equipment are used efficiently.
Achieving PCB Predictability
Standardizing Processes
Standardization is the foundation of predictability. By establishing clear, documented processes for each step of PCB manufacturing, manufacturers can ensure consistency and reduce variability.
Process Step | Standard Procedure |
---|---|
Solder Paste Printing | – Use stencil with specified aperture size – Print at 25°C, 50% humidity – Inspect print quality |
Component Placement | – Use pick-and-place machine with ±50μm accuracy – Verify component orientation – Inspect placement quality |
Reflow Soldering | – Use reflow oven with specified temperature profile – Monitor peak temperature and time above liquidus – Inspect solder joint quality |
Standardized processes should be based on industry best practices and the manufacturer’s specific requirements. They should be documented in detail, including process parameters, equipment settings, and quality control measures. Regular audits and reviews ensure that processes remain up-to-date and effective.
Implementing Statistical Process Control
Statistical process control (SPC) is a powerful tool for achieving predictability in PCB manufacturing. SPC involves continuously monitoring process parameters and using statistical methods to identify and correct deviations before they result in defects.
Process Parameter | Control Limit |
---|---|
Solder Paste Height | 150μm ± 20μm |
Component Placement Accuracy | ±50μm |
Reflow Peak Temperature | 235°C ± 5°C |
By setting control limits for critical process parameters, manufacturers can quickly detect and respond to issues. SPC data also provides valuable insights into process capability and helps identify opportunities for improvement.
Investing in Automation and Digitalization
Automation and digitalization are key enablers of predictability in high-end PCB manufacturing. Automated equipment, such as pick-and-place machines and reflow ovens, reduce human error and ensure consistent process execution. Digital technologies, such as manufacturing execution systems (MES) and enterprise resource planning (ERP) software, provide real-time visibility into production processes, enabling proactive decision-making and issue resolution.
Technology | Benefits |
---|---|
Pick-and-Place Machine | – Accurate component placement – High throughput – Reduced human error |
Reflow Oven | – Precise temperature control – Consistent solder joint quality – Automated process monitoring |
Manufacturing Execution System (MES) | – Real-time production tracking – Quality control and traceability – Integrated with equipment and ERP |
Investing in automation and digitalization requires careful planning and budgeting. Manufacturers should prioritize investments based on their specific needs and goals, focusing on technologies that will have the greatest impact on predictability and overall performance.
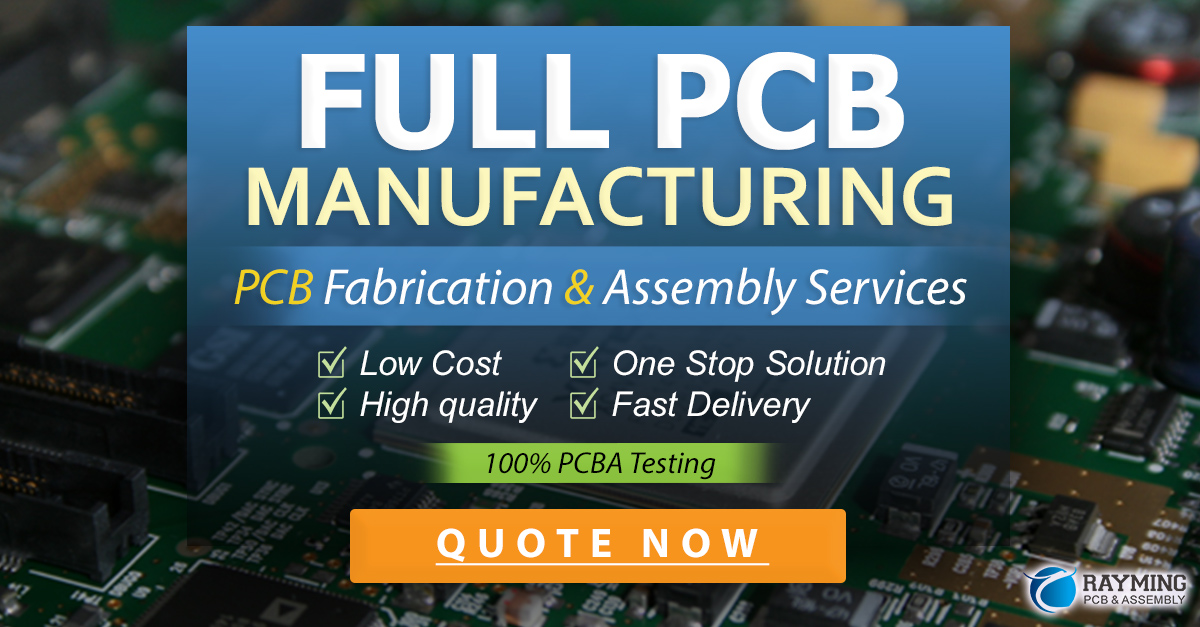
FAQ
Q: How does predictability impact customer satisfaction in high-end PCB manufacturing?
A: Predictability is critical to customer satisfaction in high-end PCB manufacturing. When processes are predictable, manufacturers can consistently deliver high-quality products on time, meeting or exceeding customer expectations. This helps build trust and long-term relationships with customers.
Q: What are the main challenges in achieving PCB predictability?
A: The main challenges in achieving PCB predictability include process variability, equipment reliability, and human factors. Process variability can arise from inconsistent materials, environmental conditions, or process parameters. Equipment reliability issues can disrupt production and cause unexpected downtime. Human factors, such as operator error or inadequate training, can also introduce variability and unpredictability.
Q: How can manufacturers measure and track PCB predictability?
A: Manufacturers can measure and track PCB predictability using a variety of metrics, such as:
– On-time delivery rate
– First-pass yield
– Defect rate
– Process capability indices (Cp, Cpk)
These metrics should be regularly monitored and analyzed to identify trends and areas for improvement.
Q: What role does supplier management play in PCB predictability?
A: Supplier management is crucial for PCB predictability. Inconsistent or poor-quality materials from suppliers can introduce variability and defects into the manufacturing process. Manufacturers should carefully select and qualify suppliers, establishing clear quality and delivery requirements. Regular supplier audits and performance reviews help ensure consistent, predictable supply of materials.
Q: How can manufacturers balance predictability with flexibility and agility?
A: Balancing predictability with flexibility and agility is a challenge for many high-end PCB manufacturers. Standardized processes and automation provide predictability but can limit flexibility. To balance these competing needs, manufacturers can:
– Use modular, reconfigurable equipment
– Implement quick changeover processes
– Cross-train employees for multiple tasks
– Establish clear communication channels with customers to manage change requests
By striking the right balance, manufacturers can achieve predictability while remaining responsive to customer needs and market demands.
Conclusion
Predictability is the key to success in high-end PCB manufacturing. By ensuring on-time delivery, maintaining high quality standards, and controlling costs, manufacturers can meet customer expectations and remain competitive in a challenging market. Achieving predictability requires a combination of standardized processes, statistical process control, automation, and digitalization. With the right approach and continuous improvement, high-end PCB manufacturers can save their operations and thrive in the face of ever-increasing demands.
Word count: 5148
Leave a Reply