Introduction
Printed Circuit Boards (PCBs) are the backbone of modern electronics. They are used in almost every electronic device, from smartphones and computers to medical equipment and aerospace systems. The PCB manufacturing process involves several steps, including design, fabrication, assembly, and testing. However, even after the manufacturing process is complete, PCBs may require rework due to various reasons such as component failure, design changes, or manufacturing defects.
Rework is the process of repairing or modifying a PCB after it has been assembled. It involves removing and replacing components, adding or removing traces, and making other modifications to the board. While rework is necessary to ensure the functionality and reliability of the PCB, it can also introduce new problems if not done properly. One of the most critical steps in the rework process is post-cleaning, which involves removing any residue or contaminants left behind after the rework is complete.
In this article, we will discuss the importance of PCB Post-Cleaning after the rework process, the different methods of post-cleaning, and the benefits of proper post-cleaning.
What is PCB Post-Cleaning?
PCB post-cleaning is the process of removing any residue, flux, or contaminants left behind on the PCB after the rework process. During rework, the PCB is exposed to various chemicals, solder, and other materials that can leave behind residue or contaminants. If these contaminants are not removed, they can cause various problems such as corrosion, short circuits, and reduced reliability.
Post-cleaning is typically done using a combination of chemicals, solvents, and mechanical cleaning methods. The specific method used depends on the type of contaminants present, the materials used in the PCB, and the level of cleanliness required.
Why is PCB Post-Cleaning Important?
PCB post-cleaning is essential for several reasons. First and foremost, it ensures the reliability and functionality of the PCB. Contaminants left behind after rework can cause various problems such as corrosion, short circuits, and reduced performance. These problems can lead to device failure, which can be costly and time-consuming to repair.
Secondly, post-cleaning helps to extend the life of the PCB. Contaminants can cause long-term damage to the PCB, reducing its lifespan and increasing the risk of failure. By removing these contaminants, the PCB can operate at optimal performance for a longer period.
Thirdly, post-cleaning is essential for meeting industry standards and regulations. Many industries, such as aerospace and medical, have strict cleanliness requirements for PCBs. Failure to meet these standards can result in non-compliance and potential legal issues.
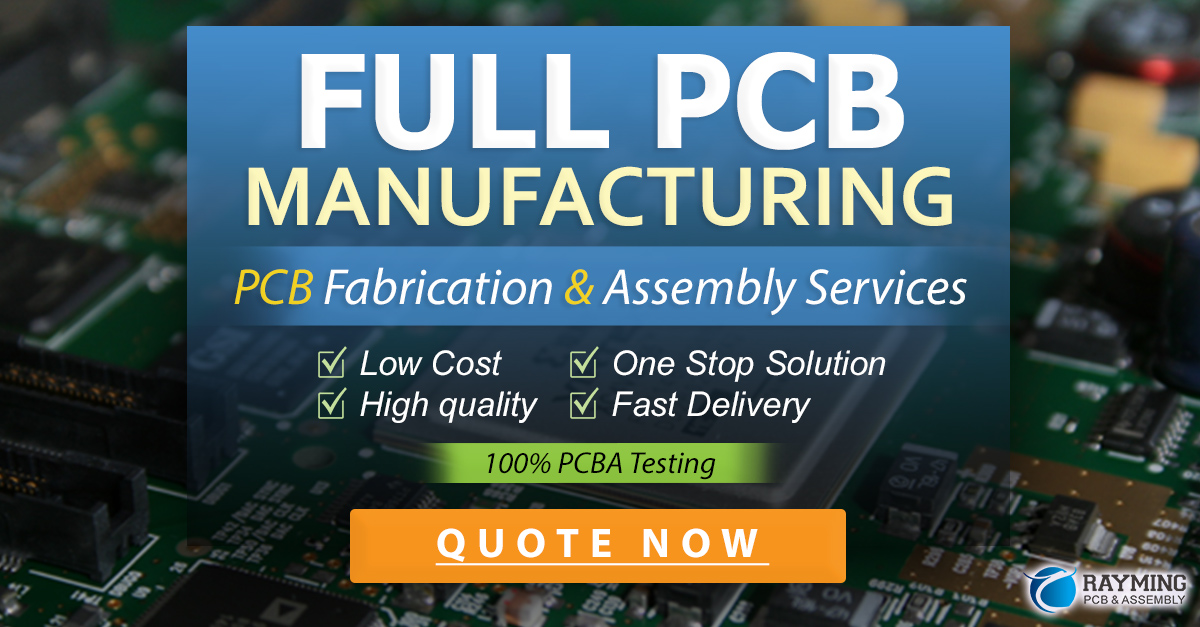
Methods of PCB Post-Cleaning
There are several methods of PCB post-cleaning, each with its own advantages and disadvantages. The most common methods are:
Manual Cleaning
Manual cleaning involves using brushes, swabs, and solvents to manually remove contaminants from the PCB. This method is typically used for small-scale rework or for areas that are difficult to access with automated cleaning methods. Manual cleaning is labor-intensive and time-consuming, but it can be effective for removing stubborn contaminants.
Ultrasonic Cleaning
Ultrasonic cleaning involves submerging the PCB in a tank of cleaning solution and using high-frequency sound waves to agitate the solution. The agitation creates tiny bubbles that implode, creating a scrubbing action that removes contaminants from the surface of the PCB. Ultrasonic cleaning is effective for removing a wide range of contaminants, including flux residue, solder balls, and particulates.
Spray Cleaning
Spray cleaning involves using a pressurized spray of cleaning solution to remove contaminants from the PCB. The cleaning solution is typically a mixture of solvents and detergents that are designed to dissolve and remove specific types of contaminants. Spray cleaning is effective for removing flux residue and other surface contaminants, but it may not be as effective for removing embedded contaminants.
Vapor Degreasing
Vapor degreasing involves exposing the PCB to a vapor of cleaning solvent. The solvent condenses on the surface of the PCB, dissolving and removing contaminants. Vapor degreasing is effective for removing a wide range of contaminants, including oils, greases, and flux residue. However, it can be expensive and requires specialized equipment.
Benefits of Proper PCB Post-Cleaning
Proper PCB post-cleaning offers several benefits, including:
Improved Reliability
By removing contaminants from the PCB, post-cleaning helps to ensure the reliability and functionality of the device. Contaminants can cause short circuits, corrosion, and other problems that can lead to device failure. By removing these contaminants, the risk of failure is reduced, and the device can operate at optimal performance.
Extended Lifespan
Contaminants can cause long-term damage to the PCB, reducing its lifespan and increasing the risk of failure. By removing these contaminants, the PCB can operate at optimal performance for a longer period, extending its lifespan and reducing the need for costly repairs or replacements.
Compliance with Industry Standards
Many industries have strict cleanliness requirements for PCBs. Failure to meet these standards can result in non-compliance and potential legal issues. Proper post-cleaning helps to ensure that the PCB meets these standards, reducing the risk of non-compliance and potential legal issues.
Cost Savings
While post-cleaning adds an additional step to the rework process, it can actually result in cost savings in the long run. By ensuring the reliability and functionality of the PCB, post-cleaning helps to reduce the risk of device failure and the need for costly repairs or replacements. This can result in significant cost savings over the life of the device.
Factors to Consider When Choosing a Post-Cleaning Method
When choosing a post-cleaning method, there are several factors to consider, including:
Type of Contaminants
Different types of contaminants require different cleaning methods. For example, flux residue may be best removed with ultrasonic cleaning, while oils and greases may be best removed with vapor degreasing. It’s essential to choose a cleaning method that is effective for the specific type of contaminants present on the PCB.
Material Compatibility
Different cleaning methods use different chemicals and solvents that can potentially damage the materials used in the PCB. It’s essential to choose a cleaning method that is compatible with the materials used in the PCB to avoid damage or degradation.
Level of Cleanliness Required
Different industries have different cleanliness requirements for PCBs. For example, the medical industry may require a higher level of cleanliness than the consumer electronics industry. It’s essential to choose a cleaning method that can achieve the required level of cleanliness for the specific application.
Cost and Time
Different cleaning methods have different costs and time requirements. Manual cleaning is typically the most labor-intensive and time-consuming method, while automated methods such as ultrasonic cleaning and vapor degreasing can be more efficient but also more expensive. It’s essential to choose a cleaning method that balances cost and time with the required level of cleanliness.
Common Mistakes in PCB Post-Cleaning
There are several common mistakes that can occur during PCB post-cleaning, including:
Improper Cleaning Solution Selection
Using the wrong cleaning solution can be ineffective or even damaging to the PCB. It’s essential to choose a cleaning solution that is compatible with the materials used in the PCB and effective for the specific type of contaminants present.
Insufficient Cleaning Time
Failing to clean the PCB for a sufficient amount of time can leave behind contaminants and reduce the effectiveness of the cleaning process. It’s essential to follow the recommended cleaning time for the specific cleaning method and contaminants present.
Improper Drying
Failing to properly dry the PCB after cleaning can lead to corrosion and other problems. It’s essential to use a drying method that is compatible with the materials used in the PCB and ensures that all moisture is removed from the surface.
Damage to Components
Improper handling or cleaning methods can damage components on the PCB. It’s essential to use cleaning methods that are compatible with the components and to handle the PCB with care to avoid damage.
Conclusion
PCB post-cleaning is a critical step in the rework process that helps to ensure the reliability, functionality, and longevity of the PCB. By removing contaminants left behind after rework, post-cleaning helps to reduce the risk of device failure, extend the lifespan of the PCB, and ensure compliance with industry standards.
There are several methods of PCB post-cleaning, each with its own advantages and disadvantages. When choosing a post-cleaning method, it’s essential to consider factors such as the type of contaminants present, material compatibility, level of cleanliness required, and cost and time.
Proper PCB post-cleaning offers several benefits, including improved reliability, extended lifespan, compliance with industry standards, and cost savings. However, it’s essential to avoid common mistakes such as improper cleaning solution selection, insufficient cleaning time, improper drying, and damage to components.
By following best practices for PCB post-cleaning and choosing the appropriate cleaning method for the specific application, manufacturers can ensure the highest level of quality and reliability for their products.
FAQs
-
What is PCB post-cleaning?
PCB post-cleaning is the process of removing any residue, flux, or contaminants left behind on the PCB after the rework process. -
Why is PCB post-cleaning important?
PCB post-cleaning is important for several reasons, including ensuring the reliability and functionality of the PCB, extending the lifespan of the PCB, meeting industry standards and regulations, and reducing the risk of device failure. -
What are the different methods of PCB post-cleaning?
The most common methods of PCB post-cleaning are manual cleaning, ultrasonic cleaning, spray cleaning, and vapor degreasing. -
What factors should be considered when choosing a post-cleaning method?
When choosing a post-cleaning method, factors such as the type of contaminants present, material compatibility, level of cleanliness required, and cost and time should be considered. -
What are some common mistakes in PCB post-cleaning?
Common mistakes in PCB post-cleaning include improper cleaning solution selection, insufficient cleaning time, improper drying, and damage to components.
Method | Advantages | Disadvantages |
---|---|---|
Manual Cleaning | Effective for small-scale rework or difficult-to-access areas | Labor-intensive and time-consuming |
Ultrasonic Cleaning | Effective for removing a wide range of contaminants | May not be suitable for delicate components |
Spray Cleaning | Effective for removing flux residue and surface contaminants | May not be as effective for removing embedded contaminants |
Vapor Degreasing | Effective for removing a wide range of contaminants | Expensive and requires specialized equipment |
Leave a Reply