Introduction to PCB Track width
Track width is a crucial aspect of printed circuit board (PCB) design that significantly impacts the overall performance, reliability, and manufacturability of the final product. In PCB design, tracks are the conductive pathways that carry electrical signals and power between components on the board. The width of these tracks plays a vital role in determining the current-carrying capacity, signal integrity, and thermal management of the PCB.
What is PCB Track Width?
PCB track width refers to the physical width of the conductive copper traces on a printed circuit board. These traces are responsible for connecting various components and enabling electrical signals to travel between them. The track width is typically measured in mils (thousandths of an inch) or millimeters.
Factors Influencing Track Width Selection
When designing a PCB, engineers must consider several factors when determining the appropriate track width for each trace. These factors include:
- Current-carrying capacity
- Signal integrity
- Manufacturing constraints
- PCB Layer Stack-Up
- Component placement and routing density
Current-Carrying Capacity and Track Width
One of the primary reasons track width is important in PCB design is its direct impact on the current-carrying capacity of the traces. The current-carrying capacity, also known as ampacity, is the maximum amount of current that a track can safely carry without causing damage or excessive heating.
Relationship Between Track Width and Current-Carrying Capacity
The current-carrying capacity of a PCB track is directly proportional to its width. As the track width increases, its cross-sectional area also increases, allowing it to carry more current without experiencing significant voltage drop or temperature rise. Conversely, narrower tracks have lower current-carrying capacities and are more susceptible to overheating and damage when subjected to high currents.
Calculating Current-Carrying Capacity
To determine the appropriate track width for a given current, PCB designers often refer to industry-standard charts or use specialized software tools. These resources provide guidelines for minimum track widths based on factors such as copper thickness, ambient temperature, and the maximum allowable temperature rise.
Here’s an example of a current-carrying capacity table for 1 oz. Copper PCB tracks:
Track Width (mils) | Current-Carrying Capacity (A) |
---|---|
10 | 0.5 |
20 | 1.0 |
30 | 1.5 |
40 | 2.0 |
50 | 2.5 |
Note: The values in this table are for reference only and may vary depending on specific design requirements and environmental conditions.
Thermal Management Considerations
In addition to current-carrying capacity, track width also plays a role in the thermal management of a PCB. As current flows through a track, it generates heat due to the track’s inherent resistance. If the track width is insufficient for the amount of current it carries, the track can experience excessive heating, leading to potential reliability issues or even track damage.
To mitigate thermal concerns, PCB designers must ensure that track widths are adequately sized to dissipate the generated heat. This may involve using wider tracks, incorporating thermal relief pads around component pins, or adding dedicated copper pour areas to act as heat sinks.
Signal Integrity and Track Width
Another crucial aspect of PCB design where track width plays a significant role is signal integrity. Signal integrity refers to the ability of a PCB to maintain the quality and fidelity of the electrical signals transmitted through its traces.
Impedance Control
In high-speed digital circuits, controlling the Characteristic Impedance of PCB Traces is essential for ensuring proper signal propagation and minimizing reflections. The characteristic impedance of a trace is determined by several factors, including its width, thickness, and the properties of the surrounding dielectric material.
To achieve the desired characteristic impedance, PCB designers must carefully select the appropriate track width and spacing. Wider tracks generally have lower impedance, while narrower tracks have higher impedance. By matching the track impedance to the impedance of the source and load devices, designers can minimize signal reflections and maintain signal integrity.
Crosstalk and EMI
Track width also influences the susceptibility of PCB traces to crosstalk and electromagnetic interference (EMI). Crosstalk occurs when signals from one trace unintentionally couple with adjacent traces, causing signal distortion and potentially leading to communication errors.
To reduce crosstalk, PCB designers can employ several techniques, including:
- Increasing the spacing between adjacent traces
- Using guard traces or ground planes to shield sensitive signals
- Routing critical traces on different layers of the PCB
- Minimizing parallel run lengths of adjacent traces
By carefully selecting track widths and implementing proper layout techniques, designers can minimize crosstalk and ensure reliable signal transmission.
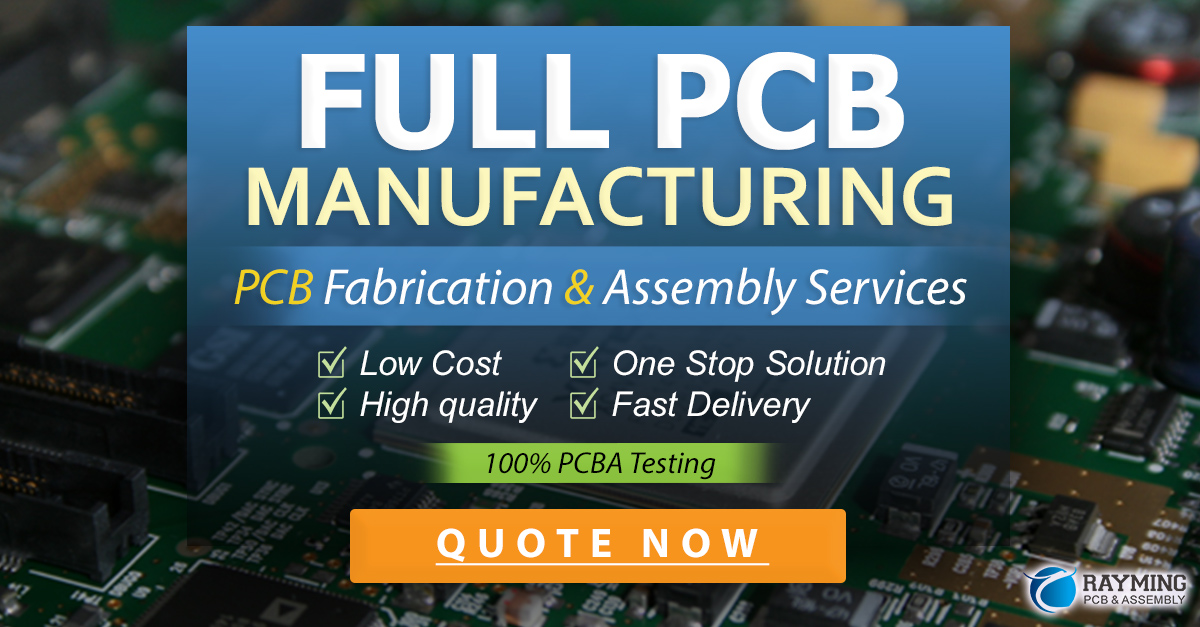
Manufacturing Constraints and Track Width
Track width is not only important for electrical performance but also plays a critical role in the manufacturability of a PCB. PCB Manufacturers have specific capabilities and limitations when it comes to producing traces of various widths.
Minimum Track Width
Each PCB manufacturer has a minimum track width that they can reliably produce. This minimum width is determined by factors such as the manufacturing process, equipment capabilities, and the expertise of the manufacturer.
Designers must be aware of the minimum track width supported by their chosen manufacturer and ensure that their designs adhere to these constraints. Attempting to use track widths below the manufacturer’s minimum can lead to production issues, reduced yields, and increased costs.
Manufacturing Tolerances
In addition to minimum track widths, PCB manufacturers also have tolerances for track width variation. These tolerances account for the inherent variability in the manufacturing process and ensure that the produced tracks fall within acceptable limits.
When designing PCBs, it is essential to consider manufacturing tolerances and incorporate appropriate design rules. This may involve adjusting track widths and spacings to accommodate potential variations and ensure reliable production.
PCB Layer Stack-up and Track Width
The layer stack-up of a PCB, which refers to the arrangement of conductive and insulating layers, also influences track width selection. The number of layers, their thicknesses, and the dielectric materials used can all impact the electrical properties of the traces.
Signal Layers and Track Width
On signal layers, where high-speed or sensitive signals are routed, track width plays a crucial role in maintaining signal integrity. Designers must carefully select track widths to achieve the desired characteristic impedance and minimize signal distortion.
In general, wider tracks are used for high-speed signals to reduce resistance and maintain signal quality. However, the actual track width will depend on the specific requirements of the design, such as the signal frequency, rise time, and the dielectric properties of the PCB material.
Power and Ground Layers
On power and ground layers, track width is primarily determined by the current-carrying capacity requirements. These layers often feature wider traces or copper pour areas to distribute power efficiently and provide a low-impedance return path for signals.
When designing power and ground layers, designers must consider the maximum expected current draw of the components and size the tracks accordingly. They may also use techniques like power plane partitioning and split planes to isolate different power domains and reduce noise coupling.
Component Placement and Routing Density
Track width also influences component placement and routing density on a PCB. The width of the tracks used to connect components directly impacts the available space for routing and the overall size of the PCB.
Component Pitch and Track Width
The pitch, or spacing, between component pins determines the minimum track width required to route signals to and from those pins. Components with finer pitches, such as ball grid array (BGA) packages, often require narrower tracks to achieve successful routing.
Designers must strike a balance between using narrow tracks to accommodate dense component placement and maintaining sufficient track width for reliable electrical performance. This may involve using advanced routing techniques, such as diagonal or multi-layer routing, to optimize trace placement and minimize congestion.
Routing Density and PCB Size
The track width used in a PCB design also affects the overall routing density and the resulting size of the PCB. Wider tracks occupy more space and can limit the available routing channels, potentially leading to a larger PCB size.
On the other hand, using narrower tracks allows for higher routing density and can help minimize PCB size. However, designers must be cautious not to compromise electrical performance or manufacturability when pushing for higher density.
Frequently Asked Questions (FAQ)
- What is the relationship between track width and current-carrying capacity?
The current-carrying capacity of a PCB track is directly proportional to its width. Wider tracks have a higher current-carrying capacity, while narrower tracks have a lower capacity. This is because wider tracks have a larger cross-sectional area, allowing them to carry more current without experiencing significant voltage drop or temperature rise.
- How does track width affect signal integrity in PCB design?
Track width plays a crucial role in maintaining signal integrity in PCB design. The width of a track influences its characteristic impedance, which is essential for ensuring proper signal propagation and minimizing reflections. Wider tracks generally have lower impedance, while narrower tracks have higher impedance. By matching the track impedance to the impedance of the source and load devices, designers can minimize signal reflections and maintain signal integrity.
- What are the manufacturing constraints related to track width?
PCB manufacturers have specific capabilities and limitations when it comes to producing traces of various widths. Each manufacturer has a minimum track width that they can reliably produce, determined by factors such as the manufacturing process, equipment capabilities, and expertise. Designers must adhere to these minimum width constraints to ensure reliable production. Additionally, manufacturers have tolerances for track width variation, which designers must consider and incorporate into their design rules.
- How does the PCB layer stack-up influence track width selection?
The layer stack-up of a PCB, which refers to the arrangement of conductive and insulating layers, influences track width selection. On signal layers, where high-speed or sensitive signals are routed, track width is crucial for maintaining signal integrity and achieving the desired characteristic impedance. Wider tracks are generally used for high-speed signals to reduce resistance and maintain signal quality. On power and ground layers, track width is primarily determined by the current-carrying capacity requirements, with wider traces or copper pour areas used to distribute power efficiently.
- How does track width affect component placement and routing density?
Track width influences component placement and routing density on a PCB. The width of the tracks used to connect components directly impacts the available space for routing and the overall size of the PCB. Components with finer pitches often require narrower tracks to achieve successful routing. Designers must balance the use of narrow tracks for dense component placement with maintaining sufficient track width for reliable electrical performance. The track width used also affects the overall routing density and the resulting size of the PCB, with wider tracks occupying more space and potentially leading to a larger PCB size.
Conclusion
Track width is a fundamental aspect of PCB design that significantly impacts the performance, reliability, and manufacturability of the final product. By understanding the importance of track width and its relationship to factors such as current-carrying capacity, signal integrity, manufacturing constraints, layer stack-up, and component placement, PCB designers can make informed decisions and create robust, high-quality designs.
When selecting track widths, designers must consider the specific requirements of their design, including the electrical characteristics of the signals, the current-carrying capacity needs, and the manufacturing capabilities of their chosen PCB fabricator. By striking the right balance between these factors and employing best practices in PCB layout and routing, designers can ensure optimal performance and reliability in their PCB designs.
Leave a Reply