What is Process Control Measurement?
Process Control Measurement is the practice of monitoring, analyzing, and controlling various parameters throughout the SMT PCB assembly process to ensure that the final product meets the required quality standards. This involves the use of specialized equipment, software, and techniques to collect data, identify potential issues, and make necessary adjustments to optimize the assembly process.
Key elements of Process Control Measurement
- Data collection
- Statistical analysis
- Real-time monitoring
- Feedback and control systems
- Continuous improvement
The SMT PCB Assembly Process
To understand the importance of Process Control Measurement, it is essential to have a basic understanding of the SMT PCB assembly process. The following table outlines the main steps involved in SMT PCB assembly:
Step | Description |
---|---|
1. Solder Paste Printing | Applying solder paste onto the PCB pads using a stencil |
2. Component Placement | Placing surface mount components onto the solder paste |
3. Reflow Soldering | Melting the solder paste to form a permanent connection between components and PCB |
4. Inspection and Testing | Verifying the quality of the assembled PCB through visual inspection and electrical testing |
Common Defects in SMT PCB Assembly
Despite advancements in technology and automation, defects can still occur during the SMT PCB assembly process. Some of the most common defects include:
- Solder bridges
- Tombstoning
- Component misalignment
- Insufficient or excessive solder
- Lifted or missing components
These defects can lead to reduced functionality, reliability issues, and even complete failure of the electronic product. Implementing effective Process Control Measurement techniques can help minimize the occurrence of these defects.
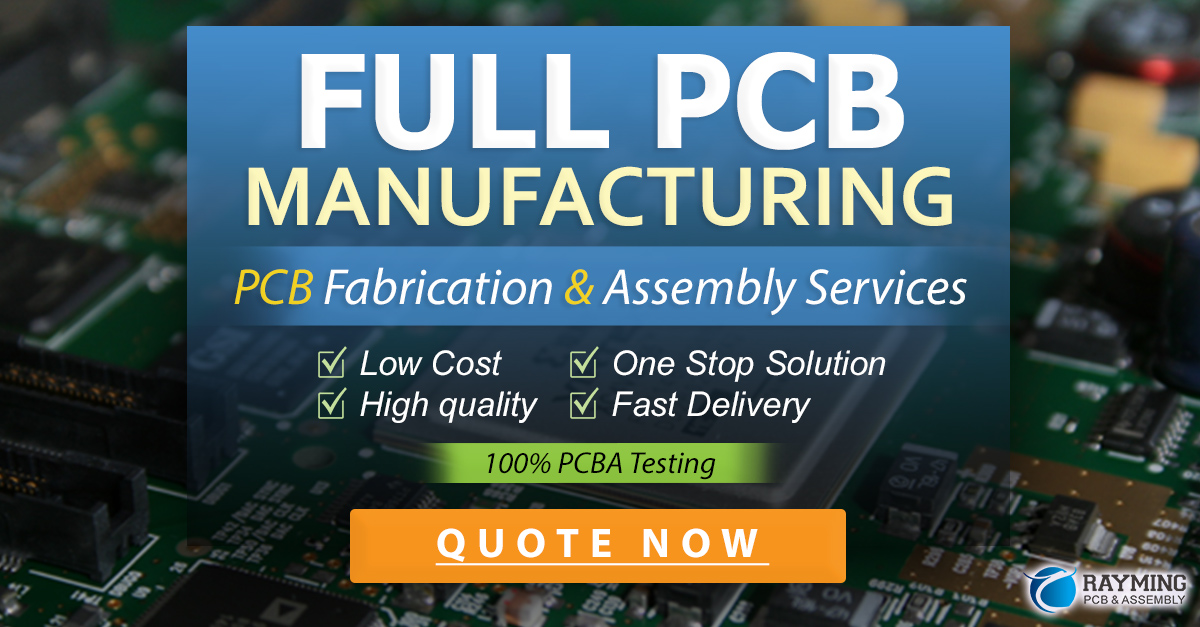
The Role of Process Control Measurement in Preventing Defects
Process Control Measurement plays a vital role in preventing defects in SMT PCB assembly by addressing potential issues at each stage of the process.
1. Solder Paste Printing
- Monitoring solder paste viscosity and temperature
- Measuring solder paste deposit volume and height
- Checking stencil alignment and cleanliness
2. Component Placement
- Verifying component orientation and polarity
- Measuring placement accuracy and repeatability
- Monitoring pick-and-place machine performance
3. Reflow Soldering
- Controlling reflow oven temperature profile
- Monitoring conveyor speed and board alignment
- Measuring oxygen levels in the reflow atmosphere
4. Inspection and Testing
- Conducting automated optical inspection (AOI)
- Performing in-circuit testing (ICT) and functional testing
- Analyzing defect data to identify root causes and implement corrective actions
Benefits of Implementing Process Control Measurement
Implementing effective Process Control Measurement techniques in SMT PCB assembly offers numerous benefits, including:
- Reduced defect rates and improved product quality
- Increased production efficiency and throughput
- Lower manufacturing costs due to reduced rework and scrap
- Enhanced customer satisfaction and brand reputation
- Continuous improvement of the assembly process
Best Practices for Process Control Measurement
To maximize the benefits of Process Control Measurement in SMT PCB assembly, consider the following best practices:
- Establish clear quality standards and specifications
- Invest in high-quality measurement equipment and software
- Train personnel on proper measurement techniques and data analysis
- Implement statistical process control (SPC) methods
- Foster a culture of continuous improvement and data-driven decision-making
Frequently Asked Questions (FAQ)
-
Q: What is the difference between Process Control Measurement and quality control?
A: Process Control Measurement focuses on monitoring and controlling the manufacturing process to prevent defects, while quality control involves inspecting and testing the final product to ensure it meets the required standards. -
Q: How often should Process Control Measurement be performed?
A: The frequency of Process Control Measurement depends on various factors, such as the complexity of the assembly process, the volume of production, and the criticality of the product. In general, measurements should be taken at regular intervals throughout the assembly process to ensure consistent quality. -
Q: What are the most critical parameters to measure in SMT PCB assembly?
A: Some of the most critical parameters to measure in SMT PCB assembly include solder paste printing accuracy, component placement accuracy, reflow oven temperature profile, and soldering quality. -
Q: Can Process Control Measurement completely eliminate defects in SMT PCB assembly?
A: While Process Control Measurement can significantly reduce the occurrence of defects, it is not possible to completely eliminate them. However, by continuously monitoring and improving the assembly process, manufacturers can minimize defects and achieve high levels of product quality. -
Q: How can manufacturers ensure the effectiveness of their Process Control Measurement system?
A: Manufacturers can ensure the effectiveness of their Process Control Measurement system by regularly auditing their measurement processes, validating measurement equipment, and analyzing defect data to identify areas for improvement. Additionally, staying updated with industry best practices and emerging technologies can help optimize the measurement system.
In conclusion, Process Control Measurement is a critical aspect of SMT PCB assembly that enables manufacturers to prevent defects, improve product quality, and enhance overall production efficiency. By implementing effective measurement techniques, analyzing data, and continuously improving the assembly process, manufacturers can deliver high-quality electronic products that meet customer expectations and industry standards.
Leave a Reply