Introduction
Printed Circuit Boards (PCBs) are the backbone of modern electronic devices. They are used in a wide range of applications, from simple consumer electronics to complex aerospace and military systems. The orientation of components on a PCB is a critical factor in ensuring the proper functioning and reliability of the circuit board. In this article, we will explore the importance of PCB component orientation in circuit board manufacturing and how it affects the performance and longevity of electronic devices.
What is PCB Component Orientation?
PCB component orientation refers to the placement and alignment of electronic components on a printed circuit board. It involves ensuring that each component is placed in the correct position and orientation relative to the other components and the PCB itself. Proper component orientation is essential for several reasons, including:
- Ensuring proper electrical connections
- Minimizing signal interference and crosstalk
- Facilitating efficient heat dissipation
- Allowing for easy assembly and maintenance
Types of Component Orientation
There are two main types of component orientation in PCB design:
-
Through-hole component orientation: Through-hole components have leads that are inserted into holes drilled in the PCB and soldered onto the opposite side. The orientation of through-hole components is typically determined by the placement of the leads and the markings on the component package.
-
Surface-mount component orientation: Surface-mount components are mounted directly onto the surface of the PCB using solder pads. The orientation of surface-mount components is determined by the placement of the solder pads and the markings on the component package.
The Importance of Proper PCB Component Orientation
Ensuring Proper Electrical Connections
One of the primary reasons for the importance of PCB component orientation is to ensure proper electrical connections between components. If a component is placed in the wrong orientation, it may not make the necessary electrical connections with other components or the PCB itself. This can lead to a range of problems, from simple malfunctions to complete failure of the circuit board.
For example, consider a simple resistor. If the resistor is placed in the wrong orientation, it may not provide the necessary resistance in the circuit, leading to incorrect voltage or current levels. This can cause other components to malfunction or even damage the entire circuit board.
Minimizing Signal Interference and Crosstalk
Another important reason for proper PCB component orientation is to minimize signal interference and crosstalk between components. When electronic components are placed too close together or in the wrong orientation, they can generate electromagnetic fields that interfere with each other. This can lead to signal degradation, noise, and other problems that can affect the performance of the circuit board.
To minimize signal interference and crosstalk, PCB designers must carefully consider the placement and orientation of components. This involves ensuring that components are spaced sufficiently apart and oriented in a way that minimizes the interaction between their electromagnetic fields.
Facilitating Efficient Heat Dissipation
Proper PCB component orientation is also important for facilitating efficient heat dissipation. Electronic components generate heat during operation, and if this heat is not dissipated effectively, it can lead to component failure and reduced lifespan of the circuit board.
The orientation of components on a PCB can have a significant impact on heat dissipation. For example, components that generate a lot of heat, such as power transistors or voltage regulators, should be placed in areas of the PCB with good airflow and heat sinking. They should also be oriented in a way that allows for efficient heat transfer to the PCB and the surrounding environment.
Allowing for Easy Assembly and Maintenance
Finally, proper PCB component orientation is important for allowing easy assembly and maintenance of the circuit board. When components are placed in the correct orientation, it is easier for assembly technicians to locate and install them correctly. This can help to reduce assembly errors and improve the overall quality of the finished product.
Similarly, proper component orientation can make it easier to troubleshoot and repair the circuit board if problems arise during operation. When components are easily accessible and clearly labeled, technicians can quickly identify and replace faulty components, minimizing downtime and repair costs.
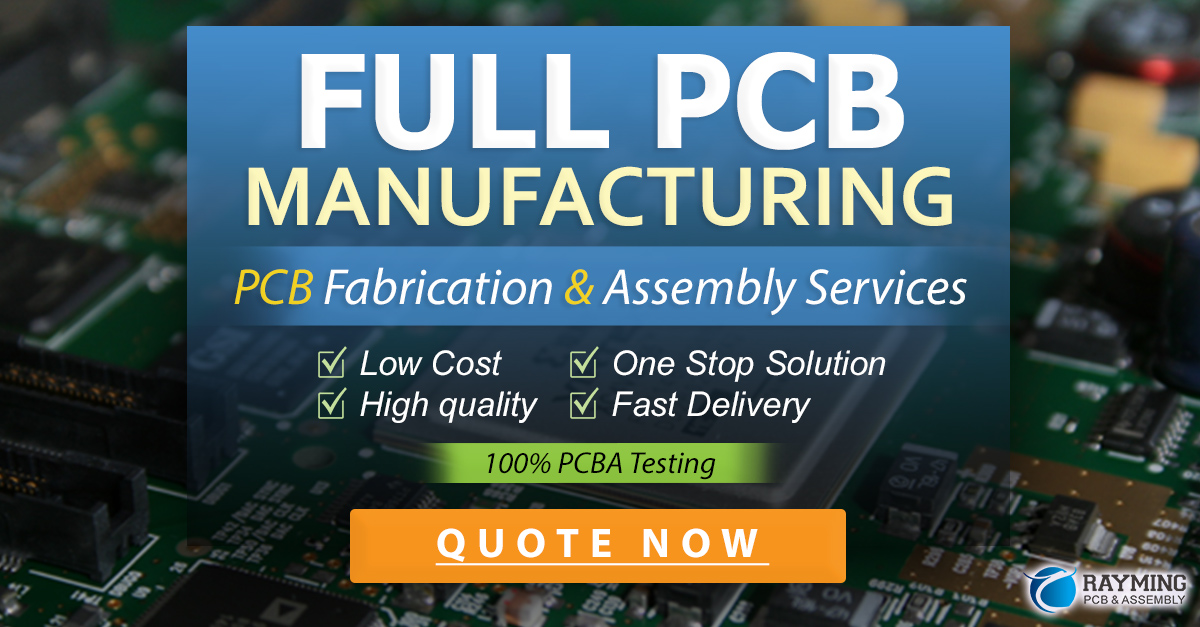
Common PCB Component Orientation Mistakes
Despite the importance of proper PCB component orientation, mistakes can and do happen during the design and assembly process. Some of the most common PCB component orientation mistakes include:
-
Incorrect polarity: Many electronic components, such as diodes and electrolytic capacitors, have a specific polarity that must be observed during installation. If these components are installed with the wrong polarity, they may not function correctly or may even be damaged.
-
Reversed orientation: Some components, such as connectors and switches, have a specific orientation that must be observed during installation. If these components are installed in the reverse orientation, they may not make the necessary electrical connections or may be difficult to use.
-
Misaligned components: Even if components are installed with the correct polarity and orientation, they may still be misaligned with respect to the PCB or other components. This can lead to poor electrical connections, signal interference, and other problems.
-
Incorrect component placement: In some cases, components may be placed in the wrong location on the PCB altogether. This can lead to a range of problems, from incorrect circuit operation to physical interference with other components.
To avoid these and other common PCB component orientation mistakes, it is important to follow best practices for PCB design and assembly. This includes:
- Using clear and accurate component markings and labels
- Following industry standards for component placement and orientation
- Using automated assembly equipment and processes where possible
- Performing thorough testing and inspection of finished circuit boards
The Role of Automated Assembly in PCB Component Orientation
One of the key ways to ensure proper PCB component orientation is through the use of automated assembly equipment and processes. Automated assembly machines, such as pick-and-place machines and reflow ovens, can place components on the PCB with a high degree of accuracy and consistency.
Automated assembly equipment uses a variety of techniques to ensure proper component orientation, including:
-
Vision systems: Many automated assembly machines use vision systems to inspect components before placement. These systems can verify the correct polarity, orientation, and location of components, and can reject components that do not meet specified criteria.
-
Placement algorithms: Automated assembly machines use sophisticated placement algorithms to determine the optimal location and orientation of components on the PCB. These algorithms take into account factors such as component size, shape, and electrical characteristics to ensure proper placement and orientation.
-
Feedback systems: Some automated assembly machines use feedback systems to monitor the placement process in real-time. These systems can detect errors or deviations from specified parameters and make adjustments on the fly to ensure proper component placement and orientation.
By using automated assembly equipment and processes, PCB manufacturers can significantly reduce the risk of component orientation errors and improve the overall quality and reliability of the finished product.
The Future of PCB Component Orientation
As electronic devices continue to become smaller, more complex, and more powerful, the importance of proper PCB component orientation will only continue to grow. In the future, we can expect to see several trends and developments in PCB component orientation, including:
-
Increased use of 3D printing: 3D printing technology is already being used in some PCB manufacturing processes, and this trend is likely to continue in the future. 3D printing can allow for more complex and customized component placement and orientation, as well as the ability to create PCBs with embedded components.
-
More advanced automation: As automated assembly equipment and processes continue to evolve, we can expect to see even greater accuracy and consistency in PCB component orientation. This may include the use of more advanced vision systems, machine learning algorithms, and other technologies to optimize component placement and orientation.
-
Greater emphasis on design for manufacturing: As the complexity of electronic devices continues to increase, there will be a greater emphasis on designing PCBs with manufacturing in mind. This may include the use of standardized component packages and footprints, as well as the development of more sophisticated PCB design software tools that can optimize component placement and orientation for automated assembly.
-
Increased use of embedded components: Embedded components, such as resistors and capacitors, are becoming increasingly common in PCB design. These components are embedded directly into the PCB substrate, rather than being placed on the surface. Embedded components can offer several advantages, including reduced board size and improved signal integrity, but they also require careful consideration of component orientation and placement during the design and manufacturing process.
Conclusion
PCB component orientation is a critical factor in ensuring the proper functioning and reliability of electronic devices. Proper component orientation ensures proper electrical connections, minimizes signal interference and crosstalk, facilitates efficient heat dissipation, and allows for easy assembly and maintenance.
To achieve proper PCB component orientation, manufacturers must follow best practices for PCB design and assembly, including the use of clear component markings and labels, adherence to industry standards, and the use of automated assembly equipment and processes.
As electronic devices continue to evolve and become more complex, the importance of proper PCB component orientation will only continue to grow. By staying up-to-date with the latest trends and technologies in PCB manufacturing, manufacturers can ensure that their products meet the highest standards of quality and reliability.
FAQs
-
What is the difference between through-hole and surface-mount components?
Through-hole components have leads that are inserted into holes drilled in the PCB and soldered onto the opposite side, while surface-mount components are mounted directly onto the surface of the PCB using solder pads. -
Why is component orientation important for heat dissipation?
The orientation of components on a PCB can have a significant impact on heat dissipation. Components that generate a lot of heat should be placed in areas of the PCB with good airflow and heat sinking, and oriented in a way that allows for efficient heat transfer to the PCB and surrounding environment. -
What are some common mistakes in PCB component orientation?
Common mistakes in PCB component orientation include incorrect polarity, reversed orientation, misaligned components, and incorrect component placement. -
How does automated assembly equipment ensure proper component orientation?
Automated assembly equipment uses a variety of techniques to ensure proper component orientation, including vision systems to inspect components before placement, placement algorithms to determine optimal location and orientation, and feedback systems to monitor the placement process in real-time. -
What are some future trends in PCB component orientation?
Some future trends in PCB component orientation include increased use of 3D printing, more advanced automation, greater emphasis on design for manufacturing, and increased use of embedded components.
Component Type | Orientation Considerations |
---|---|
Through-hole | – Lead placement – Component package markings |
Surface-mount | – Solder pad placement – Component package markings |
Common Orientation Mistakes | Potential Consequences |
---|---|
Incorrect polarity | – Component malfunction – Component damage |
Reversed orientation | – Poor electrical connections – Difficult to use |
Misaligned components | – Poor electrical connections – Signal interference |
Incorrect component placement | – Incorrect circuit operation – Physical interference |
Leave a Reply