Introduction to Metal Core PCB
Metal Core PCB, also known as MCPCB or thermal PCB, is a type of printed circuit board that utilizes a metal core as its base material instead of the traditional FR-4 substrate. The metal core, typically made of aluminum, provides excellent thermal conductivity, allowing for efficient heat dissipation in electronic devices. This unique feature has made Metal Core PCB a popular choice for LED products, where heat management is crucial for optimal performance and longevity.
Advantages of Metal Core PCB in LED Applications
- Enhanced thermal management
- Improved electrical performance
- Increased reliability and lifespan
- Compact and lightweight design
- Cost-effective solution
How Metal Core PCB Enhances Thermal Management in LED Products
Thermal Conductivity of Metal Core PCB
The metal core in MCPCB acts as a heat spreader, efficiently conducting heat away from the LED components. Aluminum, the most commonly used metal core material, has a thermal conductivity of approximately 200 W/mK, which is significantly higher than the thermal conductivity of FR-4 (0.3 W/mK). This high thermal conductivity allows for rapid heat dissipation, preventing the LED components from overheating and maintaining optimal operating temperatures.
Thermal Resistance Comparison: Metal Core PCB vs. Traditional PCB
PCB Type | Thermal Resistance (°C/W) |
---|---|
Metal Core PCB | 0.5 – 1.5 |
Traditional FR-4 PCB | 5 – 10 |
The table above demonstrates the significant difference in thermal resistance between Metal Core PCB and traditional FR-4 PCB. The lower thermal resistance of MCPCB indicates its superior ability to dissipate heat, making it an ideal choice for LED applications.
Heat Dissipation Mechanisms in Metal Core PCB
- Conduction: Heat is conducted from the LED components to the metal core through the dielectric layer and thermal vias.
- Convection: Heat is transferred from the metal core to the surrounding air through natural or forced convection.
- Radiation: Heat is radiated from the metal core to the environment, although this mechanism plays a minor role in overall heat dissipation.
Improved Electrical Performance with Metal Core PCB
Reduced Thermal Resistance and Its Impact on LED Performance
The lower thermal resistance of Metal Core PCB leads to improved electrical performance in LED products. As the LED components operate at lower temperatures, they experience less thermal stress, resulting in:
- Higher luminous efficacy
- Improved color consistency
- Longer lifespan
Comparison of Luminous Efficacy: Metal Core PCB vs. Traditional PCB
PCB Type | Luminous Efficacy (lm/W) |
---|---|
Metal Core PCB | 120 – 150 |
Traditional FR-4 PCB | 80 – 100 |
The table above illustrates the higher luminous efficacy achieved by LED products using Metal Core PCB compared to those using traditional FR-4 PCB. The improved thermal management provided by MCPCB allows LEDs to operate more efficiently, resulting in higher light output per unit of power consumed.
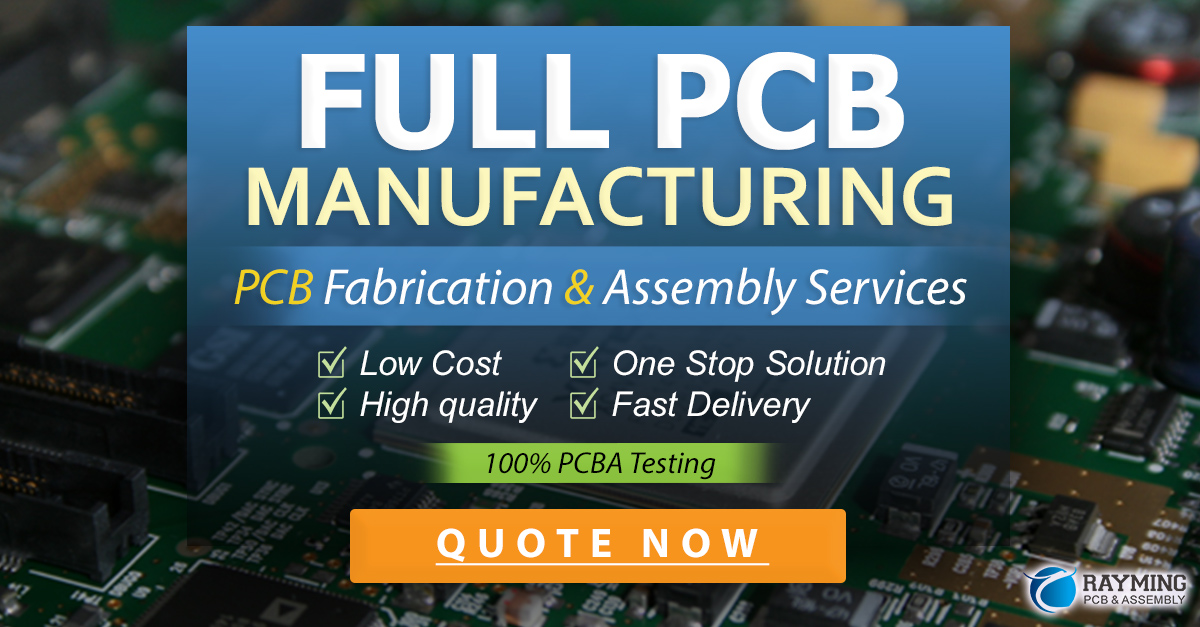
Increased Reliability and Lifespan of LED Products with Metal Core PCB
Thermal Stress Reduction and Its Impact on LED Reliability
The efficient heat dissipation provided by Metal Core PCB reduces thermal stress on LED components, leading to increased reliability and lifespan. Elevated operating temperatures can cause various issues in LEDs, such as:
- Phosphor degradation
- Silicone encapsulant yellowing
- Solder joint fatigue
- Premature failure
By maintaining lower operating temperatures, Metal Core PCB helps mitigate these issues, resulting in more reliable and longer-lasting LED products.
Lifespan Comparison: LED Products with Metal Core PCB vs. Traditional PCB
PCB Type | Estimated Lifespan (hours) |
---|---|
Metal Core PCB | 50,000 – 100,000 |
Traditional FR-4 PCB | 20,000 – 50,000 |
The table above compares the estimated lifespan of LED products using Metal Core PCB and traditional FR-4 PCB. The enhanced thermal management provided by MCPCB contributes to a significantly longer lifespan, making it a preferred choice for applications requiring long-term reliability.
Compact and Lightweight Design with Metal Core PCB
Size Reduction Opportunities in LED Products
The superior thermal performance of Metal Core PCB allows for more compact designs in LED products. As the MCPCB efficiently dissipates heat, LED components can be placed closer together without compromising thermal management. This enables manufacturers to create smaller, more space-efficient LED products, such as:
- Miniature LED spotlights
- Compact LED bulbs
- Slim LED panels
Weight Reduction Benefits of Metal Core PCB
In addition to size reduction, Metal Core PCB also contributes to weight reduction in LED products. The aluminum core used in MCPCB is lighter than the copper core used in traditional PCBs, resulting in an overall lighter product. This weight reduction is particularly advantageous in applications where weight is a critical factor, such as:
- Automotive LED lighting
- Portable LED devices
- Aerospace LED lighting
Cost-Effective Solution with Metal Core PCB
Cost Comparison: Metal Core PCB vs. Traditional PCB with Heat Sink
PCB Type | Estimated Cost (USD) |
---|---|
Metal Core PCB | 5 – 10 |
Traditional FR-4 PCB with Heat Sink | 8 – 15 |
The table above compares the estimated cost of using Metal Core PCB and traditional FR-4 PCB with an additional heat sink. Although the initial cost of MCPCB may be higher than traditional PCB, the integrated thermal management solution eliminates the need for a separate heat sink. This results in a more cost-effective solution, considering the overall system cost and assembly requirements.
Cost Savings in Assembly and Manufacturing
The use of Metal Core PCB in LED products offers cost savings in assembly and manufacturing processes. The integrated thermal management solution provided by MCPCB simplifies the assembly process by reducing the number of components required. This leads to:
- Shorter assembly time
- Reduced labor costs
- Fewer assembly errors
- Streamlined manufacturing process
Conclusion
Metal Core PCB has become widely used in LED products due to its superior thermal management capabilities, improved electrical performance, increased reliability and lifespan, compact and lightweight design, and cost-effectiveness. By efficiently dissipating heat and maintaining optimal operating temperatures, MCPCB enables LED products to achieve higher luminous efficacy, better color consistency, and longer lifespans. As the demand for high-performance, reliable, and compact LED lighting solutions continues to grow, the adoption of Metal Core PCB is expected to increase in various industries and applications.
FAQs
-
Q: What is the main difference between Metal Core PCB and traditional FR-4 PCB?
A: The main difference between Metal Core PCB and traditional FR-4 PCB is the base material. MCPCB uses a metal core, typically aluminum, as its base material, while traditional PCB uses an FR-4 substrate. The metal core in MCPCB provides significantly better thermal conductivity compared to FR-4, allowing for more efficient heat dissipation. -
Q: Can Metal Core PCB be used in applications other than LED lighting?
A: Yes, Metal Core PCB can be used in various applications where efficient thermal management is crucial. Apart from LED lighting, MCPCB is commonly used in power electronics, automotive electronics, telecommunications, and aerospace industries. -
Q: Is it possible to customize the metal core thickness in MCPCB?
A: Yes, the metal core thickness in MCPCB can be customized based on the specific thermal requirements of the application. Typical metal core thicknesses range from 0.5mm to 3.0mm, providing flexibility in designing the optimal thermal management solution. -
Q: How does the dielectric layer in Metal Core PCB affect its thermal performance?
A: The dielectric layer in Metal Core PCB acts as an electrical insulator between the metal core and the copper circuit layer. It is essential to choose a dielectric material with high thermal conductivity to minimize thermal resistance and ensure efficient heat transfer from the LED components to the metal core. -
Q: Are there any limitations or challenges in using Metal Core PCB for LED products?
A: One of the main challenges in using Metal Core PCB for LED products is the limited flexibility in circuit design compared to traditional FR-4 PCB. The metal core in MCPCB may also require special considerations during the manufacturing process, such as specific drilling and cutting techniques. Additionally, the initial cost of MCPCB may be higher than traditional PCB, although the overall system cost and performance benefits often outweigh this limitation.
Leave a Reply