What is Automated X-Ray Inspection (AXI) Technology?
Automated X-Ray Inspection (AXI) is a non-destructive testing method that utilizes X-rays to examine the internal structure and components of PCBs. Unlike traditional optical inspection techniques, AXI can penetrate through the layers of a PCB, providing a detailed view of solder joints, component placement, and other critical features that are not visible to the naked eye.
AXI systems typically consist of an X-ray source, a detector, and a computer with specialized software for image analysis and defect detection. The PCB is placed between the X-ray source and the detector, and as the X-rays pass through the board, the detector captures a series of images from different angles. These images are then processed by the software, which uses advanced algorithms to identify and classify any defects or anomalies.
Benefits of Automated X-Ray Inspection (AXI) Technology
1. Comprehensive Defect Detection
One of the primary advantages of AXI Technology is its ability to detect a wide range of defects that may be missed by other inspection methods. Some of the common defects that AXI can identify include:
- Voids: Gaps or air pockets within solder joints that can weaken the connection and lead to failures.
- Bridging: Unintended connections between adjacent solder joints or components, causing short circuits.
- Insufficient solder: Inadequate amount of solder in the joint, resulting in poor electrical and mechanical connections.
- Component misalignment: Incorrect placement or orientation of components on the PCB.
- Tombstoning: When a component stands up on one end due to uneven heating during the soldering process.
By detecting these defects early in the assembly process, manufacturers can take corrective actions and prevent costly rework or product failures in the field.
2. Improved Quality and Reliability
AXI technology enables manufacturers to achieve higher levels of quality and reliability in their PCB assemblies. By identifying and addressing defects before the boards leave the production line, companies can reduce the risk of product failures, warranty claims, and customer dissatisfaction.
Moreover, AXI can help manufacturers meet the stringent quality requirements of industries such as aerospace, medical devices, and automotive, where the consequences of PCB failures can be severe. By providing objective and traceable inspection results, AXI supports compliance with industry standards and regulations.
3. Increased Efficiency and Productivity
Automated X-Ray Inspection systems can significantly enhance the efficiency and productivity of the PCB assembly process. Unlike manual inspection methods, which are time-consuming and prone to human error, AXI can inspect hundreds of boards per hour with consistent accuracy.
This high-speed inspection capability allows manufacturers to keep up with the increasing demand for PCBs while maintaining tight production schedules. Additionally, by catching defects early in the process, AXI helps reduce the need for costly and time-consuming rework, further improving overall productivity.
4. Versatility and Adaptability
AXI technology is highly versatile and can be adapted to inspect a wide range of PCB types and configurations. Whether it’s a simple single-layer board or a complex multi-layer assembly with fine-pitch components, AXI systems can be customized to meet the specific requirements of each application.
Furthermore, as PCB technologies continue to evolve, with smaller components and denser layouts, AXI systems can be upgraded with advanced software algorithms and higher-resolution detectors to keep pace with the changing industry needs.
Applications of Automated X-Ray Inspection (AXI) Technology
AXI technology finds applications across various industries and product categories where PCB reliability is critical. Some of the common applications include:
- Consumer Electronics: Smartphones, tablets, laptops, and wearable devices.
- Automotive: Engine control units, infotainment systems, and advanced driver assistance systems (ADAS).
- Aerospace and Defense: Avionics, satellite communication systems, and military equipment.
- Medical Devices: Implantable devices, diagnostic equipment, and patient monitoring systems.
- Industrial Automation: Robotics, motor controllers, and power electronics.
In each of these applications, AXI technology plays a vital role in ensuring the quality and reliability of the PCBs, thereby contributing to the overall performance and safety of the end products.
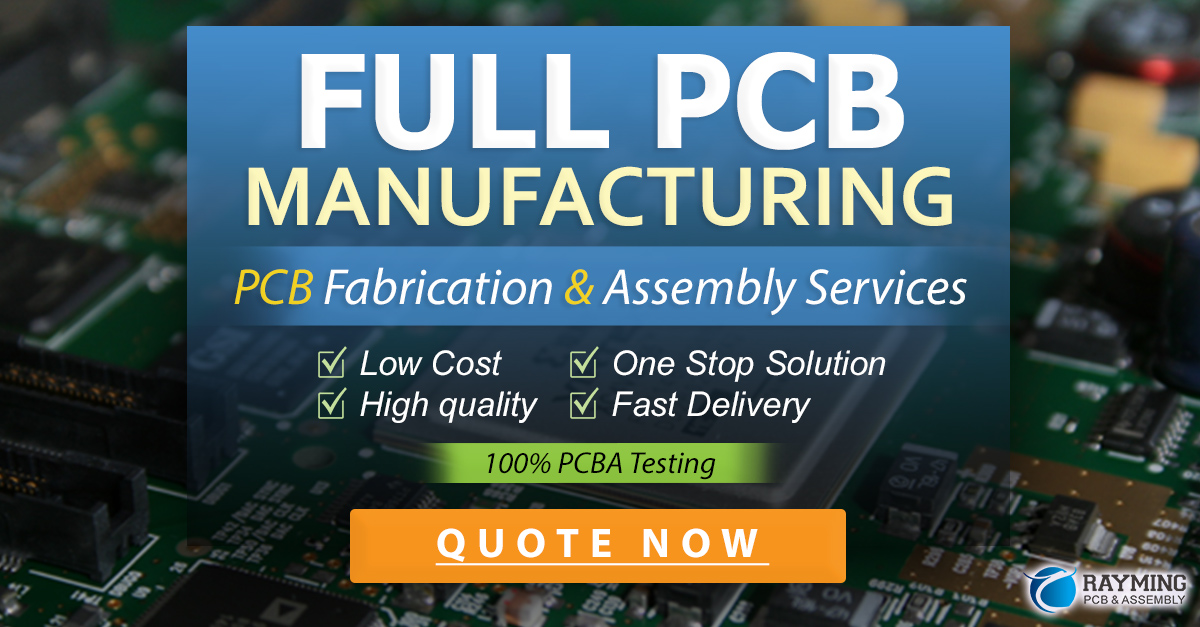
Implementing Automated X-Ray Inspection (AXI) in PCB Assembly
To effectively implement AXI technology in PCB assembly, manufacturers need to consider several key factors:
-
Defining Inspection Requirements: Clearly understanding the specific defects and quality criteria that need to be inspected based on the product specifications and industry standards.
-
Selecting the Right AXI System: Choosing an AXI system that meets the inspection requirements, considering factors such as resolution, speed, software capabilities, and ease of integration with existing production lines.
-
Developing Inspection Programs: Creating inspection programs that define the specific regions of interest (ROIs) on the PCB, the defect types to be detected, and the acceptance criteria for each defect.
-
Training and Operator Skills: Ensuring that the operators are properly trained in using the AXI system, interpreting the inspection results, and making informed decisions based on the data.
-
Integration with Manufacturing Execution Systems (MES): Integrating the AXI system with the overall manufacturing execution system to enable seamless data flow, traceability, and real-time monitoring of the inspection process.
By carefully planning and implementing AXI technology, manufacturers can optimize their PCB assembly process, improve product quality, and gain a competitive edge in the market.
Frequently Asked Questions (FAQ)
- What is the difference between AXI and traditional optical inspection methods?
-
AXI uses X-rays to inspect the internal structure of PCBs, while optical inspection methods rely on visible light to examine the surface features. AXI can detect defects that are hidden from view, such as voids, bridging, and insufficient solder, which may be missed by optical inspection.
-
Can AXI technology replace other inspection methods entirely?
-
While AXI is a powerful inspection tool, it is not a replacement for all other inspection methods. AXI is often used in combination with optical inspection, automated optical inspection (AOI), and electrical testing to provide a comprehensive quality control solution for PCB assembly.
-
Is AXI technology safe for operators and the environment?
-
AXI systems are designed with safety in mind, and they typically operate within the safe limits of X-ray exposure. Operators are protected by shielding and safety interlocks, and the systems are compliant with international safety standards. Additionally, AXI technology is environmentally friendly as it does not generate any hazardous waste or require the use of chemicals.
-
How does AXI handle the inspection of double-sided PCBs?
-
AXI systems can inspect both sides of a double-sided PCB by using angled X-ray detectors or by flipping the board during the inspection process. The software algorithms are designed to analyze the images from both sides and provide a comprehensive defect report.
-
What is the typical return on investment (ROI) for implementing AXI technology?
- The ROI for AXI technology varies depending on factors such as the production volume, the complexity of the PCBs, and the cost of defects and rework. However, many manufacturers report significant cost savings and quality improvements after implementing AXI, with the investment often paying off within a year or two.
Conclusion
In the rapidly evolving world of PCB assembly, Automated X-Ray Inspection (AXI) technology has emerged as a game-changer for ensuring the quality and reliability of electronic products. By providing a non-destructive, comprehensive, and efficient means of detecting hidden defects, AXI enables manufacturers to achieve higher levels of quality control, reduce costs associated with rework and failures, and meet the demanding requirements of various industries.
As PCB technologies continue to advance, with smaller components, higher densities, and more complex designs, the importance of AXI will only continue to grow. By embracing this powerful inspection tool and integrating it into their assembly processes, manufacturers can position themselves for success in the competitive landscape of electronic manufacturing.
Inspection Method | Defect Detection Capabilities | Speed | Cost |
---|---|---|---|
Manual Visual Inspection | Limited to surface defects | Slow | Low |
Automated Optical Inspection (AOI) | Surface defects, component placement | Fast | Moderate |
Automated X-Ray Inspection (AXI) | Internal defects, solder joints, voids, bridging | Fast | High |
Electrical Testing | Functional defects, short/open circuits | Moderate | Moderate |
Table 1: Comparison of different PCB inspection methods
In conclusion, Automated X-Ray Inspection (AXI) technology offers a comprehensive, efficient, and reliable solution for ensuring the quality and integrity of PCBs in the assembly process. By leveraging the power of AXI, manufacturers can improve their product quality, reduce costs, and stay competitive in the ever-evolving world of electronic manufacturing.
Leave a Reply