What is Ball Grid Array (BGA)?
A Ball Grid Array (BGA) is a surface-mount package that utilizes a grid of solder balls on the bottom of the package to connect it to a PCB. The solder balls are arranged in a matrix pattern, allowing for a high density of connections in a small area. BGAs are commonly used for packaging complex ICs, such as microprocessors, FPGAs, and ASICs.
Package Type | Connection Method | Pin Count Range | Pitch (mm) |
---|---|---|---|
BGA | Solder balls | 100-1000+ | 0.5-1.27 |
QFP | Leads | 32-256 | 0.4-0.8 |
DIP | Pins | 8-64 | 2.54 |
Advantages of BGA in PCB Assembly
High Connection Density
One of the primary advantages of BGA packages is their ability to provide a high density of connections in a small area. This is particularly important for complex ICs that require a large number of inputs and outputs (I/O). By utilizing a grid of solder balls, BGAs can accommodate hundreds or even thousands of connections in a package that is much smaller than other types of packages, such as Quad Flat Packages (QFPs) or Dual Inline Packages (DIPs).
Improved Signal Integrity
BGAs offer improved signal integrity compared to other package types. The short, uniform length of the solder balls reduces the inductance and capacitance of the connections, resulting in cleaner and faster signal transmission. This is particularly important for high-speed applications, such as high-performance computing and telecommunications.
Better Thermal Performance
BGAs provide better thermal performance than other package types due to their large contact area with the PCB. The grid of solder balls allows for efficient heat dissipation from the IC to the PCB, which can help prevent overheating and improve the overall reliability of the system.
Reduced PCB Size and Weight
By enabling high connection density in a small package, BGAs allow for the design of smaller and lighter PCBs. This is particularly important for applications where size and weight are critical factors, such as mobile devices, wearables, and aerospace systems.
Enhanced Manufacturability
BGAs offer several advantages in terms of manufacturability. The uniform grid of solder balls simplifies the PCB layout process, as designers do not need to route complex patterns of traces to connect the package to the board. Additionally, BGAs are well-suited for automated assembly processes, such as pick-and-place and reflow soldering, which can help reduce manufacturing costs and improve production throughput.
Challenges of BGA in PCB Assembly
Despite their numerous advantages, BGAs also present some challenges in PCB assembly.
Precise Alignment Required
Due to the small size and close spacing of the solder balls, BGAs require precise alignment during the assembly process. Any misalignment can result in poor connections or short circuits, which can lead to system failures. To ensure proper alignment, manufacturers must use specialized equipment, such as vision systems and high-precision placement machines.
Thermal Management
While BGAs offer better thermal performance than other package types, they can still present challenges in terms of heat dissipation. The high density of connections and the small size of the package can make it difficult to effectively remove heat from the IC. Designers must carefully consider the thermal requirements of the system and incorporate appropriate heat dissipation techniques, such as thermal vias, heat sinks, and fans.
Rework and Repair
Reworking or repairing BGA packages can be challenging due to the small size and close spacing of the solder balls. Specialized equipment and techniques, such as hot air rework stations and BGA reballing, are required to remove and replace BGA packages without damaging the PCB or surrounding components.
Cost Considerations
While BGAs offer many advantages in terms of performance and manufacturability, they can also be more expensive than other package types. The cost of BGA packages, as well as the specialized equipment and processes required for their assembly, can add to the overall cost of the PCB. Designers must carefully consider the cost-benefit trade-offs of using BGAs in their designs.
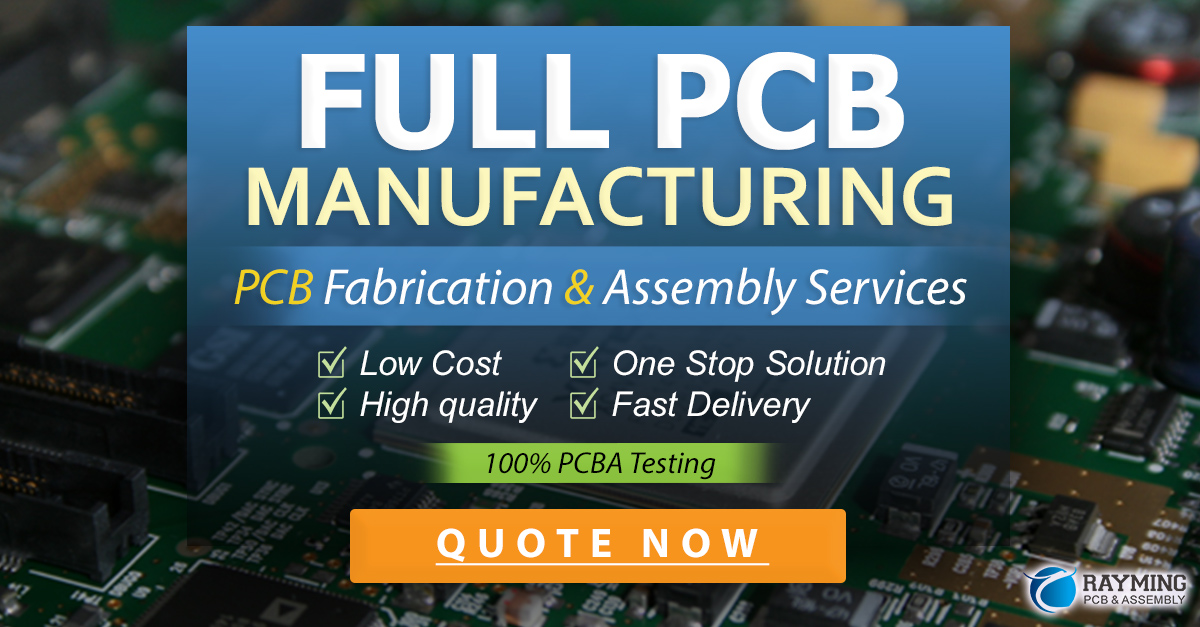
Applications of BGA in PCB Assembly
BGAs are widely used in a variety of applications across different industries. Some common applications include:
-
High-performance computing: BGAs are used in microprocessors, graphics processing units (GPUs), and other high-performance ICs found in servers, workstations, and gaming systems.
-
Telecommunications: BGAs are used in networking equipment, such as routers, switches, and base stations, where high connection density and signal integrity are critical.
-
Consumer electronics: BGAs are used in a wide range of consumer devices, including smartphones, tablets, smart watches, and digital cameras.
-
Automotive electronics: BGAs are increasingly used in automotive applications, such as advanced driver assistance systems (ADAS), infotainment systems, and powertrain control modules.
-
Medical devices: BGAs are used in various medical devices, such as imaging equipment, patient monitoring systems, and implantable devices, where reliability and performance are paramount.
Future Trends in BGA Technology
As technology continues to advance, BGA packages are expected to evolve to meet the growing demands of modern electronics. Some future trends in BGA technology include:
-
Finer pitch: The pitch, or spacing between solder balls, is expected to continue decreasing to accommodate higher connection densities. This will require advancements in manufacturing processes and equipment to ensure reliable assembly.
-
3D packaging: 3D packaging technologies, such as package-on-package (PoP) and through-silicon vias (TSVs), are expected to become more prevalent in BGA designs. These technologies enable the stacking of multiple ICs in a single package, further increasing connection density and reducing PCB size.
-
Advanced materials: New materials, such as high-performance substrates and low-temperature solders, are being developed to improve the performance and reliability of BGA packages in demanding applications.
-
Embedded components: The integration of passive components, such as capacitors and resistors, into the BGA package itself is expected to become more common. This can help reduce PCB size and improve signal integrity by minimizing the distance between the IC and its associated components.
FAQ
1. What is the difference between a BGA and a QFP?
A BGA package uses a grid of solder balls to connect to the PCB, while a QFP uses leads that extend from the sides of the package. BGAs offer higher connection density and better thermal performance, while QFPs are generally easier to rework and repair.
2. Can BGAs be soldered using traditional through-hole techniques?
No, BGAs are designed for surface-mount assembly and cannot be soldered using through-hole techniques. They require specialized equipment and processes, such as reflow soldering and hot air rework.
3. How do I choose the right BGA package for my application?
When selecting a BGA package, consider factors such as the number of I/O connections required, the thermal performance needs of the IC, the size constraints of the PCB, and the cost implications. Consult with the IC manufacturer and PCB assembly provider to determine the most suitable BGA package for your specific application.
4. Are BGAs more expensive than other package types?
In general, BGAs tend to be more expensive than other package types due to their complexity and the specialized equipment and processes required for their assembly. However, the cost difference can be justified by the improved performance, reduced PCB size, and enhanced manufacturability that BGAs offer.
5. What are the most common issues encountered when assembling BGAs?
Some of the most common issues encountered when assembling BGAs include misalignment, poor solder joint formation, and thermal management challenges. These issues can be mitigated through careful design, precise manufacturing processes, and appropriate heat dissipation techniques.
In conclusion, Ball Grid Array (BGA) packages have become an essential component in modern PCB assembly due to their numerous advantages, including high connection density, improved signal integrity, better thermal performance, and reduced PCB size. While BGAs present some challenges in terms of precise alignment, thermal management, and rework, their benefits make them a critical choice for a wide range of applications across various industries. As technology continues to advance, BGA packages are expected to evolve to meet the ever-increasing demands of modern electronics.
Leave a Reply