Introduction to PCB Additive Manufacturing
Printed Circuit Board (PCB) manufacturing has come a long way since its inception in the 1930s. From the early days of hand-drawn circuits to the modern era of computer-aided design (CAD) and automated assembly, the PCB industry has constantly evolved to meet the demands of an ever-changing technological landscape. One of the most significant advancements in recent years has been the rise of additive manufacturing, also known as 3D printing, in the production of PCBs.
What is Additive Manufacturing?
Additive manufacturing is a process by which a three-dimensional object is built layer-by-layer from a digital model. This is in contrast to traditional subtractive manufacturing methods, such as milling or drilling, where material is removed from a larger piece to create the desired shape. Additive manufacturing has been used in various industries, from aerospace to medical devices, and has now found its way into the world of PCB production.
Benefits of Additive Manufacturing for PCBs
The application of additive manufacturing techniques to PCB production offers several key advantages over traditional methods:
-
Rapid Prototyping: Additive manufacturing allows for the quick and cost-effective production of prototype PCBs, enabling faster iteration and testing of designs.
-
Increased Design Freedom: 3D printing techniques allow for the creation of complex geometries and structures that would be difficult or impossible to achieve with traditional manufacturing methods.
-
Reduced Waste: Additive manufacturing is a more sustainable approach, as it generates less waste compared to subtractive methods that remove material from a larger piece.
-
Shorter Lead Times: With additive manufacturing, PCBs can be produced on-demand, reducing the need for large inventory stockpiles and shortening overall lead times.
Types of Additive Manufacturing for PCBs
There are several additive manufacturing techniques that have been adapted for use in PCB production. Each method has its own strengths and limitations, making them suitable for different applications.
Inkjet Printing
Inkjet printing is one of the most common additive manufacturing techniques used for PCBs. This method involves depositing conductive ink onto a substrate using a specialized inkjet printer. The ink is typically composed of metal nanoparticles, such as silver or copper, suspended in a liquid carrier. Once printed, the ink is sintered, or heated, to remove the liquid carrier and form a solid conductive trace.
Advantages of Inkjet Printing
- High resolution printing, with feature sizes as small as 50 microns
- Ability to print on a variety of substrates, including flexible materials
- Cost-effective for low-volume production and prototyping
Limitations of Inkjet Printing
- Limited to the use of specialized conductive inks
- Slower than traditional PCB manufacturing methods for high-volume production
- May require post-processing steps, such as sintering, to achieve optimal conductivity
Aerosol Jet Printing
Aerosol jet printing is another additive manufacturing technique that has been adapted for PCB production. This method involves atomizing a conductive ink into a fine mist, which is then focused and deposited onto a substrate using a high-velocity gas stream. Aerosol jet printing offers several advantages over inkjet printing, including the ability to print on non-planar surfaces and the use of a wider range of materials.
Advantages of Aerosol Jet Printing
- Ability to print on non-planar surfaces and three-dimensional structures
- Higher resolution than inkjet printing, with feature sizes as small as 10 microns
- Compatible with a wide range of conductive materials, including metals, polymers, and ceramics
Limitations of Aerosol Jet Printing
- Higher equipment costs compared to inkjet printing
- Slower print speeds than inkjet printing
- May require specialized substrate preparation to ensure proper adhesion
Selective Laser Sintering (SLS)
Selective laser sintering is an additive manufacturing technique that uses a high-power laser to fuse powdered materials into a solid structure. In the context of PCB production, SLS can be used to create conductive traces by sintering powdered metals, such as copper or aluminum, onto a substrate. This method offers the ability to create complex three-dimensional structures and can be used with a variety of materials.
Advantages of Selective Laser Sintering
- Ability to create complex three-dimensional structures
- Compatible with a wide range of materials, including metals, polymers, and ceramics
- High strength and durability of the final product
Limitations of Selective Laser Sintering
- Higher equipment costs compared to other additive manufacturing methods
- Slower print speeds than inkjet or aerosol jet printing
- May require post-processing steps, such as cleaning and surface finishing
Applications of Additive Manufacturing in PCB Production
Additive manufacturing techniques have found numerous applications in the production of PCBs, ranging from rapid prototyping to the creation of custom, high-performance electronics.
Rapid Prototyping and Iteration
One of the most significant advantages of additive manufacturing in PCB production is the ability to quickly and cost-effectively produce prototype boards. This allows designers and engineers to test and refine their designs faster, reducing the overall development time and cost. Additive manufacturing techniques, such as inkjet printing, enable the creation of functional prototype PCBs in a matter of hours, compared to the days or weeks required for traditional manufacturing methods.
Customization and Low-Volume Production
Additive manufacturing also offers the ability to create highly customized PCBs for specific applications. This is particularly useful for low-volume production runs, where the cost of traditional manufacturing methods may be prohibitive. With additive manufacturing, custom PCBs can be produced on-demand, reducing the need for large inventory stockpiles and minimizing waste.
High-Performance Electronics
Additive manufacturing techniques, such as aerosol jet printing and selective laser sintering, enable the creation of high-performance electronics with complex geometries and advanced materials. These methods allow for the integration of multiple materials, such as conductive and insulating layers, into a single PCB, enabling the creation of advanced electronic devices with improved functionality and reliability.
Flexible and Wearable Electronics
Additive manufacturing has also paved the way for the development of flexible and wearable electronics. By using flexible substrates and conductive inks, additive manufacturing techniques can create PCBs that can bend, stretch, and conform to various shapes. This has led to the development of novel applications, such as smart clothing, medical sensors, and flexible displays.
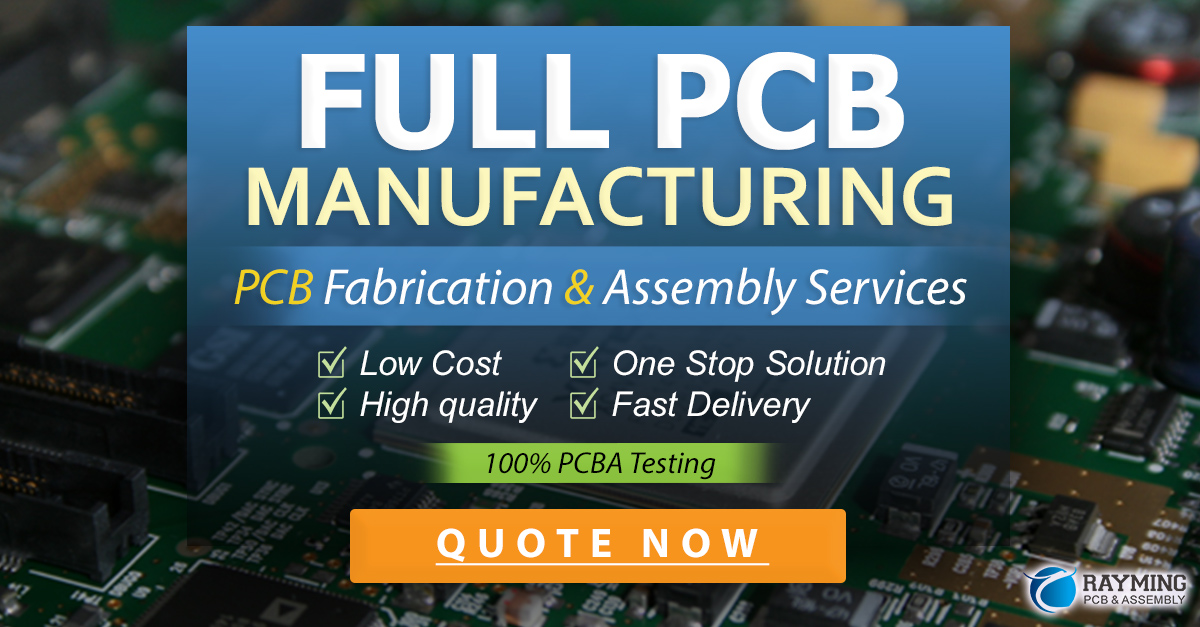
Challenges and Future Developments
Despite the numerous advantages of additive manufacturing in PCB production, there are still several challenges that need to be addressed to fully realize its potential.
Material Limitations
One of the main challenges faced by additive manufacturing in PCB production is the limited range of materials that can be used. While conductive inks and powdered metals have been successfully employed, there is still a need for the development of new materials with improved electrical and mechanical properties. Researchers are currently exploring the use of novel materials, such as graphene and conductive polymers, to enhance the performance of additively manufactured PCBs.
Scalability and Speed
Another challenge is the scalability and speed of additive manufacturing processes for PCB production. While additive manufacturing is well-suited for rapid prototyping and low-volume production, it may not be as efficient as traditional manufacturing methods for high-volume production. Efforts are being made to improve the speed and throughput of additive manufacturing techniques, such as the development of multi-nozzle inkjet printheads and high-speed laser sintering systems.
Integration with Traditional Manufacturing
As additive manufacturing continues to gain traction in the PCB industry, there is a need for seamless integration with traditional manufacturing processes. This involves the development of hybrid manufacturing systems that combine the strengths of both additive and subtractive methods, as well as the establishment of standards and guidelines for the design and production of additively manufactured PCBs.
Frequently Asked Questions (FAQ)
-
What is the difference between additive manufacturing and traditional PCB manufacturing methods?
Additive manufacturing builds up a PCB layer by layer, adding material only where needed. Traditional methods, such as etching and drilling, start with a full substrate and remove material to create the desired circuit pattern. -
What are the main benefits of using additive manufacturing for PCB production?
The main benefits include rapid prototyping, increased design freedom, reduced waste, and shorter lead times. Additive manufacturing also enables the creation of complex geometries and the integration of multiple materials. -
Can additive manufacturing be used for high-volume PCB production?
Currently, additive manufacturing is more suitable for low-volume production and rapid prototyping. However, efforts are being made to improve the speed and scalability of additive manufacturing processes for higher-volume production. -
What materials can be used in additive manufacturing for PCBs?
The most common materials used are conductive inks, such as silver and copper nanoparticles, and powdered metals, such as copper and aluminum. Researchers are also exploring the use of novel materials like graphene and conductive polymers. -
What are the main challenges facing the adoption of additive manufacturing in the PCB industry?
The main challenges include material limitations, scalability and speed of production, and the need for seamless integration with traditional manufacturing processes. Addressing these challenges will be crucial for the widespread adoption of additive manufacturing in the PCB industry.
Conclusion
Additive manufacturing has emerged as a game-changer in the PCB industry, offering numerous advantages over traditional manufacturing methods. From rapid prototyping and increased design freedom to reduced waste and shorter lead times, additive manufacturing has the potential to revolutionize the way PCBs are designed and produced.
As the technology continues to evolve, we can expect to see new materials, improved production speeds, and seamless integration with traditional manufacturing processes. The adoption of additive manufacturing in the PCB industry will not only lead to more efficient and cost-effective production but also enable the creation of innovative, high-performance electronics that were previously impossible to achieve.
In conclusion, additive manufacturing represents a promising future for the PCB industry, and its continued development and adoption will be crucial for staying competitive in an ever-evolving technological landscape.
Leave a Reply