Introduction to Printed Circuit Boards (PCBs)
Printed Circuit Boards (PCBs) are the backbone of modern electronic devices. They are used in almost every electronic device we use today, from smartphones and laptops to medical equipment and aerospace systems. PCBs are essential because they provide a platform for electronic components to be mounted and connected, enabling the device to function as intended.
PCBs come in different types, each with its own unique characteristics and applications. Two of the most common types of PCBs are Rigid PCBs and Flexible PCBs. In this article, we will explore the differences between these two types of PCBs, their advantages and disadvantages, and their applications.
What are Rigid PCBs?
Rigid PCBs are the most common type of PCBs used in electronic devices. They are made from a rigid, non-flexible material, typically FR-4, which is a glass-reinforced epoxy laminate. Rigid PCBs are known for their durability, stability, and high performance, making them ideal for a wide range of applications.
Characteristics of Rigid PCBs
- Made from a rigid, non-flexible material (FR-4)
- High durability and stability
- Excellent mechanical strength
- Good thermal conductivity
- Suitable for high-speed applications
- Available in various thicknesses and copper weights
- Can be single-sided, double-sided, or multi-layered
Advantages of Rigid PCBs
- High reliability and long lifespan
- Excellent electrical insulation properties
- Good heat dissipation
- Suitable for high-density component mounting
- Cost-effective for high-volume production
- Easy to assemble and solder components
Disadvantages of Rigid PCBs
- Limited flexibility and inability to conform to irregular shapes
- Heavier and thicker compared to flexible PCBs
- May require additional connectors for assembly
- Limited ability to withstand vibration and shock
Applications of Rigid PCBs
Rigid PCBs are used in a wide variety of electronic devices and systems, such as:
- Consumer electronics (smartphones, tablets, laptops, etc.)
- Industrial equipment (controllers, sensors, automation systems)
- Medical devices (diagnostic equipment, monitoring systems)
- Automotive electronics (engine control units, infotainment systems)
- Aerospace and defense systems (avionics, communication devices)
What are Flexible PCBs?
Flexible PCBs, also known as flex circuits, are a type of PCB that can bend and flex without damaging the electronic components or connections. They are made from a thin, flexible substrate, typically polyimide or polyester, which allows them to conform to various shapes and fit into tight spaces.
Characteristics of Flexible PCBs
- Made from a thin, flexible substrate (polyimide or polyester)
- Ability to bend and flex without damaging components or connections
- Lightweight and thin profile
- High resistance to vibration and shock
- Suitable for applications with limited space
- Can be single-sided, double-sided, or multi-layered
- Available in various thicknesses and copper weights
Advantages of Flexible PCBs
- Conformability to irregular shapes and tight spaces
- Reduced weight and thickness compared to rigid PCBs
- Excellent resistance to vibration and shock
- Improved signal integrity due to shorter interconnections
- Reduced assembly time and costs (fewer connectors required)
- Increased design flexibility and product miniaturization
Disadvantages of Flexible PCBs
- Higher material and fabrication costs compared to rigid PCBs
- Limited heat dissipation capabilities
- Reduced mechanical strength and durability
- More complex design and manufacturing process
- Susceptible to damage from repeated bending and flexing
Applications of Flexible PCBs
Flexible PCBs are used in various applications that require flexibility, lightweight design, and resistance to vibration and shock, such as:
- Wearable electronics (smartwatches, fitness trackers)
- Medical devices (implantable devices, diagnostic equipment)
- Automotive electronics (sensors, displays, control modules)
- Aerospace and defense systems (avionics, communication devices)
- Consumer electronics (smartphones, cameras, printers)
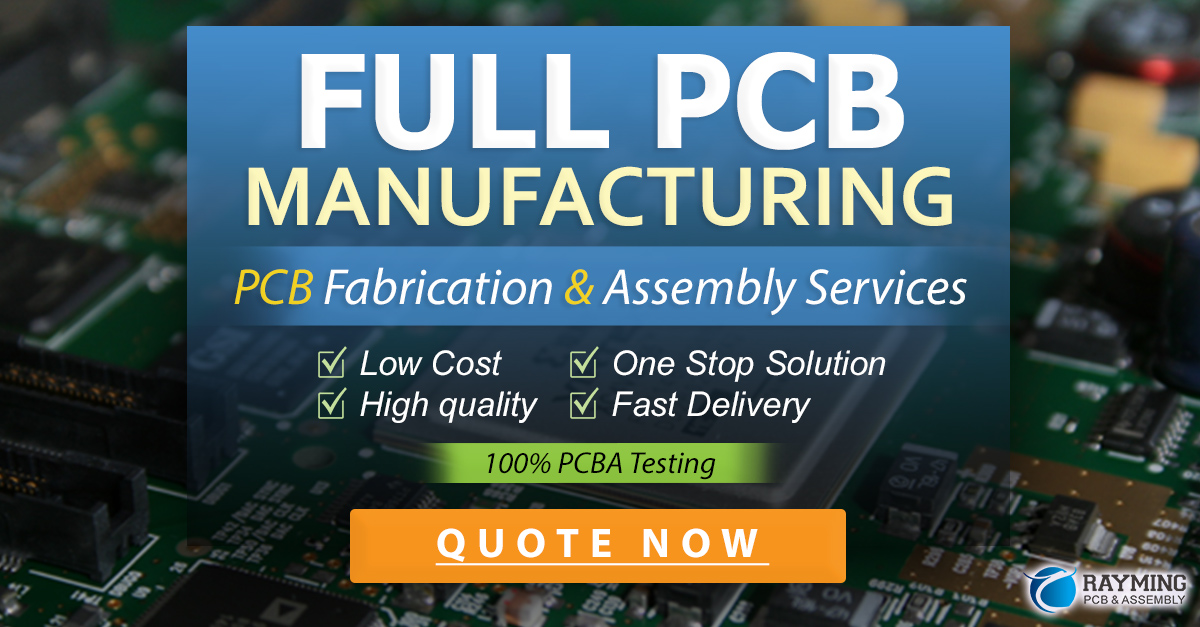
Rigid vs Flexible PCB: Key Differences
Characteristic | Rigid PCB | Flexible PCB |
---|---|---|
Material | FR-4 (glass-reinforced epoxy) | Polyimide or polyester |
Flexibility | Non-flexible, rigid | Flexible, can bend and conform to shapes |
Thickness | Thicker (typically 0.8mm to 3.2mm) | Thinner (typically 0.1mm to 0.3mm) |
Weight | Heavier | Lighter |
Durability | High mechanical strength and durability | Lower mechanical strength, susceptible to damage from repeated bending |
Heat Dissipation | Good thermal conductivity and heat dissipation | Limited heat dissipation capabilities |
Assembly | May require additional connectors | Fewer connectors required, reduced assembly time and costs |
Design Flexibility | Limited ability to conform to irregular shapes | High conformability to irregular shapes and tight spaces |
Vibration and Shock Resistance | Limited ability to withstand vibration and shock | Excellent resistance to vibration and shock |
Cost | Cost-effective for high-volume production | Higher material and fabrication costs |
Choosing Between Rigid and Flexible PCBs
When deciding between rigid and flexible PCBs for your project, consider the following factors:
-
Application requirements: Determine if your application requires flexibility, conformability to irregular shapes, or resistance to vibration and shock.
-
Space constraints: If your device has limited space or needs to fit into tight spaces, a flexible PCB may be the better choice.
-
Weight and thickness: If weight and thickness are critical factors in your design, flexible PCBs offer a lighter and thinner solution compared to rigid PCBs.
-
Durability and mechanical strength: Rigid PCBs provide higher durability and mechanical strength, making them suitable for applications that require robustness.
-
Heat dissipation: If your application generates significant heat, rigid PCBs offer better thermal conductivity and heat dissipation compared to flexible PCBs.
-
Cost: Rigid PCBs are generally more cost-effective for high-volume production, while flexible PCBs have higher material and fabrication costs.
-
Assembly: Flexible PCBs require fewer connectors and can reduce assembly time and costs, while rigid PCBs may require additional connectors for assembly.
Future Trends in PCB Technology
As electronic devices continue to evolve and become more complex, PCB technology must adapt to meet new challenges and demands. Some of the future trends in PCB technology include:
-
Increased adoption of flexible and stretchable PCBs: With the rise of wearable electronics and IoT devices, flexible and stretchable PCBs will become more prevalent, enabling the development of innovative and conformable products.
-
High-density interconnect (HDI) PCBs: HDI PCBs allow for higher component density and improved signal integrity, facilitating the miniaturization of electronic devices and the development of advanced applications.
-
Embedded components: Integrating components within the PCB layers can save space, reduce assembly time, and improve device performance, leading to more compact and efficient designs.
-
Advanced materials: The development of new PCB materials with improved thermal, electrical, and mechanical properties will enable the creation of PCBs that can withstand harsh environments and meet the demands of emerging technologies.
-
Eco-friendly manufacturing: As environmental concerns continue to grow, PCB manufacturers will focus on developing more sustainable and eco-friendly production processes, such as using lead-free materials and reducing waste.
FAQ
- Can flexible PCBs completely replace rigid PCBs?
-
No, flexible PCBs cannot completely replace rigid PCBs. While flexible PCBs offer unique advantages, such as conformability and resistance to vibration and shock, rigid PCBs still have their place in applications that require high durability, mechanical strength, and better heat dissipation. The choice between rigid and flexible PCBs depends on the specific requirements of the application.
-
Are flexible PCBs more expensive than rigid PCBs?
-
Yes, flexible PCBs are generally more expensive than rigid PCBs due to higher material and fabrication costs. The thin, flexible substrates used in flexible PCBs, such as polyimide or polyester, are more costly than the FR-4 material used in rigid PCBs. Additionally, the manufacturing process for flexible PCBs is more complex, contributing to higher overall costs.
-
Can rigid and flexible PCBs be combined in a single design?
-
Yes, rigid and flexible PCBs can be combined in a single design, known as a rigid-flex PCB. Rigid-flex PCBs incorporate both rigid and flexible sections, allowing for the benefits of both types of PCBs in one design. This combination enables the creation of more complex and versatile electronic devices that require both stability and flexibility.
-
How do I choose the right thickness for my rigid or flexible PCB?
-
The choice of PCB thickness depends on several factors, such as the application requirements, component sizes, and manufacturing capabilities. For rigid PCBs, common thicknesses range from 0.8mm to 3.2mm, with 1.6mm being a popular choice. Flexible PCBs are typically thinner, ranging from 0.1mm to 0.3mm. Consult with your PCB manufacturer to determine the most suitable thickness for your specific design.
-
What are the challenges in designing flexible PCBs compared to rigid PCBs?
- Designing flexible PCBs presents several challenges compared to rigid PCBs. These include considering the bending and flexing requirements, ensuring the proper placement of components to minimize stress, and selecting suitable materials that can withstand repeated bending. Additionally, the manufacturing process for flexible PCBs is more complex, requiring specialized equipment and expertise. It is essential to work closely with an experienced PCB manufacturer to ensure the successful design and production of flexible PCBs.
Conclusion
Rigid PCBs and flexible PCBs are two distinct types of printed circuit boards, each with its own unique characteristics, advantages, and applications. Rigid PCBs offer high durability, mechanical strength, and better heat dissipation, making them suitable for applications that require robustness and stability. On the other hand, flexible PCBs provide conformability, lightweight design, and resistance to vibration and shock, making them ideal for applications with limited space or that require flexibility.
When choosing between rigid and flexible PCBs, it is essential to consider the specific requirements of your application, such as space constraints, weight and thickness, durability, heat dissipation, and cost. In some cases, a combination of both rigid and flexible PCBs, known as rigid-flex PCBs, can offer the best of both worlds, enabling the creation of more complex and versatile electronic devices.
As PCB technology continues to evolve, we can expect to see increased adoption of flexible and stretchable PCBs, high-density interconnect (HDI) PCBs, embedded components, advanced materials, and eco-friendly manufacturing processes. By staying informed about these developments and working closely with experienced PCB manufacturers, engineers and designers can create innovative and high-performance electronic devices that meet the demands of the future.
Leave a Reply