Introduction to PCB design guidelines
Printed Circuit Board (PCB) design is a critical aspect of electronic product development. Proper PCB design ensures that the board functions as intended, is reliable, and can be manufactured efficiently. However, designing a PCB that meets all these criteria can be challenging, especially for those new to the process. This article will provide a comprehensive guide to PCB design for assembly guidelines, covering key topics such as component placement, routing, signal integrity, and manufacturability.
The Importance of Following PCB Design Guidelines
Following PCB design guidelines is essential for several reasons:
- Functionality: A well-designed PCB ensures that the electronic components function as intended, minimizing the risk of errors and malfunctions.
- Reliability: Proper PCB design enhances the reliability of the board, reducing the likelihood of failures due to environmental factors, such as temperature, humidity, and vibration.
- Manufacturability: Adhering to PCB design guidelines makes the board easier to manufacture, reducing the risk of defects and improving production yield.
- Cost-effectiveness: By designing a PCB that is easy to manufacture and assemble, you can reduce production costs and improve overall cost-effectiveness.
Key Aspects of PCB Design Guidelines
Component Placement
Component placement is a critical aspect of PCB design, as it directly impacts the board’s functionality, reliability, and manufacturability. Here are some guidelines to follow when placing components on a PCB:
- Grouping: Group related components together to minimize the distance between them, reducing the length of traces and improving signal integrity.
- Orientation: Orient components in a consistent direction to facilitate assembly and minimize the risk of errors during the manufacturing process.
- Clearance: Ensure that there is sufficient clearance between components to allow for proper soldering and to prevent short circuits.
- Thermal considerations: Place components that generate significant heat away from temperature-sensitive components to prevent thermal damage.
Component Type | Placement Guidelines |
---|---|
ICs | Place near related components, consider thermal dissipation |
Resistors | Group by value, orient consistently |
Capacitors | Place near ICs for decoupling, consider polarity |
Connectors | Place near board edges, consider mechanical stress |
Power components | Place near power input, consider thermal dissipation and high current traces |
Routing
Routing is the process of creating the conductive traces that connect components on the PCB. Proper routing is essential for ensuring signal integrity and minimizing electromagnetic interference (EMI). Here are some guidelines to follow when routing a PCB:
- Width: Use appropriate trace widths based on the current requirements of the circuit. Wider traces can handle higher currents and reduce voltage drop.
- Spacing: Maintain adequate spacing between traces to minimize crosstalk and EMI. The spacing required depends on the signal frequency and the board’s layer stack-up.
- Vias: Use vias sparingly, as they can introduce signal integrity issues and increase manufacturing costs. When using vias, ensure that they are properly sized and spaced.
- Length matching: Match the length of traces for critical signals, such as clock and high-speed data lines, to maintain signal integrity and prevent timing issues.
Signal Type | Routing Guidelines |
---|---|
Power | Use wide traces, minimize voltage drop, consider current density |
Ground | Use ground planes, provide multiple return paths, minimize loop area |
High-speed | Match trace lengths, control impedance, minimize vias |
Analog | Separate from digital signals, use guard rings, consider shielding |
Digital | Use appropriate spacing, consider crosstalk and EMI |
Signal Integrity
Signal integrity refers to the quality of the electrical signals transmitted through the PCB. Maintaining signal integrity is crucial for ensuring that the board functions as intended and meets performance requirements. Here are some guidelines for maintaining signal integrity:
- Impedance control: Match the impedance of the traces to the impedance of the source and load to minimize reflections and signal distortion.
- Termination: Use appropriate termination techniques, such as series termination or parallel termination, to minimize reflections and improve signal quality.
- Crosstalk: Minimize crosstalk between adjacent traces by maintaining adequate spacing and using guard traces or ground planes where necessary.
- EMI: Reduce EMI by using proper grounding techniques, minimizing loop areas, and using shielding or filtering where required.
Signal Integrity Issue | Mitigation Techniques |
---|---|
Reflections | Impedance matching, termination |
Crosstalk | Increase spacing, use guard traces, control trace geometry |
EMI | Proper grounding, minimize loop areas, shielding, filtering |
Attenuation | Use appropriate trace widths, minimize trace length |
Jitter | Control impedance, minimize vias, use appropriate termination |
Manufacturability
Designing a PCB that is easy to manufacture is essential for reducing production costs and improving yield. Here are some guidelines for enhancing the manufacturability of your PCB:
- Design for Assembly (DFA): Follow DFA principles, such as using standard component sizes, minimizing the number of unique parts, and providing adequate clearances for automated assembly equipment.
- Panelization: Design your board to fit efficiently into a standard panel size to maximize material utilization and reduce manufacturing costs.
- Testability: Incorporate test points and other features that facilitate automated testing, such as boundary scan or flying probe testing.
- Documentation: Provide clear and comprehensive documentation, including assembly drawings, bill of materials (BOM), and Gerber files, to ensure that the manufacturer has all the necessary information to produce your board.
Manufacturability Factor | Guidelines |
---|---|
Component selection | Use standard sizes, minimize unique parts, consider availability |
Board size and shape | Design for efficient panelization, consider assembly requirements |
Solder mask and legend | Provide adequate clearances, use standard colors and fonts |
Silkscreen and markings | Ensure clarity and legibility, consider assembly requirements |
Drill holes and vias | Use standard sizes, minimize number of unique sizes |
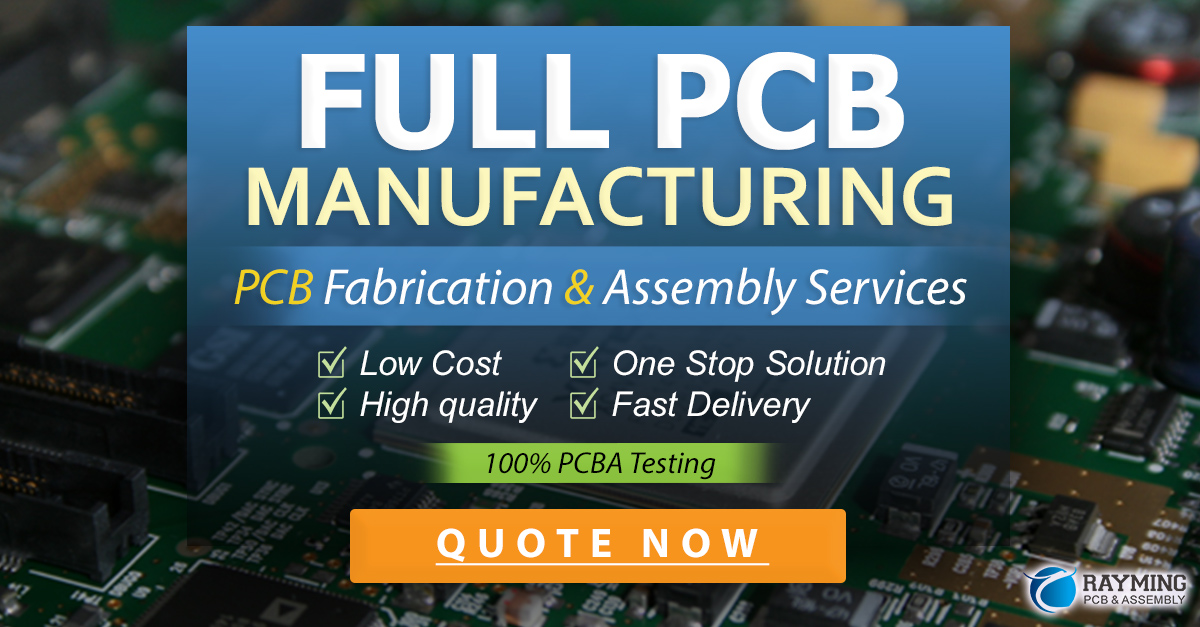
Frequently Asked Questions (FAQ)
-
What are the most important factors to consider when placing components on a PCB?
When placing components on a PCB, the most important factors to consider are grouping related components together, orienting components consistently, ensuring adequate clearances, and considering thermal dissipation requirements. -
How can I minimize crosstalk between traces on my PCB?
To minimize crosstalk between traces, maintain adequate spacing between them, use guard traces or ground planes where necessary, and control trace geometry to minimize coupling. -
What is the importance of impedance control in PCB design?
Impedance control is important in PCB design because it helps to minimize reflections and signal distortion, which can degrade signal integrity and lead to performance issues. Matching the impedance of the traces to the impedance of the source and load is crucial for maintaining signal quality. -
How can I design my PCB to be easily manufacturable?
To design a PCB that is easily manufacturable, follow Design for Assembly (DFA) principles, such as using standard component sizes, minimizing unique parts, and providing adequate clearances for automated assembly equipment. Additionally, design your board to fit efficiently into a standard panel size, incorporate testability features, and provide clear and comprehensive documentation. -
What are the benefits of using a ground plane in my PCB design?
Using a ground plane in your PCB design offers several benefits, including improved signal integrity, reduced EMI, and better thermal management. Ground planes provide a low-impedance return path for signals, minimizing loop areas and reducing the risk of crosstalk and EMI. They also help to distribute heat more evenly across the board, improving thermal performance.
Conclusion
Designing a PCB that meets functionality, reliability, and manufacturability requirements can be a complex task, but following established design guidelines can greatly simplify the process. By considering factors such as component placement, routing, signal integrity, and manufacturability, you can create a PCB that performs as intended and is cost-effective to produce.
Remember to keep the guidelines discussed in this article in mind when designing your next PCB, and don’t hesitate to consult with experienced professionals or reference industry standards for more detailed guidance. With careful planning and attention to detail, you can develop a PCB that meets your specific needs and exceeds your expectations.
Leave a Reply