The Importance of Medical PCB Standards
Medical PCBs are critical components of a wide range of medical devices, from simple monitoring equipment to complex diagnostic and treatment systems. These PCBs must be able to perform reliably and accurately in demanding environments, often for extended periods of time. Any failure or malfunction of a medical PCB can have serious consequences for patient health and safety.
To mitigate these risks, medical PCBs are subject to a range of standards and regulations that govern their design, manufacture, and assembly. These standards ensure that medical PCBs meet the highest levels of quality, reliability, and performance, and that they are suitable for use in medical applications.
Compliance with these standards is not only a legal requirement but also a moral imperative for manufacturers of medical devices. By adhering to these standards, manufacturers can ensure that their products are safe and effective for patients, and that they are contributing to the overall quality and integrity of the healthcare system.
Key Standards and Regulations for Medical PCBs
There are several key standards and regulations that apply to the assembly of medical PCBs. These include:
IPC Standards
The Association Connecting Electronics Industries (IPC) is a global trade association that develops and publishes standards for the electronics industry. Several IPC standards are directly relevant to medical PCB assembly, including:
- IPC-A-600: Acceptability of Printed Boards
- IPC-A-610: Acceptability of Electronic Assemblies
- IPC-6012: Qualification and Performance Specification for Rigid Printed Boards
- IPC-6013: Qualification and Performance Specification for Flexible/Rigid-Flexible Printed Boards
These standards specify requirements for the design, fabrication, and assembly of PCBs, including criteria for acceptability, quality, and performance. Manufacturers of medical PCBs must comply with these standards to ensure that their products meet the necessary levels of reliability and functionality.
ISO Standards
The International Organization for Standardization (ISO) is an independent, non-governmental organization that develops and publishes standards for a wide range of industries, including healthcare. Several ISO standards are relevant to medical PCB assembly, including:
- ISO 13485: Medical Devices – Quality Management Systems – Requirements for Regulatory Purposes
- ISO 14971: Medical Devices – Application of Risk Management to Medical Devices
These standards specify requirements for quality management systems and risk management processes in the manufacture of medical devices. Manufacturers of medical PCBs must implement these systems and processes to ensure that their products are safe, effective, and compliant with regulatory requirements.
FDA Regulations
The U.S. Food and Drug Administration (FDA) is responsible for regulating the manufacture and sale of medical devices in the United States. The FDA has established several regulations that apply to medical PCB assembly, including:
- 21 CFR Part 820: Quality System Regulation
- 21 CFR Part 11: Electronic Records; Electronic Signatures
These regulations specify requirements for quality management systems, design controls, production and process controls, and electronic record-keeping in the manufacture of medical devices. Manufacturers of medical PCBs must comply with these regulations to ensure that their products are safe, effective, and traceable.
Specific Requirements for Medical PCB Assembly
In addition to the general standards and regulations outlined above, there are several specific requirements that apply to the assembly of medical PCBs. These requirements are designed to ensure that medical PCBs are able to withstand the unique demands of medical applications, including:
- High reliability and durability
- Resistance to harsh environments and sterilization processes
- Electromagnetic compatibility (EMC) and interference (EMI) shielding
- Biocompatibility and non-toxicity
To meet these requirements, medical PCBs must be designed and assembled using specialized materials, components, and processes. For example:
- Medical-grade laminates and substrates must be used to ensure high reliability and durability
- Conformal coatings and encapsulants must be used to protect against moisture, dust, and other contaminants
- Specialized cleaning and sterilization processes must be used to ensure biocompatibility and non-toxicity
- Shielding and grounding techniques must be used to ensure EMC and EMI protection
Manufacturers of medical PCBs must carefully select and qualify their materials, components, and processes to ensure that they meet these specific requirements. They must also implement rigorous testing and validation procedures to verify the performance and reliability of their products.
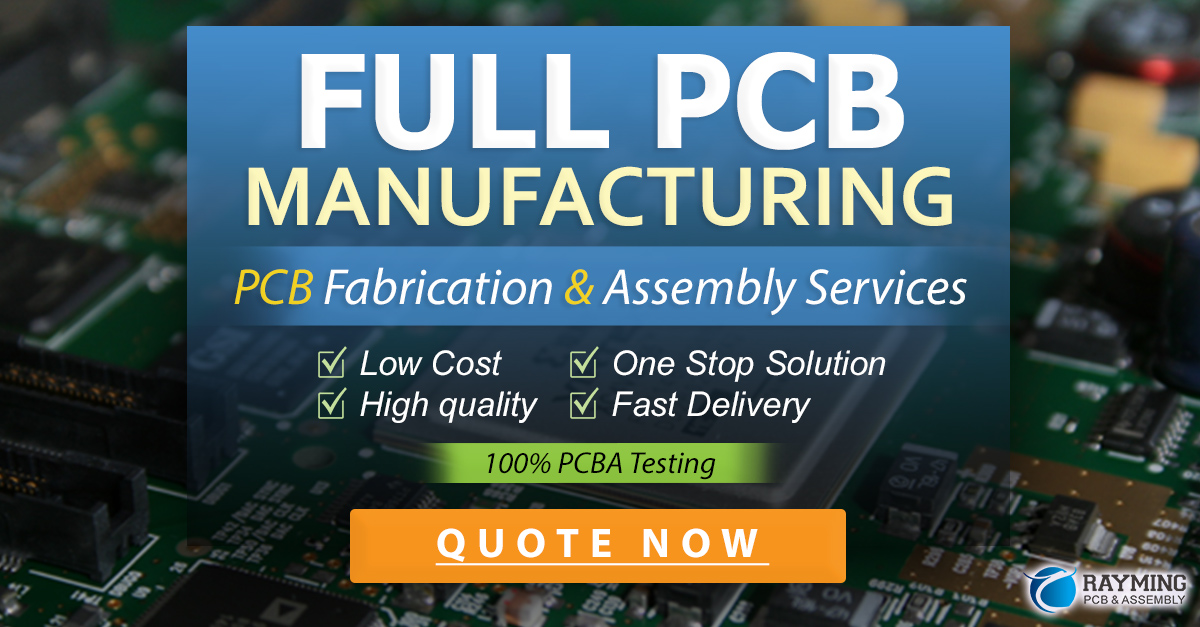
Ensuring Compliance with Medical PCB Standards
To ensure compliance with the various standards and regulations that govern medical PCB assembly, manufacturers must implement a comprehensive quality management system (QMS). A QMS is a set of policies, processes, and procedures that are designed to ensure that products are consistently manufactured to the required levels of quality and safety.
Key elements of a QMS for medical PCB assembly include:
- Design controls: A systematic approach to product design that includes risk management, verification, and validation activities
- Production and process controls: Procedures for controlling and monitoring the manufacturing process to ensure consistency and quality
- Traceability: The ability to track and trace products throughout the supply chain, from raw materials to finished goods
- Training and competency: Programs for ensuring that personnel are adequately trained and qualified to perform their assigned tasks
- Continuous improvement: A commitment to ongoing monitoring, measurement, and improvement of the QMS and its processes
Manufacturers of medical PCBs must also undergo regular audits and inspections by regulatory bodies and third-party certification agencies to verify their compliance with relevant standards and regulations. These audits may include on-site visits, document reviews, and product testing to ensure that the manufacturer’s QMS is effective and that their products meet the required levels of quality and safety.
The Benefits of Medical PCB Standards
While compliance with medical PCB standards and regulations can be a complex and costly undertaking for manufacturers, the benefits of doing so are significant. By adhering to these standards, manufacturers can:
- Ensure the safety and effectiveness of their products for patients
- Reduce the risk of product failures, recalls, and liability claims
- Enhance their reputation and credibility in the medical device industry
- Access new markets and customers that require compliance with specific standards and regulations
- Continuously improve their processes and products through the implementation of a robust QMS
In the end, the ultimate beneficiary of medical PCB standards is the patient. By ensuring that medical devices are designed, manufactured, and assembled to the highest levels of quality and safety, these standards help to promote better health outcomes and improved quality of life for patients around the world.
FAQs
-
What are the consequences of non-compliance with medical PCB standards and regulations?
Non-compliance with medical PCB standards and regulations can result in serious consequences for manufacturers, including product recalls, fines, legal liability, and damage to reputation. In extreme cases, non-compliance can also pose risks to patient safety and public health. -
How often do medical PCB standards and regulations change?
Medical PCB standards and regulations are subject to periodic review and revision to keep pace with advances in technology and changes in the healthcare industry. Manufacturers must stay up-to-date with the latest standards and regulations to ensure ongoing compliance. -
What is the difference between IPC and ISO standards for medical PCBs?
IPC standards are specific to the electronics industry and focus on the design, fabrication, and assembly of PCBs. ISO standards, on the other hand, are more general in nature and focus on quality management systems and risk management processes across a range of industries, including healthcare. -
How can manufacturers ensure that their medical PCBs are biocompatible and non-toxic?
To ensure biocompatibility and non-toxicity, manufacturers must carefully select materials and components that have been tested and approved for use in medical applications. They must also implement specialized cleaning and sterilization processes to remove any contaminants or residues that could pose risks to patients. -
What is the role of traceability in medical PCB assembly?
Traceability is a critical aspect of medical PCB assembly that enables manufacturers to track and trace products throughout the supply chain. This includes tracking raw materials, components, and finished goods, as well as documenting any changes or modifications made to the product during the manufacturing process. Traceability helps to ensure that products are consistently manufactured to the required levels of quality and safety, and that any issues or defects can be quickly identified and resolved.
Standard/Regulation | Scope | Key Requirements |
---|---|---|
IPC-A-600 | Acceptability of printed boards | Visual and dimensional criteria for PCBs |
IPC-A-610 | Acceptability of electronic assemblies | Acceptance criteria for PCB assemblies |
IPC-6012 | Qualification and performance of rigid PCBs | Material, construction, and performance requirements for rigid PCBs |
IPC-6013 | Qualification and performance of flexible/rigid-flexible PCBs | Material, construction, and performance requirements for flexible/rigid-flexible PCBs |
ISO 13485 | Quality management systems for medical devices | Requirements for design, production, installation, and servicing of medical devices |
ISO 14971 | Risk management for medical devices | Requirements for identifying, analyzing, evaluating, and controlling risks associated with medical devices |
21 CFR Part 820 | Quality system regulation for medical devices | Requirements for design, manufacturing, packaging, labeling, storage, installation, and servicing of medical devices |
21 CFR Part 11 | Electronic records and signatures | Requirements for the use of electronic records and signatures in the manufacture of medical devices |
In conclusion, the standards and regulations that govern medical PCB assembly are complex and multifaceted, reflecting the critical importance of these components in ensuring the safety and effectiveness of medical devices. By adhering to these standards and implementing robust quality management systems, manufacturers can ensure that their products meet the highest levels of quality and reliability, while also promoting better health outcomes for patients around the world. As technology continues to advance and the healthcare industry evolves, it is likely that these standards and regulations will also continue to evolve to keep pace with changing needs and expectations. Manufacturers that are able to stay ahead of the curve and maintain a commitment to quality and compliance will be well-positioned to succeed in this dynamic and demanding industry.
Leave a Reply