Introduction to Metal Core PCB
A Metal Core PCB (MCPCB) is a type of printed circuit board that uses a metal substrate as its base material instead of the traditional FR-4 laminate. The metal substrate, typically aluminum, provides excellent thermal conductivity, allowing for better heat dissipation compared to standard PCBs. This makes MCPCBs ideal for applications that generate high amounts of heat, such as power electronics, LED lighting, and automotive systems.
Advantages of Metal Core PCBs
- Enhanced thermal management
- Improved reliability and longevity
- Reduced size and weight
- Better mechanical stability
Structure and Composition of MCPCBs
Layers of a Metal Core PCB
A typical MCPCB consists of the following layers:
1. Dielectric layer
2. Circuit layer
3. Metal substrate (core)
Dielectric Layer
The dielectric layer is an insulating material that separates the circuit layer from the metal substrate. It is typically made of a thermally conductive, electrically insulating material such as aluminum oxide or boron nitride.
Circuit Layer
The circuit layer is where the electronic components and copper traces are located. It is similar to the top layer of a standard PCB.
Metal Substrate (Core)
The metal substrate serves as the base of the MCPCB and is responsible for its excellent thermal conductivity. Aluminum is the most commonly used material due to its good thermal properties, low cost, and ease of manufacturing.
Thermal Conductivity Comparison
Material | Thermal Conductivity (W/mK) |
---|---|
Aluminum | 205 |
Copper | 385 |
FR-4 | 0.3 |
As seen in the table above, aluminum and copper have significantly higher thermal conductivity compared to FR-4, making them ideal for use in MCPCBs.
Manufacturing Process of Metal Core PCBs
Step 1: Substrate Preparation
The aluminum substrate is cleaned and treated to improve adhesion with the dielectric layer.
Step 2: Dielectric Layer Application
The dielectric layer is applied to the metal substrate using techniques such as lamination, spraying, or screen printing.
Step 3: Circuit Layer Fabrication
The circuit layer is fabricated using standard PCB manufacturing techniques, such as photolithography and etching.
Step 4: Surface Finishing
The MCPCB undergoes surface finishing processes, such as HASL (Hot Air Solder Leveling) or ENIG (Electroless Nickel Immersion Gold), to protect the copper traces and improve solderability.
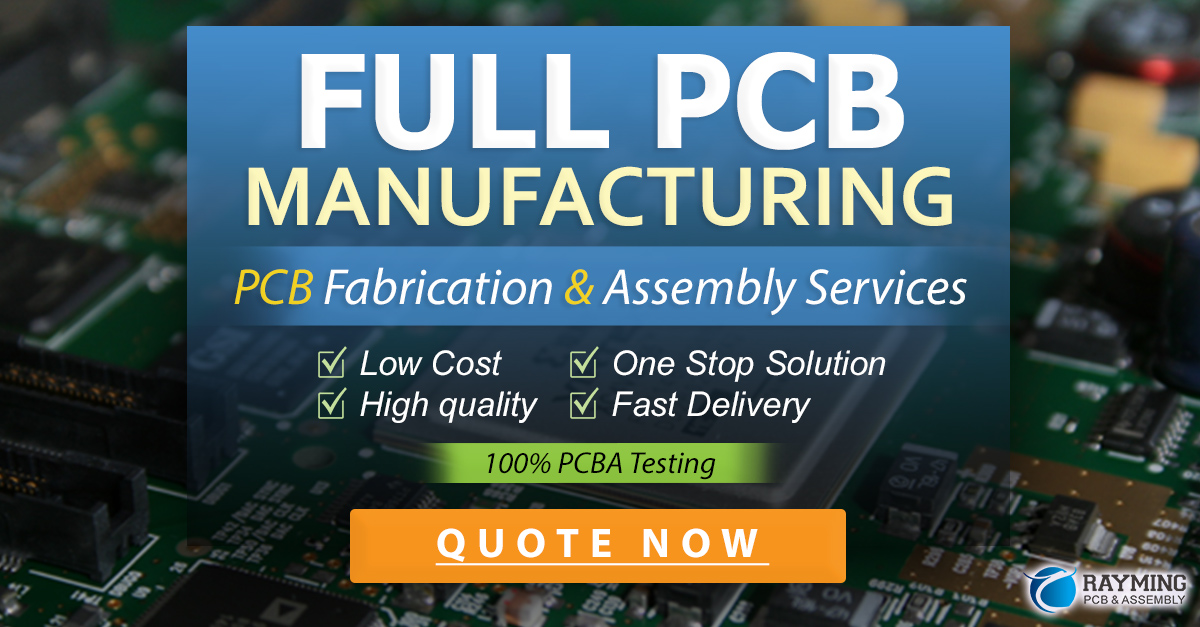
Applications of Metal Core PCBs
Power Electronics
MCPCBs are commonly used in power electronic applications, such as switch-mode power supplies (SMPS), motor drives, and inverters. The enhanced thermal management provided by MCPCBs helps dissipate heat generated by high-power components like MOSFETs and IGBTs.
LED Lighting
LED lighting applications benefit greatly from the use of MCPCBs. LEDs generate a significant amount of heat, which can negatively impact their performance and lifespan. By using MCPCBs, the heat generated by LEDs can be effectively dissipated, ensuring optimal performance and longer lifetimes.
Automotive Electronics
MCPCBs are increasingly being used in automotive electronic systems, such as engine control units (ECUs), power steering modules, and headlight control modules. The harsh operating environment in vehicles, including high temperatures and vibrations, makes the thermal management and mechanical stability of MCPCBs particularly advantageous.
Design Considerations for Metal Core PCBs
Thermal Management
When designing MCPCBs, it is essential to consider the thermal requirements of the application. Factors such as the power dissipation of components, ambient temperature, and airflow should be taken into account to ensure adequate thermal management.
Dielectric Layer Selection
The choice of dielectric material is crucial for the performance of an MCPCB. The dielectric layer should have high thermal conductivity to facilitate heat transfer from the circuit layer to the metal substrate. Additionally, it should have good electrical insulation properties to prevent short circuits.
Circuit Layer Design
The circuit layer design should be optimized for thermal performance. This can be achieved by using wider traces, multiple vias, and strategic component placement to minimize hot spots and ensure even heat distribution.
Mechanical Considerations
MCPCBs have different mechanical properties compared to standard PCBs due to the presence of the metal substrate. Designers should consider factors such as the coefficient of thermal expansion (CTE) mismatch between layers, mechanical stress, and vibration resistance when designing MCPCBs.
FAQs
1. What is the difference between a Metal Core PCB and a standard PCB?
A Metal Core PCB uses a metal substrate, typically aluminum, as its base material, while a standard PCB uses an FR-4 laminate. The metal substrate provides better thermal conductivity, allowing for improved heat dissipation.
2. What are the main advantages of using Metal Core PCBs?
The main advantages of using MCPCBs include enhanced thermal management, improved reliability and longevity, reduced size and weight, and better mechanical stability.
3. What are the common applications of Metal Core PCBs?
MCPCBs are commonly used in power electronics, LED lighting, and automotive electronics applications, where thermal management is critical.
4. How does the manufacturing process of Metal Core PCBs differ from standard PCBs?
The manufacturing process of MCPCBs involves additional steps, such as substrate preparation and dielectric layer application, compared to standard PCBs. However, the circuit layer fabrication and surface finishing processes are similar.
5. What are the key design considerations for Metal Core PCBs?
When designing MCPCBs, key considerations include thermal management, dielectric layer selection, circuit layer design, and mechanical factors such as CTE mismatch and vibration resistance.
Conclusion
Metal Core PCBs offer a unique solution for applications that require excellent thermal management and mechanical stability. By using a metal substrate, typically aluminum, MCPCBs provide enhanced heat dissipation compared to standard PCBs. This makes them ideal for power electronics, LED lighting, and automotive electronics applications.
When designing MCPCBs, it is essential to consider factors such as thermal management, dielectric layer selection, circuit layer design, and mechanical properties. By carefully addressing these considerations, designers can create MCPCBs that deliver optimal performance and reliability in demanding environments.
As technology continues to advance and the demand for high-performance electronic systems grows, the use of Metal Core PCBs is expected to increase. With their excellent thermal and mechanical properties, MCPCBs are well-positioned to meet the challenges of future electronic applications.
Leave a Reply