Understanding the Importance of PCB Prototyping
Before diving into the specifics of what makes a suitable PCB Prototype, let’s first understand the significance of prototyping in the PCB manufacturing process.
Benefits of PCB Prototyping
-
Design Validation: PCB prototyping allows you to validate your design before mass production. By creating a physical prototype, you can test the functionality, performance, and compatibility of your PCB design. This step helps identify and rectify any design flaws early in the development process, saving time and resources in the long run.
-
Cost Savings: Prototyping enables you to catch and fix design issues before committing to large-scale production. By addressing problems early, you can avoid costly mistakes and rework, ultimately reducing overall manufacturing costs.
-
Improved Product Quality: Through prototyping, you can thoroughly test and refine your PCB design. This iterative process leads to a higher-quality final product that meets your specifications and performs reliably.
-
Faster Time to Market: By identifying and resolving issues during the prototyping phase, you can streamline the development process and accelerate your product’s time to market. This competitive advantage can be crucial in today’s fast-paced electronics industry.
Now that we understand the importance of PCB prototyping, let’s explore the key factors to consider when determining the suitable PCB prototype for your project.
Factors to Consider for a Suitable PCB Prototype
1. PCB Material Selection
The choice of PCB material is a critical factor in determining the performance and reliability of your prototype. Different materials have varying properties that affect the PCB’s electrical, thermal, and mechanical characteristics. Some common PCB materials include:
-
FR-4: FR-4 is the most widely used PCB material due to its good electrical insulation properties, mechanical strength, and cost-effectiveness. It is suitable for a wide range of applications, including consumer electronics and industrial devices.
-
High-Frequency Materials: For high-frequency applications, such as RF and microwave circuits, specialized materials like Rogers, Teflon, or ceramic-based substrates are often used. These materials have lower dielectric loss and better signal integrity at higher frequencies.
-
Flexible PCBs: Flexible PCBs are made from materials like polyimide or polyester and offer the ability to bend and conform to various shapes. They are commonly used in wearable devices, medical equipment, and aerospace applications.
When selecting the PCB material for your prototype, consider the following factors:
- Electrical requirements (dielectric constant, loss tangent, etc.)
- Thermal properties (thermal conductivity, coefficient of thermal expansion)
- Mechanical properties (flexibility, strength, durability)
- Environmental factors (temperature range, humidity, chemical resistance)
- Cost and availability
PCB Material | Dielectric Constant | Loss Tangent | Thermal Conductivity (W/mK) | Typical Applications |
---|---|---|---|---|
FR-4 | 4.5 | 0.02 | 0.3 | General-purpose |
Rogers RO4003 | 3.55 | 0.0027 | 0.71 | High-frequency |
Polyimide | 3.5 | 0.002 | 0.12 | Flexible PCBs |
2. Layer Stack-up Design
The layer stack-up of your PCB prototype refers to the arrangement and configuration of the conductive layers and insulating materials. The number of layers and their arrangement significantly impact the PCB’s performance, manufacturability, and cost. Consider the following aspects when designing your PCB prototype’s layer stack-up:
-
Number of Layers: Determine the number of layers required based on your circuit complexity, routing requirements, and signal integrity considerations. More layers offer better signal routing options but increase manufacturing complexity and cost.
-
Signal Integrity: Proper layer stack-up design is crucial for maintaining signal integrity, especially in high-speed designs. Consider factors such as impedance control, crosstalk reduction, and electromagnetic compatibility (EMC) when designing your layer stack-up.
-
Power and Ground Planes: Incorporate dedicated power and ground planes to provide stable and low-impedance power distribution. Proper placement of these planes can also help reduce noise and improve signal quality.
-
Blind and Buried Vias: Blind and buried vias can be used to optimize routing and reduce board size. However, they also increase manufacturing complexity and cost compared to through-hole vias.
Layer Stack-up Example | Description |
---|---|
2-Layer | Signal – Ground |
4-Layer | Signal – Ground – Power – Signal |
6-Layer | Signal – Ground – Signal – Power – Ground – Signal |
8-Layer | Signal – Ground – Signal – Power – Ground – Signal – Ground – Signal |
3. Component Selection and Placement
The selection and placement of components on your PCB prototype are critical factors in ensuring proper functionality and manufacturability. Consider the following points:
-
Component Selection: Choose components that meet your design requirements in terms of functionality, performance, and reliability. Consider factors such as package type, size, and availability when selecting components.
-
Placement Guidelines: Follow best practices for component placement to optimize signal routing, minimize crosstalk, and improve manufacturability. Consider factors such as component orientation, spacing, and thermal management.
-
Design for Manufacturing (DFM): Incorporate DFM principles into your component selection and placement to ensure ease of manufacturing and assembly. This includes considerations such as component footprint compatibility, solder mask clearance, and assembly process requirements.
-
Thermal Management: Proper thermal management is crucial for the reliability and longevity of your PCB prototype. Consider the power dissipation of components and incorporate appropriate thermal management techniques, such as heatsinks, thermal vias, or copper pours.
4. Signal Integrity and EMC Considerations
Signal integrity and electromagnetic compatibility (EMC) are critical aspects to consider when designing your PCB prototype. Poor signal integrity and EMC can lead to performance issues, reliability problems, and non-compliance with regulatory standards. Consider the following factors:
-
Impedance Control: Ensure proper impedance control for high-speed signals to minimize reflections and signal distortion. This involves selecting appropriate trace widths, spacing, and dielectric materials.
-
Crosstalk Reduction: Minimize crosstalk between adjacent signals by optimizing trace routing, spacing, and layer stack-up design. Techniques such as guard traces, ground planes, and differential signaling can help reduce crosstalk.
-
EMC Compliance: Design your PCB prototype to meet relevant EMC standards and regulations. This includes considerations such as proper grounding, shielding, filtering, and layout techniques to minimize electromagnetic interference (EMI) and susceptibility.
-
Simulation and Analysis: Utilize simulation tools and analysis techniques to predict and optimize signal integrity and EMC performance. This includes signal integrity simulations, power integrity analysis, and EMC simulations.
5. Manufacturing Process and Capabilities
The manufacturing process and capabilities of your PCB prototype vendor play a significant role in determining the suitability of your prototype. Consider the following aspects:
-
Manufacturing Technology: Choose a PCB manufacturer that has the necessary technology and equipment to fabricate your prototype according to your specifications. This includes considerations such as minimum trace width, hole size, and layer count capabilities.
-
Quality Control: Ensure that your PCB manufacturer follows robust quality control processes to deliver high-quality prototypes. This includes inspections, testing, and adherence to industry standards such as IPC.
-
Lead Time: Consider the lead time required for PCB prototype fabrication and assembly. Faster lead times can accelerate your development process, but may come at a higher cost.
-
Cost: Evaluate the cost of PCB prototyping in relation to your budget and project requirements. Consider factors such as material costs, manufacturing costs, and minimum order quantities (MOQs).
Frequently Asked Questions (FAQ)
-
What is the difference between a PCB prototype and a production PCB?
A PCB prototype is a preliminary version of the PCB used for testing, validation, and design refinement before mass production. Production PCBs are the final version of the PCB used in the end product. Prototypes may have different materials, manufacturing processes, and tolerances compared to production PCBs. -
How long does it typically take to manufacture a PCB prototype?
The lead time for PCB prototype manufacturing can vary depending on factors such as design complexity, manufacturing process, and vendor capabilities. Typical lead times range from a few days to several weeks. Some PCB manufacturers offer expedited services for faster prototype delivery. -
What is the minimum order quantity (MOQ) for PCB prototypes?
The MOQ for PCB prototypes varies among manufacturers. Some vendors offer low MOQs, even as low as one piece, to facilitate prototype development. However, lower MOQs may come at a higher cost per unit compared to larger production runs. -
Can I use the same PCB design for both prototyping and production?
In many cases, the PCB design used for prototyping can be used for production as well. However, there may be some modifications required to optimize the design for mass production, such as adjusting tolerances, material selection, or manufacturing processes. It’s essential to work closely with your PCB manufacturer to ensure a smooth transition from prototyping to production. -
What should I do if my PCB prototype fails to meet the desired performance or functionality?
If your PCB prototype does not meet the expected performance or functionality, it’s crucial to analyze and identify the root cause of the issue. This may involve debugging, testing, and design revisions. Work closely with your PCB design team and manufacturer to troubleshoot and implement necessary changes to improve the prototype’s performance. Iterative prototyping may be required until the desired results are achieved.
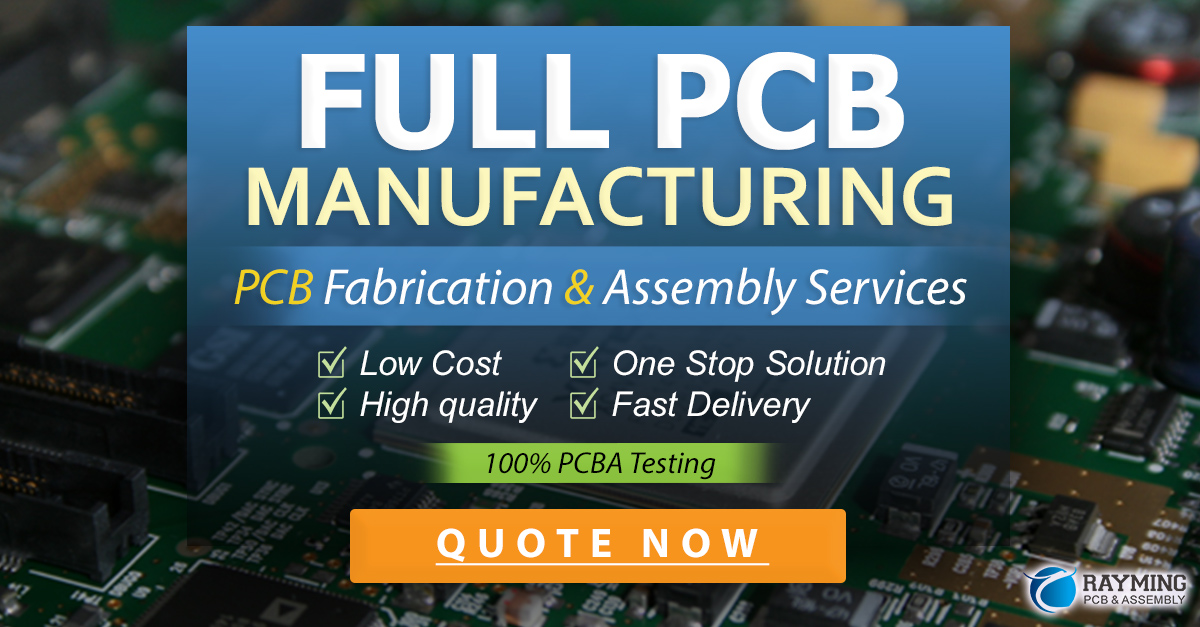
Conclusion
Selecting the suitable PCB prototype is a critical step in the successful development and manufacturing of electronic products. By considering factors such as PCB material selection, layer stack-up design, component selection and placement, signal integrity, and manufacturing process, you can ensure that your prototype meets your design requirements and performs reliably.
Remember to work closely with your PCB design team and manufacturing partner to optimize your prototype design and streamline the development process. Effective communication, attention to detail, and adherence to best practices will help you achieve a suitable PCB prototype that lays the foundation for a successful final product.
With a well-designed and thoroughly tested PCB prototype, you can confidently move forward with mass production, knowing that your electronic device has a solid foundation for performance and reliability.
Leave a Reply