ISO 9001 Certification
ISO 9001 is the international standard for quality management systems (QMS). It provides a framework for companies to consistently meet customer and regulatory requirements and continually improve their processes. An ISO 9001 certified PCB manufacturer has demonstrated their ability to provide high-quality products and services.
Key requirements of ISO 9001 include:
- Implementing a quality management system
- Setting quality objectives and measuring performance
- Conducting internal audits and management reviews
- Maintaining controlled documentation
- Managing nonconforming products
- Taking corrective and preventive action
ISO 9001 certification is awarded by accredited third-party certification bodies after thorough audits. Manufacturers must undergo surveillance audits to maintain their certification.
Benefits of ISO 9001 Certification |
---|
Consistent quality |
Improved efficiency and productivity |
Higher customer satisfaction |
Access to new markets |
Increased competitiveness |
UL Certification
Underwriters Laboratories (UL) is a global safety certification company that tests and certifies products, including PCBs. UL certification marks on PCBs provide assurance that they meet safety standards and won’t pose fire, shock, or other hazards.
Some common UL standards for PCBs include:
- UL 796 – Standard for Printed Wiring Boards
- UL 94 – Standard for Flammability of Plastic Materials
- UL 746 – Standard for Polymeric Materials
UL certified PCBs undergo rigorous testing, including:
- Flame resistance
- Electrical tracking resistance
- Thermal shock resistance
- Conductivity and insulance resistance
- Mechanical strength and adhesion
Having UL certified PCBs is often a requirement, especially for boards used in electrical equipment, appliances, and other end products that will undergo UL evaluation.
IPC Certifications
IPC (formerly the Institute for Interconnecting and Packaging Electronic Circuits) is the leading standards organization for the electronics manufacturing industry. IPC publishes standards covering nearly all aspects of PCB design, fabrication, assembly, and inspection.
Some key IPC standards for PCBs include:
Standard | Description |
---|---|
IPC-A-600 | Acceptability of Printed Circuit Boards |
IPC-6012 | Qualification and Performance Specification for Rigid Printed Boards |
IPC-6013 | Qualification and Performance Specification for Flexible/Rigid-Flexible Printed Boards |
IPC-6018 | Qualification and Performance Specification for High Frequency (Microwave) Printed Boards |
J-STD-003 | Solderability Tests for Printed Circuit Boards |
IPC also offers certification and qualification programs to validate a manufacturer’s ability to build PCBs to IPC standards:
- IPC-A-610 Acceptability of Electronic Assemblies – Certification on inspection criteria for PCB assemblies
- IPC-A-600 Acceptability of Printed Circuit Boards – Qualification to inspect bare PCBs
- IPC/WHMA-A-620 Requirements and Acceptance for Cable and Wire Harness Assemblies – Certification on inspection of cable and harness assemblies
- IPC J-STD-001 Requirements for Soldered Electrical and Electronic Assemblies – Certification on soldering processes and acceptability
IPC certified PCB manufacturers must demonstrate proficiency in interpreting and applying these standards through training and examinations. Choosing an IPC certified manufacturer ensures your PCBs will be built to industry standards.
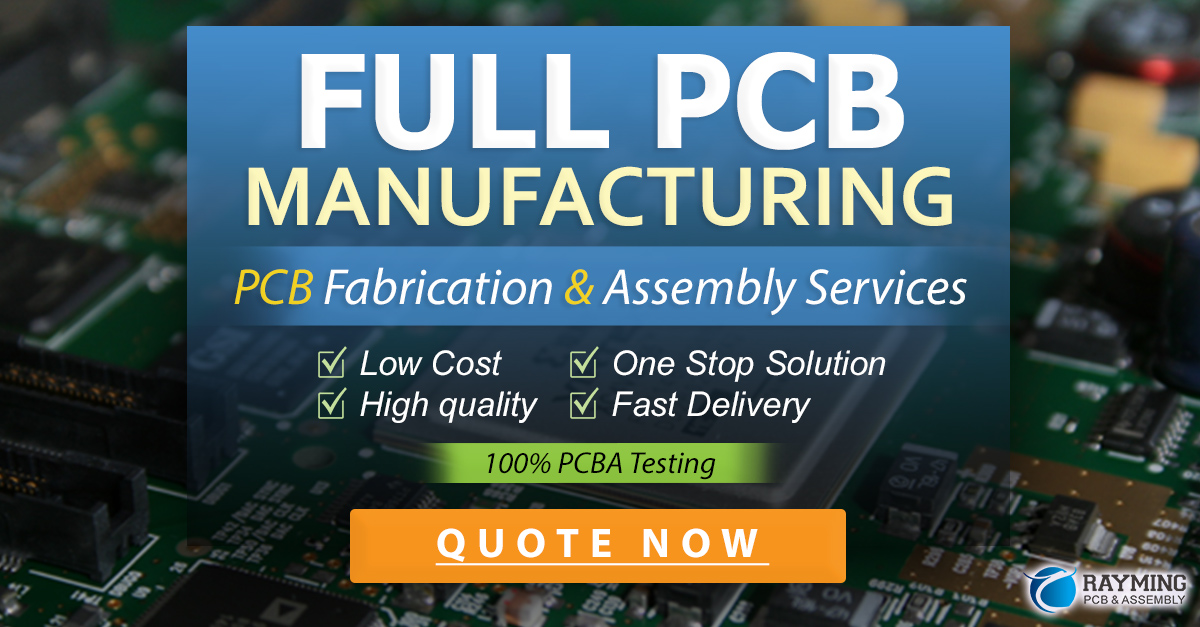
IATF 16949 Certification
IATF 16949 (International Automotive Task Force) is the international standard for automotive quality management systems, based on ISO 9001. It was developed by leading automotive manufacturers to promote continuous improvement in the automotive supply chain.
IATF 16949 certified PCB manufacturers have met additional requirements above ISO 9001, specific to the needs of the automotive industry, such as:
- Advanced product quality planning (APQP)
- Production part approval process (PPAP)
- Failure mode and effects analysis (FMEA)
- Measurement system analysis (MSA)
- Statistical process control (SPC)
If you are manufacturing PCBs for automotive applications, choosing an IATF 16949 certified supplier is crucial to ensure your boards meet the strict quality and reliability requirements of the industry.
AS9100 Certification
AS9100 is the international quality management standard for the aerospace industry, based on ISO 9001. It includes additional requirements for aerospace suppliers, such as:
- Configuration management
- Design verification and validation
- Counterfeit parts prevention
- FOD (foreign object debris/damage) prevention
- Awareness of product safety and ethical behavior
AS9100 certified PCB manufacturers have demonstrated their ability to meet the stringent requirements of aerospace customers. If you are manufacturing PCBs for aerospace applications, AS9100 certification should be a requirement for your supplier.
NADCAP Certification
NADCAP (National Aerospace and Defense Contractors Accreditation Program) is a global program that accredits special processes and products for the aerospace and defense industries. PCB manufacturers can achieve NADCAP accreditation for processes such as:
- Soldering
- Conformal coating
- Plating
- Bare board testing
NADCAP accreditation involves rigorous audits to ensure conformance to customer requirements and industry standards. Choosing a NADCAP accredited PCB manufacturer provides additional confidence in their special process capabilities for high-reliability applications.
ISO 13485 Certification
ISO 13485 is the international standard for quality management systems for medical device manufacturers. It is based on ISO 9001 with additional requirements specific to the medical device industry, such as:
- Risk management
- Traceability
- Sterile product handling
- Regulatory compliance
If you are manufacturing PCBs for medical devices, your supplier should be ISO 13485 certified to ensure they meet the quality and regulatory requirements of the industry.
ITAR Registration
ITAR (International Traffic in Arms Regulations) is a set of US government regulations that control the export and import of defense-related articles and services. If you are manufacturing PCBs for military or defense applications, your supplier should be ITAR registered.
ITAR registered PCB manufacturers have implemented controls to ensure compliance with ITAR regulations, such as:
- Access controls for ITAR-controlled data and products
- Training for employees on ITAR requirements
- Record keeping and reporting
Choosing an ITAR registered supplier ensures your PCB design data and products are handled properly and not exposed to unauthorized foreign nationals.
FAQ
What is the most important PCB certification?
The most important PCB certification depends on your specific industry and application. In general, ISO 9001 is considered a baseline certification for quality management. For automotive, IATF 16949 is essential. For aerospace, AS9100 and NADCAP are key. For medical devices, ISO 13485 is crucial.
Can a PCB manufacturer be certified to multiple standards?
Yes, many PCB manufacturers hold multiple certifications to serve different industries and customer requirements. It is common to see manufacturers certified to ISO 9001, IATF 16949, AS9100, ISO 13485, and ITAR registered.
How do I verify a PCB manufacturer’s certifications?
Most PCB manufacturers will list their certifications on their website. You can also request copies of their certificates which should be issued by accredited certification bodies. Many certification bodies also have online directories where you can search for certified companies.
Do PCB Certifications guarantee quality?
While PCB certifications demonstrate a manufacturer’s adherence to industry standards and best practices, they do not necessarily guarantee quality. Certifications should be considered one factor in your supplier selection process, along with capabilities, experience, references, and other assessments.
How often do PCB manufacturers need to renew their certifications?
Most PCB certifications are valid for three years, after which the manufacturer must undergo a recertification audit. However, surveillance audits are typically conducted annually to ensure ongoing compliance. NADCAP accreditation is renewed every year.
In conclusion, PCB certifications are an important factor to consider when choosing a manufacturing partner. They provide assurance that the manufacturer has the processes and controls in place to consistently produce high-quality, reliable PCBs that meet industry standards. By understanding the key PCB certifications and what they mean, you can make an informed decision on the right partner for your specific needs.
Leave a Reply