Why is PCB Incoming Inspection Important?
PCB incoming inspection is a vital step in the electronics manufacturing process for several reasons:
-
Identifying defects early: By inspecting PCBs upon arrival, manufacturers can identify any defects or issues before the boards are used in the assembly process. This early detection helps prevent potential problems down the line, saving time and money.
-
Ensuring supplier quality: Incoming inspection allows manufacturers to monitor and evaluate the quality of their PCB Suppliers. By tracking defects and issues, manufacturers can provide feedback to suppliers and work with them to improve their processes and maintain high-quality standards.
-
Meeting customer requirements: Many customers have specific quality requirements for the PCBs used in their products. By conducting thorough incoming inspections, manufacturers can ensure that the PCBs they receive meet these requirements, thus maintaining customer satisfaction and trust.
-
Compliance with industry standards: PCB incoming inspection helps manufacturers comply with various industry standards and regulations, such as IPC-A-610, which provides guidelines for PCB Quality and acceptability.
The PCB Incoming Inspection Process
The PCB incoming inspection process typically involves several steps, each designed to assess different aspects of the PCBs’ quality. These steps may vary slightly depending on the manufacturer and the specific requirements of the project, but they generally include the following:
1. Visual Inspection
The first step in the incoming inspection process is a visual examination of the PCBs. This inspection is carried out using various tools, such as magnifying lenses, microscopes, or automated optical inspection (AOI) systems. The purpose of the visual inspection is to identify any obvious defects or issues, such as:
- Scratches, dents, or cracks on the PCB surface
- Discoloration or inconsistencies in the solder mask or silkscreen
- Incorrect or missing components
- Improper alignment or orientation of components
- Solder bridging or insufficient solder coverage
2. Dimensional Inspection
After the visual inspection, the PCBs undergo a dimensional inspection to ensure that they meet the specified measurements and tolerances. This inspection is typically performed using precision measuring tools, such as calipers, micrometers, or coordinate measuring machines (CMMs). The dimensional inspection checks for:
- Board thickness
- Hole sizes and locations
- Trace widths and spacing
- Copper thickness
- Overall board dimensions
3. Electrical Testing
Electrical testing is a crucial part of the incoming inspection process, as it verifies that the PCBs function as intended. There are several types of electrical tests that may be performed, depending on the complexity of the PCB and the specific requirements of the project. Some common electrical tests include:
- Continuity testing: This test checks for any open circuits or broken connections on the PCB.
- Insulation resistance testing: This test measures the resistance between isolated conductors on the PCB to ensure proper insulation.
- High-potential (HiPot) testing: This test applies a high voltage between conductors to check for any leakage or breakdown in the insulation.
- Impedance testing: This test measures the impedance of the PCB traces to ensure they meet the required specifications for signal integrity.
- Functional testing: This test involves powering up the PCB and verifying that it performs its intended functions correctly.
4. X-Ray Inspection
For complex PCBs with high-density interconnects or hidden features, X-ray inspection may be necessary. X-ray inspection allows manufacturers to see through the layers of the PCB and examine the internal structure for any defects or anomalies. This type of inspection is particularly useful for detecting issues such as:
- Voids or inconsistencies in the solder joints
- Misaligned or shifted components
- Broken or damaged traces within the PCB layers
- Foreign object debris (FOD) trapped within the PCB
5. Solderability Testing
Solderability testing is performed to ensure that the PCB’s surface finish and pads are suitable for the soldering process. This test typically involves applying a small amount of solder to a sample of pads on the PCB and examining the results under a microscope. The solderability test assesses:
- Wetting: The ability of the molten solder to flow and adhere to the pad surface
- Spread: The extent to which the solder spreads out over the pad
- Consistency: The uniformity of the solder coverage across multiple pads
6. Documentation and Reporting
Throughout the incoming inspection process, it is essential to maintain accurate documentation and reporting. This documentation serves several purposes:
- Tracking defects and issues: By recording the types and frequencies of defects found during inspection, manufacturers can identify trends and work with suppliers to address recurring problems.
- Providing evidence of compliance: Detailed inspection reports serve as evidence that the manufacturer has carried out the necessary quality control procedures and that the PCBs meet the required standards and specifications.
- Facilitating communication: Inspection reports can be shared with suppliers, customers, and internal teams to ensure that all stakeholders are aware of the PCB quality and any issues that need to be addressed.
Tools and Equipment Used in PCB Incoming Inspection
To carry out the various steps of the incoming inspection process, manufacturers rely on a range of tools and equipment. Some of the most common tools and equipment used in PCB incoming inspection include:
Tool/Equipment | Purpose |
---|---|
Magnifying lenses and microscopes | Visual inspection of PCBs for defects and anomalies |
Automated optical inspection (AOI) systems | High-speed, automated visual inspection of PCBs |
Calipers, micrometers, and coordinate measuring machines (CMMs) | Dimensional inspection of PCBs |
Continuity testers and multimeters | Electrical testing for open circuits and continuity |
Insulation resistance testers | Measuring the resistance between isolated conductors |
High-potential (HiPot) testers | Applying high voltage to check for insulation breakdown |
Impedance analyzers | Measuring the impedance of PCB traces |
X-ray inspection systems | Examining internal PCB structure for defects and anomalies |
Solderability test equipment | Assessing the solderability of PCB Surface Finishes and pads |
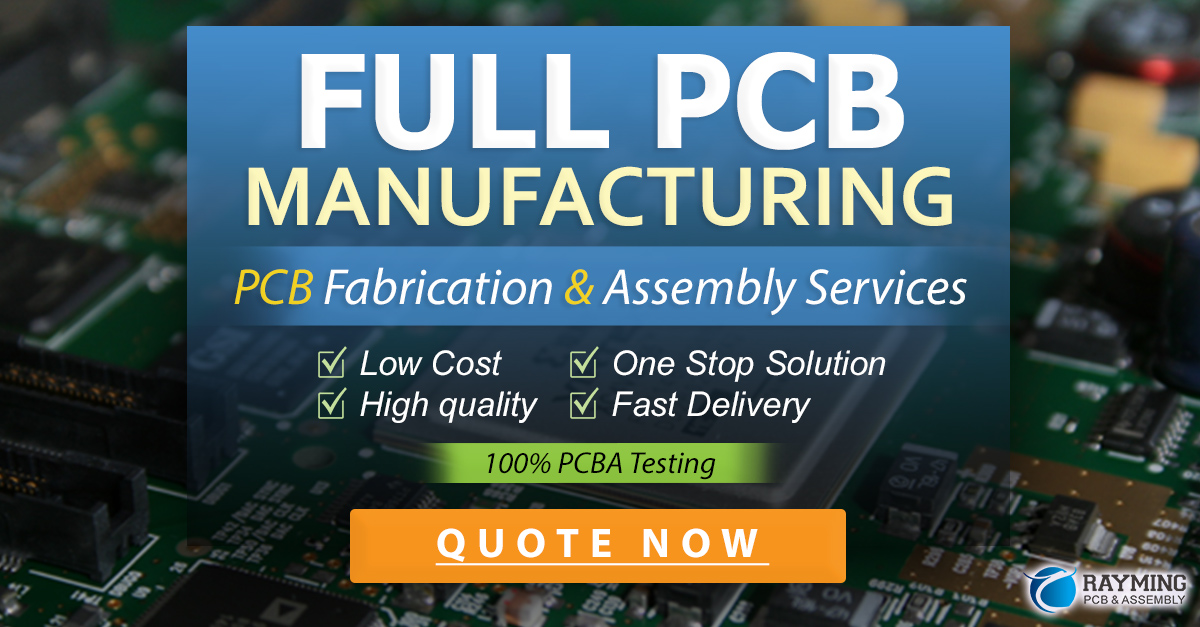
Sampling Plans and Acceptance Criteria
Given the high volume of PCBs that many manufacturers receive, it is often impractical to inspect every single board. Instead, manufacturers typically employ sampling plans to select a representative subset of PCBs for inspection. The sampling plan and acceptance criteria are based on factors such as:
- The criticality of the PCBs and their end-use application
- The historical quality performance of the supplier
- The lot size and production volume
- The specific requirements of the customer or industry standards
There are several common sampling plans used in PCB incoming inspection, such as:
- AQL (Acceptable Quality Level): This plan defines the maximum percentage of defective PCBs that can be considered acceptable in a lot. The sample size and acceptance criteria are determined based on the AQL and the lot size.
- c=0 Sampling Plan: This plan requires that no defective PCBs be found in the sample for the lot to be accepted. If any defects are found, the entire lot is rejected.
- Reduced Inspection: For suppliers with a history of consistently high quality, a reduced inspection plan may be used, where a smaller sample size is inspected, or certain inspection steps are skipped.
When defects are found during incoming inspection, the manufacturer must decide whether to accept or reject the lot based on the predetermined acceptance criteria. In some cases, the manufacturer may work with the supplier to rework or replace the defective PCBs, depending on the nature and severity of the defects.
Challenges and Best Practices in PCB Incoming Inspection
While PCB incoming inspection is a critical process for ensuring quality, it also presents several challenges that manufacturers must navigate:
-
Time and resource constraints: Incoming inspection can be time-consuming and resource-intensive, particularly for high-volume production runs. Manufacturers must balance the need for thorough inspection with the pressure to maintain production schedules and minimize costs.
-
Evolving technology and standards: As PCB technology advances and new standards emerge, manufacturers must continually adapt their incoming inspection processes and tools to keep pace with these changes.
-
Supplier management: Working with multiple PCB suppliers can make it challenging to maintain consistent quality standards and inspection procedures. Manufacturers must establish clear communication channels and expectations with their suppliers to ensure that all parties are aligned on quality requirements.
To overcome these challenges and optimize the incoming inspection process, manufacturers can follow several best practices:
-
Implement a risk-based approach: By prioritizing inspection efforts based on the criticality of the PCBs and the historical performance of the suppliers, manufacturers can allocate their resources more efficiently and effectively.
-
Invest in automation: Automated inspection tools, such as AOI systems and X-ray inspection equipment, can significantly increase the speed and accuracy of the inspection process, reducing the reliance on manual labor.
-
Foster supplier partnerships: Building strong, collaborative relationships with PCB suppliers can help manufacturers address quality issues proactively and work together to implement process improvements.
-
Continuously monitor and improve: Regularly reviewing inspection data and metrics can help manufacturers identify trends and opportunities for improvement in their incoming inspection process and supplier quality management.
FAQ
-
What is the purpose of PCB incoming inspection?
The purpose of PCB incoming inspection is to verify that the PCBs received from suppliers meet the required quality standards and specifications before they are used in the production process. This helps identify defects early, ensure supplier quality, meet customer requirements, and comply with industry standards. -
What are the main steps in the PCB incoming inspection process?
The main steps in the PCB incoming inspection process include visual inspection, dimensional inspection, electrical testing, X-ray inspection (for complex PCBs), solderability testing, and documentation and reporting. -
What tools and equipment are used in PCB incoming inspection?
Common tools and equipment used in PCB incoming inspection include magnifying lenses and microscopes, automated optical inspection (AOI) systems, calipers, micrometers, coordinate measuring machines (CMMs), continuity testers, insulation resistance testers, high-potential (HiPot) testers, impedance analyzers, X-ray inspection systems, and solderability test equipment. -
What is a sampling plan in PCB incoming inspection?
A sampling plan in PCB incoming inspection is a method for selecting a representative subset of PCBs from a lot for inspection, rather than inspecting every single board. Common sampling plans include AQL (Acceptable Quality Level), c=0 Sampling Plan, and Reduced Inspection. -
What are some best practices for optimizing the PCB incoming inspection process?
Some best practices for optimizing the PCB incoming inspection process include implementing a risk-based approach, investing in automation, fostering supplier partnerships, and continuously monitoring and improving the process based on inspection data and metrics.
In conclusion, the PCB incoming inspection process is a critical step in ensuring the quality and reliability of PCBs used in electronics manufacturing. By employing a thorough and well-defined inspection process, manufacturers can identify defects early, maintain supplier quality, meet customer requirements, and comply with industry standards. As PCB technology continues to advance, manufacturers must remain vigilant in adapting their incoming inspection processes and tools to keep pace with these changes and maintain the highest levels of quality and performance.
Leave a Reply