Introduction to PCB Current Calculators
A PCB (printed circuit board) current calculator is an essential tool for electronics designers and engineers. It allows you to accurately determine the current carrying capacity of copper traces on a PCB based on varios parameters such as trace width, thickness, temperature rise, and more.
Using a PCB current calculator helps ensure your PCB traces are sized appropriately to handle the required current without excessive heating that could damage the board or components. Undersized traces can result in too much resistance and heat generation, while oversized traces waste board space.
In this comprehensive guide, we’ll cover everything you need to know about PCB current calculators, including:
- How PCB current calculators work
- Key parameters and inputs
- IPC-2152 standards for current carrying capacity
- Online vs. standalone calculator tools
- Limitations and additional considerations
- Frequently asked questions
Whether you’re a seasoned PCB designer or just starting out, a reliable PCB current calculator is a must-have in your toolkit. Let’s dive in and explore this topic in detail.
How PCB Current Calculators Work
A PCB current calculator works by taking various input parameters about your copper traces and board characteristics and using standardized formulas to determine the maximum current a trace can safely carry.
The primary standard used is IPC-2152, “Standard for Determining Current-Carrying Capacity in Printed Board Design.” This standard provides equations to calculate current limits based on a trace’s cross-sectional area, taking into account factors like ambient temperature, temperature rise, and board/trace properties.
Here are the key parameters used in IPC-2152 current calculations:
- Cross-sectional area of trace (width x thickness)
- Trace length
- Allowable temperature rise above ambient
- Ambient temperature
- Board thermal conductivity (how easily the PCB conducts heat)
- Trace thermal conductivity (for copper)
- Board thickness
The calculator plugs these inputs into the IPC-2152 formulas to determine the ampacity (current capacity) of the trace. The calculator may also consider additional factors such as copper thickness (weight), trace shape (rectangular vs. circular), and the presence of thermal reliefs or planes.
Some calculators use more advanced modeling, such as finite element analysis (FEA), to simulate heat flow and determine current limits. However, the IPC-2152 equations are generally accurate for most common 1-oz Copper PCBs.
Key Parameters for PCB Current Calculators
To use a PCB current calculator effectively, it’s important to understand the key input parameters and how they impact the current carrying capacity. Here’s a detailed look at each parameter:
Trace Width
Trace width is one of the most important factors in determining current capacity. Wider traces have more cross-sectional area and can carry more current with less resistance and heating.
Common trace widths for PCBs include:
Trace Width (mils) | Trace Width (mm) |
---|---|
5 | 0.127 |
10 | 0.254 |
15 | 0.381 |
20 | 0.508 |
25 | 0.635 |
30 | 0.762 |
40 | 1.016 |
50 | 1.27 |
Wider traces are typically used for power lines, while narrower traces are used for signals. A PCB current calculator will show you the current limit for a given trace width.
Trace Thickness
Trace thickness, also known as copper weight or height, refers to how thick the copper layer is on the PCB. Thicker copper can carry more current than thinner copper.
Standard copper weights and their thicknesses are:
Copper Weight (oz) | Thickness (mils) | Thickness (μm) |
---|---|---|
0.5 | 0.7 | 17.5 |
1 | 1.4 | 35 |
2 | 2.8 | 70 |
3 | 4.2 | 105 |
4 | 5.6 | 140 |
1-oz copper is most common, but 2-oz or higher may be used for high-current applications. The PCB current calculator will factor in trace thickness when determining ampacity.
Temperature Rise
Temperature rise refers to how much hotter the trace is allowed to get relative to the ambient temperature. A higher allowable temperature rise means the trace can carry more current, but it also means the components and PCB will get hotter.
IPC-2152 provides different temperature rise limits for external (component) layers vs. internal layers:
Layer Type | Temperature Rise Above Ambient |
---|---|
External | 10°C |
Internal | 20°C |
The current calculator will use these default temperature rise limits unless you specify a different value. Keep in mind that higher temperature rises may shorten the lifespan of components and the PCB.
Ambient Temperature
Ambient temperature is the air temperature around the PCB during operation. A higher ambient temperature reduces the current carrying capacity of traces, since there is less “headroom” before reaching the temperature rise limit.
Default ambient temperatures used in IPC-2152 calculations are:
Environment | Ambient Temperature |
---|---|
Handheld | 40°C |
Desktop | 25°C |
Industrial | 70°C |
Choose the appropriate ambient temperature for your application when using a PCB current calculator.
Board Thermal Conductivity
Board thermal conductivity measures how easily the PCB conducts heat away from the traces. A higher thermal conductivity allows traces to carry more current without overheating.
The thermal conductivity of a PCB depends on its material, typically FR-4 glass epoxy or metal core. IPC-2152 uses the following default values:
Board Material | Thermal Conductivity (W/mK) |
---|---|
FR-4 | 0.34 |
Metal Core | 2.2 |
Most PCB current calculators assume FR-4 material unless otherwise specified. Metal core PCBs can handle much higher currents than FR-4 due to their better thermal conductivity.
Other Factors
In addition to the key parameters above, PCB current calculators may consider other factors such as:
- Trace shape (rectangular, circular, etc.)
- Presence of thermal reliefs or planes
- Via size and number
- High voltage effects
- AC vs. DC current
Some of these factors are accounted for in the IPC-2152 equations, while others may require more advanced simulation. When in doubt, consult the documentation for your specific PCB current calculator.
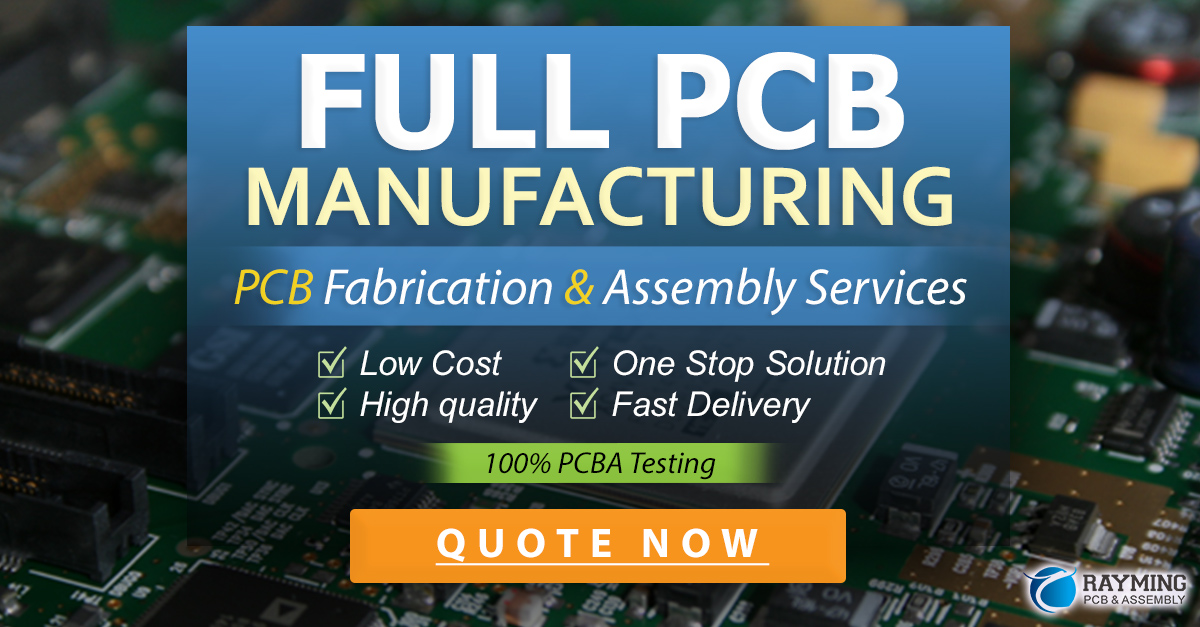
IPC-2152 Standards for Current Carrying Capacity
IPC-2152, “Standard for Determining Current-Carrying Capacity in Printed Board Design,” is the primary standard used by PCB current calculators. It provides a set of equations to determine the maximum current a trace can handle based on its cross-sectional area and other properties.
The main IPC-2152 equation for external (component) traces is:
I = k * ΔT^0.44 * A^0.725
Where:
- I = Current (amps)
- ΔT = Temperature rise above ambient (°C)
- A = Cross-sectional area (mils^2)
- k = Constant (0.048 for external traces)
For internal traces, the equation is similar but with a different constant (k = 0.024).
These equations assume a rectangular trace shape and FR-4 board material. IPC-2152 provides additional equations and modifiers for other trace shapes, board materials, and high voltage applications.
The standard also includes tables of precalculated current limits for common trace sizes and temperature rises. However, using a PCB current calculator is generally more convenient than looking up values in tables.
It’s important to note that IPC-2152 is a conservative standard and may result in slightly oversized traces compared to real-world conditions. However, it’s better to err on the side of caution when sizing traces to ensure reliability and longevity.
By using IPC-2152 equations and standards, PCB current calculators provide a reliable and industry-accepted method for determining trace current capacity.
Online vs. Standalone PCB Current Calculators
PCB current calculators come in two main varieties: online calculators and standalone software tools.
Online Calculators
Online PCB current calculators are web-based tools that allow you to quickly calculate trace current capacity without installing any software. They typically have a simple user interface where you enter the key parameters (trace width, thickness, temperature rise, etc.) and the calculator spits out the maximum current.
Advantages of online calculators include:
- No installation required
- Free to use
- Accessible from any device with a web browser
- Easy to use for quick calculations
However, online calculators may have some limitations:
- Require an internet connection
- May not support advanced features or input parameters
- Limited customization or integration with other tools
Some popular online PCB current calculators include:
- Saturn PCB Toolkit
- EEWeb PCB Trace Width Calculator
- Advanced Circuits Current Carrying Capacity Calculator
Standalone Calculators
Standalone PCB current calculators are software programs that you install on your computer. They offer more advanced features and customization than online calculators.
Advantages of standalone calculators include:
- More input parameters and advanced options
- Ability to save and load trace settings
- Integration with other PCB design tools
- Faster performance for complex simulations
Disadvantages of standalone calculators include:
- Require installation and updates
- May have a steeper learning curve
- Typically cost money for full featured versions
Some popular standalone PCB current calculators include:
- Altium PCB Editor (built-in)
- Saturn PCB Design Toolkit (standalone version)
- TraceSim PCB Trace Simulator
Ultimately, the choice between an online or standalone calculator depends on your specific needs and budget. For occasional quick calculations, an online tool may suffice. But for more complex designs and analysis, a standalone calculator is often the better choice.
Limitations and Additional Considerations
While PCB current calculators are valuable tools, they do have some limitations and additional factors to consider.
Limitations
PCB current calculators based on IPC-2152 make some assumptions and simplifications that may not reflect real-world conditions exactly. Some limitations to keep in mind include:
- Calculations assume steady-state conditions, not transient currents
- Equations are based on empirical data and curve fitting, not exact physics
- Factors like trace proximity, layer stackup, and thermal coupling are not fully accounted for
- Copper thickness and resistivity may vary from nominal values
- Calculators don’t account for external cooling (airflow, heatsinks, etc.)
For these reasons, it’s a good idea to use conservative values and include a margin of safety when sizing traces. PCB current calculators should be used as a starting point, not an absolute guarantee.
Additional Considerations
In addition to the basic trace parameters, there are other factors that can affect current carrying capacity and overall PCB performance. Some additional considerations include:
- Via size and number: Vias can act as heat sinks and increase current capacity, but they also add resistance and potential failure points.
- Thermal reliefs: Adding thermal reliefs (spokes) around via pads can help dissipate heat and increase current capacity.
- Copper pours: Using copper fills or pours can help spread heat and increase current capacity, but they also add capacitance.
- High voltage: At high voltages (>500V), additional spacing and insulation requirements may affect trace sizing.
- AC current: AC currents can cause additional heating due to skin effect and proximity effect, which may require larger traces than DC.
- Extreme environments: Harsh conditions like high humidity, vibration, or corrosive atmospheres may degrade PCB performance over time.
Designers should carefully consider these factors and consult additional resources, such as IPC standards, component datasheets, and test data, to ensure reliable PCB performance.
Conclusion
PCB current calculators are essential tools for sizing traces to ensure reliable and efficient current carrying capacity. By using industry-standard equations and input parameters, these calculators help designers create PCBs that can handle the required current without overheating or wasting space.
When using a PCB current calculator, it’s important to understand the key parameters, such as trace width, thickness, temperature rise, and board properties. Choosing appropriate input values and including a margin of safety can help compensate for real-world variations and uncertainties.
While PCB current calculators have some limitations, they are still valuable tools for quickly estimating trace sizes and optimizing designs. By using these calculators in conjunction with other design techniques and standards, PCB designers can create reliable, high-performance boards that meet the needs of their applications.
Frequently Asked Questions (FAQ)
What is a PCB current calculator?
A PCB current calculator is a tool that determines the maximum current a PCB trace can carry based on its size, temperature rise, and other properties. It uses standardized equations to ensure traces are sized appropriately to handle the required current without overheating.
What parameters do I need to use a PCB current calculator?
The key parameters for a PCB current calculator include:
– Trace width
– Trace thickness (copper weight)
– Allowable temperature rise
– Ambient temperature
– Board material and thermal conductivity
Additional parameters may include trace length, shape, and the presence of vias or planes.
What is the IPC-2152 standard?
IPC-2152 is the standard for determining current carrying capacity in PCB design. It provides equations and guidelines for sizing traces based on their cross-sectional area, temperature rise, and other factors. Most PCB current calculators use IPC-2152 equations.
What’s the difference between online and standalone PCB current calculators?
Online PCB current calculators are web-based tools that are quick and easy to use, but may have limited features. Standalone calculators are installed software programs that offer more advanced capabilities and customization, but require installation and may have a learning curve.
How accurate are PCB current calculators?
PCB current calculators based on IPC-2152 are generally accurate for most common PCB designs. However, they make some simplifying assumptions and may not account for all real-world factors. It’s a good idea to use conservative values and include a safety margin when sizing traces.
Leave a Reply