Understanding PCB Current Carrying Capacity
What is Current Carrying Capacity?
Current carrying capacity, also known as ampacity, is the maximum amount of electric current that a conductor can safely carry without causing damage or excessive heating. In the context of PCBs, the current carrying capacity refers to the maximum current that a trace can handle without compromising the board’s integrity or performance.
Factors Affecting Current Carrying Capacity
Several factors influence the current carrying capacity of a PCB trace:
-
Trace Width: Wider traces can carry more current than narrower ones, as they have a larger cross-sectional area for the current to flow through.
-
Trace Thickness: Thicker traces can carry more current than thinner ones, as they have a greater volume of conductive material.
-
Ambient Temperature: Higher ambient temperatures reduce the current carrying capacity of a trace, as the trace’s ability to dissipate heat decreases.
-
Trace Length: Longer traces have a higher resistance, which can lead to increased voltage drop and heat generation, thus reducing the current carrying capacity.
-
Copper Weight: The amount of copper used in the PCB, typically measured in ounces per square foot (oz/ft²), affects the current carrying capacity. Higher copper weights allow for greater current carrying capacity.
How Does a PCB Current Calculator Work?
A PCB current calculator uses a set of mathematical equations and empirical data to determine the appropriate trace width for a given current, considering the factors mentioned above. The calculator takes into account the following parameters:
- Current (in amperes)
- Trace thickness (in ounces)
- Temperature rise above ambient (in °C)
- Trace length (in inches or millimeters)
- Copper weight (in oz/ft²)
The calculator then applies the IPC-2221 standard, which provides guidelines for determining the current carrying capacity of PCB traces. The IPC-2221 standard is based on extensive research and testing, and it offers a reliable method for calculating trace widths.
Using a PCB Current Calculator
Step 1: Determine the Required Current
The first step in using a PCB current calculator is to determine the maximum current that the trace will need to carry. This information can be obtained from the specifications of the components connected to the trace or by analyzing the circuit’s power requirements.
Step 2: Select the Appropriate Parameters
Next, input the necessary parameters into the PCB current calculator. These include:
- Current (in amperes)
- Trace thickness (in ounces)
- Temperature rise above ambient (in °C)
- Trace length (in inches or millimeters)
- Copper weight (in oz/ft²)
The temperature rise above ambient is typically set to 10°C for most applications, but it can be adjusted based on the specific requirements of the design.
Step 3: Calculate the Trace Width
Once all the parameters have been entered, the PCB current calculator will provide the minimum trace width required to safely carry the specified current. The result will be given in either mils (thousandths of an inch) or millimeters, depending on the calculator’s settings.
Step 4: Verify and Optimize
After obtaining the minimum trace width, it is essential to verify that the calculated value is appropriate for the design. Consider factors such as the available space on the PCB, the proximity of other traces, and the manufacturing capabilities of the PCB fabricator.
If the calculated trace width is too large for the available space or if it exceeds the manufacturer’s capabilities, consider the following options:
- Increase the copper weight of the PCB
- Use multiple traces in parallel to distribute the current
- Reduce the current by using more efficient components or optimizing the circuit design
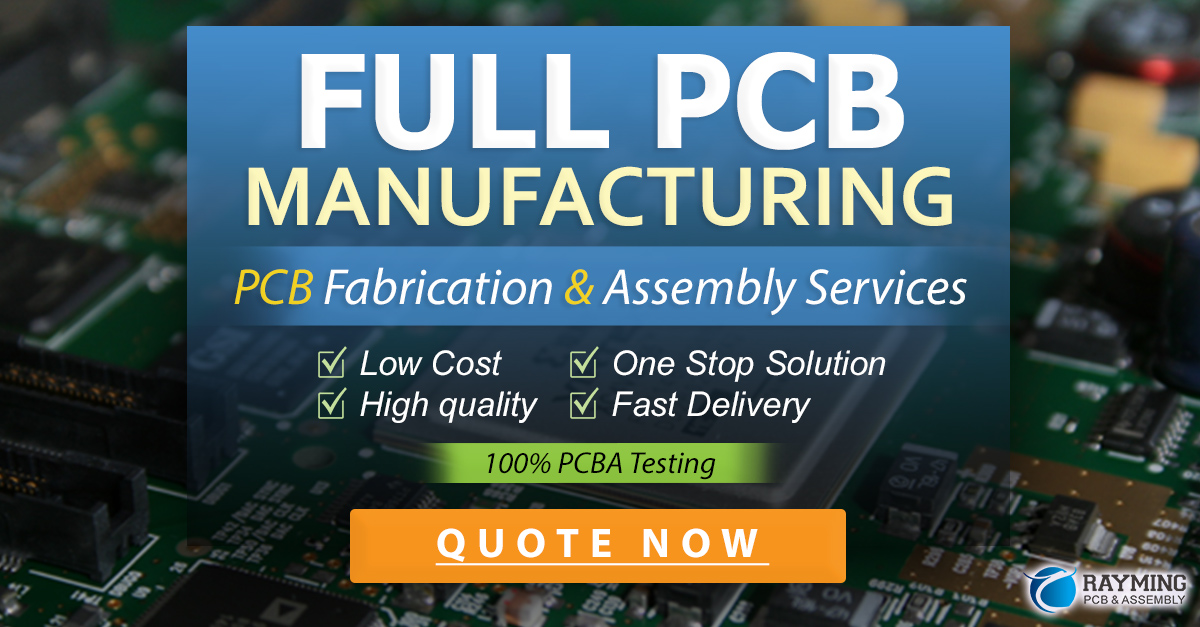
PCB Current Calculator Examples
To better understand how a PCB current calculator works, let’s look at a few examples.
Example 1: Single Trace
Suppose we have a trace that needs to carry a current of 2A, and we want to determine the minimum trace width required. The PCB has a copper weight of 1 oz/ft², and the trace length is 5 inches. We’ll assume a temperature rise of 10°C above ambient and a trace thickness of 1 oz.
Using a PCB current calculator with these parameters, we find that the minimum trace width required is approximately 50 mils (1.27 mm).
Example 2: Multiple Traces
Now, let’s consider a scenario where we have three traces in parallel, each carrying a current of 1.5A. The PCB has a copper weight of 2 oz/ft², and the trace length is 3 inches. We’ll assume a temperature rise of 10°C above ambient and a trace thickness of 2 oz.
Using a PCB current calculator, we find that each trace should have a minimum width of approximately 20 mils (0.508 mm). By using multiple traces in parallel, we can reduce the required trace width compared to using a single trace carrying the total current.
PCB Current Calculator Table
The following table provides a quick reference for minimum trace widths based on current, copper weight, and trace length. The values assume a temperature rise of 10°C above ambient and a trace thickness of 1 oz.
Current (A) | Copper Weight (oz/ft²) | Trace Length (in) | Minimum Trace Width (mils) |
---|---|---|---|
1 | 1 | 5 | 25 |
2 | 1 | 5 | 50 |
3 | 1 | 5 | 75 |
1 | 2 | 5 | 20 |
2 | 2 | 5 | 40 |
3 | 2 | 5 | 60 |
Please note that these values are for reference only and should be verified using a PCB current calculator for your specific design requirements.
Frequently Asked Questions (FAQ)
-
Q: What is the purpose of a PCB current calculator?
A: A PCB current calculator is used to determine the minimum trace width required to safely carry a specified current on a printed circuit board (PCB). It takes into account factors such as current, trace thickness, temperature rise, trace length, and copper weight to provide an accurate calculation based on the IPC-2221 standard. -
Q: Why is it important to use a PCB current calculator?
A: Using a PCB current calculator is crucial to ensure that the traces on a PCB are designed to handle the required current without causing damage or excessive heating. Underestimating the necessary trace width can lead to reliability issues, while overestimating it can result in wasted space and increased manufacturing costs. -
Q: What factors influence the current carrying capacity of a PCB trace?
A: The current carrying capacity of a PCB trace is influenced by several factors, including trace width, trace thickness, ambient temperature, trace length, and copper weight. Wider, thicker traces with higher copper weights and shorter lengths can carry more current than narrower, thinner traces with lower copper weights and longer lengths. -
Q: Can I use multiple traces in parallel to carry a higher current?
A: Yes, using multiple traces in parallel is a common technique to increase the current carrying capacity of a PCB. By distributing the current across multiple traces, the required trace width for each individual trace can be reduced compared to using a single trace carrying the total current. -
Q: How do I choose the appropriate temperature rise above ambient when using a PCB current calculator?
A: The temperature rise above ambient is typically set to 10°C for most applications, as this value provides a reasonable balance between current carrying capacity and PCB temperature. However, if your design has specific temperature requirements or operates in a high-temperature environment, you may need to adjust this value accordingly.
Conclusion
The PCB current calculator is an indispensable tool for electronics designers and engineers working on printed circuit boards. By understanding the factors that influence current carrying capacity and using a PCB current calculator to determine the appropriate trace widths, designers can create reliable and efficient PCBs that meet their specific requirements.
Remember to consider factors such as available space, manufacturing capabilities, and the option to use multiple traces in parallel when optimizing your PCB design. By following the guidelines provided by the IPC-2221 standard and verifying your calculations with a PCB current calculator, you can ensure that your PCBs are designed to handle the required currents safely and effectively.
Leave a Reply