Introduction to PCB Outer Layers
Printed Circuit Boards (PCBs) are essential components in modern electronics, providing a platform for mounting and interconnecting electronic components. A PCB consists of multiple layers, including the outer layers, which play a crucial role in the overall functionality and protection of the board. In this article, we will delve into the details of the outer layers of a PCB, exploring their composition, manufacturing process, and importance in the PCB Assembly.
What are the Outer Layers of a PCB?
The outer layers of a PCB, also known as the top and bottom layers, are the outermost layers of the board. These layers are typically composed of a copper foil laminated onto a substrate material, such as FR-4 (Flame Retardant 4), which is a glass-reinforced epoxy laminate. The copper foil on the outer layers is used for creating conductive traces, pads, and other features that allow for the connection of electronic components.
Functions of the Outer Layers
The outer layers of a PCB serve several critical functions:
-
Component Mounting: The outer layers provide a surface for mounting electronic components, such as resistors, capacitors, and integrated circuits (ICs). The copper pads on the outer layers are designed to match the footprint of the components, allowing for secure soldering and electrical connection.
-
Electrical Connectivity: The conductive traces on the outer layers enable electrical connectivity between components. These traces are carefully designed to ensure proper signal integrity and minimize interference.
-
Protection: The outer layers act as a protective barrier for the inner layers of the PCB. They shield the sensitive inner layers from environmental factors such as moisture, dust, and physical damage.
-
Aesthetics and Labeling: The outer layers can be used for applying silkscreen printing, which includes labels, logos, and other identifying information. This enhances the aesthetics of the PCB and aids in the assembly and troubleshooting process.
Manufacturing Process of Outer Layers
The manufacturing process of the outer layers involves several steps:
1. Copper Foil Lamination
The process begins with the lamination of a thin copper foil onto the substrate material. The copper foil is typically available in various thicknesses, ranging from 0.5 oz to 2 oz per square foot. The choice of copper thickness depends on the desired current carrying capacity and the manufacturing capabilities.
2. Photoresist Application
A photoresist, which is a light-sensitive material, is applied onto the copper foil. The photoresist can be either liquid or dry film, with dry film being more commonly used in the PCB industry due to its ease of handling and consistent thickness.
3. Exposure and Development
The PCB Artwork, which contains the design of the conductive traces and pads, is used to create a photomask. The photomask is placed on top of the photoresist, and the assembly is exposed to UV light. The areas of the photoresist that are exposed to UV light become soluble, while the unexposed areas remain intact.
After exposure, the PCB is developed using a chemical solution that removes the soluble photoresist, revealing the copper foil underneath.
4. Etching
The exposed copper foil is then etched away using a chemical etching process, typically involving an acidic solution such as ferric chloride or ammonium persulfate. The remaining photoresist protects the desired copper features during the etching process.
5. Photoresist Removal and Cleaning
After etching, the remaining photoresist is removed using a stripping solution, leaving behind the copper traces and pads on the outer layers. The PCB is then thoroughly cleaned to remove any residues.
6. Surface Finish Application
To protect the exposed copper and enhance solderability, a surface finish is applied to the outer layers. Common surface finishes include:
- Hot Air Solder Leveling (HASL): A thin layer of solder is applied to the copper surfaces using a hot air leveling process.
- Electroless Nickel Immersion Gold (ENIG): A layer of nickel is electrolessly plated onto the copper, followed by a thin layer of gold.
- Organic Solderability Preservative (OSP): An organic compound is applied to the copper surfaces to prevent oxidation and enhance solderability.
Design Considerations for Outer Layers
When designing the outer layers of a PCB, several factors must be considered:
1. Trace Width and Spacing
The width and spacing of the copper traces on the outer layers are critical for ensuring proper signal integrity and preventing short circuits. The trace width is determined by the current carrying requirements and the manufacturing capabilities, while the spacing between traces is governed by the PCB design rules and the voltage levels of the signals.
2. Pad Size and Shape
The pads on the outer layers must be designed to match the footprint of the components being used. The size and shape of the pads depend on the component package type and the soldering process employed. Proper pad design ensures reliable soldering and prevents issues such as tombstoning (when a component stands up on one end due to uneven heating) or insufficient solder joint strength.
3. Via Placement
Vias are conductive holes that allow for the connection of traces between layers. The placement of vias on the outer layers is crucial for maintaining signal integrity and preventing manufacturing issues. Vias should be placed strategically to minimize the length of the signal paths and avoid interference with other components or traces.
4. Copper Pour and Grounding
Copper pour, also known as a ground plane or power plane, is a large area of copper on the outer layers that is used for providing a low-impedance path for power distribution and grounding. Proper copper pour design helps to reduce electromagnetic interference (EMI) and improve signal integrity.
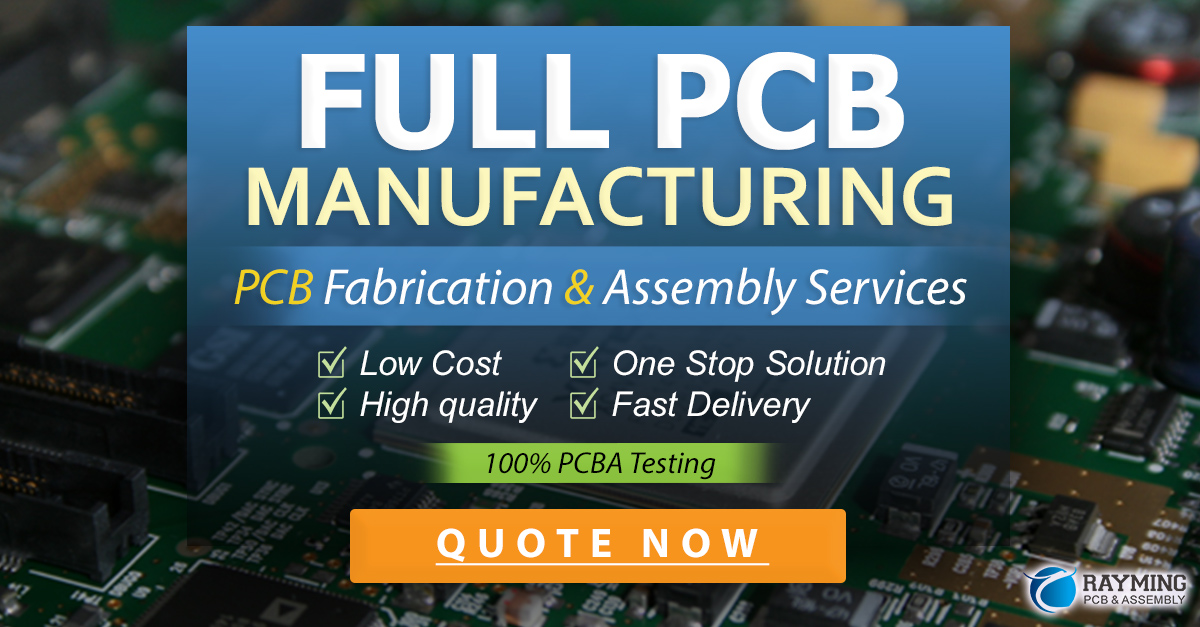
Importance of Outer Layers in PCB Assembly
The outer layers of a PCB play a vital role in the assembly process:
1. Component Placement
The accurate placement of components on the outer layers is essential for ensuring proper functionality and reliability of the PCB. The pads on the outer layers must align precisely with the component leads or pins to allow for successful soldering.
2. Soldering
The outer layers are where the soldering process takes place. The copper pads on the outer layers are coated with a solder paste, which contains tiny solder particles suspended in a flux matrix. During the reflow soldering process, the solder paste melts and forms a strong mechanical and electrical connection between the components and the pads.
3. Inspection and Testing
The outer layers are accessible for visual inspection and testing after the assembly process. Automated optical inspection (AOI) systems can check for proper component placement, Solder Joint Quality, and other visible defects on the outer layers. Electrical testing, such as in-circuit testing (ICT) or functional testing, can also be performed by accessing test points on the outer layers.
Challenges in Outer Layer Manufacturing
The manufacturing of outer layers presents several challenges:
1. Copper Thickness Variation
Variations in the copper thickness across the outer layers can lead to inconsistencies in the etching process, resulting in over-etching or under-etching of features. Proper process control and monitoring are necessary to maintain consistent copper thickness.
2. Photoresist Adhesion
Poor adhesion of the photoresist to the copper foil can cause issues during the exposure and development stages, leading to defects in the final etched pattern. Proper surface preparation and storage conditions are essential for ensuring good photoresist adhesion.
3. Etching Uniformity
Achieving uniform etching across the entire panel can be challenging, particularly for high-density designs with fine features. Factors such as etchant concentration, temperature, and agitation must be carefully controlled to ensure consistent etching results.
4. Surface Finish Quality
The quality of the surface finish on the outer layers is critical for ensuring good solderability and preventing oxidation. Inconsistencies in the surface finish can lead to soldering defects or reduced shelf life of the PCBs. Proper process control and regular maintenance of the surface finish equipment are necessary to maintain high-quality finishes.
Frequently Asked Questions (FAQ)
1. What is the difference between the outer layers and inner layers of a PCB?
The outer layers of a PCB are the top and bottom layers that are visible and accessible for component mounting and soldering. The inner layers are the layers sandwiched between the outer layers and are used for additional routing and power distribution. The inner layers are not accessible for component mounting or direct soldering.
2. Can the outer layers of a PCB have different copper thicknesses?
Yes, the outer layers of a PCB can have different copper thicknesses depending on the design requirements. For example, the top layer may have a thicker copper foil to accommodate higher current carrying traces, while the bottom layer may have a thinner copper foil for more precise etching of fine-pitch features.
3. What is the purpose of applying a surface finish to the outer layers?
The purpose of applying a surface finish to the outer layers is to protect the exposed copper from oxidation and enhance solderability. The surface finish acts as a barrier between the copper and the environment, preventing the formation of oxide layers that can hinder soldering. Additionally, some surface finishes, such as ENIG or OSP, provide a better surface for solder wetting and joint formation.
4. How do vias connect the outer layers to the inner layers?
Vias are conductive holes drilled through the PCB that allow for the connection of traces between layers. The walls of the vias are plated with copper to create a conductive path. When a via is used to connect an outer layer to an inner layer, it is called a blind via (when it starts from an outer layer and ends at an inner layer) or a buried via (when it connects two or more inner layers without reaching the outer layers).
5. Can the outer layers of a PCB have different Solder Mask Colors?
Yes, the outer layers of a PCB can have different solder mask colors. The solder mask is a protective coating applied over the copper traces and pads, leaving only the areas intended for soldering exposed. While green is the most common solder mask color, other colors such as red, blue, black, or white can be used for aesthetic or functional purposes, such as improving contrast for vision systems or indicating different assembly variants.
Conclusion
The outer layers of a PCB are critical components that serve multiple functions, including providing a surface for component mounting, enabling electrical connectivity, offering protection, and enhancing aesthetics. The manufacturing process of outer layers involves several steps, from copper foil lamination to surface finish application, each contributing to the final quality and functionality of the PCB.
When designing the outer layers, factors such as trace width and spacing, pad size and shape, via placement, and copper pour must be carefully considered to ensure optimal performance and manufacturability. The outer layers also play a crucial role in the PCB assembly process, facilitating component placement, soldering, and inspection.
Understanding the importance and challenges associated with the outer layers of a PCB is essential for designers, manufacturers, and assembly personnel to ensure the production of high-quality, reliable electronic products.
Layer | Function | Manufacturing Steps |
---|---|---|
Top Layer | Component mounting, routing, protection | Copper lamination, photoresist, etching, finish |
Bottom Layer | Component mounting, routing, protection | Copper lamination, photoresist, etching, finish |
Inner Layers | Additional routing, power and ground planes | Copper lamination, photoresist, etching |
Solder Mask | Insulation, protection, defining soldering areas | Photoimageable coating, exposure, development |
Silkscreen | Labeling, orientation, and identification | Screen printing or direct legend printing |
By mastering the intricacies of the outer layers and their role in the overall PCB structure, manufacturers can optimize their processes, minimize defects, and deliver high-quality PCBs that meet the ever-increasing demands of modern electronics.
Leave a Reply