Understanding PCB shelf life and Its Importance
PCB (Printed Circuit Board) shelf life is a critical factor to consider when manufacturing and storing electronic components. It refers to the maximum period a PCB can be stored before its quality and functionality start to deteriorate. Understanding PCB shelf life is crucial for ensuring the reliability and longevity of electronic devices.
Factors Affecting PCB Shelf Life
Several factors can impact the shelf life of a PCB, including:
-
Storage Conditions: Temperature, humidity, and exposure to light can all affect PCB shelf life. Ideally, PCBs should be stored in a cool, dry, and dark environment.
-
Material Composition: The materials used in PCB manufacturing, such as the substrate, copper, and solder mask, can influence shelf life. Higher quality materials generally have longer shelf lives.
-
Manufacturing Process: The quality of the manufacturing process, including the cleanliness of the environment and the precision of the equipment, can impact PCB shelf life.
The Importance of Proper PCB Storage
Proper storage of PCBs is essential to maintain their quality and functionality over time. Improper storage can lead to various issues, such as:
-
Oxidation: Exposure to air and moisture can cause the copper traces on a PCB to oxidize, leading to reduced conductivity and potential failures.
-
Delamination: Temperature fluctuations and humidity can cause the layers of a PCB to separate, resulting in delamination and potential short circuits.
-
Solderability Issues: Over time, the solderability of PCB pads and components can degrade, making it difficult to achieve reliable solder joints during assembly.
PCB Shelf Life for Double Side PCBs After First Reflow
Double side PCBs, also known as double-sided or two-layer PCBs, have components and circuitry on both sides of the board. These PCBs undergo a reflow process, where the components are soldered to the board using a controlled heating profile.
First Reflow and Its Impact on Shelf Life
The first reflow process is critical in determining the shelf life of a double side PCB. During this process, the solder paste is melted and forms a permanent bond between the components and the PCB pads. After the first reflow, the PCB is considered to be in its “assembled” state.
The maximum shelf life for a double side PCB after the first reflow depends on several factors, including:
-
Solder Mask Quality: The quality of the solder mask, which protects the copper traces and pads, can impact the shelf life of the PCB. A high-quality solder mask can help prevent oxidation and maintain solderability.
-
Solder Paste Composition: The type and quality of the solder paste used during the first reflow can affect the shelf life of the PCB. Some solder pastes have better long-term stability than others.
-
Storage Conditions: As mentioned earlier, proper storage conditions are crucial for maintaining PCB shelf life. Double side PCBs should be stored in moisture barrier bags with desiccants to control humidity.
Typical Shelf Life for Double Side PCBs After First Reflow
The typical shelf life for a double side PCB after the first reflow can vary depending on the specific manufacturing process and materials used. However, a general guideline is as follows:
Storage Condition | Shelf Life |
---|---|
Moisture Barrier Bag with Desiccant | 12-24 months |
Moisture Barrier Bag without Desiccant | 6-12 months |
No Moisture Barrier Bag | 1-3 months |
It’s important to note that these are just guidelines, and actual shelf life may vary. It’s always best to consult with the PCB manufacturer for specific recommendations based on their processes and materials.
Best Practices for Maximizing PCB Shelf Life
To ensure the longest possible shelf life for double side PCBs after the first reflow, consider the following best practices:
-
Use High-Quality Materials: Choose high-quality PCB substrates, copper, solder mask, and solder paste to ensure the best possible shelf life.
-
Control Storage Conditions: Store PCBs in a cool, dry, and dark environment with controlled humidity. Use moisture barrier bags with desiccants for optimal protection.
-
Follow Manufacturer Guidelines: Adhere to the PCB manufacturer’s guidelines for storage and handling to ensure the best possible shelf life.
-
Implement First-In, First-Out (FIFO) Inventory Management: Use a FIFO inventory management system to ensure that the oldest PCBs are used first, minimizing the risk of quality degradation due to extended storage.
-
Regularly Inspect and Test: Periodically inspect stored PCBs for signs of degradation, such as oxidation or delamination. Perform solderability tests to ensure that the PCBs are still suitable for assembly.
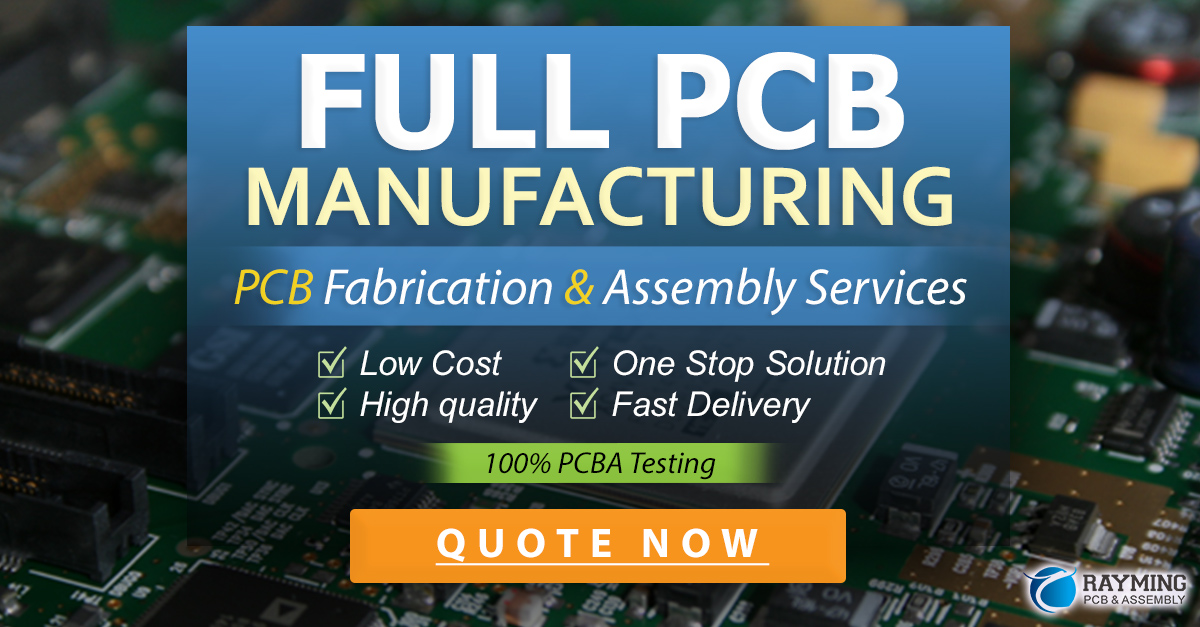
Frequently Asked Questions (FAQ)
-
What happens if a PCB exceeds its shelf life?
If a PCB exceeds its shelf life, it may experience quality and functionality issues, such as reduced solderability, oxidation, or delamination. This can lead to difficulties during assembly and potential failures in the final product. -
Can PCBs be reworked after exceeding their shelf life?
In some cases, PCBs that have exceeded their shelf life can be reworked to improve solderability and functionality. This may involve cleaning the PCB, applying fresh solder paste, and performing a new reflow process. However, the success of rework depends on the extent of the degradation and is not always guaranteed. -
How can I tell if a PCB has exceeded its shelf life?
Visual inspection can often reveal signs of PCB degradation, such as oxidation (darkening of the copper traces) or delamination (separation of the PCB layers). Solderability tests can also be performed to assess the quality of the solder pads and components. -
Can I extend the shelf life of a PCB?
Proper storage conditions, such as using moisture barrier bags with desiccants and controlling temperature and humidity, can help extend the shelf life of a PCB. However, it’s important to note that shelf life cannot be extended indefinitely, and PCBs should be used within the recommended timeframe. -
What should I do with PCBs that have exceeded their shelf life?
PCBs that have exceeded their shelf life and cannot be reworked should be properly disposed of in accordance with local regulations. It’s important not to use these PCBs in production, as they may lead to quality and reliability issues in the final product.
Conclusion
Understanding and managing PCB shelf life is crucial for ensuring the quality and reliability of electronic devices. For double side PCBs, the maximum shelf life after the first reflow can vary depending on various factors, such as storage conditions, material composition, and manufacturing processes.
By following best practices for PCB storage and handling, manufacturers can maximize the shelf life of their double side PCBs and minimize the risk of quality and functionality issues. Regular inspection, testing, and adherence to manufacturer guidelines can further ensure the longevity and reliability of these critical electronic components.
Leave a Reply