How Does a Pre-heater Work?
The working principle of a pre-heater depends on the specific type and design of the unit. However, the general concept involves the transfer of heat from a hot medium (such as exhaust gases or steam) to the raw materials or process fluids. This heat transfer occurs through various mechanisms, including:
-
Direct contact: In some pre-heaters, the hot medium is in direct contact with the material being heated. For example, in a suspension pre-heater used in the cement industry, hot exhaust gases from the kiln are mixed with the raw meal, allowing direct heat transfer.
-
Indirect contact: Other pre-heaters utilize indirect contact, where the hot medium and the material being heated are separated by a heat transfer surface, such as tubes or plates. Heat is transferred through conduction and convection without the two substances mixing. Shell and tube heat exchangers are a common example of indirect contact pre-heaters.
-
Regenerative heating: In regenerative pre-heaters, the heat transfer medium is alternately heated and cooled in a cyclic process. The medium absorbs heat from a hot source and then releases it to the material being heated. Regenerative pre-heaters are often used in high-temperature applications, such as in the steel industry.
Types of Pre-heaters
There are several types of pre-heaters used in industrial processes, each with its own unique design and application. Some common types include:
-
Suspension pre-heaters: Used in the cement industry to pre-heat raw meal before it enters the kiln. Hot exhaust gases from the kiln are used to heat the raw meal in a series of cyclones.
-
Shell and tube heat exchangers: Widely used in various industries for liquid-to-liquid or gas-to-liquid heat transfer. One fluid flows through the tubes, while the other fluid flows through the shell, allowing heat exchange between the two.
-
Plate heat exchangers: Consist of a series of corrugated plates stacked together, creating channels for hot and cold fluids to flow through alternately. These pre-heaters are compact and efficient, making them suitable for a wide range of applications.
-
Rotary regenerative pre-heaters: Used in high-temperature applications, such as in the steel industry. A rotating matrix of heat-absorbing material is alternately exposed to hot exhaust gases and cold inlet air, allowing heat transfer between the two streams.
Benefits of Using a Pre-heater
Incorporating a pre-heater into an industrial process offers several significant benefits:
-
Improved energy efficiency: By recovering waste heat from exhaust gases or other sources, pre-heaters reduce the amount of fuel required to heat the raw materials or process fluids. This leads to improved overall energy efficiency of the process.
-
Reduced fuel consumption: As pre-heaters utilize waste heat, the demand for primary fuel decreases. This results in lower fuel consumption and associated costs.
-
Increased production capacity: Pre-heating raw materials or process fluids allows the main processing unit to operate at a higher capacity, as it requires less time and energy to bring the materials up to the desired temperature.
-
Enhanced product quality: In some processes, pre-heating helps to ensure uniform heating of raw materials, leading to improved product quality and consistency.
-
Reduced emissions: By reducing fuel consumption, pre-heaters also contribute to lower greenhouse gas emissions and other pollutants associated with fuel combustion.
Applications of Pre-heaters in Different Industries
Pre-heaters find applications across various industries, playing a crucial role in optimizing process efficiency and product quality. Some key industries and their specific applications include:
Cement Industry
In the cement manufacturing process, pre-heaters are used to heat the raw meal (a mixture of limestone, clay, and other additives) before it enters the kiln. The most common type of pre-heater in this industry is the suspension pre-heater, which consists of a series of cyclones.
Hot exhaust gases from the kiln, with temperatures ranging from 800°C to 1100°C, are passed through the cyclones in a counter-current flow to the raw meal. The raw meal is fed into the top cyclone and progressively moves down through the series of cyclones, coming into direct contact with the hot gases. By the time the raw meal reaches the kiln, it is heated to about 800°C.
The pre-heating process in the cement industry offers several advantages:
-
Improved energy efficiency: Suspension pre-heaters recover a significant portion of the waste heat from the kiln exhaust gases, reducing the amount of fuel required in the kiln.
-
Increased production capacity: Pre-heating the raw meal allows the kiln to operate at a higher throughput, as it requires less time and energy to bring the material up to the desired temperature.
-
Reduced emissions: By reducing fuel consumption in the kiln, pre-heaters help to lower greenhouse gas emissions and other pollutants associated with fuel combustion.
Steel Industry
In the steel industry, pre-heaters are used in various stages of the manufacturing process, including the pre-heating of blast furnace air, coke oven gas, and combustion air for reheating furnaces.
One common type of pre-heater used in the steel industry is the rotary regenerative pre-heater, also known as a Cowper stove. These pre-heaters are used to heat the blast air before it enters the blast furnace. The working principle of a Cowper stove involves a cyclic process of heating and cooling a regenerative matrix, typically made of refractory bricks.
During the heating phase, hot exhaust gases from the blast furnace are passed through the matrix, heating the bricks to temperatures around 1200°C to 1400°C. Once the bricks are sufficiently heated, the exhaust gases are diverted, and cold blast air is passed through the matrix in the opposite direction. The cold air absorbs heat from the bricks, reaching temperatures of 900°C to 1200°C before entering the blast furnace.
The use of pre-heaters in the steel industry provides several benefits:
-
Improved blast furnace efficiency: Pre-heated blast air reduces the amount of coke required in the blast furnace, leading to improved energy efficiency and reduced operating costs.
-
Increased production capacity: With pre-heated blast air, the blast furnace can operate at a higher throughput, increasing the overall production capacity of the steel plant.
-
Reduced emissions: By reducing coke consumption in the blast furnace, pre-heaters contribute to lower greenhouse gas emissions and other pollutants associated with coke combustion.
Chemical Industry
In the chemical industry, pre-heaters are used to heat process fluids, such as reactants, solvents, or catalysts, before they enter reaction vessels or other processing units. The most common types of pre-heaters in this industry are shell and tube heat exchangers and plate heat exchangers.
Shell and tube heat exchangers consist of a bundle of tubes enclosed within a shell. One fluid (typically the hot medium) flows through the tubes, while the other fluid (the process fluid being heated) flows through the shell, on the outside of the tubes. Heat is transferred from the hot fluid to the process fluid through the tube walls.
Plate heat exchangers, on the other hand, consist of a series of corrugated plates stacked together, creating channels for hot and cold fluids to flow through alternately. The corrugated design of the plates enhances heat transfer by increasing the surface area and promoting turbulent flow.
The use of pre-heaters in the chemical industry offers several advantages:
-
Improved reaction kinetics: Pre-heating reactants to the desired temperature before they enter the reaction vessel can improve reaction rates and selectivity, leading to higher product yields and quality.
-
Reduced energy consumption: By recovering waste heat from process streams or utilities, pre-heaters help to reduce the overall energy consumption of the chemical plant.
-
Enhanced process safety: Pre-heating process fluids can help to prevent undesirable side reactions or phase changes that could lead to safety hazards or equipment damage.
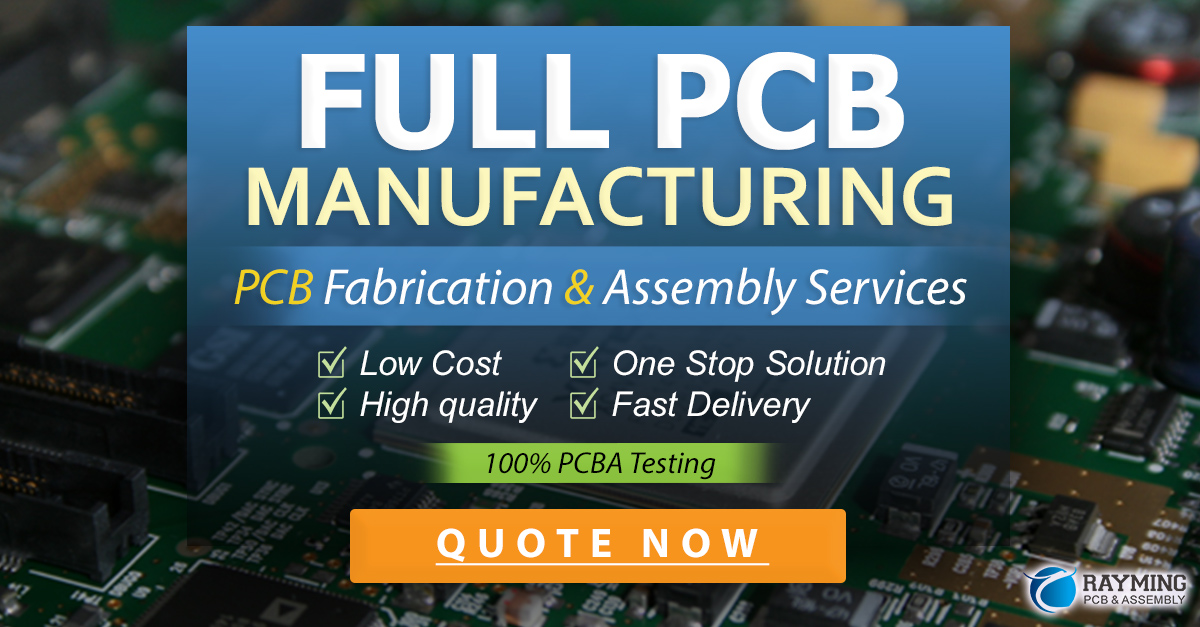
Designing and Selecting a Pre-heater
When designing or selecting a pre-heater for a specific industrial application, several key factors must be considered:
-
Heat duty: The heat duty is the amount of heat that needs to be transferred from the hot medium to the material being heated. This is determined by the flow rates, inlet and outlet temperatures, and the specific heat capacities of the fluids involved.
-
Temperature range: The operating temperature range of the pre-heater should be compatible with the process requirements and the materials of construction.
-
Pressure drop: The pressure drop across the pre-heater should be minimized to reduce pumping or compression costs and to ensure proper flow distribution.
-
Fouling tendency: The pre-heater design should account for the fouling tendency of the fluids involved. Fouling can reduce heat transfer efficiency and increase maintenance requirements.
-
Materials of construction: The materials used in the pre-heater should be compatible with the fluids being handled and the operating conditions, such as temperature, pressure, and corrosivity.
-
Space constraints: The size and layout of the pre-heater should be optimized to fit within the available space in the plant, while still meeting performance requirements.
-
Cost: The capital and operating costs of the pre-heater should be evaluated and optimized based on the specific application and process requirements.
Maintenance and Troubleshooting of Pre-heaters
To ensure the optimal performance and longevity of pre-heaters, regular maintenance and troubleshooting are essential. Some key aspects of pre-heater maintenance include:
-
Cleaning: Pre-heaters should be periodically cleaned to remove any fouling or deposits that can reduce heat transfer efficiency. The cleaning method and frequency will depend on the type of pre-heater and the nature of the fluids being handled.
-
Inspection: Regular inspections should be conducted to check for any signs of wear, corrosion, or damage to the pre-heater components, such as tubes, plates, or seals.
-
Performance monitoring: Key performance indicators, such as inlet and outlet temperatures, flow rates, and pressure drops, should be continuously monitored to detect any deviations from normal operating conditions.
-
Calibration: Instrumentation and control systems associated with the pre-heater should be regularly calibrated to ensure accurate measurement and control of process parameters.
If performance issues are detected during operation, troubleshooting steps may include:
-
Checking for leaks: Leaks in the pre-heater can lead to reduced performance and potential safety hazards. Any leaks should be promptly identified and repaired.
-
Verifying flow distribution: Uneven flow distribution can lead to localized fouling or overheating. The flow distribution should be checked and adjusted as necessary to ensure uniform heat transfer.
-
Evaluating heat transfer coefficients: A decrease in heat transfer coefficients can indicate fouling, scaling, or other issues that reduce pre-heater efficiency. Cleaning or other maintenance actions may be required to restore performance.
-
Assessing control system performance: The control system should be evaluated to ensure that it is properly regulating process parameters, such as temperatures and flow rates, within the desired ranges.
Frequently Asked Questions (FAQ)
-
What is the difference between a pre-heater and a heat exchanger?
A pre-heater is a specific type of heat exchanger that is used to heat raw materials or process fluids before they enter the main processing unit. Heat exchangers, on the other hand, are a broader category of equipment that includes pre-heaters and other types of devices used for transferring heat between two or more fluids. -
Can pre-heaters be used for cooling applications?
While pre-heaters are primarily designed for heating applications, some types of heat exchangers, such as shell and tube or plate heat exchangers, can be used for both heating and cooling applications, depending on the configuration and the temperatures of the fluids involved. -
How do I select the right type of pre-heater for my process?
The selection of the right type of pre-heater depends on several factors, including the heat duty, temperature range, pressure drop, fouling tendency, materials of construction, space constraints, and cost. It is essential to work with an experienced heat transfer equipment supplier or consultant to evaluate the specific requirements of your process and recommend the most suitable pre-heater option. -
How often should I clean my pre-heater?
The cleaning frequency for a pre-heater depends on the type of pre-heater, the nature of the fluids being handled, and the operating conditions. Some pre-heaters may require cleaning every few months, while others may operate for several years without needing cleaning. It is important to monitor the performance of the pre-heater and establish a cleaning schedule based on the specific needs of your process. -
What are the signs that my pre-heater may need maintenance or repair?
Some common signs that a pre-heater may need maintenance or repair include reduced heat transfer efficiency, increased pressure drop, leaks, unusual noises or vibrations, and visible damage to the pre-heater components. If any of these signs are observed, it is important to investigate the issue promptly and take appropriate maintenance or repair actions to prevent further damage or performance deterioration.
Conclusion
Pre-heaters are essential components in many industrial processes, providing a means to efficiently heat raw materials or process fluids before they enter the main processing unit. By recovering waste heat and reducing fuel consumption, pre-heaters contribute to improved energy efficiency, increased production capacity, and reduced emissions.
The selection, design, and maintenance of pre-heaters require careful consideration of various factors, such as heat duty, temperature range, fouling tendency, and materials of construction. Working with experienced heat transfer equipment suppliers and following best practices for maintenance and troubleshooting can help ensure the optimal performance and longevity of pre-heaters in industrial applications.
As industries continue to focus on sustainability and energy efficiency, the role of pre-heaters in optimizing process performance and reducing environmental impact will remain crucial. Ongoing research and development in heat transfer technologies will likely lead to further advancements in pre-heater design and application, enabling even greater benefits for industrial processes in the future.
Leave a Reply