FR4 and alumina are two widely used printed circuit board (PCB) substrate materials with distinct properties and trade-offs.
FR4 is the ubiquitous budget substrate for everyday electronics, while alumina ceramic caters to specialized high performance applications.
This article examines the key differences between FR4 and alumina PCB substrates in terms of composition, properties, fabrication, costs and typical applications.
FR4 PCB Overview
FR4 is the common substrate material used in majority of PCBs. It consists of woven fiberglass cloth bonded with an epoxy resin matrix.
Some key properties of FR4 PCBs are:
- Low cost, standard material
- Moderate thermal conductivity
- Low thermal expansion coefficient
- Easy drilling and machining
- Good mechanical strength
- Simple PCB fabrication process
- Absorbs moisture affecting electrical properties
- Maximum operating temperature around 130°C
FR4 offers a balance of electrical performance, mechanical rigidity, ease of fabrication and cost-effectiveness for a wide range of commercial electronic products.
Alumina PCB Overview
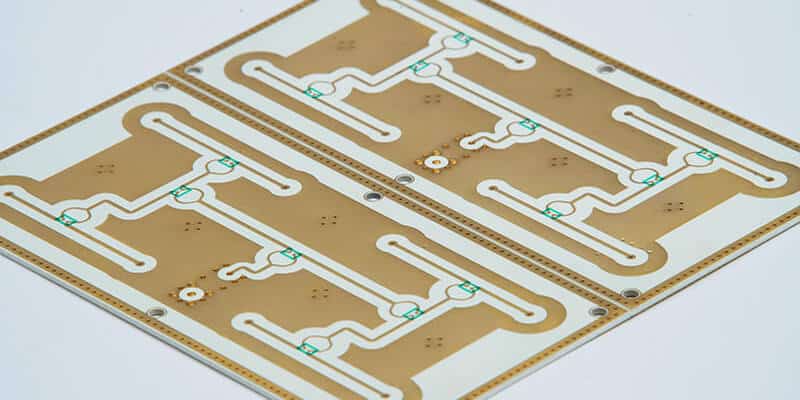
Alumina PCBs utilize aluminum oxide ceramic as the substrate material instead of FR4 laminates.
Some salient properties of alumina PCBs include:
- High thermal conductivity for heat dissipation
- Electrically insulating up to high frequencies
- Temperature resistant exceeding 250°C
- Resilient to harsh chemicals, moisture, and radiation
- Hermetic sealing of components
- Hard and wear resistant surface
- Excellent dimensional stability
- Challenging PCB fabrication requiring high temperatures
These characteristics make alumina PCBs suitable for specialized applications with extreme temperature, power, frequency or environmental requirements.
Composition and Structure Difference
The composition and structure difference between the materials leads to the variance in substrate properties:
FR4
FR4 consists of woven fiberglass cloth fabric bonded together using epoxy resin. The epoxy polymer matrix provides electrical insulation while the glass fibers give mechanical rigidity.
Alumina
Alumina ceramic consists of aluminum oxide molecules arranged in a crystalline structure through strong ionic and covalent bonds. There are no polymeric components.
Property Differences
Some key differences in the properties of FR4 vs alumina PCB substrates are:
Parameter | FR4 PCB | Alumina PCB |
---|---|---|
Thermal conductivity | 0.25 W/mK | 30 W/mK |
Coefficient of thermal expansion | 17 ppm/°C | 7 ppm/°C |
Maximum operating temperature | 130°C | >250°C |
Water absorption | 0.2% | Zero |
Surface hardness | Soft | 9 Mohs scale |
Dielectric strength | Good | Excellent |
High frequency performance | Moderate | Excellent |
Fabrication | Standard PCB processes | Challenging, requires high heat |
Flexibility | Flexible | Brittle |
Chemical resistance | moderate | Excellent |
Cost | Low | High |
Design and Layout Differences
PCB layout and design considerations also differ between FR4 and alumina boards:
FR4 PCBs
- Large panel sizes available
- Fine line widths and spacing
- Closely spaced vias possible
- Minimal constraints on component types and sizes
- Standard drilling and routing
- Requires solder mask layer
- Multiple supplier options
Alumina PCBs
- Smaller panel sizes
- Larger minimum line widths and spacing
- Via spacing requirements to prevent cracking
- High temperature assembly limitations
- Challenging machining requiring diamond tooling
- Commercial alumina options limited
Fabrication Process Differences
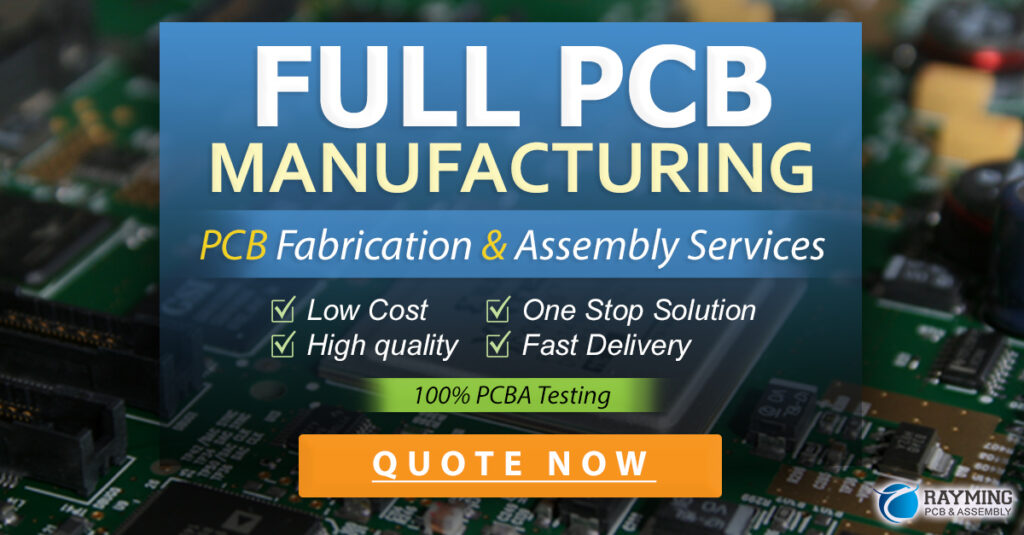
FR4 PCB Fabrication
- Simple lamination of epoxy prepregs
- Drilling holes after lamination
- Plating vias and conductors
- Photolithographic patterning of conductors
- Screen printing solder mask and legends
Alumina PCB Fabrication
- Tape casting of ceramic slurry
- Punching vias before lamination
- Screen printing conductors using tungsten or molybdenum based inks
- Layer stacking and high pressure lamination
- Binder burnout and sintering over 1000°C
- Edge metallization before firing
- Plating vias and conductors post-firing
- Metallization compatible with ceramic co-firing
So alumina PCB fabrication involves specialized ceramic processes like tape casting, binder burnout, high temperature sintering and metallization compatible with ceramics.
Cost Difference
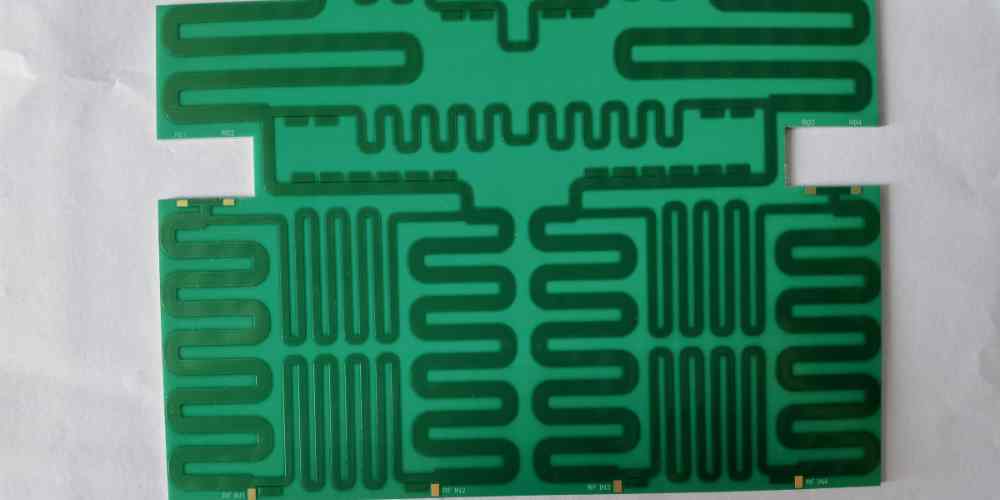
The costs of FR4 and alumina PCBs differ significantly:
- FR4 PCB Cost – Ranges from $2 to $15 per square foot depending on layer count, density, size and quantity.
- Alumina PCB Cost – $50 to $300+ per square foot owing to exotic material, processing complexity and smaller volumes.
So alumina PCBs cost at least 4-5 times more than FR4 boards. Their high performance justifies the price premium for certain applications.
Typical Applications
FR4 PCB Applications
- Consumer electronics
- Computers and IT equipment
- Communication systems
- Industrial controls
- Instrumentation
- Automotive electronics
Alumina PCB Applications
- Military and aerospace systems
- Power electronics and power supplies
- Electric vehicle components
- Downhole drilling tools
- Medical devices and implants
- Wireless infrastructure
- Automotive engine electronics
FAQs
Can you solder components to alumina PCB?
Yes, active brazing alloys are used to solder components to alumina PCBs to withstand the high ceramic temperatures. Soldering is done before firing or via high temperature surface mount post-fire.
What are some alternatives to alumina for ceramic PCBs?
Alternatives include aluminum nitride for thermal performance, glass ceramic for cost benefits, beryllium oxide for high frequency, and silicon nitride for mechanical strength.
Is alumina hydrophilic or hydrophobic?
Alumina possesses a hydrophilic water-loving surface that tends to absorb moisture, unlike hydrophobic FR4. Hermetic sealing of components is required.
Can you bend alumina PCBs?
No, alumina PCBs cannot be bent or flexed owing to the brittle and rigid nature of ceramics. Alumina lacks the flexibility of FR4 boards.
Which is better – FR4 or alumina substrate?
For most commercial applications, FR4 provides the optimal balance of cost and performance. Alumina is chosen when extreme temperature, power or other specialized capabilities are needed despite higher cost.
In summary, while both are PCB substrate materials, alumina and FR4 differ significantly in composition, properties, fabrication, costs and target applications. Alumina ceramic caters to high performance and reliability demands unachievable with standard FR4 boards.
Leave a Reply