Understanding the Basics of a Custom Drone Board
To fully understand the core of a custom drone board, it is essential to familiarize yourself with its basic components and their roles:
Microcontroller or Flight Controller
The microcontroller, also known as the flight controller, is the brain of the drone. It processes data from various sensors and controls the motors, ensuring stable and controlled flight. Some popular flight controllers include:
- Arduino-based boards
- Pixhawk
- Naze32
- CC3D
Sensors
Drones rely on a variety of sensors to maintain stability, navigate, and gather data. The most common sensors found on a custom drone board include:
- Gyroscope: Measures angular velocity and helps maintain orientation
- Accelerometer: Measures acceleration and detects tilt
- Magnetometer: Acts as a compass, providing heading information
- Barometer: Measures atmospheric pressure to determine altitude
- GPS: Provides precise location data for navigation
Motor Speed Controllers (ESCs)
ESCs are responsible for controlling the speed and direction of the drone’s motors. They receive signals from the flight controller and regulate the power supplied to the motors accordingly. The number of ESCs on a custom drone board depends on the number of motors the drone has (e.g., quadcopter, hexacopter, octocopter).
Power Distribution Board (PDB)
The PDB distributes power from the battery to the various components of the drone, such as the flight controller, ESCs, and sensors. It also provides voltage regulation and protection against short circuits and overcurrent.
Radio Receiver
The radio receiver allows the drone to communicate with the ground control station or remote control. It receives commands from the pilot and relays them to the flight controller for execution.
Designing a Custom Drone Board
When designing a custom drone board, several factors must be considered to ensure optimal performance and reliability:
Size and Weight
The size and weight of the drone board are critical, as they directly impact the drone’s flight time, maneuverability, and payload capacity. A smaller and lighter board allows for longer flight times and better agility, while a larger board may be necessary to accommodate additional sensors or peripherals.
Power Efficiency
Efficient power management is essential for maximizing flight time and preventing component damage. The custom drone board should be designed to minimize power consumption and heat generation, using high-quality voltage regulators and power distribution components.
Sensor Integration
The board must be designed to accommodate the necessary sensors for the drone’s intended application. This involves selecting appropriate sensor modules, designing the PCB layout to minimize interference, and developing firmware to process and interpret sensor data.
Modularity and Expandability
A modular design allows for easy upgrades and customization of the drone board. By using standard connectors and protocols (e.g., I2C, SPI, UART), additional sensors or peripherals can be added without significant modifications to the board.
Reliability and Durability
Drones are subjected to various environmental stresses, such as vibration, temperature fluctuations, and moisture. The custom drone board must be designed to withstand these conditions, using high-quality components, robust PCB Construction, and protective enclosures.
Manufacturing a Custom Drone Board
Once the design is finalized, the custom drone board can be manufactured using the following process:
-
PCB Fabrication: The PCB layout is sent to a manufacturer, who creates the physical board using materials such as FR-4, aluminum, or flexible substrates.
-
Component Sourcing: The necessary components, such as the microcontroller, sensors, and power regulators, are procured from reliable suppliers.
-
PCB assembly: The components are soldered onto the PCB, either through manual assembly or automated processes like SMT (Surface Mount Technology) or THT (Through-Hole Technology).
-
Quality Control: The assembled board undergoes rigorous testing to ensure proper functionality, including continuity tests, power-on tests, and firmware validation.
-
Integration: The custom drone board is integrated with the other drone components, such as the frame, motors, and propellers, to create a complete and functional drone.
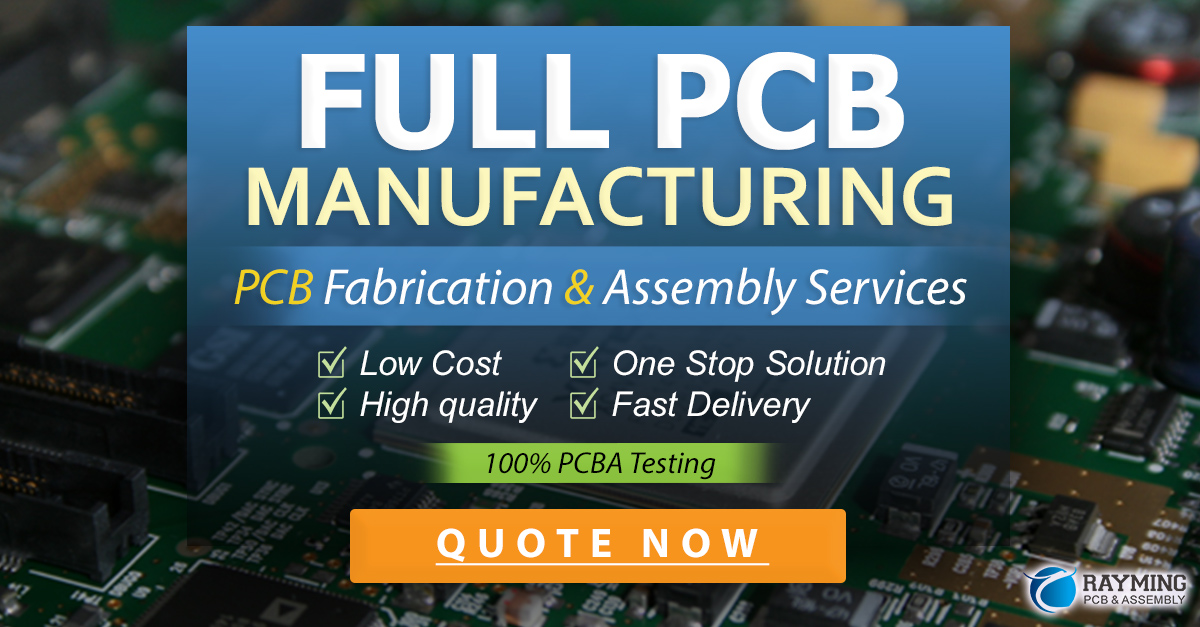
Firmware Development for Custom Drone Boards
Firmware is the software that runs on the microcontroller, controlling the drone’s behavior and processing sensor data. Developing firmware for a custom drone board involves the following steps:
-
Choosing a Programming Language: Popular choices include C, C++, and Python, depending on the microcontroller and the developer’s preference.
-
Configuring Peripherals: The firmware must initialize and configure the microcontroller’s peripherals, such as GPIO pins, I2C, SPI, and UART, to communicate with sensors and other components.
-
Sensor Integration: Drivers and libraries for the sensors must be developed or adapted to work with the custom drone board, ensuring accurate data acquisition and interpretation.
-
Control Algorithms: The firmware must implement control algorithms, such as PID (Proportional-Integral-Derivative) or AHRS (Attitude and Heading Reference System), to maintain stable flight and execute user commands.
-
Fail-safe Mechanisms: Safety features, such as auto-landing or return-to-home, must be implemented to prevent crashes or loss of control in case of emergencies.
-
Testing and Debugging: Thorough testing and debugging are essential to ensure the firmware is reliable, efficient, and free of bugs.
Applications of Custom Drone Boards
Custom drone boards find applications in various fields, such as:
- Agriculture: Precision farming, crop monitoring, and spraying
- Surveillance and Security: Aerial surveillance, border patrol, and crowd monitoring
- Delivery Services: Package delivery, medical supply transport, and food delivery
- Search and Rescue: Disaster relief, missing person searches, and wildlife conservation
- Photography and Videography: Aerial photography, cinematography, and 3D mapping
Frequently Asked Questions (FAQ)
-
Q: What is the difference between a custom drone board and an off-the-shelf flight controller?
A: A custom drone board is designed specifically for a particular drone, taking into account its unique requirements and applications. Off-the-shelf flight controllers, on the other hand, are generic boards that cater to a wider range of drones and may not be optimized for specific use cases. -
Q: Can I use a custom drone board for a commercial drone?
A: Yes, custom drone boards can be used for commercial drones, provided they meet the necessary regulations and certifications for the specific application and region. -
Q: How much does it cost to develop a custom drone board?
A: The cost of developing a custom drone board varies depending on factors such as the complexity of the design, the components used, and the scale of production. Prototype development can range from a few hundred to several thousand dollars, while large-scale production can lead to lower per-unit costs. -
Q: What skills are required to design and develop a custom drone board?
A: Designing and developing a custom drone board requires a combination of skills, including: - PCB design and layout
- Embedded systems programming
- Sensor integration and data processing
- Control systems engineering
-
Mechanical design and integration
-
Q: How long does it take to develop a custom drone board?
A: The development time for a custom drone board depends on the complexity of the design and the experience of the development team. A simple prototype can be developed in a few weeks, while a more complex board with advanced features and optimizations can take several months to a year.
In conclusion, a custom drone board is the core of a drone, responsible for connecting and controlling all the components. Designing and developing a custom drone board requires careful consideration of factors such as size, weight, power efficiency, sensor integration, and reliability. With the right skills and resources, custom drone boards can be developed for a wide range of applications, from agriculture and surveillance to delivery services and search and rescue operations.
Leave a Reply