How Peelable Soldermask Works
Peelable soldermask is typically applied to PCBs using screen printing or spray coating techniques. The mask is composed of a polymer material that is formulated to withstand the high temperatures associated with soldering while remaining easy to remove once the process is complete.
The main functions of peelable soldermask include:
- Protecting specific areas of the PCB from solder during the soldering process
- Preventing solder bridges and short circuits
- Facilitating selective soldering of components
- Allowing for easy inspection and rework of soldered joints
Application Process
The application process for peelable soldermask involves several steps:
- PCB Cleaning: The PCB surface is thoroughly cleaned to remove any contaminants that may affect the adhesion of the soldermask.
- Soldermask Application: The peelable soldermask is applied to the PCB using screen printing or spray coating techniques. The thickness of the mask varies depending on the specific requirements of the project.
- Curing: The applied soldermask is cured using heat or UV light to ensure proper adhesion and durability.
- Soldering: The PCB undergoes the soldering process, with the peelable soldermask protecting the desired areas from solder.
- Removal: After soldering, the peelable soldermask is carefully removed, exposing the underlying copper for further processing or inspection.
Advantages of Peelable Soldermask
Peelable soldermask offers several advantages over traditional permanent soldermask:
- Selective Soldering: Peelable soldermask allows for selective soldering of components, which is particularly useful for PCBs with high component density or complex designs.
- Improved Inspection: With the soldermask removed, the soldered joints can be easily inspected for quality and accuracy.
- Rework and Repair: If a soldered joint requires rework or repair, the peelable soldermask can be easily removed, allowing for access to the affected area.
- Compatibility with Various Soldering Techniques: Peelable soldermask is compatible with a range of soldering techniques, including wave soldering, selective soldering, and hand soldering.
Characteristics of High-Quality Peelable Soldermask
To ensure optimal performance, peelable soldermask should possess several key characteristics:
- Temperature Resistance: The soldermask must withstand the high temperatures associated with soldering without degrading or losing its protective properties.
- Easy Removal: The soldermask should be easily removable after soldering without leaving residue or damaging the underlying copper.
- Good Adhesion: The soldermask must adhere well to the PCB surface to prevent lifting or peeling during the soldering process.
- Compatibility with PCB Materials: The soldermask should be compatible with the various materials used in PCB fabrication, such as FR-4, polyimide, and flexible substrates.
- Consistent Thickness: The soldermask should be applied with a consistent thickness to ensure uniform protection and ease of removal.
Comparison with Permanent Soldermask
While peelable soldermask offers several advantages, it is important to understand the differences between peelable and permanent soldermask:
Characteristic | Peelable Soldermask | Permanent Soldermask |
---|---|---|
Durability | Temporary protection during soldering | Long-term protection throughout PCB lifetime |
Removal | Easily removable after soldering | Designed to remain on the PCB permanently |
Thickness | Typically thicker than permanent soldermask | Thinner and more uniform |
Cost | Higher cost due to specialized materials and processing | Lower cost for standard PCB fabrication |
The choice between peelable and permanent soldermask depends on the specific requirements of the project, such as the need for selective soldering, ease of inspection, and rework capabilities.
Applications of Peelable Soldermask
Peelable soldermask finds applications in various industries and product categories, including:
- Consumer Electronics: Smartphones, tablets, laptops, and wearables
- Automotive Electronics: Engine control units, infotainment systems, and sensors
- Medical Devices: Implantable devices, diagnostic equipment, and monitoring systems
- Industrial Equipment: Process control systems, automation devices, and power electronics
- Aerospace and Defense: Avionics, military communications, and satellite components
In each of these applications, peelable soldermask enables the production of high-quality, reliable PCBs with enhanced soldering accuracy and ease of inspection.
Case Study: Smartphone PCB Assembly
Smartphone PCBs are a prime example of the benefits of peelable soldermask. These PCBs are characterized by high component density, complex layouts, and the need for precise soldering. Peelable soldermask allows for selective soldering of fine-pitch components, such as ball grid arrays (BGAs) and quad-flat no-leads (QFNs), without affecting nearby components.
After soldering, the peelable soldermask is removed, allowing for thorough visual inspection of the soldered joints. If any issues are identified, the affected areas can be easily reworked without damaging the surrounding components.
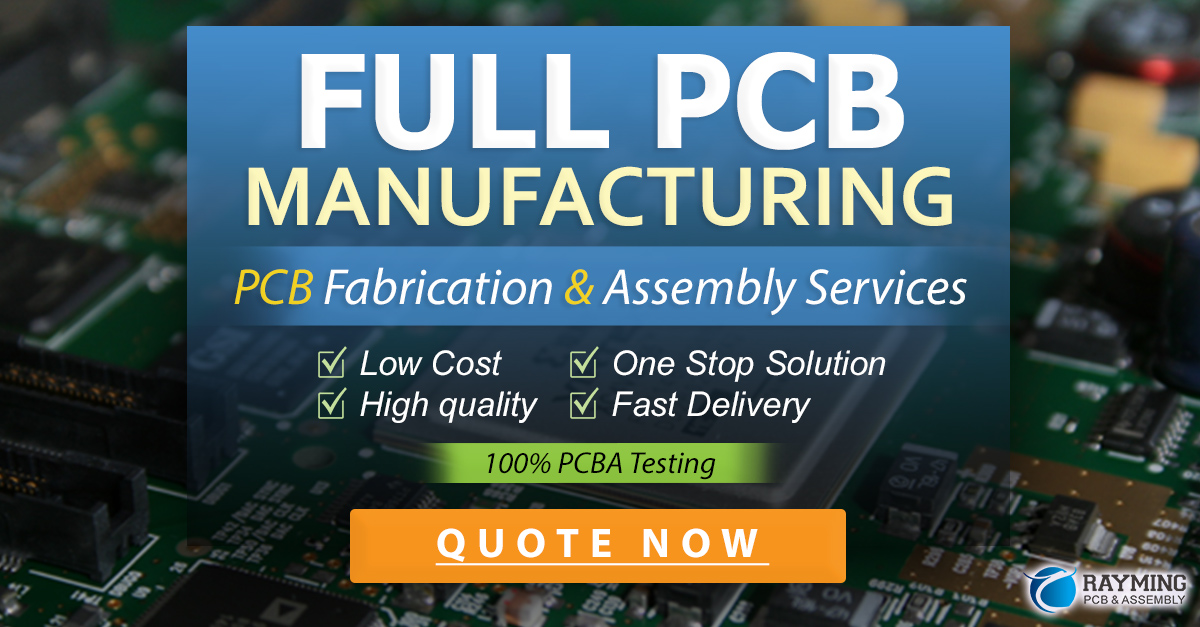
Challenges and Considerations
While peelable soldermask offers numerous benefits, there are some challenges and considerations to keep in mind:
- Cost: Peelable soldermask is typically more expensive than permanent soldermask due to the specialized materials and processing required.
- Compatibility: Not all PCB materials and surface finishes are compatible with peelable soldermask. It is important to consult with the PCB manufacturer to ensure compatibility.
- Removal Process: The removal of peelable soldermask must be done carefully to avoid damaging the underlying copper or components. Proper training and equipment are necessary for successful removal.
- Environmental Considerations: The disposal of removed peelable soldermask must be done in accordance with local environmental regulations.
Despite these challenges, the benefits of peelable soldermask make it a valuable tool for PCB assembly in a wide range of industries.
Frequently Asked Questions (FAQ)
-
Q: Can peelable soldermask be used on all types of PCBs?
A: Peelable soldermask is compatible with most PCB materials, including FR-4, polyimide, and flexible substrates. However, it is important to consult with the PCB manufacturer to ensure compatibility with the specific materials and surface finishes used in your project. -
Q: How does peelable soldermask compare to other selective soldering techniques?
A: Peelable soldermask offers several advantages over other selective soldering techniques, such as laser masking or selective wave soldering. It provides a more cost-effective solution for high-volume production, allows for easy removal and inspection, and is compatible with a wider range of PCB materials and components. -
Q: Can peelable soldermask be used for double-sided PCBs?
A: Yes, peelable soldermask can be applied to both sides of a double-sided PCB. This allows for selective soldering on both sides of the board, which is particularly useful for complex designs with components on both sides. -
Q: How does the thickness of peelable soldermask affect its performance?
A: The thickness of peelable soldermask is typically higher than that of permanent soldermask to ensure adequate protection during soldering. However, the thickness should be carefully controlled to ensure easy removal and compatibility with the specific soldering process used. -
Q: Are there any special handling or storage requirements for PCBs with peelable soldermask?
A: PCBs with peelable soldermask should be handled and stored with care to avoid damaging the mask. They should be kept in a clean, dry environment and protected from excessive heat or humidity. Proper handling and storage procedures should be followed to ensure the integrity of the peelable soldermask.
Conclusion
Peelable soldermask is a valuable tool for PCB assembly, offering numerous benefits over traditional permanent soldermask. Its ability to provide selective soldering, easy removal, and improved inspection capabilities make it an attractive option for a wide range of industries and applications.
As PCB designs continue to become more complex and component densities increase, the use of peelable soldermask is likely to grow. By understanding the characteristics, advantages, and challenges associated with peelable soldermask, engineers and PCB manufacturers can make informed decisions about when and how to incorporate this technology into their projects.
As with any specialized process, it is important to work closely with experienced PCB manufacturers and assembly partners to ensure the successful implementation of peelable soldermask. By leveraging the expertise of these professionals, companies can realize the full benefits of this innovative technology and produce high-quality, reliable PCBs that meet the demands of today’s complex electronic devices.
Leave a Reply