Introduction to Peelable Solder Mask
Peelable solder mask (PSM) is a specialized type of solder mask used in printed circuit board (PCB) manufacturing. It is a temporary protective coating applied to specific areas of a PCB during the soldering process, providing a barrier against solder bridging and ensuring precise solder application. Unlike permanent solder masks, peelable solder masks can be easily removed after the soldering process is complete, leaving behind clean and exposed contact pads ready for further assembly or testing.
What is a Solder Mask?
A solder mask, also known as a solder resist or solder stop, is a protective layer applied to the copper traces of a PCB. Its primary purpose is to prevent solder from adhering to unwanted areas of the board during the soldering process. Solder masks are typically made of a polymer material and are applied through various methods such as screen printing, liquid photoimaging, or dry film lamination.
Solder masks serve several important functions in PCB manufacturing:
- Solder Control: Solder masks define the areas where solder should be applied, preventing solder bridges and short circuits.
- Protection: They protect the copper traces from oxidation, corrosion, and mechanical damage.
- Insulation: Solder masks provide electrical insulation between adjacent traces and components.
- Aesthetics: They enhance the visual appearance of the PCB by providing a uniform color and finish.
Advantages of Peelable Solder Mask
Peelable solder masks offer several advantages over traditional permanent solder masks in certain PCB manufacturing scenarios:
- Selective Soldering: PSMs allow for selective soldering of specific components or areas on the PCB. This is particularly useful for complex boards with multiple soldering steps or when certain components need to be soldered separately.
- Improved Solder Joint Quality: By preventing solder from spreading to unwanted areas, peelable solder masks help achieve cleaner and more precise solder joints, reducing the risk of bridging or short circuits.
- Ease of Removal: Unlike permanent solder masks, peelable masks can be easily removed after the soldering process. This eliminates the need for additional cleaning steps and allows for immediate inspection and testing of the soldered components.
- Compatibility with Various Soldering Techniques: Peelable solder masks are compatible with different soldering methods, including wave soldering, selective soldering, and hand soldering.
- Cost-Effective: PSMs can be a cost-effective solution for prototyping or low-volume production runs, as they eliminate the need for expensive solder mask application and removal equipment.
Types of Peelable Solder Masks
Peelable solder masks come in different forms, each with its own characteristics and application methods. The most common types of PSMs are:
Liquid Peelable Solder Masks
Liquid peelable solder masks are applied to the PCB using screen printing or spray coating techniques. They are typically made of a water-based or solvent-based polymer material that cures upon exposure to heat or UV light. After the soldering process, the mask can be easily peeled off by hand or with tweezers.
Advantages of liquid peelable solder masks include:
– Easy application using standard screen printing or spraying equipment
– Good adhesion to the PCB surface
– Ability to achieve thin and uniform coating thickness
– Fast curing time
Dry Film Peelable Solder Masks
Dry film peelable solder masks are supplied in the form of a pre-formed film that is laminated onto the PCB surface using heat and pressure. The film consists of a polymer material coated on a carrier sheet, which is removed after lamination. Dry film PSMs offer excellent dimensional stability and can be patterned using photolithography techniques.
Advantages of dry film peelable solder masks include:
– High resolution and accuracy in patterning
– Consistent thickness and uniformity
– Good chemical and thermal resistance
– Easy handling and storage
Peelable Solder Mask Tapes
Peelable solder mask tapes are pre-cut adhesive tapes that are manually applied to specific areas of the PCB where solder masking is required. These tapes are made of a heat-resistant polymer material with a pressure-sensitive adhesive backing. After the soldering process, the tapes can be easily peeled off, leaving behind clean and exposed contact pads.
Advantages of peelable solder mask tapes include:
– Quick and easy application
– Flexibility in placement and patterning
– No curing or drying time required
– Suitable for small-scale or prototype production
Peelable Solder Mask Application Process
The application process for peelable solder masks varies depending on the type of PSM being used. However, the general steps involved in applying a peelable solder mask are as follows:
-
PCB Cleaning: The PCB surface is thoroughly cleaned to remove any contaminants, oxides, or residues that may affect the adhesion of the solder mask.
-
Solder Mask Application: The peelable solder mask is applied to the PCB using the appropriate method (screen printing, lamination, or manual taping) based on the type of PSM being used.
-
Curing or Drying: If required, the applied solder mask is cured or dried according to the manufacturer’s specifications. This step ensures proper adhesion and stability of the mask.
-
Soldering: The PCB undergoes the soldering process, such as wave soldering or selective soldering, with the peelable solder mask in place. The mask prevents solder from adhering to the protected areas.
-
Mask Removal: After soldering, the peelable solder mask is carefully removed by peeling it off the PCB surface. This can be done manually using tweezers or by using an automated peeling machine for larger production volumes.
-
Inspection and Cleaning: The exposed contact pads are inspected for any residues or damage. If necessary, a cleaning step may be performed to remove any remaining solder mask particles or flux residues.
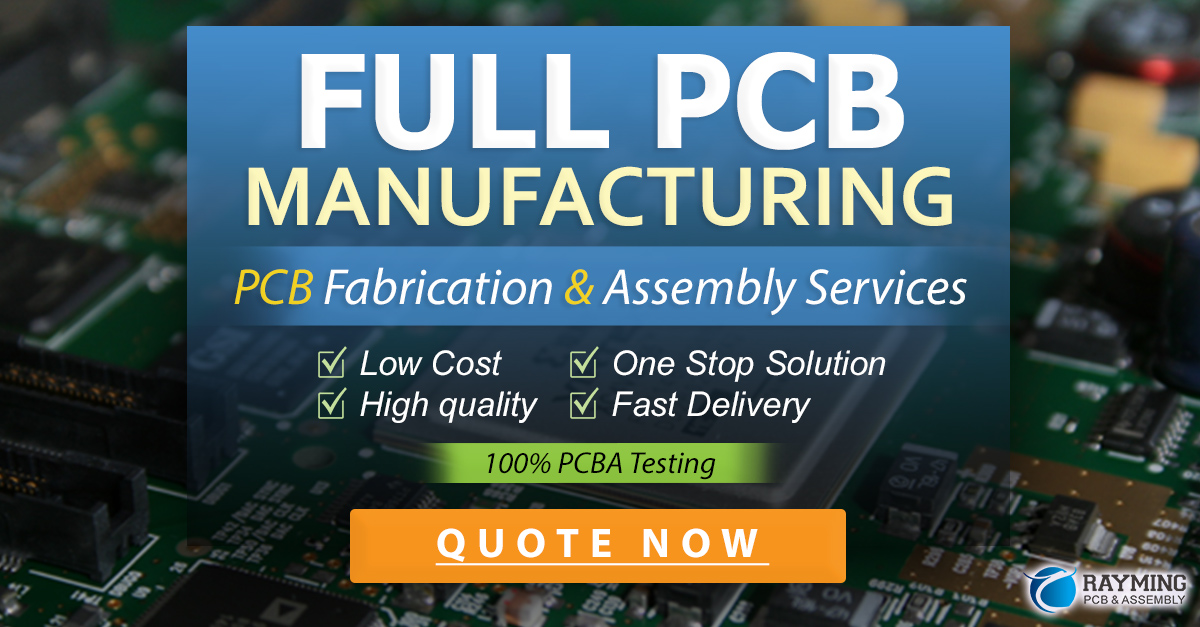
Considerations for Using Peelable Solder Masks
When using peelable solder masks in PCB manufacturing, there are several factors to consider to ensure optimal results:
Compatibility with PCB Materials
It is important to select a peelable solder mask that is compatible with the PCB substrate material and the soldermask being used. Some PSMs may not adhere properly to certain surfaces or may leave residues that can affect the performance of the PCB.
Thickness and Coverage
The thickness and coverage of the peelable solder mask should be carefully controlled to ensure adequate protection during soldering while also allowing for easy removal. Too thick a layer may be difficult to remove, while too thin a layer may not provide sufficient protection.
Curing and Drying Conditions
If the peelable solder mask requires curing or drying, it is crucial to follow the manufacturer’s recommended guidelines for temperature, time, and humidity. Improper curing or drying can lead to poor adhesion, incomplete protection, or difficulty in removing the mask.
Removal Technique
The removal of the peelable solder mask should be done carefully to avoid damaging the PCB or the components. It is recommended to use tweezers or a dedicated peeling tool to minimize the risk of lifting pads or traces. In some cases, using a solvent or heat may be necessary to facilitate the removal process.
Storage and Shelf Life
Peelable solder masks have a limited shelf life and should be stored according to the manufacturer’s instructions. Factors such as temperature, humidity, and exposure to light can affect the performance and usability of the PSM. It is important to use the solder mask within its specified shelf life to ensure optimal results.
Frequently Asked Questions (FAQ)
-
Q: Can peelable solder masks be used for all types of PCBs?
A: Peelable solder masks are suitable for most types of PCBs, including rigid, flexible, and rigid-flex boards. However, compatibility with the specific PCB material and soldermask should be verified before use. -
Q: How long does it take to apply and remove a peelable solder mask?
A: The application time depends on the type of PSM and the method used. Liquid masks may take a few minutes to screen print and cure, while dry film masks require lamination and exposure. Removal typically takes only a few seconds to a minute per component or area. -
Q: Are peelable solder masks reusable?
A: No, peelable solder masks are designed for single use only. Once removed, they cannot be reapplied to the PCB. -
Q: Can peelable solder masks be used for high-volume production?
A: While peelable solder masks are commonly used for prototyping and low-volume production, they can also be used in high-volume manufacturing with the help of automated application and removal equipment. -
Q: Are there any environmental concerns with using peelable solder masks?
A: Most peelable solder masks are made of non-toxic and environmentally friendly materials. However, it is important to properly dispose of used masks and any waste generated during the application and removal process in accordance with local regulations.
Conclusion
Peelable solder masks are a valuable tool in PCB manufacturing, providing temporary protection during the soldering process and enabling selective soldering of specific components or areas. They offer advantages such as improved solder joint quality, ease of removal, and compatibility with various soldering techniques. By understanding the types of peelable solder masks available, their application process, and the considerations for their use, PCB manufacturers can effectively incorporate PSMs into their production workflows to achieve optimal results and efficiency.
As PCB designs continue to become more complex and miniaturized, the use of peelable solder masks is likely to grow in importance. Advancements in PSM materials and application techniques will further enhance their performance and usability, making them an indispensable part of modern PCB manufacturing processes.
Leave a Reply