What is PCB Solder Mask?
PCB solder mask, also known as solder resist or solder stop mask, is a thin layer of polymer that is applied to the copper traces of a printed circuit board (PCB). The primary purpose of the solder mask is to protect the copper traces from oxidation, prevent solder bridges from forming between closely spaced pads, and provide electrical insulation.
Solder mask is usually applied as a liquid or dry film and then cured through exposure to UV light or heat. The most common colors for solder mask are green, red, blue, and black, although other colors are available for specific applications.
Composition of Solder Mask
Solder mask is typically composed of the following materials:
- Epoxy resins
- Photoinitiators
- Fillers
- Pigments
- Additives (such as adhesion promoters and flow control agents)
The exact composition of the solder mask may vary depending on the manufacturer and the specific requirements of the PCB.
Functions of PCB Solder Mask
1. Protection from Oxidation
One of the primary functions of solder mask is to protect the copper traces on the PCB from oxidation. When exposed to air, copper can quickly oxidize, forming a layer of copper oxide that can negatively impact the electrical conductivity of the traces. By covering the copper with a layer of solder mask, oxidation is prevented, ensuring the long-term reliability of the PCB.
2. Prevention of Solder Bridges
Solder mask also helps to prevent the formation of solder bridges between closely spaced pads or traces. During the soldering process, molten solder can sometimes flow between adjacent pads, creating unintended electrical connections known as solder bridges. These bridges can cause short circuits and other issues that can compromise the functionality of the PCB. Solder mask acts as a barrier, preventing the solder from flowing where it shouldn’t.
3. Electrical Insulation
Another important function of solder mask is to provide electrical insulation between the copper traces and the environment. This insulation helps to prevent short circuits caused by accidental contact with conductive materials and reduces the risk of electrical shock to users.
4. Improved Aesthetics
In addition to its practical functions, solder mask also enhances the aesthetics of the PCB. The various colors available for solder mask can be used to create visually appealing designs or to color-code different sections of the board for easier identification.
Solder Mask Application Process
The process of applying solder mask to a PCB typically involves the following steps:
-
Cleaning: The bare PCB is thoroughly cleaned to remove any contaminants that could interfere with the adhesion of the solder mask.
-
Solder Mask Application: The solder mask is applied to the PCB, either as a liquid or a dry film. Liquid solder mask is typically applied using a screen printing process, while dry film solder mask is laminated onto the board.
-
Exposure: The solder mask is then exposed to UV light through a photomask, which selectively hardens the areas of the mask that will remain on the board.
-
Developing: The unexposed areas of the solder mask are removed using a chemical developer, leaving only the hardened mask on the PCB.
-
Curing: The solder mask is then fully cured using heat or additional UV exposure to ensure its durability and adhesion to the board.
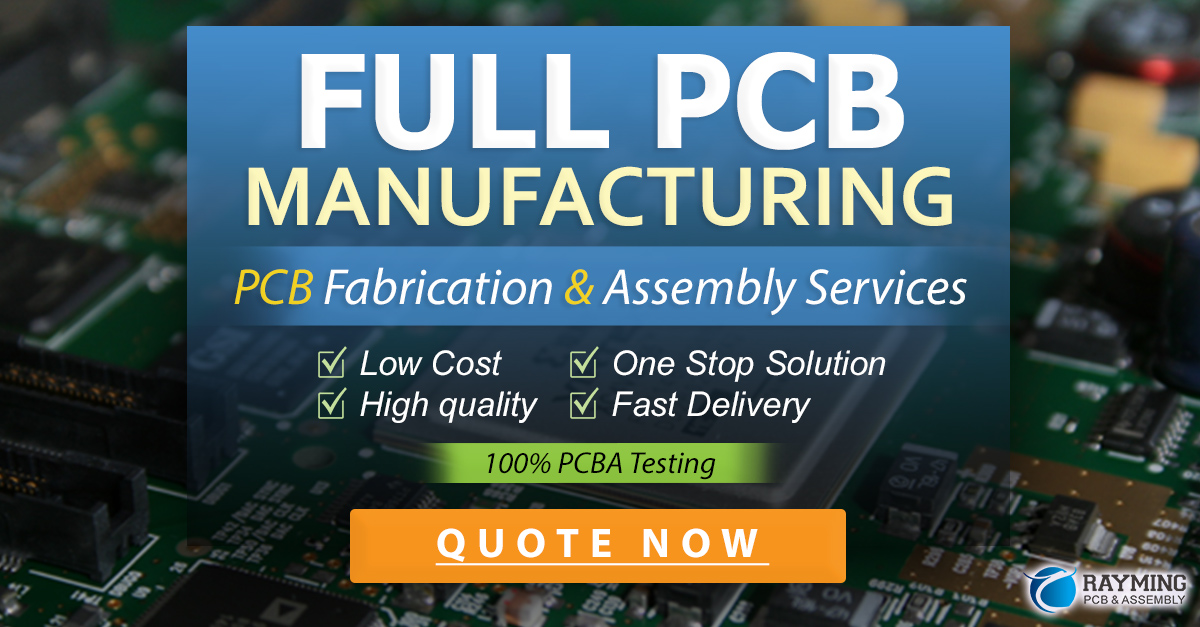
Types of Solder Mask
There are two main types of solder mask used in PCB manufacturing:
-
Liquid Photo Imageable (LPI) Solder Mask: LPI solder mask is applied as a liquid using a screen printing process. It is then exposed to UV light and developed, as described in the application process above. LPI solder mask is known for its excellent adhesion, durability, and resistance to chemicals and high temperatures.
-
Dry Film Solder Mask: Dry film solder mask is supplied as a solid film that is laminated onto the PCB. It is then exposed, developed, and cured in a similar manner to LPI solder mask. Dry film solder mask is often used for high-volume production due to its ease of application and consistency.
Solder Mask Colors
Solder mask is available in a variety of colors, with the most common being:
- Green
- Red
- Blue
- Black
- Yellow
- White
The choice of color is often a matter of personal preference or specific application requirements. For example, white solder mask is sometimes used for LED lighting applications to maximize light reflection, while black solder mask may be used for high-end audio equipment for its perceived aesthetic qualities.
Solder Mask Finish
The surface finish of the solder mask can also vary depending on the application and the desired properties of the PCB. The most common solder mask finishes are:
-
Glossy: A smooth, shiny surface that is easy to clean and provides good resistance to chemicals and moisture.
-
Matte: A non-reflective surface that reduces glare and provides a better surface for applying labels or markings.
-
Semi-Matte: A compromise between glossy and matte finishes, offering some of the benefits of both.
Solder Mask Design Considerations
When designing a PCB that will use solder mask, there are several key considerations to keep in mind:
-
Minimum Solder Mask Sliver: The minimum solder mask sliver refers to the smallest allowable gap between two openings in the solder mask. This is an important design parameter, as overly small slivers can lead to manufacturing defects or reduced insulation properties.
-
Solder Mask Expansion: Solder mask expansion refers to the amount by which the solder mask openings are enlarged compared to the copper pads beneath them. This expansion is necessary to account for any misalignment during the solder mask application process and to ensure that the copper pads are fully exposed for soldering.
-
Solder Mask Registration: Solder mask registration refers to the accuracy with which the solder mask openings are aligned with the copper pads. Poor registration can lead to issues such as partially covered pads or exposed copper traces.
-
Solder Mask Thickness: The thickness of the solder mask can impact its insulation properties and durability. Thicker solder mask provides better insulation and protection, but may also increase the cost and complexity of the manufacturing process.
Frequently Asked Questions (FAQ)
-
Q: Is solder mask required on all PCBs?
A: While solder mask is not strictly required on all PCBs, it is highly recommended for most applications due to its protective and insulating properties. Some very simple or low-cost PCBs may omit solder mask to reduce manufacturing costs, but this can compromise the reliability and longevity of the board. -
Q: Can solder mask be removed from a PCB?
A: Yes, solder mask can be removed from a PCB using abrasive methods such as sanding or scraping, or by using chemical solvents designed for this purpose. However, removing the solder mask can expose the underlying copper traces to oxidation and other damage, so it should only be done when absolutely necessary and with great care. -
Q: What is the difference between solder mask and conformal coating?
A: Solder mask and conformal coating are both protective layers applied to PCBs, but they serve different purposes. Solder mask is applied before the soldering process and is primarily intended to prevent solder bridges and protect against oxidation. Conformal coating, on the other hand, is applied after soldering and provides additional protection against moisture, dust, and other environmental factors. -
Q: Can solder mask be applied to both sides of a PCB?
A: Yes, solder mask can be applied to both sides of a PCB. This is common practice for double-sided boards, where components are soldered on both the top and bottom surfaces. In these cases, the solder mask helps to prevent solder bridges and provide insulation on both sides of the board. -
Q: How does solder mask affect the impedance of a PCB?
A: Solder mask can have a slight impact on the impedance of a PCB, as it acts as an additional dielectric layer between the copper traces and the environment. However, this impact is usually minimal and can be accounted for during the PCB design process by adjusting the width and spacing of the copper traces. In most cases, the benefits of using solder mask far outweigh any minor effects on impedance.
Conclusion
PCB solder mask is an essential component of modern PCB manufacturing, providing critical protection, insulation, and aesthetic benefits. By understanding the functions, types, and design considerations associated with solder mask, PCB designers and manufacturers can ensure the production of high-quality, reliable circuit boards that meet the demands of a wide range of applications.
As PCB technology continues to advance, innovations in solder mask materials and application processes will likely emerge, offering even greater protection and performance for the increasingly complex and sophisticated electronic devices of the future.
Leave a Reply