What is OSP Finish?
OSP finish is a chemical process that involves applying a thin, transparent layer of organic compounds to the exposed copper pads on a PCB. This layer acts as a barrier, preventing the copper from oxidizing and maintaining its solderability. The OSP coating is typically composed of benzimidazole derivatives, which form a complex with the copper surface.
How is OSP Applied?
The OSP application process usually follows these steps:
- Cleaning: The PCB is thoroughly cleaned to remove any contaminants or residues.
- Microetching: A mild etching solution is used to remove a thin layer of copper, ensuring a pristine surface for OSP application.
- OSP Application: The PCB is immersed in an OSP solution, which forms a protective layer on the copper pads.
- Drying: The PCB is then dried using hot air or infrared heating to evaporate any remaining solvents.
Advantages of OSP Finish
Cost-effective
One of the primary advantages of OSP finish is its cost-effectiveness compared to other surface finishes like ENIG (Electroless Nickel Immersion Gold) or HASL (Hot Air Solder Leveling). OSP application requires fewer processing steps and materials, resulting in lower production costs.
Flat Surface
OSP finish provides a flat, planar surface on the PCB, making it ideal for fine-pitch components and high-density designs. The flat surface ensures better contact between the component leads and the pads, improving solderability and reducing the risk of assembly defects.
Quick Turn-around
The OSP application process is relatively fast, allowing for shorter lead times in PCB fabrication. This is particularly advantageous for projects with tight deadlines or rapid prototyping requirements.
Environmentally Friendly
Unlike some other surface finishes, OSP is RoHS (Restriction of Hazardous Substances) compliant and does not contain harmful substances such as lead or heavy metals. This makes OSP an environmentally friendly choice for PCB manufacturing.
Disadvantages of OSP Finish
Limited Shelf Life
One of the main drawbacks of OSP finish is its limited shelf life. The organic compounds in the OSP coating can degrade over time, especially when exposed to high temperatures or humidity. This degradation can lead to reduced solderability and potential assembly issues.
Condition | Shelf Life |
---|---|
Room Temperature (20-25°C) | 6-12 months |
Elevated Temperature (30-35°C) | 3-6 months |
High Humidity (>60% RH) | 1-3 months |
To mitigate this issue, PCBs with OSP finish should be stored in a controlled environment and assembled within the recommended shelf life.
Sensitivity to Handling
OSP-coated PCBs are more sensitive to handling compared to other surface finishes. The organic layer can be easily contaminated by skin oils, dirt, or other substances, which can deteriorate its solderability. Proper handling procedures, such as wearing gloves and using clean tools, are essential to maintain the integrity of the OSP finish.
Difficulty in Visual Inspection
The transparent nature of the OSP coating makes visual inspection of the PCB more challenging. Unlike HASL or ENIG, which have distinct visual characteristics, OSP-coated pads may appear similar to bare copper. This can make it harder to detect soldering defects or assess the quality of the finish.
Limited Rework Capability
Reworking OSP-coated PCBs can be more difficult compared to other surface finishes. The OSP layer is typically removed during the rework process, exposing the bare copper pads. Reapplying OSP on a reworked PCB is not practical, so alternative surface finishes or additional protection methods may be necessary.
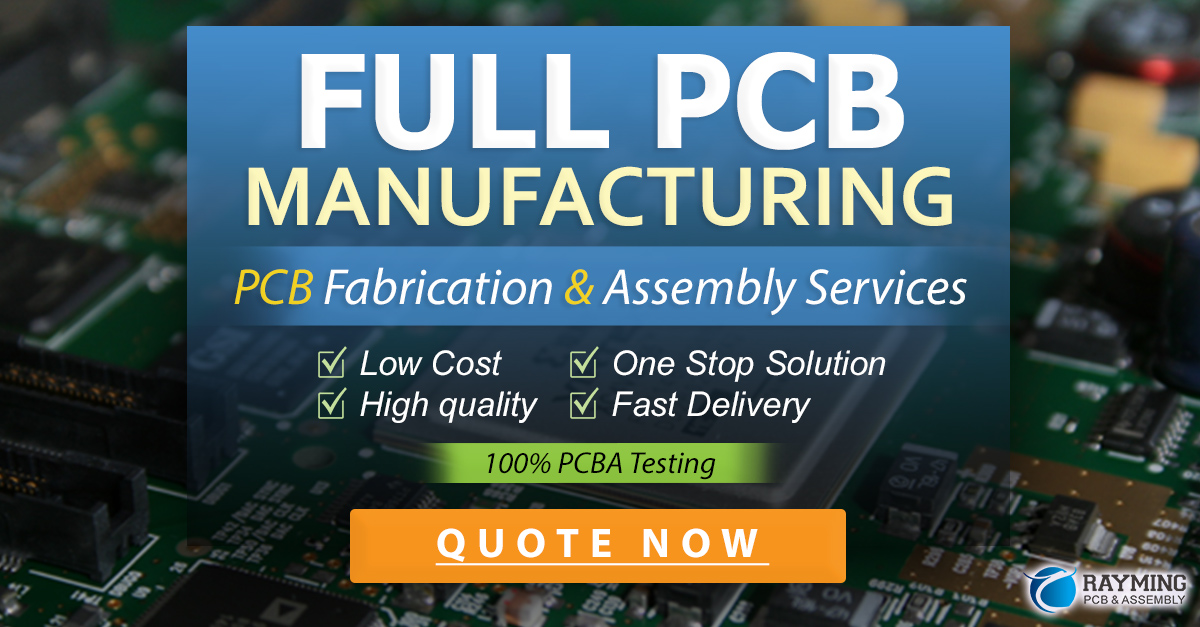
Frequently Asked Questions (FAQ)
1. Is OSP suitable for all types of PCBs?
OSP finish is generally suitable for most PCB applications, especially those with fine-pitch components and high-density designs. However, it may not be the best choice for PCBs that require a longer shelf life or will be exposed to harsh environmental conditions.
2. Can OSP be used for both leaded and lead-free soldering?
Yes, OSP finish is compatible with both leaded and lead-free soldering processes. The organic compounds in the OSP coating can withstand the higher temperatures required for lead-free soldering.
3. How does OSP compare to other surface finishes in terms of cost?
OSP is one of the most cost-effective surface finishes available. It is generally less expensive than ENIG, HASL, or immersion silver. The lower cost is attributed to the simpler application process and fewer materials required.
4. What is the typical thickness of an OSP coating?
The thickness of an OSP coating is typically very thin, ranging from 0.2 to 0.5 microns (μm). This thin layer is sufficient to protect the copper pads from oxidation while maintaining good solderability.
5. Can OSP be used for press-fit connections?
OSP finish is not recommended for press-fit connections due to its thin and relatively soft nature. Press-fit connections require a more robust surface finish, such as ENIG or hard gold plating, to withstand the mechanical forces involved in the press-fit process.
Conclusion
OSP finish is a popular choice for PCB surface protection due to its cost-effectiveness, flat surface, and environmental friendliness. However, its limited shelf life, sensitivity to handling, and difficulty in visual inspection should be considered when choosing a surface finish for a specific application.
By understanding the pros and cons of OSP-PCB“>OSP-PCB, designers and manufacturers can make informed decisions and take appropriate measures to ensure the reliability and quality of their PCB assemblies.
Leave a Reply