Introduction to Image Transfer in PCB Manufacturing
Image transfer is a critical process in the manufacturing of printed circuit boards (PCBs). It involves transferring the designed circuit pattern onto the copper-clad laminate, which serves as the foundation for the PCB. The accuracy and precision of the image transfer process directly impact the quality and functionality of the final PCB product.
In this article, we will delve into the various aspects of image transfer in PCB manufacturing, including the different methods used, the importance of proper image transfer, and the factors that influence the success of the process.
The Importance of Image Transfer in PCB Manufacturing
Image transfer plays a vital role in the PCB manufacturing process for several reasons:
-
Accuracy: The transferred image must accurately represent the designed circuit pattern to ensure proper connectivity and functionality of the PCB.
-
Precision: The image transfer process must maintain high precision to accommodate the increasingly smaller features and higher densities of modern PCB designs.
-
Consistency: The image transfer process must be consistent across multiple PCBs to ensure uniform quality and performance.
-
Reliability: Proper image transfer contributes to the overall reliability of the PCB by minimizing defects and ensuring the integrity of the circuit pattern.
Methods of Image Transfer in PCB Manufacturing
There are several methods used for image transfer in PCB manufacturing, each with its own advantages and limitations. The choice of method depends on factors such as the desired resolution, production volume, and cost considerations.
1. Screen Printing
Screen printing is a traditional method of image transfer that involves using a stencil (screen) to apply a thick layer of ink or paste onto the copper-clad laminate. The screen is made by stretching a fine mesh over a frame and creating a stencil of the circuit pattern on the mesh using a photosensitive emulsion.
Advantages:
– Cost-effective for high-volume production
– Suitable for simple circuit patterns
– Fast and efficient process
Limitations:
– Limited resolution compared to other methods
– Not suitable for complex or high-density designs
– Requires frequent maintenance and cleaning of screens
2. Photolithography
Photolithography, also known as optical lithography, is a high-resolution image transfer method that uses light to transfer the circuit pattern onto the copper-clad laminate. The process involves applying a photosensitive resist onto the laminate, exposing it to light through a photomask containing the circuit pattern, and then developing the resist to reveal the desired image.
Advantages:
– High resolution and precision
– Suitable for complex and high-density designs
– Consistent and repeatable results
Limitations:
– Higher cost compared to screen printing
– Requires specialized equipment and facilities
– Longer processing time
3. Direct Imaging (DI)
Direct imaging is a modern image transfer method that eliminates the need for a physical photomask. Instead, the circuit pattern is directly imaged onto the photoresist-coated laminate using a high-resolution laser or LED light source. The digital image data is used to control the light source, allowing for quick and accurate image transfer.
Advantages:
– Eliminates the need for physical photomasks
– High resolution and precision
– Fast and flexible process
– Suitable for quick turnaround and prototype production
Limitations:
– Higher equipment cost compared to traditional methods
– Requires specialized software and digital image processing
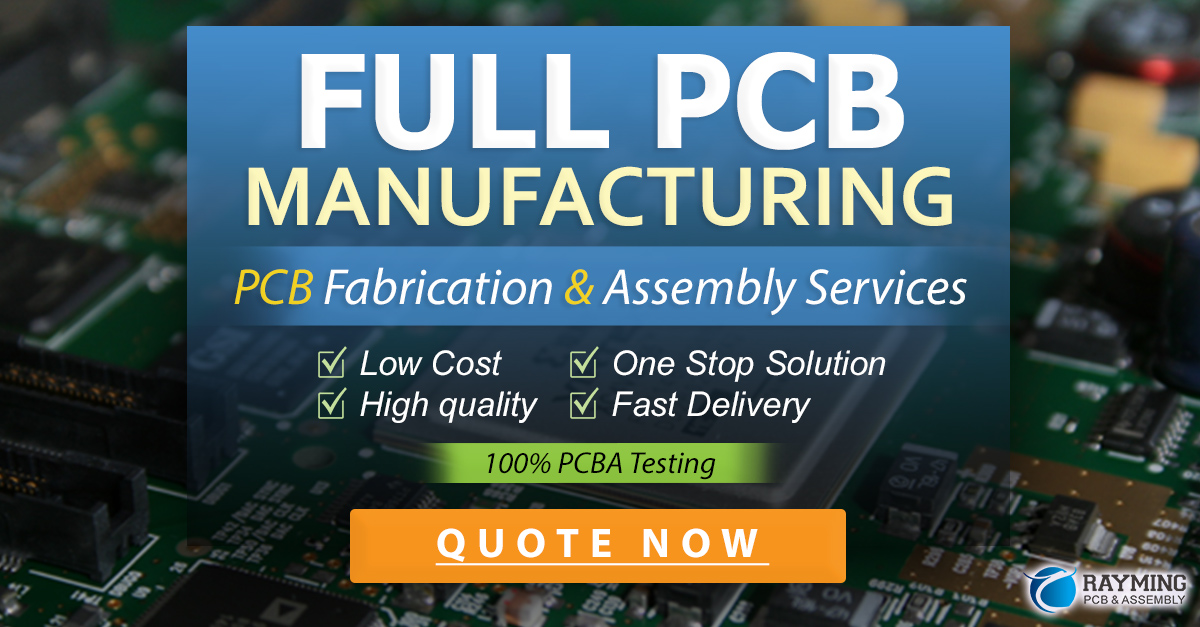
Factors Influencing Image Transfer Quality
Several factors can influence the quality and success of the image transfer process in PCB manufacturing:
-
Copper-clad laminate quality: The surface cleanliness, roughness, and consistency of the copper-clad laminate can affect the adhesion and uniformity of the applied photoresist or ink.
-
Photoresist or ink properties: The quality, consistency, and compatibility of the photoresist or ink with the chosen image transfer method can impact the resolution and accuracy of the transferred image.
-
Exposure and development conditions: The exposure time, light intensity, and development parameters must be carefully controlled to ensure proper image formation and minimize defects.
-
Equipment maintenance and calibration: Regular maintenance and calibration of the image transfer equipment are essential to maintain consistent performance and minimize process variations.
-
Environmental conditions: Temperature, humidity, and cleanliness of the production environment can affect the image transfer process and the quality of the resulting PCBs.
Image Transfer Defects and Their Causes
Despite the advancements in image transfer technology, various defects can still occur during the process. These defects can lead to reduced yields, increased production costs, and compromised PCB performance. Some common image transfer defects and their causes include:
-
Overexposure or underexposure: Incorrect exposure time or light intensity can result in overexposed or underexposed images, leading to poor line definition or incomplete image transfer.
-
Misalignment: Misalignment between the photomask and the copper-clad laminate can cause the transferred image to be shifted or distorted, affecting the connectivity and functionality of the PCB.
-
Pinholes or voids: Pinholes or voids in the transferred image can be caused by surface contamination, air bubbles, or non-uniform photoresist application, resulting in incomplete circuit patterns.
-
Edge roughness: Rough edges or poor line definition can occur due to factors such as insufficient resolution, poor photomask quality, or improper development conditions.
-
Undercutting or overdevelopment: Excessive development time or aggressive developer chemistry can lead to undercutting of the photoresist, resulting in widened or distorted circuit features.
Best Practices for Successful Image Transfer
To ensure successful image transfer and minimize defects, PCB manufacturers should follow these best practices:
-
Proper substrate preparation: Ensure that the copper-clad laminate is clean, dry, and free from surface contaminants before applying the photoresist or ink.
-
Consistent photoresist or ink application: Use automated coating equipment to apply a uniform and consistent layer of photoresist or ink onto the laminate.
-
Precise alignment: Employ alignment marks and vision systems to ensure accurate registration between the photomask and the laminate.
-
Optimal exposure and development: Determine the optimal exposure time, light intensity, and development parameters for the specific photoresist and image transfer method used.
-
Regular equipment maintenance: Perform regular maintenance, cleaning, and calibration of the image transfer equipment to ensure consistent performance and minimize process variations.
-
Environmental control: Maintain a clean, temperature-controlled, and humidity-controlled production environment to minimize the impact of environmental factors on the image transfer process.
-
Quality control and inspection: Implement robust quality control measures, including visual inspection, automated optical inspection (AOI), and electrical testing, to identify and address any image transfer defects early in the production process.
Future Trends in Image Transfer Technology
As PCB designs continue to evolve with smaller features, higher densities, and more complex layouts, image transfer technology must keep pace to meet the increasing demands. Some of the future trends in image transfer technology include:
-
Ultra-high resolution: The development of advanced photoresists and imaging systems that can achieve sub-micron resolution, enabling the fabrication of even smaller and more intricate circuit features.
-
Inkjet printing: The use of inkjet printing technology for image transfer, allowing for the direct deposition of conductive inks onto the substrate, eliminating the need for photoresists and etching processes.
-
3D printing: The integration of 3D printing technology with PCB manufacturing, enabling the creation of three-dimensional circuit structures and the embedding of electronic components within the PCB.
-
Artificial intelligence and machine learning: The application of AI and machine learning algorithms to optimize and control the image transfer process, enabling real-time process monitoring, defect detection, and adaptive process control.
Frequently Asked Questions (FAQ)
-
What is the most common method of image transfer in PCB manufacturing?
The most common method of image transfer in PCB manufacturing is photolithography, which offers high resolution, precision, and consistency for a wide range of PCB designs. -
How does the image transfer process affect the quality of the final PCB product?
The image transfer process directly impacts the quality of the final PCB product by determining the accuracy, precision, and consistency of the transferred circuit pattern. Poor image transfer can lead to defects, reduced yields, and compromised PCB performance. -
What are the advantages of direct imaging over traditional image transfer methods?
Direct imaging offers several advantages over traditional image transfer methods, including the elimination of physical photomasks, high resolution and precision, fast and flexible processing, and suitability for quick turnaround and prototype production. -
How can PCB manufacturers minimize image transfer defects?
PCB manufacturers can minimize image transfer defects by following best practices such as proper substrate preparation, consistent photoresist or ink application, precise alignment, optimal exposure and development, regular equipment maintenance, environmental control, and robust quality control measures. -
What are some of the future trends in image transfer technology for PCB manufacturing?
Some of the future trends in image transfer technology for PCB manufacturing include ultra-high resolution, inkjet printing, 3D printing, and the application of artificial intelligence and machine learning for process optimization and control.
Conclusion
Image transfer is a critical process in PCB manufacturing that directly impacts the quality, functionality, and reliability of the final PCB product. Understanding the various methods, factors, and best practices involved in image transfer is essential for PCB manufacturers to ensure successful and efficient production.
As PCB designs continue to evolve, image transfer technology must keep pace to meet the increasing demands for smaller features, higher densities, and more complex layouts. By staying informed about the latest trends and advancements in image transfer technology, PCB manufacturers can position themselves to deliver high-quality, reliable, and innovative PCB solutions to their customers.
Image Transfer Method | Advantages | Limitations |
---|---|---|
Screen Printing | – Cost-effective for high-volume production – Suitable for simple circuit patterns – Fast and efficient process |
– Limited resolution compared to other methods – Not suitable for complex or high-density designs – Requires frequent maintenance and cleaning of screens |
Photolithography | – High resolution and precision – Suitable for complex and high-density designs – Consistent and repeatable results |
– Higher cost compared to screen printing – Requires specialized equipment and facilities – Longer processing time |
Direct Imaging (DI) | – Eliminates the need for physical photomasks – High resolution and precision – Fast and flexible process – Suitable for quick turnaround and prototype production |
– Higher equipment cost compared to traditional methods – Requires specialized software and digital image processing |
Table 1: Comparison of common image transfer methods in PCB manufacturing
By understanding the strengths and limitations of each image transfer method, PCB manufacturers can make informed decisions when selecting the most appropriate technology for their specific production requirements and customer needs.
Leave a Reply