What is Electromechanical Assembly?
Electromechanical assembly refers to the process of combining electrical and mechanical components to create a functional system. This process involves the integration of various elements, such as printed circuit boards (PCBs), sensors, actuators, motors, and mechanical structures. The goal of electromechanical assembly is to ensure that all components work together seamlessly to achieve the desired functionality and performance.
Electromechanical assembly is used in a wide range of applications, including:
- Automotive systems (e.g., engine control units, sensors, and actuators)
- Medical devices (e.g., pacemakers, insulin pumps, and surgical robots)
- Industrial automation (e.g., programmable logic controllers, servo motors, and sensors)
- Consumer electronics (e.g., smartphones, wearables, and home appliances)
- Aerospace and defense systems (e.g., avionics, guidance systems, and communication devices)
Factors to Consider for Designing Electromechanical Assembly
1. Functionality and Performance Requirements
The first step in designing an electromechanical assembly is to clearly define the desired functionality and performance requirements. This involves understanding the specific tasks the system needs to perform, the operating conditions it will be subjected to, and the expected lifespan of the product. Some key questions to consider include:
- What are the primary functions of the system?
- What are the expected input and output parameters?
- What are the environmental conditions (e.g., temperature, humidity, vibration) the system will be exposed to?
- What are the power requirements and energy efficiency targets?
- What are the size and weight constraints?
By answering these questions, designers can establish a clear set of design goals and constraints, which will guide the selection of components and the overall system architecture.
2. Component Selection
Once the functionality and performance requirements are established, the next step is to select the appropriate components for the electromechanical assembly. This involves evaluating various options based on their technical specifications, cost, availability, and compatibility with other components. Some key considerations include:
- Electrical components:
- Microcontrollers or microprocessors
- Sensors (e.g., temperature, pressure, position)
- Actuators (e.g., motors, solenoids, piezoelectric devices)
- Power management components (e.g., voltage regulators, power converters)
-
Communication interfaces (e.g., USB, Ethernet, wireless)
-
Mechanical components:
- Enclosures and housings
- Connectors and fasteners
- Gears, bearings, and drive systems
- Heat sinks and cooling solutions
- Vibration and shock isolation
When selecting components, it is essential to consider their reliability, durability, and compliance with relevant industry standards and regulations.
3. Printed Circuit Board (PCB) Design
The PCB is the backbone of the electrical subsystem in an electromechanical assembly. It provides the interconnections between various electrical components and ensures proper signal integrity and power distribution. When designing a PCB for an electromechanical assembly, several factors need to be considered:
- Schematic design:
- Component selection and placement
- Power supply and grounding
- Signal integrity and electromagnetic compatibility (EMC)
-
Design for testability and manufacturability
-
PCB layout:
- Component placement and orientation
- Trace routing and impedance control
- Power and ground plane design
- Thermal management and heat dissipation
- Manufacturing considerations (e.g., minimum trace width, spacing, and hole sizes)
Proper PCB design is crucial for ensuring the reliability, performance, and cost-effectiveness of the electromechanical assembly.
4. Mechanical Design and Packaging
The mechanical design and packaging of an electromechanical assembly play a critical role in protecting the components, ensuring proper heat dissipation, and providing a user-friendly interface. Some key considerations include:
- Enclosure design:
- Material selection (e.g., plastic, metal, composite)
- Dimensional constraints and form factor
- Ingress protection (IP) rating for environmental sealing
-
Aesthetic and ergonomic considerations
-
Thermal management:
- Heat generation and dissipation analysis
- Selection of appropriate cooling methods (e.g., natural convection, forced air, liquid cooling)
-
Thermal interface materials and heat sinks
-
Mechanical stress and vibration:
- Structural analysis and finite element modeling (FEM)
- Selection of appropriate mounting and fastening methods
-
Vibration and shock isolation techniques
-
Assembly and manufacturing:
- Design for assembly (DFA) principles
- Tolerance analysis and stack-up management
- Selection of appropriate joining methods (e.g., screws, snap-fits, adhesives)
Effective mechanical design and packaging ensure that the electromechanical assembly can withstand the intended operating conditions and provide a reliable and user-friendly product.
5. Integration and Testing
Once the electrical and mechanical subsystems have been designed, the next step is to integrate them into a complete electromechanical assembly. This involves careful planning and execution to ensure proper fit, function, and performance. Some key considerations include:
- Assembly sequence and process:
- Defining the optimal assembly order and steps
- Identifying potential challenges and bottlenecks
-
Developing assembly fixtures and jigs
-
Interconnections and interfaces:
- Ensuring proper mating of electrical and mechanical components
- Verifying signal integrity and power transmission
-
Testing for continuity and insulation resistance
-
Functional testing and validation:
- Developing comprehensive test plans and procedures
- Performing functional tests under various operating conditions
- Conducting environmental and durability testing
- Validating system performance against design requirements
Thorough integration and testing help identify and resolve any issues early in the development process, reducing the risk of costly redesigns and delays.
6. Manufacturing and Supply Chain Management
Designing an electromechanical assembly is not complete without considering the manufacturing and supply chain aspects. Some key factors to consider include:
- Manufacturing processes:
- Selecting appropriate fabrication methods (e.g., injection molding, CNC machining, 3D printing)
- Defining assembly processes and sequences
-
Establishing quality control and inspection procedures
-
Supply chain management:
- Identifying and qualifying suppliers for components and materials
- Managing lead times and inventory levels
-
Ensuring compliance with regulations and standards (e.g., RoHS, REACH, UL)
-
Cost optimization:
- Conducting design for manufacturing (DFM) analysis
- Identifying opportunities for part consolidation and standardization
- Negotiating pricing and terms with suppliers
Effective manufacturing and supply chain management help ensure the timely and cost-effective production of the electromechanical assembly.
Frequently Asked Questions (FAQ)
-
What is the difference between electromechanical assembly and electronic assembly?
Electromechanical assembly involves the integration of both electrical and mechanical components, while electronic assembly focuses primarily on the assembly of electronic components onto PCBs. -
What are some common challenges in Electromechanical assembly design?
Some common challenges include ensuring proper signal integrity, managing thermal dissipation, dealing with mechanical stress and vibration, and optimizing the assembly process for manufacturability and cost-effectiveness. -
What software tools are used for electromechanical assembly design?
Various software tools are used, including electronic design automation (EDA) tools for PCB design, mechanical CAD (MCAD) tools for 3D modeling and simulation, and product lifecycle management (PLM) tools for data management and collaboration. -
How can I ensure the reliability of my electromechanical assembly?
To ensure reliability, consider factors such as component selection, thermal management, vibration isolation, and thorough testing and validation. Adhering to industry standards and best practices can also help improve reliability. -
What are some best practices for managing the supply chain for electromechanical assemblies?
Best practices include identifying and qualifying multiple suppliers, establishing long-term relationships, managing inventory levels, and ensuring compliance with relevant regulations and standards. Regularly monitoring supplier performance and conducting audits can also help maintain a robust supply chain.
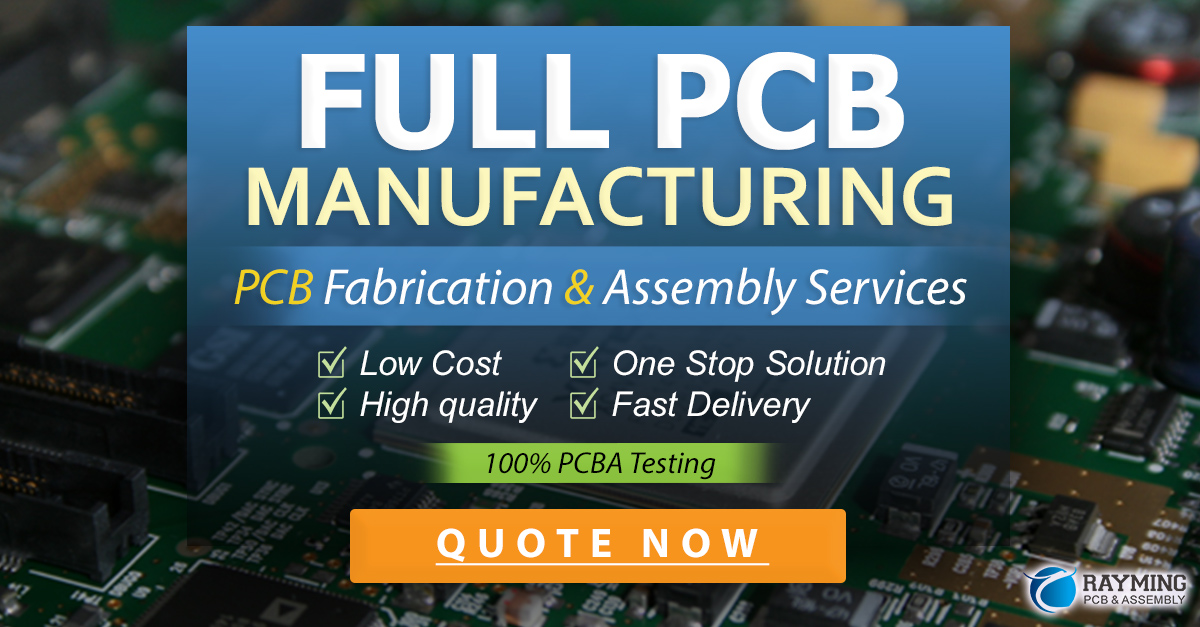
Conclusion
Electromechanical assembly design is a complex and multidisciplinary process that requires careful consideration of various factors, including functionality, component selection, PCB design, mechanical design, integration, testing, and manufacturing. By understanding these factors and following best practices, designers can create reliable, high-performance, and cost-effective electromechanical systems for a wide range of applications.
As technology continues to advance, the importance of electromechanical assembly design will only continue to grow. By staying up-to-date with the latest trends, tools, and techniques, designers can position themselves to tackle the challenges and opportunities presented by this dynamic field.
Leave a Reply