Introduction to Bill of Materials (BOM)
A Bill of Materials (BOM) is a comprehensive list of all the components, parts, and materials required to manufacture a product or complete a project. It serves as a crucial document that provides a detailed breakdown of the product structure, including the quantities, descriptions, and specifications of each item needed. The BOM is an essential tool for various departments within an organization, such as engineering, procurement, production, and inventory management.
Key Components of a Bill of Materials
A typical BOM includes the following key components:
- Part Number: A unique identifier for each component or subassembly.
- Part Name: A brief description of the part or component.
- Quantity: The number of units required for each component.
- Unit of Measure: The standard unit used to measure the quantity of each component (e.g., pieces, liters, kilograms).
- Description: A detailed description of the part, including specifications, materials, and dimensions.
- Level: The hierarchical level of the component within the product structure.
- Reference Designators: Specific labels or codes that indicate the location or function of the component within the product.
Types of Bill of Materials
There are several types of BOMs, each serving a specific purpose within the product development and manufacturing process. Some common types include:
1. Engineering Bill of Materials (EBOM)
An Engineering BOM (EBOM) is created by the engineering department and focuses on the product design aspect. It includes all the components and subassemblies required to build the product as designed. The EBOM is typically used for product development, prototyping, and testing.
2. Manufacturing Bill of Materials (MBOM)
A Manufacturing BOM (MBOM) is derived from the EBOM and is tailored for the production process. It includes all the components and materials needed to manufacture the product on the factory floor. The MBOM may differ from the EBOM due to factors such as packaging requirements, assembly instructions, and manufacturing constraints.
3. Sales Bill of Materials (SBOM)
A Sales BOM (SBOM) is created for the purpose of sales and customer communication. It includes the finished product and any optional or configurable components that can be sold separately. The SBOM is used to generate quotes, process orders, and manage inventory for finished goods.
4. Service Bill of Materials (SBOM)
A Service BOM (SBOM) is used for after-sales support and maintenance. It includes all the components, spare parts, and consumables required to service or repair the product. The SBOM is essential for managing service inventory and ensuring timely maintenance and repair operations.
Importance of Bill of Materials in Manufacturing
The Bill of Materials plays a vital role in various aspects of manufacturing, including:
1. Production Planning
The BOM provides a clear and detailed list of all the components required to manufacture a product. This information is crucial for production planning, as it helps in determining the lead times, production schedules, and capacity requirements. By analyzing the BOM, manufacturers can optimize their production processes, minimize delays, and ensure timely delivery of products.
2. Inventory Management
An accurate BOM helps in effective inventory management by providing a complete list of all the components and their quantities needed for production. This information enables manufacturers to maintain optimal inventory levels, avoid stockouts, and reduce the risk of obsolete inventory. By tracking inventory levels against the BOM, companies can make informed decisions regarding purchasing, storage, and distribution of materials.
3. Cost Control
The BOM is a valuable tool for cost control in manufacturing. By providing a detailed breakdown of all the components and their quantities, the BOM enables accurate cost estimation and analysis. Manufacturers can use this information to identify cost-saving opportunities, negotiate better prices with suppliers, and optimize their procurement processes. The BOM also helps in tracking and controlling the actual costs incurred during production, allowing for better financial management.
4. Quality Assurance
The BOM serves as a reference document for quality assurance purposes. It specifies the exact components, materials, and specifications required to manufacture a product that meets the desired quality standards. By adhering to the BOM during production, manufacturers can ensure consistency in product quality and minimize the risk of defects or variations. The BOM also facilitates traceability, allowing manufacturers to track the source of components and identify potential quality issues.
5. Collaboration and Communication
The BOM is a central document that facilitates collaboration and communication among various departments within an organization. It serves as a common language that enables cross-functional teams, such as engineering, procurement, production, and quality control, to work together effectively. The BOM provides a clear understanding of the product structure, dependencies, and requirements, reducing the chances of miscommunication and errors.
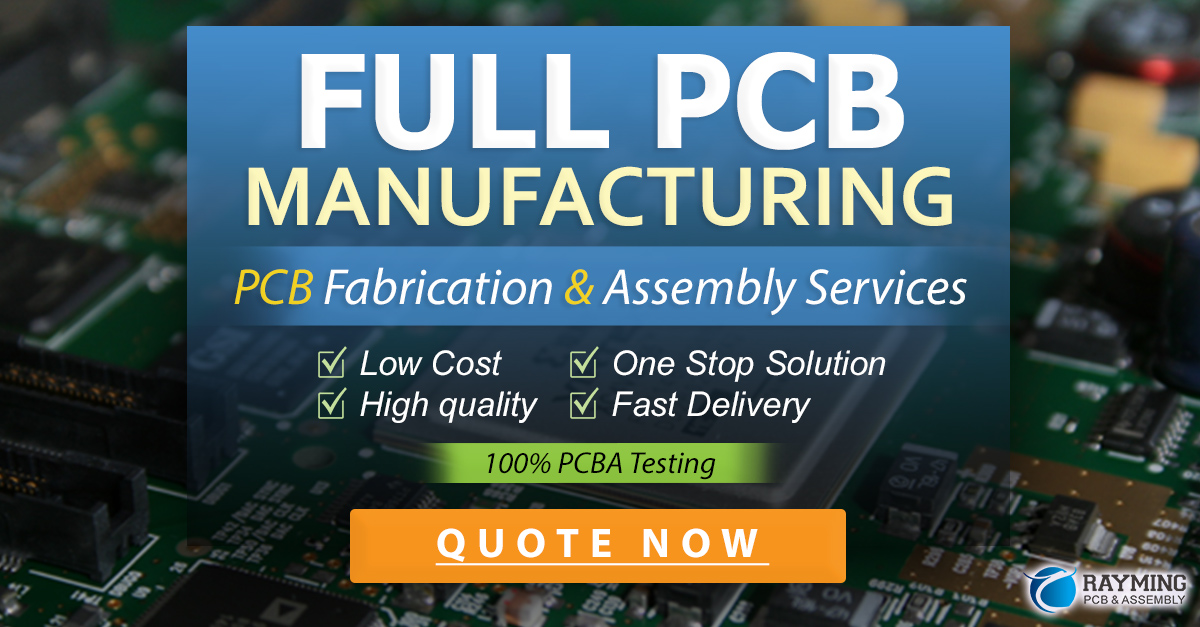
Creating a Bill of Materials
Creating a comprehensive and accurate BOM is essential for efficient manufacturing operations. The following steps outline the general process of creating a BOM:
1. Product Design and Engineering
The process begins with the product design and engineering phase. The engineering team develops the product concept, creates detailed designs, and specifies the required components and materials. This information forms the basis of the Engineering BOM (EBOM).
2. BOM Structure and Hierarchy
The next step is to define the BOM structure and hierarchy. This involves organizing the components and subassemblies into a logical and structured format. The BOM hierarchy typically starts with the finished product at the top level and then breaks down into subassemblies, components, and raw materials at lower levels.
3. Part Numbering and Naming Conventions
Each component and subassembly in the BOM should be assigned a unique part number and name. Consistent numbering and naming conventions should be used to ensure clarity and avoid confusion. Part numbers can be sequential, meaningful, or a combination of both, depending on the company’s practices.
4. Quantity and Unit of Measure
For each component in the BOM, the required quantity and unit of measure should be specified. The quantity indicates the number of units needed for a single unit of the finished product. The unit of measure should be clearly defined, such as pieces, liters, or kilograms, to ensure accurate inventory management and procurement.
5. Description and Specifications
A detailed description and specification should be provided for each component in the BOM. This includes information such as dimensions, materials, tolerances, and any other relevant technical details. The description should be clear and concise, enabling easy identification and understanding of the component.
6. Reference Designators
Reference designators are labels or codes assigned to each component in the BOM to indicate its location or function within the product. These designators are typically used in conjunction with the product’s schematic diagram or assembly drawing. They help in identifying and tracking components during the manufacturing and assembly process.
7. Revisions and Updates
As the product design evolves or changes are made, the BOM should be revised and updated accordingly. Each revision should be clearly indicated with a revision number or date, and the changes should be communicated to all relevant stakeholders. Proper version control and documentation of revisions are essential to maintain the accuracy and integrity of the BOM.
BOM Example and Template
To provide a clearer understanding of a Bill of Materials, let’s consider an example of a simple product and its corresponding BOM. The product in this example is a basic desk lamp.
Desk Lamp BOM Example
Level | Part Number | Part Name | Quantity | Unit of Measure | Description |
---|---|---|---|---|---|
0 | DL-001 | Desk Lamp Assembly | 1 | Each | Complete desk lamp assembly |
1 | DL-002 | Lamp Base | 1 | Each | Plastic base, black, 150mm diameter |
1 | DL-003 | Lamp Neck | 1 | Each | Adjustable metal neck, chrome finish |
1 | DL-004 | Lamp Shade | 1 | Each | Fabric shade, white, 200mm diameter |
1 | DL-005 | Light Bulb Socket | 1 | Each | E26 socket, ceramic, max 60W |
1 | DL-006 | Power Cord | 1 | Each | 6ft, 18AWG, black, with plug |
1 | DL-007 | On/Off Switch | 1 | Each | Rocker switch, 125V/3A, black |
2 | DL-008 | Screw, M3x10mm | 4 | Each | Machine screw, M3 thread, 10mm length |
2 | DL-009 | Nut, M3 | 4 | Each | Hex nut, M3 thread, zinc plated |
This BOM example shows the hierarchical structure of the desk lamp, with the top-level assembly (Level 0) and its components (Level 1 and 2). Each component is assigned a unique part number, name, quantity, unit of measure, and description. The BOM provides a clear and organized list of all the components required to manufacture the desk lamp.
To help you create your own BOM, we have provided a downloadable BOM template in Microsoft Excel format. Download BOM Template
Frequently Asked Questions (FAQ)
- What is the difference between an Engineering BOM and a Manufacturing BOM?
-
An Engineering BOM (EBOM) focuses on the product design and includes all the components and subassemblies required to build the product as designed. A Manufacturing BOM (MBOM) is derived from the EBOM and is tailored for the production process, including components, materials, and packaging required for manufacturing.
-
How do I assign part numbers in a BOM?
-
Part numbers can be assigned using various methods, such as sequential numbering, meaningful codes, or a combination of both. The key is to use a consistent and clear numbering system that allows for easy identification and tracking of components.
-
What is the purpose of reference designators in a BOM?
-
Reference designators are labels or codes assigned to each component in the BOM to indicate its location or function within the product. They help in identifying and tracking components during the manufacturing and assembly process, especially when used in conjunction with the product’s schematic diagram or assembly drawing.
-
How often should I update my BOM?
-
The BOM should be updated whenever there are changes to the product design, components, or specifications. It is essential to maintain an up-to-date BOM to ensure accurate production planning, inventory management, and quality control.
-
Can I use the same BOM for different product variations?
- If the product variations have significant differences in components or structure, it is recommended to create separate BOMs for each variation. However, if the variations are minor and share a large portion of common components, you can use a single BOM with notes or options to indicate the differences.
Conclusion
A Bill of Materials (BOM) is a critical document in the manufacturing process that provides a comprehensive list of all the components, parts, and materials required to produce a product. It serves as a foundation for various functions, including production planning, inventory management, cost control, quality assurance, and collaboration among cross-functional teams.
Creating an accurate and detailed BOM involves a systematic process, starting from product design and engineering, defining the BOM structure and hierarchy, assigning part numbers and descriptions, specifying quantities and units of measure, and maintaining revisions and updates.
By understanding the importance of a BOM and following best practices in its creation and management, manufacturers can streamline their operations, improve efficiency, and ensure the production of high-quality products.
Remember, a well-structured and maintained BOM is not just a list of components; it is a powerful tool that enables effective communication, collaboration, and decision-making throughout the manufacturing process.
Leave a Reply