Understanding BGA Packages
Before we dive into the reballing process, it’s essential to understand what a BGA package is. A BGA is a type of surface-mount packaging used for integrated circuits (ICs). It consists of a rectangular or square package with a grid of solder balls on the bottom. These solder balls are used to connect the IC to the printed circuit board (PCB).
BGA packages offer several advantages over other types of IC packaging:
- Higher pin density: BGA packages can accommodate a large number of pins in a small area, making them suitable for complex ICs.
- Better thermal and electrical performance: The solder balls provide a low-resistance path for heat dissipation and electrical signals.
- Reduced package size: BGA packages have a smaller footprint compared to other types of packaging, allowing for more compact designs.
However, BGA packages also have some disadvantages:
- Difficulty in inspection: Since the solder connections are hidden under the package, it’s challenging to visually inspect them for defects.
- Complexity in repair: Replacing or repairing a BGA package requires specialized equipment and expertise.
Reasons for BGA Reballing
There are several reasons why BGA reballing may be necessary:
- Manufacturing defects: During the manufacturing process, issues such as poor soldering, misalignment, or contamination can lead to defective solder connections.
- Wear and tear: Over time, the solder balls can degrade due to thermal stress, vibration, or mechanical shock, resulting in intermittent or complete failure of the device.
- Upgrading or modifying: In some cases, reballing may be performed to upgrade or modify the IC package to improve performance or add new features.
The BGA Reballing Process
The BGA reballing process involves several steps, each requiring precision and care to ensure a successful outcome.
Step 1: Removal of the Old Solder Balls
The first step in reballing is to remove the old solder balls from the BGA package. This is typically done using a specialized tool called a BGA Rework station. The rework station heats the package to a specific temperature, causing the solder balls to melt. The package is then carefully lifted off the PCB, leaving the solder balls behind.
Step 2: Cleaning the BGA Package
After removing the old solder balls, the BGA package needs to be cleaned to remove any residual solder or contaminants. This is usually done using a solvent and a soft brush. It’s crucial to ensure that the package is thoroughly cleaned to prevent any issues during the reballing process.
Step 3: Applying Flux
Next, a thin layer of flux is applied to the bottom of the BGA package. Flux is a chemical compound that helps to improve the flow of solder and prevent oxidation during the soldering process. The type of flux used depends on the specific application and the type of solder being used.
Step 4: Placing the New Solder Balls
Once the flux has been applied, the new solder balls are placed onto the BGA package. This is typically done using a stencil or a template that matches the pattern of the solder balls on the package. The solder balls are carefully aligned with the pads on the package to ensure proper connection.
Step 5: Reflowing the Solder Balls
After the new solder balls have been placed, the package is heated again using the BGA rework station. This process, known as reflowing, melts the solder balls and bonds them to the pads on the package. The temperature and duration of the reflow process must be carefully controlled to ensure a strong and reliable connection.
Step 6: Inspection and Testing
Finally, the reballed BGA package is inspected and tested to ensure that all connections are properly formed and functioning. This may involve visual inspection under a microscope, X-ray imaging, or electrical testing using specialized equipment.
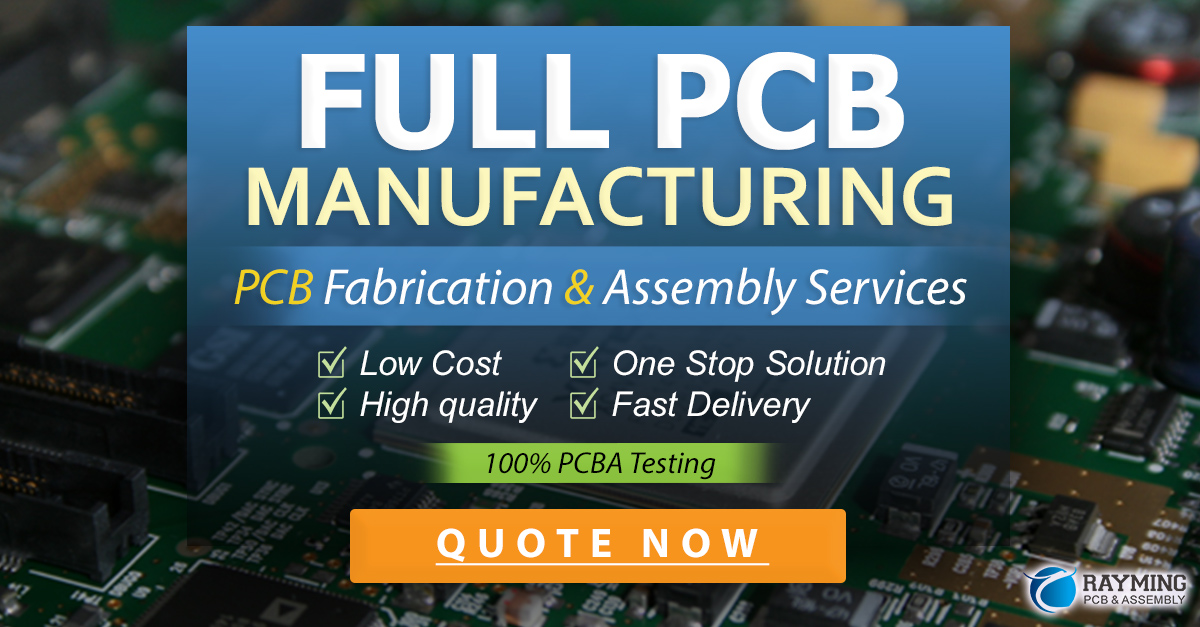
Tools and Equipment for BGA Reballing
BGA reballing requires specialized tools and equipment to ensure a successful outcome. Some of the essential tools and equipment include:
- BGA rework station: A specialized machine that provides precise temperature control and alignment for removing and replacing BGA packages.
- Soldering iron: A tool used for melting and applying solder to the BGA package.
- Solder balls: The small, spherical pieces of solder that are used to replace the old solder balls on the BGA package.
- Flux: A chemical compound used to improve the flow of solder and prevent oxidation during the soldering process.
- Stencils and templates: Used for placing the new solder balls onto the BGA package in the correct pattern.
- Microscope: Used for visual inspection of the BGA package and solder connections.
- X-ray machine: Used for non-destructive inspection of the internal solder connections.
Tool/Equipment | Purpose |
---|---|
BGA rework station | Provides precise temperature control and alignment for removing and replacing BGA packages |
Soldering iron | Used for melting and applying solder to the BGA package |
Solder balls | Small, spherical pieces of solder used to replace the old solder balls on the BGA package |
Flux | A chemical compound used to improve the flow of solder and prevent oxidation during the soldering process |
Stencils and templates | Used for placing the new solder balls onto the BGA package in the correct pattern |
Microscope | Used for visual inspection of the BGA package and solder connections |
X-ray machine | Used for non-destructive inspection of the internal solder connections |
Challenges in BGA Reballing
While BGA reballing is a critical process in electronics repair and manufacturing, it also presents several challenges:
- Precision and accuracy: BGA reballing requires a high level of precision and accuracy to ensure proper alignment and connection of the solder balls. Even a small misalignment can lead to device failure.
- Thermal management: Controlling the temperature during the reflow process is crucial to avoid damaging the BGA package or the PCB. Overheating can cause warping or delamination, while underheating can result in weak or incomplete solder connections.
- Contamination: Any contaminants, such as dust or oxidation, can interfere with the solder flow and cause defects in the connections. Maintaining a clean work environment and using proper cleaning techniques is essential.
- Training and skill: BGA reballing requires specialized knowledge and skills. Technicians must be properly trained and experienced to ensure a successful outcome.
Benefits of BGA Reballing
Despite the challenges, BGA reballing offers several benefits:
- Cost-effective repair: In many cases, reballing a BGA package is more cost-effective than replacing the entire PCB or device.
- Improved reliability: When done correctly, BGA reballing can restore the device to its original functionality and improve its reliability.
- Extended device lifespan: By replacing worn-out or damaged solder connections, BGA reballing can extend the lifespan of the device.
- Reduced environmental impact: Reballing allows for the repair and reuse of electronic devices, reducing the amount of electronic waste that ends up in landfills.
Frequently Asked Questions (FAQ)
1. What is the difference between BGA reballing and rework?
BGA reballing specifically refers to the process of replacing the solder balls on a BGA package. BGA rework, on the other hand, is a broader term that encompasses the entire process of removing and replacing a BGA package, including reballing.
2. Can BGA reballing be done at home?
While it is possible to perform BGA reballing at home with the right tools and equipment, it is not recommended for individuals without proper training and experience. BGA reballing requires specialized knowledge and skills to ensure a successful outcome and avoid damaging the device.
3. How much does BGA reballing cost?
The cost of BGA reballing varies depending on several factors, such as the size and complexity of the BGA package, the type of device, and the service provider. On average, BGA reballing can cost anywhere from $50 to $200 or more.
4. How long does BGA reballing take?
The duration of the BGA reballing process depends on the complexity of the job and the experience of the technician. On average, a simple reballing job can take anywhere from 30 minutes to an hour, while more complex jobs can take several hours or even days.
5. What are the risks of BGA reballing?
BGA reballing is a complex process that requires precision and care. If not done correctly, it can lead to several risks, such as:
- Damage to the BGA package or PCB
- Weak or incomplete solder connections
- Short circuits or other electrical issues
- Reduced device performance or reliability
To minimize these risks, it’s essential to choose a reputable and experienced service provider and follow proper procedures and guidelines.
Conclusion
BGA reballing is a critical process in electronics repair and manufacturing that involves replacing the solder balls on a BGA package. It requires specialized tools, equipment, and expertise to ensure a successful outcome. While BGA reballing presents several challenges, it also offers numerous benefits, such as cost-effective repair, improved reliability, and extended device lifespan.
As electronics continue to evolve and become more complex, the importance of BGA reballing will only continue to grow. By understanding the process, challenges, and benefits of BGA reballing, electronics professionals can make informed decisions and ensure the longevity and reliability of their devices.
Leave a Reply