Introduction to Heat Sink PCBs
In the world of electronics, heat management is a crucial factor in ensuring the optimal performance and longevity of devices. As electronic components become more compact and powerful, the need for efficient heat dissipation solutions has become increasingly important. This is where Heat Sink Printed Circuit Boards (PCBs) come into play. Heat Sink PCBs are specially designed circuit boards that incorporate heat sinking capabilities to effectively remove heat from critical components, preventing overheating and ensuring reliable operation.
What is a Heat Sink PCB?
A Heat Sink PCB is a type of printed circuit board that integrates heat sinking features directly into its design. Unlike traditional PCBs, which primarily focus on electrical connectivity, Heat Sink PCBs prioritize thermal management. These boards are engineered to efficiently transfer heat away from heat-generating components, such as high-power processors, power modules, and other heat-sensitive devices.
Key Features of Heat Sink PCBs
-
Thermal Conductivity: Heat Sink PCBs are manufactured using materials with high thermal conductivity, such as copper or aluminum. These materials facilitate the rapid transfer of heat from the components to the heat sink, allowing for effective heat dissipation.
-
Increased Copper Thickness: Heat Sink PCBs often feature thicker copper layers compared to standard PCBs. The increased copper thickness enhances the board’s ability to conduct heat, providing a larger cross-sectional area for heat transfer.
-
Thermal Vias: Heat Sink PCBs incorporate thermal vias, which are small, conductive holes drilled through the board. These vias create a thermal path between the heat-generating components and the heat sink, allowing heat to be efficiently transferred away from the components.
-
Heat Sink Attachment: Heat Sink PCBs are designed to accommodate the attachment of external heat sinks. The board may include dedicated mounting points or thermal pads that facilitate the secure and thermally efficient connection between the PCB and the heat sink.
Importance of Heat Sink PCBs in the Electrical Industry
Thermal Management
The primary importance of Heat Sink PCBs lies in their ability to effectively manage heat generated by electronic components. As electronic devices become more compact and powerful, the heat generated by components can reach critical levels. Overheating can lead to performance degradation, reduced reliability, and even permanent damage to the components. Heat Sink PCBs address this challenge by providing an efficient means of heat dissipation, ensuring that components operate within their safe temperature range.
Reliability and Longevity
By effectively managing heat, Heat Sink PCBs contribute to the overall reliability and longevity of electronic devices. When components are subjected to excessive heat, their lifespan can be significantly reduced. Heat-related stress can cause material degradation, solder joint failures, and other reliability issues. By maintaining a stable and controlled thermal environment, Heat Sink PCBs help prevent premature component failure and extend the operational life of electronic devices.
High-Power Applications
Heat Sink PCBs are particularly crucial in high-power applications, such as power electronics, automotive systems, and industrial control devices. These applications often involve components that generate substantial amounts of heat, such as power transistors, rectifiers, and voltage regulators. Heat Sink PCBs provide the necessary thermal management solution to ensure that these components can operate reliably and efficiently, even under demanding conditions.
Space Optimization
In modern electronics, space is often at a premium. Designers strive to create compact and highly integrated systems to meet consumer demands for smaller, lighter, and more portable devices. Heat Sink PCBs enable designers to optimize space utilization by integrating heat sinking capabilities directly into the PCB. This eliminates the need for separate heat sinks or additional thermal management components, resulting in more compact and streamlined designs.
Cost Reduction
Implementing Heat Sink PCBs can lead to cost savings in the long run. By effectively managing heat and improving the reliability of electronic devices, Heat Sink PCBs can reduce the occurrence of heat-related failures and minimize the need for repairs or replacements. This translates to lower maintenance costs and improved overall system reliability. Additionally, the integration of heat sinking features into the PCB itself can simplify the manufacturing process and reduce assembly costs compared to using separate heat sinks.
Design Considerations for Heat Sink PCBs
Thermal Analysis
Designing a Heat Sink PCB requires careful thermal analysis to ensure optimal heat dissipation. Designers must consider factors such as component power dissipation, thermal resistance, and heat flow paths. Thermal simulation software is often used to model and analyze the thermal behavior of the PCB, helping designers optimize the placement of components and heat sinking features.
Material Selection
The choice of materials is crucial in Heat Sink PCB design. The PCB substrate and copper layers should have high thermal conductivity to facilitate efficient heat transfer. Common materials used in Heat Sink PCBs include:
- FR-4: A glass-reinforced epoxy laminate that offers good thermal conductivity and is widely used in PCB manufacturing.
- Metal Core PCBs (MCPCBs): PCBs with a metal core, such as aluminum or copper, that provide excellent thermal conductivity and heat spreading capabilities.
- Ceramic Substrates: High-performance ceramic materials, such as aluminum nitride (AlN) or beryllium oxide (BeO), that offer exceptional thermal conductivity and electrical insulation properties.
Copper Thickness and Trace Routing
The thickness of the copper layers and the routing of traces on a Heat Sink PCB play a significant role in its thermal performance. Thicker copper layers provide a larger cross-sectional area for heat conduction, allowing for more efficient heat transfer. Trace routing should be optimized to minimize thermal resistance and ensure adequate heat flow from the components to the heat sink.
Thermal Vias and Heat Spreading
Thermal vias are essential for transferring heat from the components to the heat sink. The number, size, and placement of thermal vias should be carefully considered to maximize heat transfer efficiency. Heat spreading techniques, such as using thermal pads or heat spreaders, can also be employed to distribute heat evenly across the PCB and improve overall thermal performance.
Integration with External Heat Sinks
Heat Sink PCBs are often used in conjunction with external heat sinks to further enhance heat dissipation. The PCB should be designed to accommodate the attachment of heat sinks, whether through direct contact or using thermal interface materials. Proper mounting and thermal interface selection are crucial to ensure efficient heat transfer between the PCB and the heat sink.
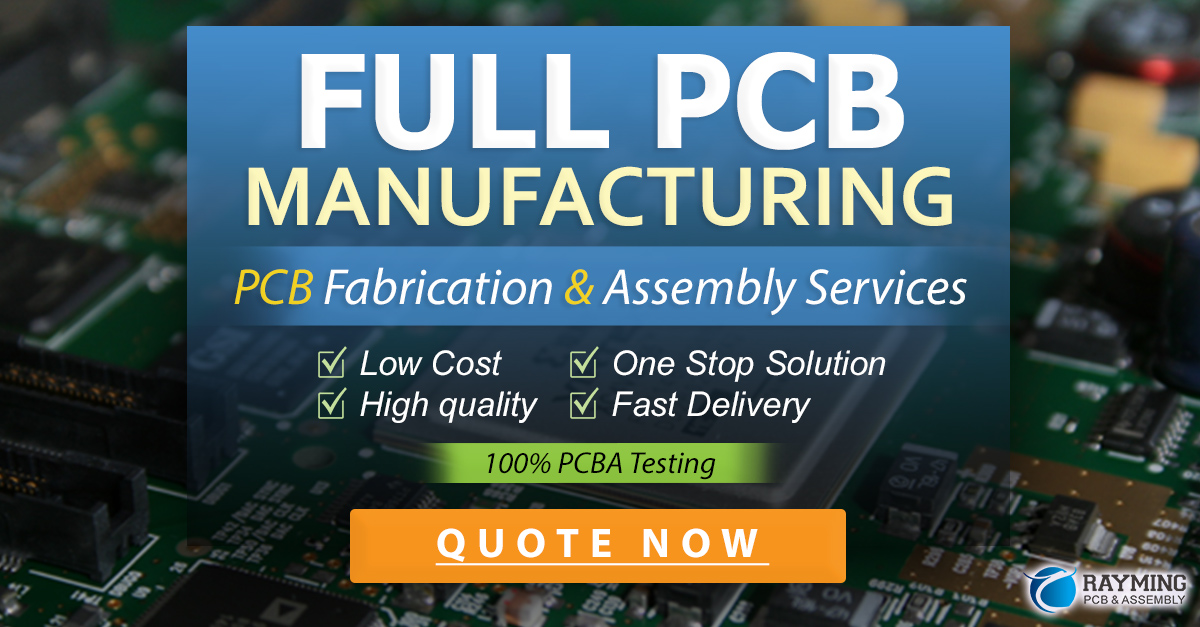
Applications of Heat Sink PCBs
Heat Sink PCBs find applications in various industries and sectors where thermal management is critical. Some common applications include:
-
Power Electronics: Heat Sink PCBs are extensively used in power electronic devices, such as power supplies, inverters, and motor drives. These applications involve high-power components that generate significant heat, making efficient thermal management essential.
-
Automotive Electronics: In the automotive industry, Heat Sink PCBs are used in engine control units (ECUs), power steering systems, and other electronic modules. The harsh operating environment and stringent reliability requirements in automotive applications necessitate robust thermal management solutions.
-
Industrial Control Systems: Heat Sink PCBs are employed in industrial control systems, such as programmable logic controllers (PLCs), servo drives, and motion control devices. These systems often operate in demanding environments and require reliable thermal management to ensure continuous operation.
-
Telecommunications: In the telecommunications industry, Heat Sink PCBs are used in base stations, routers, and other network equipment. The high-density packaging and high-speed data processing in these devices generate substantial heat, making efficient heat dissipation crucial.
-
Consumer Electronics: Heat Sink PCBs are increasingly used in consumer electronic devices, such as gaming consoles, high-performance laptops, and virtual reality headsets. As these devices become more powerful and compact, effective thermal management is necessary to prevent overheating and ensure optimal performance.
Advantages of Heat Sink PCBs
-
Efficient Heat Dissipation: Heat Sink PCBs provide an efficient means of removing heat from critical components, ensuring that they operate within their safe temperature range. The integrated heat sinking features facilitate rapid heat transfer and dissipation.
-
Improved Reliability: By effectively managing heat, Heat Sink PCBs contribute to the overall reliability and longevity of electronic devices. Maintaining a stable thermal environment reduces the risk of heat-related failures and extends the operational life of components.
-
Space Optimization: Heat Sink PCBs enable designers to integrate heat sinking capabilities directly into the PCB, eliminating the need for separate heat sinks or additional thermal management components. This results in more compact and streamlined designs.
-
Cost Reduction: Implementing Heat Sink PCBs can lead to cost savings by reducing the occurrence of heat-related failures and minimizing the need for repairs or replacements. The integration of heat sinking features into the PCB itself can also simplify the manufacturing process and reduce assembly costs.
-
Design Flexibility: Heat Sink PCBs offer design flexibility by allowing designers to customize the thermal management solution based on the specific requirements of the application. The ability to optimize copper thickness, trace routing, and thermal via placement enables tailored thermal performance.
Challenges and Considerations
While Heat Sink PCBs offer numerous benefits, there are also challenges and considerations to keep in mind:
-
Design Complexity: Designing a Heat Sink PCB requires expertise in both electrical and thermal engineering. The complex interplay between component placement, trace routing, and thermal management necessitates careful analysis and optimization.
-
Manufacturing Challenges: The manufacturing process for Heat Sink PCBs can be more complex compared to standard PCBs. The increased copper thickness, thermal vias, and heat sink attachment features may require specialized manufacturing techniques and equipment.
-
Cost Considerations: Heat Sink PCBs may have higher initial costs compared to standard PCBs due to the additional materials and manufacturing processes involved. However, the long-term benefits in terms of reliability and performance often outweigh the initial investment.
-
Integration with Other Components: When integrating Heat Sink PCBs into a larger system, designers must consider the compatibility and thermal interface with other components. Proper thermal coupling and heat transfer between the PCB and adjacent components are crucial for optimal system-level thermal management.
-
Testing and Validation: Thorough testing and validation are essential to ensure that Heat Sink PCBs meet the desired thermal performance requirements. Thermal characterization, stress testing, and reliability assessments should be conducted to verify the effectiveness of the heat sinking solution.
Future Trends and Innovations
As electronic devices continue to advance and become more compact and powerful, the demand for innovative thermal management solutions will only increase. Some future trends and innovations in Heat Sink PCBs include:
-
Advanced Materials: Researchers are exploring new materials with enhanced thermal conductivity, such as graphene, carbon nanotubes, and diamond-like carbon coatings. These materials have the potential to further improve the thermal performance of Heat Sink PCBs.
-
3D Printing: Additive manufacturing techniques, such as 3D printing, are being investigated for the fabrication of Heat Sink PCBs. 3D printing allows for the creation of complex geometries and customized heat sinking structures, enabling more efficient and targeted heat dissipation.
-
Embedded Cooling: The integration of active cooling solutions, such as miniature fans or liquid cooling channels, directly into the PCB is an emerging trend. Embedded cooling can provide additional heat removal capabilities, particularly for high-power applications.
-
Intelligent Thermal Management: The incorporation of sensors and control algorithms into Heat Sink PCBs is gaining traction. Intelligent thermal management systems can dynamically adjust cooling parameters based on real-time temperature data, optimizing heat dissipation and energy efficiency.
-
Multifunctional PCBs: The concept of multifunctional PCBs, where the PCB serves multiple purposes beyond electrical connectivity, is gaining attention. Heat Sink PCBs can be combined with other functionalities, such as electromagnetic shielding or structural support, to create highly integrated and efficient electronic systems.
Frequently Asked Questions (FAQ)
-
What is the difference between a Heat Sink PCB and a standard PCB?
A Heat Sink PCB incorporates heat sinking features directly into its design, prioritizing thermal management. It uses materials with high thermal conductivity, increased copper thickness, thermal vias, and provisions for heat sink attachment. In contrast, a standard PCB primarily focuses on electrical connectivity and may not have dedicated heat sinking capabilities. -
How do Heat Sink PCBs improve the reliability of electronic devices?
Heat Sink PCBs improve reliability by effectively managing the heat generated by electronic components. By maintaining a stable and controlled thermal environment, they prevent overheating, reduce heat-related stress on components, and minimize the risk of premature failures. This extends the operational life of electronic devices and enhances overall system reliability. -
What are thermal vias, and how do they contribute to heat dissipation in Heat Sink PCBs?
Thermal vias are small, conductive holes drilled through the PCB that create a thermal path between the heat-generating components and the heat sink. They facilitate the efficient transfer of heat from the components to the heat sink, allowing for effective heat dissipation. The number, size, and placement of thermal vias are crucial factors in maximizing heat transfer efficiency. -
Can Heat Sink PCBs be used in combination with external heat sinks?
Yes, Heat Sink PCBs are often used in conjunction with external heat sinks to further enhance heat dissipation. The PCB is designed to accommodate the attachment of heat sinks, either through direct contact or using thermal interface materials. Proper mounting and thermal interface selection ensure efficient heat transfer between the PCB and the heat sink, maximizing overall thermal performance. -
What are the key considerations when designing a Heat Sink PCB?
When designing a Heat Sink PCB, several key considerations should be taken into account: - Thermal analysis to optimize component placement and heat flow paths.
- Material selection, focusing on high thermal conductivity and compatibility with the application.
- Copper thickness and trace routing to minimize thermal resistance and ensure adequate heat conduction.
- Incorporation of thermal vias and heat spreading techniques to efficiently transfer heat.
- Integration with external heat sinks, considering mounting and thermal interface requirements.
- Manufacturing feasibility, cost implications, and compatibility with other system components.
Conclusion
Heat Sink Printed Circuit Boards have emerged as a crucial solution for effective thermal management in the electrical industry. By integrating heat sinking capabilities directly into the PCB design, Heat Sink PCBs offer an efficient means of dissipating heat from critical components, ensuring reliable operation and extended device lifespan. The importance of Heat Sink PCBs is evident in their ability to tackle the challenges posed by the increasing power density and miniaturization of electronic devices.
From power electronics and automotive systems to industrial control and consumer electronics, Heat Sink PCBs find applications across various sectors where thermal management is paramount. Their ability to optimize space, reduce costs, and improve overall system reliability makes them an indispensable tool in the designer’s arsenal.
As electronic devices continue to evolve and push the boundaries of performance, the demand for innovative thermal management solutions will only grow. Heat Sink PCBs, with their design flexibility and potential for integration with advanced materials and technologies, are well-positioned to meet the thermal challenges of the future.
By understanding the principles, design considerations, and benefits of Heat Sink PCBs, electrical engineers and designers can harness their potential to create more reliable, efficient, and compact electronic systems. As the electrical industry continues to innovate and adapt to the ever-changing landscape of technology, Heat Sink PCBs will undoubtedly play a vital role in ensuring the success and longevity of electronic devices.
Leave a Reply