Introduction to Flying Probe Testing
A Flying probe tester is an advanced printed circuit board (PCB) testing machine that utilizes movable test probes to perform electrical tests on bare or assembled PCBs. Unlike traditional bed-of-nails (or fixtureless) testers, which require custom-built test fixtures for each unique PCB design, flying probe testers offer a more flexible and cost-effective solution for low-volume production runs, prototypes, and high-mix manufacturing environments.
Key Features of Flying Probe Testers
- Movable test probes
- Automatic test program generation
- High accuracy and repeatability
- No need for custom test fixtures
- Suitable for low-volume production and prototyping
How Does a Flying Probe Tester Work?
The Testing Process
A flying probe tester consists of several key components that work together to perform electrical tests on a PCB:
-
Movable test probes: The heart of a flying probe tester is its set of movable test probes, which are typically mounted on a gantry system that allows them to move freely across the surface of the PCB. The number of probes can vary depending on the model, with some testers featuring up to 8 or more probes for increased testing speed.
-
Cameras and vision systems: To accurately position the test probes on the PCB, flying probe testers use high-resolution cameras and advanced vision systems to identify and locate test points, such as component leads, vias, and test pads. This enables the tester to adapt to variations in PCB design and placement without the need for custom fixtures.
-
Test program generation: Flying probe testers use software to automatically generate test programs based on the PCB design data, such as Gerber files or CAD files. The software analyzes the PCB layout and generates a test sequence that covers all the necessary electrical tests, such as continuity, resistance, capacitance, and insulation resistance tests.
-
Probe contact and measurement: During the testing process, the movable probes descend onto the PCB and make contact with the test points. The tester then performs the programmed electrical measurements, comparing the results against predefined tolerance limits to determine if the PCB passes or fails the test.
Advantages of Flying Probe Testing
Flying probe testers offer several key advantages over traditional bed-of-nails testers:
-
Flexibility: With their ability to adapt to different PCB designs without the need for custom fixtures, flying probe testers offer unparalleled flexibility in testing a wide range of PCBs. This makes them particularly well-suited for high-mix, low-volume production environments, where the cost and time required to develop custom fixtures for each PCB design would be prohibitive.
-
Cost-effectiveness: By eliminating the need for custom test fixtures, flying probe testers can significantly reduce the overall cost of PCB Testing, particularly for low-volume production runs and prototypes. This can help manufacturers bring new products to market faster and more efficiently.
-
High accuracy and repeatability: Flying probe testers are known for their high accuracy and repeatability, thanks to their advanced vision systems and precise probe placement. This ensures that PCBs are tested consistently and reliably, reducing the risk of defective products reaching the customer.
-
Rapid test program development: With automatic test program generation based on PCB design data, flying probe testers can significantly reduce the time and effort required to develop test programs compared to traditional methods. This allows manufacturers to quickly adapt to changes in PCB design and bring new products to market faster.
Applications of Flying Probe Testers
Flying probe testers are used in a wide range of industries and applications, including:
-
Consumer electronics: From smartphones and tablets to wearables and IoT devices, flying probe testers are essential for ensuring the quality and reliability of consumer electronics PCBs.
-
Automotive electronics: As vehicles become increasingly reliant on electronic systems, flying probe testers play a crucial role in testing Automotive PCBs, such as engine control modules, infotainment systems, and advanced driver assistance systems (ADAS).
-
Medical devices: Flying probe testers are used to test PCBs for medical devices, such as patient monitors, diagnostic equipment, and implantable devices, where reliability and safety are of utmost importance.
-
Aerospace and defense: In the aerospace and defense industries, flying probe testers are used to test PCBs for applications such as avionics, communications systems, and military equipment, where high reliability and performance are critical.
-
Industrial automation: Flying probe testers are used to test PCBs for industrial automation systems, such as programmable logic controllers (PLCs), human-machine interfaces (HMIs), and sensors, ensuring the smooth operation of manufacturing processes.
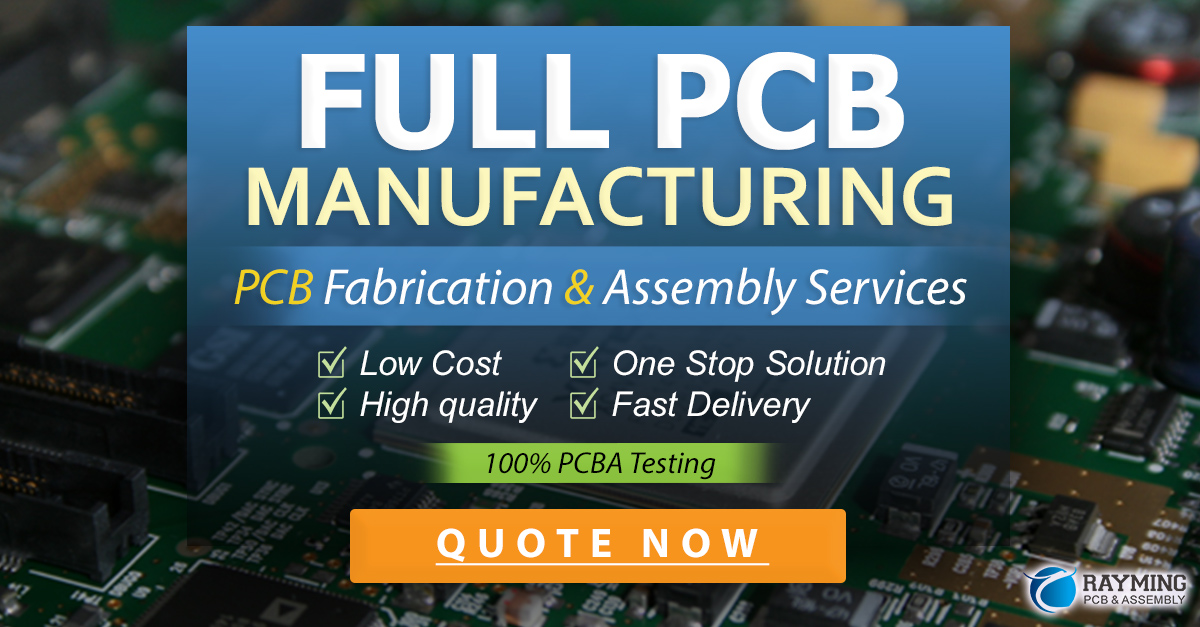
Choosing the Right Flying Probe Tester
When selecting a flying probe tester for your specific application, there are several key factors to consider:
-
Number of test probes: The number of test probes on a flying probe tester directly impacts its testing speed and throughput. Higher-end models may feature 8 or more probes, allowing for faster testing of complex PCBs.
-
Probe accuracy and repeatability: Look for a tester with high probe accuracy and repeatability to ensure consistent and reliable testing results. This is particularly important for PCBs with small component pitches and high-density layouts.
-
Vision system capabilities: A flying probe tester’s vision system plays a critical role in accurately locating and positioning the test probes. Consider a tester with advanced vision capabilities, such as high-resolution cameras and automatic component recognition, to ensure precise probe placement on a wide range of PCBs.
-
Test program generation: Choose a tester with user-friendly software that can automatically generate test programs based on PCB design data, such as Gerber files or CAD files. This can significantly reduce the time and effort required to develop test programs and adapt to changes in PCB design.
-
Expandability and upgradability: As your testing needs evolve, it’s important to choose a flying probe tester that can grow with your business. Look for a tester with expandable hardware and software options, such as additional test probes, enhanced vision systems, and updated test libraries, to ensure that your investment can keep pace with your changing requirements.
Best Practices for Flying Probe Testing
To ensure optimal results when using a flying probe tester, consider the following best practices:
-
Ensure accurate PCB design data: The accuracy of your flying probe tester’s results depends on the quality of the PCB design data used to generate the test program. Ensure that your Gerber files or CAD files are up-to-date and free of errors to avoid test failures and false positives.
-
Optimize PCB layout for testability: When designing PCBs for flying probe testing, consider factors such as component spacing, test pad size and location, and trace routing to ensure adequate access for the test probes. Consult with your PCB designer and flying probe tester manufacturer for specific guidelines and recommendations.
-
Perform regular maintenance and calibration: To ensure consistent and reliable testing results, perform regular maintenance and calibration on your flying probe tester. This may include cleaning the test probes, updating software and firmware, and verifying the accuracy of the vision system and measurement instruments.
-
Train operators thoroughly: Proper operator training is essential for maximizing the efficiency and effectiveness of your flying probe tester. Ensure that your operators are well-versed in the tester’s software, hardware, and maintenance procedures, as well as best practices for PCB Handling and testing.
-
Monitor and analyze test results: Regularly monitor and analyze the test results from your flying probe tester to identify trends, anomalies, and opportunities for improvement. This can help you optimize your testing process, reduce defects, and improve overall product quality.
FAQ
-
Q: What is the difference between a flying probe tester and a bed-of-nails tester?
A: A flying probe tester uses movable test probes to perform electrical tests on a PCB, while a bed-of-nails tester requires a custom-built test fixture with fixed probes for each unique PCB design. Flying probe testers offer greater flexibility and cost-effectiveness for low-volume production and high-mix environments. -
Q: How long does it take to develop a test program for a flying probe tester?
A: The time required to develop a test program for a flying probe tester varies depending on the complexity of the PCB and the specific tester model. However, with automatic test program generation based on PCB design data, the process is generally much faster than traditional methods, often taking just a few hours or days. -
Q: Can flying probe testers be used for both bare and assembled PCBs?
A: Yes, flying probe testers can be used to test both bare PCBs (before components are mounted) and assembled PCBs (after components are soldered in place). The specific tests performed may vary depending on the stage of production and the requirements of the application. -
Q: What types of electrical tests can a flying probe tester perform?
A: Flying probe testers can perform a wide range of electrical tests, including continuity, resistance, capacitance, insulation resistance, and diode and transistor tests. Some advanced models may also offer additional capabilities, such as in-circuit programming and boundary scan testing. -
Q: How much does a flying probe tester cost?
A: The cost of a flying probe tester can vary widely depending on factors such as the number of test probes, vision system capabilities, and software features. Entry-level models may start at around $50,000, while high-end systems can cost $500,000 or more. However, the long-term cost savings and flexibility offered by flying probe testers can make them a valuable investment for many PCB manufacturers.
Conclusion
Flying probe testers are a versatile and cost-effective solution for electrical testing of PCBs, particularly in low-volume production runs, prototyping, and high-mix manufacturing environments. By utilizing movable test probes and advanced vision systems, flying probe testers offer unparalleled flexibility, accuracy, and repeatability, eliminating the need for custom test fixtures and reducing overall testing costs.
When selecting a flying probe tester, it’s essential to consider factors such as the number of test probes, probe accuracy and repeatability, vision system capabilities, test program generation, and expandability. By following best practices for PCB design, tester maintenance, operator training, and results analysis, manufacturers can maximize the efficiency and effectiveness of their flying probe testing process, ensuring high-quality, reliable products for their customers.
As the demand for high-quality, reliable electronics continues to grow across industries, from consumer devices to automotive and medical applications, flying probe testers will undoubtedly play an increasingly important role in ensuring the integrity and performance of PCBs. By embracing this advanced testing technology, manufacturers can streamline their production processes, reduce costs, and deliver better products to market faster than ever before.
Leave a Reply