The Importance of Medical device PCBAs
PCBAs are essential components in a wide range of medical devices, from patient monitors and diagnostic imaging systems to implantable devices and surgical instruments. These electronic assemblies enable the functionality, control, and communication capabilities of medical equipment. The performance and reliability of medical device PCBAs directly impact patient safety and the effectiveness of medical procedures.
Some examples of medical devices that rely heavily on PCBAs include:
- Cardiac pacemakers and defibrillators
- Infusion pumps and drug delivery systems
- Blood glucose monitors and insulin pumps
- Electrocardiogram (ECG) and electroencephalogram (EEG) machines
- Computed tomography (CT) and magnetic resonance imaging (MRI) scanners
- Surgical robotics and navigation systems
Given the critical role of PCBAs in these life-sustaining and life-saving devices, manufacturers must adhere to stringent quality standards and regulatory requirements to ensure the highest levels of reliability, functionality, and patient safety.
Key Challenges in Medical Equipment Manufacturing
Manufacturing medical devices, including PCBAs, presents several unique challenges compared to other industries. Some of the key challenges include:
1. Regulatory Compliance
Medical device manufacturers must comply with a complex web of regulations and standards enforced by various regulatory bodies worldwide. In the United States, the Food and Drug Administration (FDA) oversees medical device safety and effectiveness. Manufacturers must follow the FDA’s Quality System Regulation (QSR), also known as 21 CFR Part 820, which outlines current Good Manufacturing Practices (cGMP) for medical devices.
Other major regulatory bodies include:
- European Union: Medical Device Regulation (MDR) and In Vitro Diagnostic Regulation (IVDR)
- Canada: Health Canada Medical Devices Regulations
- Japan: Pharmaceutical and Medical Device Act (PMDA)
- China: National Medical Products Administration (NMPA)
Complying with these regulations involves implementing robust quality management systems, maintaining extensive documentation, conducting rigorous testing and validation, and undergoing regular audits and inspections.
2. Quality Management
Ensuring consistent quality is paramount in medical device manufacturing. Manufacturers must establish and maintain an effective quality management system (QMS) that covers all aspects of design, production, and post-market surveillance. Key elements of a medical device QMS include:
- Design controls and verification
- Supplier management and incoming inspection
- Manufacturing process controls and validation
- Product traceability and serialization
- Complaint handling and adverse event reporting
- Corrective and preventive actions (CAPA)
Implementing a QMS compliant with standards such as ISO 13485 and 21 CFR Part 820 helps manufacturers consistently produce safe and effective devices while minimizing the risk of quality issues and regulatory non-compliance.
3. Materials Selection and Biocompatibility
Medical devices often come into direct contact with patients, either externally or as implantable devices. As such, the materials used in medical device PCBAs must be carefully selected to ensure biocompatibility and avoid any adverse reactions or toxicity. Manufacturers must consider factors such as:
- Material safety and toxicology data
- Sterilization compatibility (e.g., autoclave, ethylene oxide, radiation)
- Long-term stability and durability
- Mechanical and electrical properties
- Regulatory requirements for biocompatibility testing (e.g., ISO 10993)
Choosing the right materials and documenting their biocompatibility is crucial to ensuring patient safety and obtaining regulatory approval.
4. Design for Manufacturability and Reliability
Medical device PCBAs must be designed with manufacturability and reliability in mind. Designers must consider factors such as:
- Component selection and sourcing (e.g., medical-grade components, long-term availability)
- PCB layout and routing (e.g., signal integrity, EMI/EMC considerations)
- Assembly processes (e.g., soldering, cleaning, inspection)
- Environmental conditions (e.g., temperature, humidity, shock, and vibration)
- Reliability testing and qualification (e.g., accelerated life testing, HALT/HASS)
Designing for manufacturability helps ensure consistent quality and reduces the risk of defects and failures. Reliability engineering is crucial to predict and mitigate potential failure modes, ensuring the device performs safely and effectively throughout its intended lifetime.
5. Supply Chain Management
Medical device manufacturers often rely on a complex network of suppliers for components, materials, and services. Managing the supply chain is critical to ensure quality, traceability, and continuity of supply. Key challenges include:
- Supplier qualification and auditing
- Material and component traceability
- Managing obsolescence and end-of-life components
- Ensuring compliance with regulations (e.g., RoHS, REACH, Conflict Minerals)
- Maintaining adequate inventory and lead times
- Contingency planning for supply disruptions
Effective supply chain management helps manufacturers maintain quality, control costs, and minimize the risk of production delays or quality issues.
Standards and Regulations Applicable to Medical Device PCBAs
Several standards and regulations specifically apply to the design, manufacture, and testing of medical device PCBAs. Some of the key standards include:
IPC Standards
- IPC-A-610: Acceptability of Electronic Assemblies
- IPC-J-STD-001: Requirements for Soldered Electrical and Electronic Assemblies
- IPC-6012: Qualification and Performance Specification for Rigid Printed Boards
These IPC standards provide guidelines for quality, workmanship, and acceptance criteria for PCBAs, helping ensure consistent manufacturing processes and product quality.
ISO 13485: Medical devices – Quality management systems
ISO 13485 specifies requirements for a quality management system specific to the medical device industry. It covers design, development, production, installation, and servicing of medical devices. Manufacturers must demonstrate compliance with ISO 13485 to obtain regulatory approval in many markets.
IEC 60601: Medical electrical equipment
The IEC 60601 series of standards applies to the safety and essential performance of medical electrical equipment. It covers various aspects, including:
- Electrical safety and isolation
- Electromagnetic compatibility (EMC)
- Usability and human factors engineering
- Risk management and essential performance
Medical device PCBAs must be designed and tested to comply with the relevant IEC 60601 requirements based on the specific device and its intended use.
FDA 21 CFR Part 820: Quality System Regulation
The FDA’s Quality System Regulation (QSR) outlines current Good Manufacturing Practices (cGMP) for medical devices. It covers various aspects of design, manufacture, packaging, labeling, storage, installation, and servicing. Manufacturers must establish and maintain a quality system that complies with 21 CFR Part 820 to market devices in the United States.
Risk Management: ISO 14971
ISO 14971 specifies requirements for risk management applied to medical devices. Manufacturers must identify, analyze, evaluate, and control risks associated with their devices throughout the product lifecycle. This includes risks related to PCBAs, such as component failures, manufacturing defects, and potential hazards to patients and users.
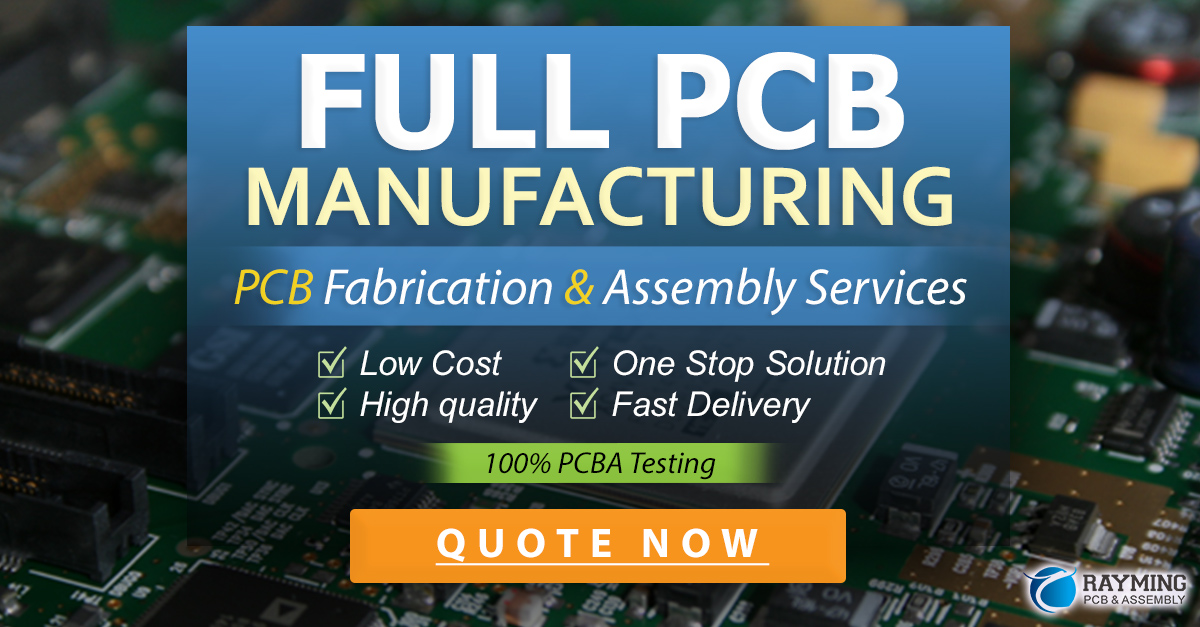
Frequently Asked Questions (FAQ)
1. What are the main differences between PCBAs for medical devices and those for other industries?
Medical device PCBAs are subject to more stringent quality, reliability, and regulatory requirements compared to PCBAs for other industries. Key differences include:
- Use of medical-grade components and materials
- Emphasis on biocompatibility and sterilization compatibility
- Higher levels of traceability and documentation
- More extensive testing and validation requirements
- Compliance with specific medical device standards and regulations
2. How can medical device manufacturers ensure compliance with the various regulations and standards?
To ensure compliance, manufacturers should:
- Establish and maintain a robust quality management system (QMS) compliant with standards such as ISO 13485 and 21 CFR Part 820
- Conduct thorough design reviews, risk assessments, and validation testing
- Maintain comprehensive documentation, including design files, production records, and traceability data
- Perform regular internal audits and participate in external audits by regulatory bodies and customers
- Stay up-to-date with changes in regulations and standards and adapt processes accordingly
3. What are the consequences of non-compliance with medical device regulations?
Non-compliance with medical device regulations can result in severe consequences, including:
- Regulatory enforcement actions, such as warning letters, fines, or product seizures
- Delayed or denied market approval for new devices
- Mandatory product recalls or market withdrawals
- Loss of customer trust and damage to brand reputation
- Civil or criminal liability in case of patient harm or injury
4. How can medical device manufacturers manage supply chain risks related to PCBAs?
To manage supply chain risks, manufacturers should:
- Conduct thorough supplier qualification and audits to ensure compliance with quality and regulatory requirements
- Establish long-term agreements with key suppliers to ensure continuity of supply
- Implement robust traceability systems to track components and materials throughout the supply chain
- Monitor suppliers’ performance and maintain open communication to identify and address potential issues proactively
- Develop contingency plans for alternative suppliers or redesigns in case of component obsolescence or supply disruptions
5. What are the key considerations for selecting materials and components for medical device PCBAs?
When selecting materials and components for medical device PCBAs, manufacturers should consider:
- Biocompatibility and toxicology data to ensure patient safety
- Compatibility with sterilization methods required for the specific device
- Long-term stability and reliability under expected environmental conditions
- Availability of materials and components throughout the device’s lifecycle
- Compliance with relevant regulations, such as RoHS and REACH
- Electrical and mechanical properties required for the specific application
- Cost and supply chain implications of material and component choices
Conclusion
Manufacturing PCBAs for medical devices presents unique challenges due to the stringent quality, reliability, and regulatory requirements essential for ensuring patient safety and device effectiveness. Medical device manufacturers must navigate a complex landscape of standards and regulations while addressing technical challenges related to design, materials selection, manufacturing processes, and supply chain management.
By implementing robust quality management systems, conducting thorough testing and validation, and maintaining strict compliance with relevant standards and regulations, manufacturers can consistently produce high-quality, reliable PCBAs that meet the demanding requirements of the medical device industry. As technology advances and regulations evolve, staying informed and adaptable will be crucial for success in this critical and ever-changing field.
Leave a Reply