Key Factors Influencing Solder Joint Quality
1. Solder Alloy Composition
The choice of solder alloy composition is one of the most important factors influencing solder joint quality. Different solder alloys have varying melting points, wetting properties, and mechanical strengths, which can affect the formation and reliability of solder joints.
Common Solder Alloys
Alloy | Composition | Melting Point (°C) |
---|---|---|
Sn-Pb | 63% Sn, 37% Pb | 183 |
SAC305 | 96.5% Sn, 3% Ag, 0.5% Cu | 217-220 |
SAC405 | 95.5% Sn, 4% Ag, 0.5% Cu | 217-220 |
Sn-Bi | 42% Sn, 58% Bi | 139 |
Lead-free solder alloys, such as SAC305 and SAC405, have become increasingly popular due to environmental regulations (e.g., RoHS). These alloys have higher melting points compared to traditional Sn-Pb alloys, which can affect the soldering process and joint formation.
2. Flux Selection
Flux plays a critical role in removing oxides from the surfaces of the solder and the components being soldered, promoting better wetting and joint formation. The selection of the appropriate flux is essential for achieving high-quality solder joints.
Flux Types
- Rosin-based flux
- Rosin (R)
- Rosin Mildly Activated (RMA)
- Rosin Activated (RA)
- Water-soluble flux
- No-clean flux
The choice of flux depends on the soldering process, the components being soldered, and the cleanliness requirements of the final assembly.
3. Soldering Temperature Profile
The soldering temperature profile is another critical factor influencing solder joint quality. The temperature profile should be optimized to ensure proper melting and wetting of the solder while minimizing thermal stress on the components.
Key Aspects of Temperature Profile
- Preheat: Gradually raises the temperature of the assembly to minimize thermal shock.
- Soak: Allows the assembly to reach a uniform temperature before the reflow stage.
- Reflow: Melts the solder and forms the solder joints.
- Cooling: Gradually cools the assembly to room temperature, allowing the solder joints to solidify.
Improper temperature profiles can lead to defects such as cold joints, poor wetting, and component damage.
4. Component and PCB Surface Finish
The surface finish of the components and the printed circuit board (PCB) can significantly impact solder joint quality. Common surface finishes include:
- Hot Air Solder Leveling (HASL)
- Organic Solderability Preservative (OSP)
- Electroless Nickel Immersion Gold (ENIG)
- Immersion Silver (ImAg)
- Immersion Tin (ImSn)
Each surface finish has its advantages and disadvantages in terms of solderability, shelf life, and cost. The compatibility between the surface finish and the solder alloy should be considered to ensure optimal joint formation.
5. Solder Paste Printing
Solder paste printing is a critical step in the surface mount assembly process. The quality of the solder paste deposit can significantly influence the formation and reliability of solder joints.
Factors Affecting Solder Paste Printing Quality
- Stencil design
- Aperture size and shape
- Stencil thickness
- Solder paste properties
- Viscosity
- Particle size distribution
- Printing parameters
- Print speed
- Squeegee pressure
- Separation speed
Proper control of these factors is essential for achieving consistent solder paste deposits and high-quality solder joints.
6. Reflow Soldering Process
The reflow soldering process involves heating the assembly to melt the solder paste and form the solder joints. The quality of the reflow process is influenced by several factors:
- Oven type (convection, vapor phase, infrared)
- Heating zones and temperature settings
- Conveyor speed
- Nitrogen environment (for reducing oxidation)
Optimization of the reflow soldering process is crucial for achieving consistent and reliable solder joints.
7. Cleaning Process
After soldering, the assembly may require cleaning to remove flux residues and other contaminants. The choice of cleaning method and the effectiveness of the cleaning process can impact the long-term reliability of solder joints.
Cleaning Methods
- Aqueous cleaning
- Solvent cleaning
- No-clean (for no-clean fluxes)
Proper cleaning ensures the removal of potentially corrosive flux residues and improves the electrical and mechanical properties of the solder joints.
8. Environmental Factors
Environmental factors can influence the formation and long-term reliability of solder joints. These factors include:
- Temperature cycling
- Humidity
- Vibration and mechanical shock
- Corrosive environments
Designing and testing solder joints for environmental robustness is essential for ensuring the reliability of electronic assemblies in various operating conditions.
Frequently Asked Questions (FAQ)
-
Q: What is the difference between lead-based and lead-free solder alloys?
A: Lead-based solder alloys, such as Sn-Pb, have been widely used in the electronics industry due to their low melting point and good wetting properties. However, environmental regulations, such as RoHS, have led to the adoption of lead-free solder alloys, such as SAC305 and SAC405. Lead-free alloys have higher melting points and different wetting behaviors compared to lead-based alloys, which can affect the soldering process and joint formation. -
Q: How does flux help in the soldering process?
A: Flux serves several important functions in the soldering process. It removes oxides and other contaminants from the surfaces of the solder and the components being soldered, promoting better wetting and joint formation. Flux also protects the surfaces from re-oxidation during the soldering process. The selection of the appropriate flux is essential for achieving high-quality solder joints. -
Q: What is the importance of the soldering temperature profile?
A: The soldering temperature profile is critical for ensuring proper melting and wetting of the solder while minimizing thermal stress on the components. An optimized temperature profile consists of preheat, soak, reflow, and cooling stages. Improper temperature profiles can lead to defects such as cold joints, poor wetting, and component damage. Therefore, careful control and optimization of the temperature profile are essential for achieving high-quality solder joints. -
Q: How does the surface finish of components and PCBs affect solder joint quality?
A: The surface finish of the components and the printed circuit board (PCB) can significantly impact solder joint quality. Different surface finishes, such as HASL, OSP, ENIG, ImAg, and ImSn, have varying solderability, shelf life, and cost. The compatibility between the surface finish and the solder alloy should be considered to ensure optimal joint formation. Proper selection of the surface finish is crucial for achieving reliable solder joints. -
Q: Why is cleaning important after the soldering process?
A: Cleaning after the soldering process is important for removing flux residues and other contaminants that can potentially degrade the long-term reliability of solder joints. Flux residues can be corrosive and can lead to electrical and mechanical issues over time. Proper cleaning, using methods such as aqueous or solvent cleaning, ensures the removal of these residues and improves the overall quality and reliability of the solder joints.
Conclusion
The quality of solder joints is influenced by a complex interplay of various factors, including solder alloy composition, flux selection, soldering temperature profile, component and PCB surface finish, solder paste printing, reflow soldering process, cleaning process, and environmental factors. Understanding and optimizing these factors is essential for achieving high-quality and reliable solder joints in electronic assemblies.
By carefully considering and controlling these influential factors, manufacturers can minimize defects, improve the performance and reliability of their electronic products, and ensure customer satisfaction. Continuous monitoring, process control, and quality assurance practices are necessary to maintain consistent solder joint quality in the ever-evolving electronics industry.
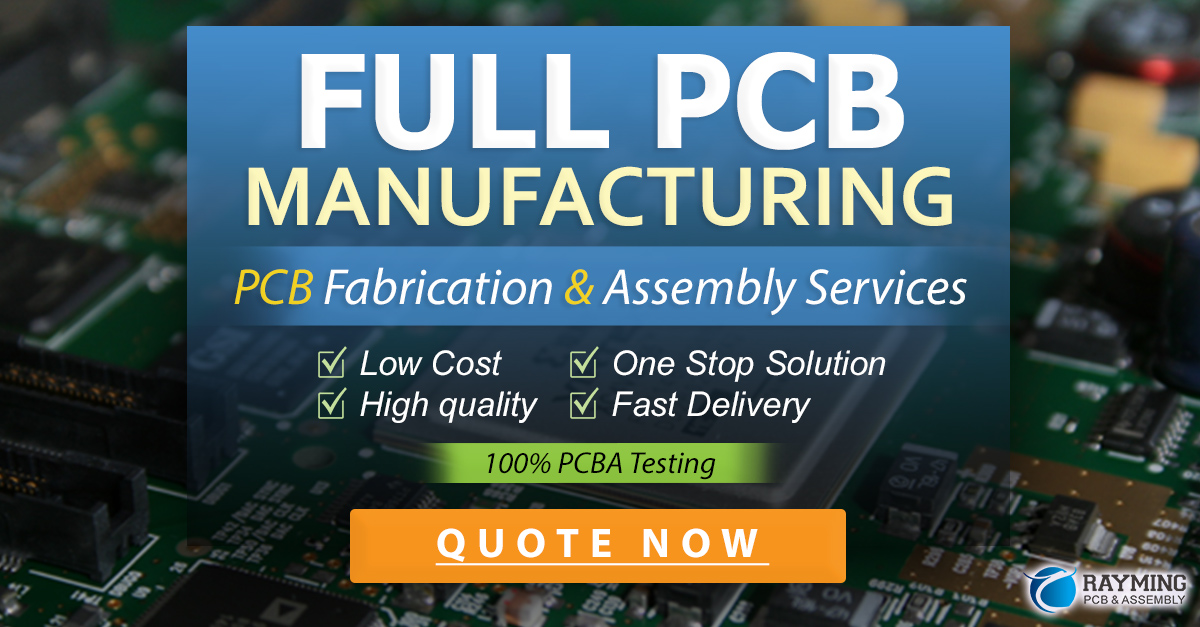
Leave a Reply