Types of PCB Defects
Before delving into the defect detection strategies, it is essential to understand the common types of defects that can occur in PCBs. These defects can be categorized into several types:
- Open circuits: Broken or missing traces, leading to incomplete electrical connections.
- Short circuits: Unintended connections between traces or components, causing electrical shorts.
- Solder defects: Issues related to soldering, such as insufficient solder, bridging, or poor solder joints.
- Component defects: Damaged, misaligned, or missing components on the PCB.
- Hole defects: Misaligned, oversized, or missing holes for through-hole components.
- Copper thickness variations: Inconsistent copper thickness across the PCB, affecting electrical performance.
- Laminate defects: Issues with the PCB substrate, such as delamination or blistering.
PCB Defect Detection Strategies
To identify and mitigate PCB defects, several defect detection strategies are employed in the manufacturing process:
1. Automated Optical Inspection (AOI)
Automated Optical Inspection (AOI) is a widely used technique for detecting surface-level defects on PCBs. AOI systems utilize high-resolution cameras and advanced image processing algorithms to inspect the PCB for defects such as:
- Incorrect component placement
- Missing or misaligned components
- Solder defects (bridges, insufficient solder, etc.)
- Trace defects (breaks, shorts, etc.)
AOI systems compare the captured images of the PCB with a predefined golden sample or CAD data to identify any discrepancies or anomalies. The benefits of AOI include:
- High-speed inspection
- Consistent and objective defect detection
- Ability to detect a wide range of surface-level defects
- Integration with automated production lines
However, AOI has limitations in detecting internal or hidden defects, such as those within the PCB layers or beneath components.
AOI Defect Detection Rates
Defect Type | Detection Rate |
---|---|
Component placement | 95-99% |
Solder defects | 90-95% |
Trace defects | 85-90% |
Hole defects | 80-85% |
2. X-Ray Inspection
X-ray inspection is a non-destructive testing method that allows for the detection of internal and hidden defects in PCBs. X-ray systems use high-energy radiation to penetrate the PCB and generate images of its internal structure. This technique is particularly useful for inspecting:
- Ball Grid Array (BGA) solder joints
- Flip-chip connections
- Vias and through-hole connections
- Internal delamination or voids
X-ray inspection provides a detailed view of the PCB’s internal structure, enabling the detection of defects that are not visible on the surface. The advantages of X-ray inspection include:
- Detection of hidden and internal defects
- Non-destructive testing
- Ability to inspect complex and high-density PCBs
However, X-ray inspection can be more time-consuming and expensive compared to AOI, and it may require specialized training for operators to interpret the X-ray images accurately.
X-Ray Inspection Defect Detection Rates
Defect Type | Detection Rate |
---|---|
BGA solder joints | 95-99% |
Flip-chip connections | 90-95% |
Via and through-hole | 85-90% |
Internal delamination | 80-85% |
3. In-Circuit Testing (ICT)
In-Circuit Testing (ICT) is a method that involves directly probing the PCB to verify the functionality and connectivity of individual components and circuits. ICT systems use a bed-of-nails fixture with spring-loaded probes that make contact with specific test points on the PCB. The system applies electrical signals and measures the response to detect defects such as:
- Open circuits
- Short circuits
- Incorrect component values
- Faulty components
ICT is highly effective in detecting electrical defects and ensuring the functional integrity of the PCB. The benefits of ICT include:
- Detection of electrical defects that may not be visible
- Verification of component values and functionality
- Ability to test both analog and digital circuits
However, ICT requires the design of specific test fixtures for each PCB, which can be time-consuming and costly. Additionally, the increasing component density and the use of surface-mount technology (SMT) can make it challenging to access test points on the PCB.
ICT Defect Detection Rates
Defect Type | Detection Rate |
---|---|
Open circuits | 95-99% |
Short circuits | 95-99% |
Incorrect component values | 90-95% |
Faulty components | 90-95% |
4. Flying Probe Testing
Flying Probe Testing is an alternative to the traditional ICT method. Instead of using a fixed bed-of-nails fixture, flying probe systems employ movable probes that can access different test points on the PCB. The probes are controlled by a software program that guides them to the desired locations on the PCB. Flying probe testing is used to detect defects similar to those identified by ICT, including:
- Open circuits
- Short circuits
- Incorrect component values
- Faulty components
The advantages of flying probe testing include:
- Flexibility in testing different PCB designs without the need for custom fixtures
- Ability to test high-density and fine-pitch components
- Reduced setup time and cost compared to ICT
However, flying probe testing is generally slower than ICT due to the sequential probing of test points. It may also have limitations in accessing certain areas of the PCB, such as those obscured by tall components.
Flying Probe Testing Defect Detection Rates
Defect Type | Detection Rate |
---|---|
Open circuits | 90-95% |
Short circuits | 90-95% |
Incorrect component values | 85-90% |
Faulty components | 85-90% |
5. Boundary Scan Testing
Boundary Scan Testing, also known as JTAG (Joint Test Action Group) testing, is a method that utilizes the built-in test capabilities of certain integrated circuits (ICs) to detect defects on the PCB. Boundary scan-enabled ICs have dedicated test circuitry that allows access to their input and output pins. By connecting these ICs in a chain, the boundary scan system can control and monitor the signals between them, enabling the detection of defects such as:
- Open circuits
- Short circuits
- Faulty connections between ICs
The benefits of boundary scan testing include:
- Ability to test complex and high-density PCBs
- Detection of defects that are difficult to access physically
- Reduced need for physical test points on the PCB
However, boundary scan testing requires the presence of boundary scan-enabled ICs on the PCB, and not all components may support this feature. Additionally, boundary scan testing primarily focuses on the interconnections between ICs and may not cover all aspects of the PCB.
Boundary Scan Testing Defect Detection Rates
Defect Type | Detection Rate |
---|---|
Open circuits | 95-99% |
Short circuits | 95-99% |
Faulty connections between ICs | 90-95% |
Frequently Asked Questions (FAQ)
-
Q: What is the most common defect in PCB manufacturing?
A: Solder defects, such as insufficient solder, bridging, or poor solder joints, are among the most common defects encountered in PCB manufacturing. -
Q: Can a single defect detection method catch all types of PCB defects?
A: No, each defect detection method has its strengths and limitations. A combination of different methods is often used to achieve comprehensive defect coverage. -
Q: How can PCB defects be prevented in the manufacturing process?
A: Implementing strict quality control measures, following best practices in PCB design and manufacturing, and conducting regular maintenance of production equipment can help prevent PCB defects. -
Q: What is the impact of PCB defects on electronic devices?
A: PCB defects can lead to malfunctions, reduced performance, or complete failure of electronic devices. They can also pose safety risks, such as electrical shorts or overheating. -
Q: How often should defect detection be performed during PCB manufacturing?
A: Defect detection should be performed at various stages of the manufacturing process, including after PCB fabrication, assembly, and final testing, to identify and rectify defects as early as possible.
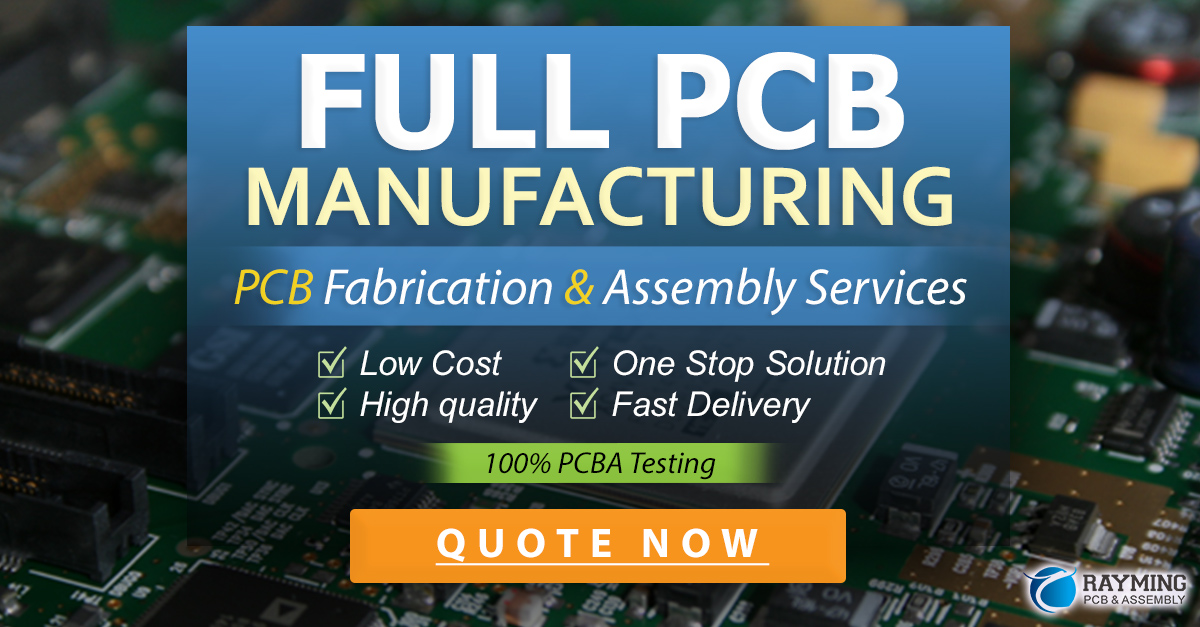
Conclusion
Detecting and mitigating defects in bare PCB boards is crucial for ensuring the quality, reliability, and performance of electronic devices. Various defect detection strategies, such as Automated Optical Inspection (AOI), X-ray inspection, In-Circuit Testing (ICT), Flying Probe Testing, and Boundary Scan Testing, are employed to identify different types of defects. Each method has its strengths and limitations, and a combination of techniques is often used to achieve comprehensive defect coverage.
By implementing effective defect detection strategies and following best practices in PCB design and manufacturing, manufacturers can minimize the occurrence of defects and produce high-quality PCBs. Regular monitoring, maintenance, and continuous improvement of the manufacturing process are essential for staying ahead of potential defect issues and ensuring customer satisfaction.
As technology advances and PCBs become more complex, the importance of robust defect detection strategies will only continue to grow. Manufacturers must stay updated with the latest inspection technologies and adapt their processes accordingly to meet the ever-increasing demands for reliable and defect-free PCBs in the electronics industry.
Leave a Reply