Introduction to Prototype PCB Manufacturing
Prototype PCB (Printed Circuit Board) manufacturing is a crucial process in the development of electronic devices. It involves creating a small batch of PCBs for testing and validation purposes before mass production. Prototype PCBs allow designers and engineers to evaluate the functionality, performance, and reliability of their designs, making necessary adjustments and improvements before committing to large-scale production.
In this article, we will explore the benefits of prototype PCB manufacturing and why it is essential in the electronics industry. We will also discuss the various aspects of prototype PCB manufacturing, including design considerations, fabrication techniques, and testing methods.
The Importance of Prototype PCB Manufacturing
1. Design Validation
One of the primary benefits of prototype PCB manufacturing is design validation. By creating a physical prototype of the PCB, designers can test and verify the functionality of their designs in real-world conditions. This allows them to identify and resolve any issues or errors in the design before proceeding to mass production.
Prototype PCBs enable designers to:
– Check the electrical connectivity and signal integrity
– Verify the component placement and routing
– Test the power distribution and thermal management
– Assess the mechanical fit and assembly process
2. Cost Savings
Prototype PCB manufacturing can significantly reduce the overall cost of product development. By identifying and resolving design issues early in the development cycle, companies can avoid costly mistakes and rework during mass production.
Consider the following scenario:
Scenario | Cost of Prototype PCB | Cost of Rework in Mass Production |
---|---|---|
Without Prototype PCB | $0 | $100,000 |
With Prototype PCB | $5,000 | $10,000 |
In this example, investing in prototype PCB manufacturing can save the company $85,000 in potential rework costs during mass production.
3. Time-to-Market Acceleration
Prototype PCB manufacturing can also help accelerate the time-to-market for new products. By validating the design and functionality of the PCB early in the development process, companies can avoid delays and setbacks during mass production.
Prototype PCBs allow companies to:
– Test and refine the design iteratively
– Evaluate the manufacturing process and identify bottlenecks
– Obtain customer feedback and make necessary adjustments
– Prepare for regulatory certifications and compliance testing
4. Risk Mitigation
Prototype PCB manufacturing helps mitigate risks associated with product development. By identifying and addressing potential issues early on, companies can reduce the likelihood of product failures, recalls, and customer dissatisfaction.
Prototype PCBs enable companies to:
– Verify the reliability and durability of the design
– Test the product under various environmental conditions
– Assess the compatibility with other components and systems
– Validate the manufacturing process and quality control measures
Prototype PCB Design Considerations
When designing a prototype PCB, there are several key considerations to keep in mind:
1. Schematic Design
The schematic design is the first step in creating a prototype PCB. It involves capturing the electrical connections and components of the circuit using a schematic capture tool. The schematic should be carefully reviewed and verified to ensure accuracy and completeness.
2. Component Selection
Selecting the appropriate components for the prototype PCB is crucial for its functionality and performance. Designers should consider factors such as:
– Electrical specifications (e.g., voltage, current, power rating)
– Mechanical dimensions and footprint
– Availability and lead time
– Cost and sourcing options
3. Layout Design
The layout design involves arranging the components and routing the traces on the PCB. Designers should follow best practices and guidelines to ensure optimal signal integrity, power distribution, and manufacturability. Some key considerations include:
– Component placement and orientation
– Trace width and spacing
– Via size and placement
– Grounding and shielding
– Design for manufacturability (DFM) rules
4. Design Rule Check (DRC)
Before proceeding to fabrication, the prototype PCB design should undergo a thorough design rule check (DRC). The DRC verifies that the design adheres to the manufacturing constraints and guidelines, such as minimum trace width, spacing, and hole size. This helps ensure the manufacturability and reliability of the prototype PCB.
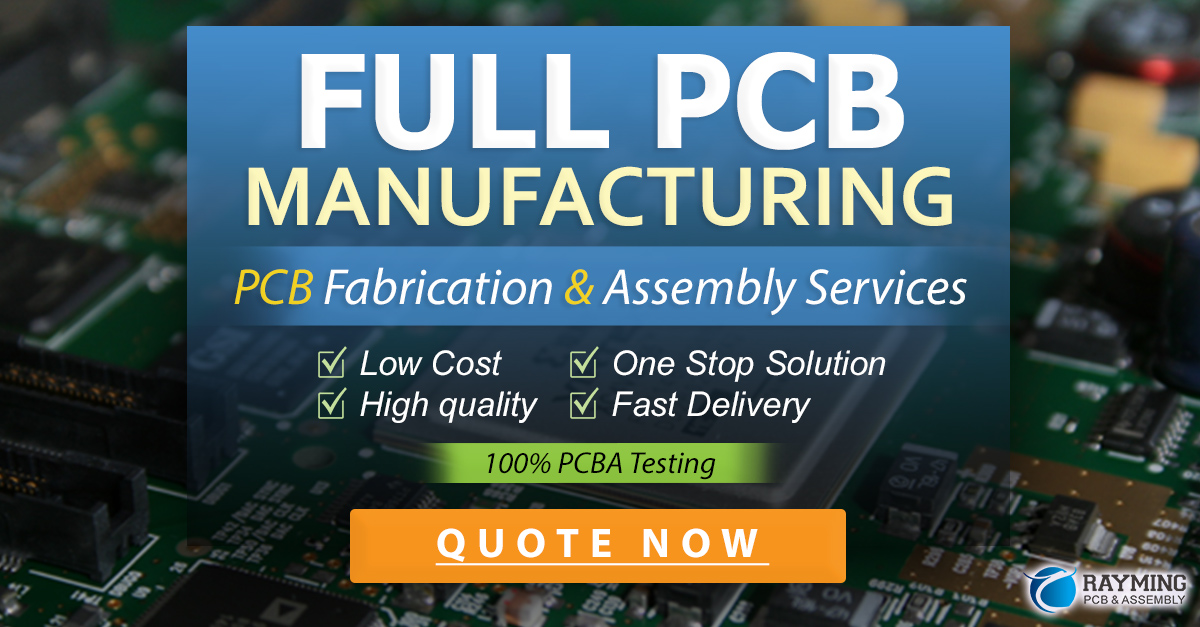
Prototype PCB Fabrication Techniques
There are several fabrication techniques used for prototype PCB manufacturing, each with its own advantages and limitations. The choice of fabrication technique depends on factors such as the complexity of the design, the required turnaround time, and the budget.
1. Subtractive Manufacturing
Subtractive manufacturing is the most common fabrication technique for prototype PCBs. It involves removing the unwanted copper from a pre-clad laminate using chemical etching or mechanical milling. The process typically includes the following steps:
– Applying a photoresist layer to the copper-clad laminate
– Exposing the photoresist to UV light through a photomask
– Developing the photoresist to remove the unexposed areas
– Etching away the exposed copper using a chemical solution
– Stripping the remaining photoresist and applying a protective finish
Subtractive manufacturing is suitable for most prototype PCB designs and offers a good balance between cost and quality.
2. Additive Manufacturing
Additive manufacturing, also known as 3D printing or direct write, is an emerging fabrication technique for prototype PCBs. It involves depositing conductive and insulating materials directly onto a substrate using inkjet printing or dispensing technology. The process typically includes the following steps:
– Printing the conductive traces and pads using silver or copper nanoparticle ink
– Curing the printed features using heat or UV light
– Printing the insulating layers and vias using dielectric ink
– Repeating the process to build up the multi-layer PCB
Additive manufacturing offers several advantages, such as rapid prototyping, design flexibility, and reduced material waste. However, it may have limitations in terms of resolution, conductivity, and long-term reliability compared to subtractive manufacturing.
3. Hybrid Manufacturing
Hybrid manufacturing combines both subtractive and additive techniques to leverage their respective strengths. It involves selectively removing and depositing materials on the PCB substrate using a combination of etching, milling, and printing processes.
Hybrid manufacturing enables the fabrication of complex and high-density prototype PCBs with fine features and embedded components. It offers greater design flexibility and faster turnaround times compared to traditional subtractive manufacturing.
Prototype PCB Testing and Validation
Once the prototype PCB is fabricated, it must undergo rigorous testing and validation to ensure its functionality, performance, and reliability. The testing process typically includes the following steps:
1. Visual Inspection
Visual inspection is the first step in prototype PCB testing. It involves examining the PCB for any visible defects, such as:
– Broken or missing traces
– Short circuits or open connections
– Incorrect component placement or orientation
– Solder bridging or poor soldering quality
Visual inspection can be performed manually using a microscope or automatically using machine vision systems.
2. Electrical Testing
Electrical testing involves verifying the electrical characteristics and functionality of the prototype PCB. It typically includes the following tests:
– Continuity testing to check for open or short circuits
– Resistance testing to measure the resistance of traces and components
– Capacitance and inductance testing to verify the values of passive components
– Voltage and current measurements to assess the power distribution and signal integrity
– Functional testing to validate the overall operation of the PCB
Electrical testing can be performed using various tools, such as multimeters, oscilloscopes, and automated test equipment (ATE).
3. Environmental Testing
Environmental testing evaluates the performance and reliability of the prototype PCB under various environmental conditions. It helps ensure that the PCB can withstand the expected operating conditions and maintain its functionality over its intended lifetime. Environmental testing may include:
– Temperature cycling to assess the thermal stress and fatigue
– Humidity testing to evaluate the moisture resistance and corrosion
– Vibration and shock testing to verify the mechanical robustness
– Electromagnetic compatibility (EMC) testing to ensure compliance with regulatory standards
Environmental testing is typically performed in specialized chambers and facilities that can simulate the desired environmental conditions.
4. Functional Testing
Functional testing validates the overall operation and functionality of the prototype PCB in its intended application. It involves integrating the PCB with other components and subsystems and testing the complete system under real-world scenarios.
Functional testing may include:
– Power-on and boot-up testing
– Software and firmware integration testing
– User interface and input/output testing
– Communication and networking testing
– Performance and stress testing
Functional testing helps identify any issues or compatibility problems that may arise when the prototype PCB is integrated into the final product.
Frequently Asked Questions (FAQ)
- What is the difference between a prototype PCB and a production PCB?
-
A prototype PCB is a small batch of PCBs manufactured for testing and validation purposes, while a production PCB is mass-produced for commercial use. Prototype PCBs are typically made using different fabrication techniques and may have looser tolerances and specifications compared to production PCBs.
-
How long does it take to manufacture a prototype PCB?
-
The turnaround time for prototype PCB manufacturing varies depending on the complexity of the design, the fabrication technique used, and the supplier’s capabilities. Typically, prototype PCBs can be manufactured within a few days to a couple of weeks, depending on the specific requirements and priorities.
-
What are the common file formats used for prototype PCB design?
-
The most common file formats used for prototype PCB design include Gerber files (RS-274X), ODB++ (Open Database++), and IPC-2581. These file formats contain the necessary information for PCB fabrication, such as layer data, drill data, and aperture definitions.
-
How much does it cost to manufacture a prototype PCB?
-
The cost of prototype PCB manufacturing depends on various factors, such as the PCB size, layer count, material, quantity, and turnaround time. Prototype PCBs are generally more expensive per unit compared to production PCBs due to the lower volume and higher setup costs. The cost can range from a few hundred to several thousand dollars, depending on the specific requirements.
-
What are the benefits of using a turnkey prototype PCB manufacturing service?
- A turnkey prototype PCB manufacturing service offers end-to-end support, including design review, fabrication, assembly, and testing. The benefits of using such a service include:
- Streamlined process and communication
- Faster turnaround time and time-to-market
- Access to expertise and advanced manufacturing capabilities
- Reduced risk and improved quality control
- Cost savings through bundled services and volume discounts
Conclusion
Prototype PCB manufacturing plays a vital role in the development of electronic products. It enables designers and engineers to validate their designs, identify and resolve issues early, and accelerate the time-to-market. By investing in prototype PCB manufacturing, companies can reduce costs, mitigate risks, and ensure the success of their products.
When embarking on a prototype PCB project, it is essential to carefully consider the design requirements, fabrication techniques, and testing methods. Partnering with a reliable and experienced prototype PCB manufacturer can provide valuable support and expertise throughout the development process.
As technology continues to advance, prototype PCB manufacturing will remain a critical step in bringing innovative electronic products to market. By embracing best practices and leveraging the latest tools and techniques, companies can stay ahead of the competition and deliver high-quality products to their customers.
Leave a Reply